- お役立ち記事
- Role and effective operation of racks in manufacturing
月間76,176名の
製造業ご担当者様が閲覧しています*
*2025年3月31日現在のGoogle Analyticsのデータより
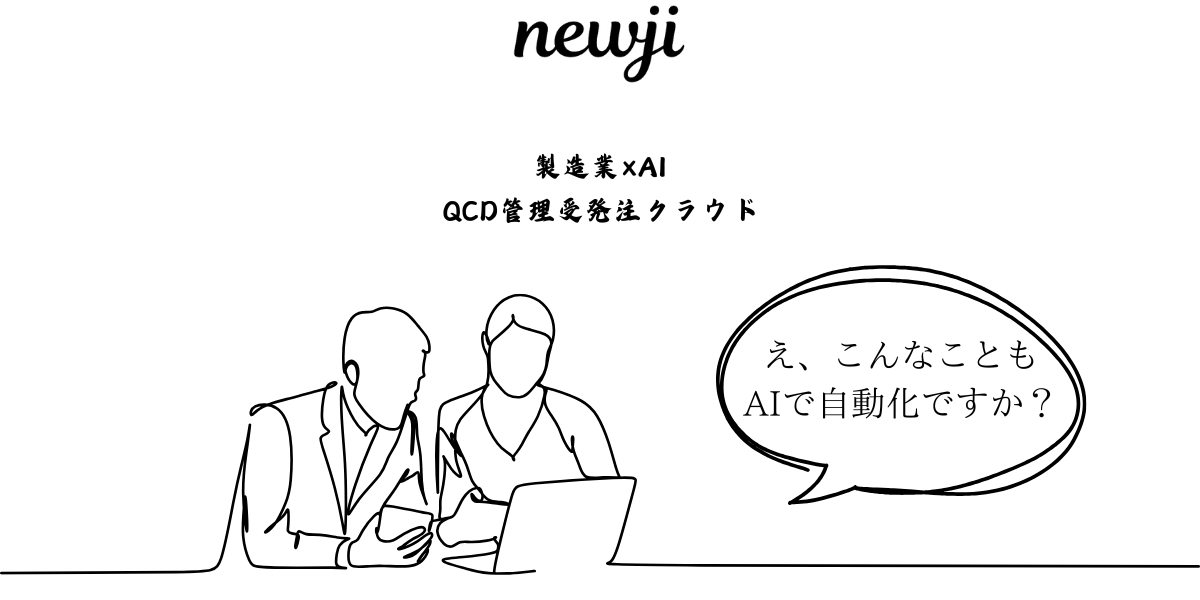
Role and effective operation of racks in manufacturing
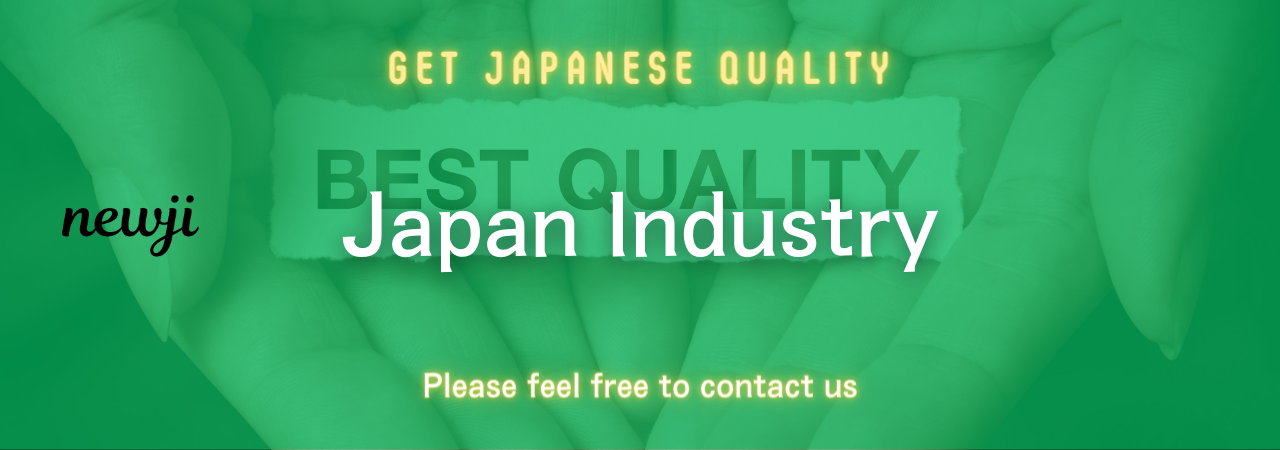
In the manufacturing industry, efficiency and organization are crucial to producing high-quality products consistently. An important component contributing to this is the effective operation of racks. Racking systems not only aid in conserving space but also improve productivity, worker safety, and inventory management.
目次
Understanding the Role of Racks in Manufacturing
Racks serve a fundamental purpose in the manufacturing industry. Their primary role is to provide organized storage for materials, tools, and finished products. By storing items vertically, racks maximize available floor space. This is essential in a manufacturing environment where space is often at a premium.
Maximizing Storage Space
One of the biggest challenges manufacturers face is optimizing the available space. Racking systems address this issue by utilizing vertical space, which would otherwise remain unused. By stacking items vertically, manufacturers can store a higher volume of materials within the same footprint.
Enhancing Organization
Well-organized racks help in maintaining an orderly workplace. When everything has its designated place, workers can easily find the materials and tools they need. This reduces the time spent searching for items and enhances overall productivity. An organized racking system also facilitates efficient inventory management by providing a clear view of stock levels and locations.
Improving Safety
Safety is a significant concern in any manufacturing environment. Racks contribute to workplace safety by keeping the floor area clear of obstacles, which reduces the risk of accidents. Additionally, properly designed and maintained racks prevent stored items from falling and causing injury.
Types of Racks in Manufacturing
Different manufacturing processes and materials require specific types of racking systems. Understanding the various types helps manufacturers choose the most suitable option for their needs.
Pallet Racks
Pallet racks are among the most common types used in manufacturing. They are designed to store palletized materials and typically feature adjustable shelves to accommodate different heights. These racks are highly versatile and can support heavy loads, making them ideal for storing bulk materials.
Cantilever Racks
Cantilever racks are perfect for storing long, bulky items such as pipes, lumber, or metal sheets. They consist of a series of horizontal arms extending from a vertical column, providing unobstructed access. This design allows for easy loading and unloading using forklifts or other equipment.
Drive-In and Drive-Through Racks
Drive-in and drive-through racks are designed for high-density storage. In a drive-in rack, forklifts enter an aisle to place or retrieve items, creating deep storage lanes. Drive-through racks are similar but allow access from both ends. These systems are ideal for storing large quantities of similar items.
Mezzanine Floors
Mezzanine floors are an innovative way to create additional storage space within the existing building height. They are elevated platforms that provide extra floor space for storing materials or assembling products. Mezzanines can be customized to fit specific requirements, offering flexible storage solutions.
Effective Operation of Racking Systems
Once the appropriate type of racking system is chosen, it is crucial to operate and maintain it effectively. Several best practices can ensure the optimal performance and longevity of racks.
Regular Inspections
Conducting regular inspections is essential to identify and rectify issues before they escalate. Check for any signs of damage or wear and tear, such as bent beams or loose bolts. Addressing these issues promptly can prevent accidents and extend the rack’s lifespan.
Proper Loading Techniques
Proper loading techniques are vital to maintaining the stability of racks. Ensure that loads are evenly distributed and do not exceed the rack’s weight capacity. Overloading racks can lead to structural failures and compromise safety.
Training and Education
Providing training and education to workers on the correct use of racking systems is imperative. Workers should be familiar with loading and unloading procedures, weight limits, and safety practices. This knowledge reduces the likelihood of accidents and ensures the efficient use of racks.
Implementing Safety Measures
Implementing safety measures such as guardrails, safety netting, and signage is crucial to preventing accidents. Guardrails can protect against forklift collisions, while safety netting can prevent items from falling. Clear signage indicating weight limits and load distribution guidelines can also enhance safety.
Automated Racking Systems
With advancements in technology, automated racking systems have become increasingly popular in manufacturing. These systems offer several advantages over traditional manual racking systems.
Increased Efficiency
Automated racking systems utilize robotics and automation to handle storage and retrieval tasks. This significantly reduces the time and effort required for these operations, leading to increased efficiency. Automated systems can operate around the clock, further enhancing productivity.
Enhanced Accuracy
Automation improves accuracy in inventory management. Automated systems use sensors and data-driven algorithms to precisely track inventory levels and locations. This minimizes errors and ensures that the right items are always available when needed.
Space Optimization
Automated racking systems can optimize space usage more effectively than manual systems. They can store items in compact configurations, reducing the need for aisles and maximizing storage capacity. This is especially beneficial in facilities with limited space.
Conclusion
In the manufacturing industry, the role and effective operation of racks cannot be overstated. They are essential for maximizing storage space, enhancing organization, and improving safety. By choosing the appropriate type of racking system and implementing best practices for their operation, manufacturers can achieve optimal efficiency and productivity. Moreover, the advent of automated racking systems offers a glimpse into the future of manufacturing, where technology and innovation drive progress. Ultimately, the effective use of racks is a key factor in the success of any manufacturing enterprise.
資料ダウンロード
QCD管理受発注クラウド「newji」は、受発注部門で必要なQCD管理全てを備えた、現場特化型兼クラウド型の今世紀最高の受発注管理システムとなります。
ユーザー登録
受発注業務の効率化だけでなく、システムを導入することで、コスト削減や製品・資材のステータス可視化のほか、属人化していた受発注情報の共有化による内部不正防止や統制にも役立ちます。
NEWJI DX
製造業に特化したデジタルトランスフォーメーション(DX)の実現を目指す請負開発型のコンサルティングサービスです。AI、iPaaS、および先端の技術を駆使して、製造プロセスの効率化、業務効率化、チームワーク強化、コスト削減、品質向上を実現します。このサービスは、製造業の課題を深く理解し、それに対する最適なデジタルソリューションを提供することで、企業が持続的な成長とイノベーションを達成できるようサポートします。
製造業ニュース解説
製造業、主に購買・調達部門にお勤めの方々に向けた情報を配信しております。
新任の方やベテランの方、管理職を対象とした幅広いコンテンツをご用意しております。
お問い合わせ
コストダウンが利益に直結する術だと理解していても、なかなか前に進めることができない状況。そんな時は、newjiのコストダウン自動化機能で大きく利益貢献しよう!
(β版非公開)