- お役立ち記事
- Role and selection of master sample in product inspection
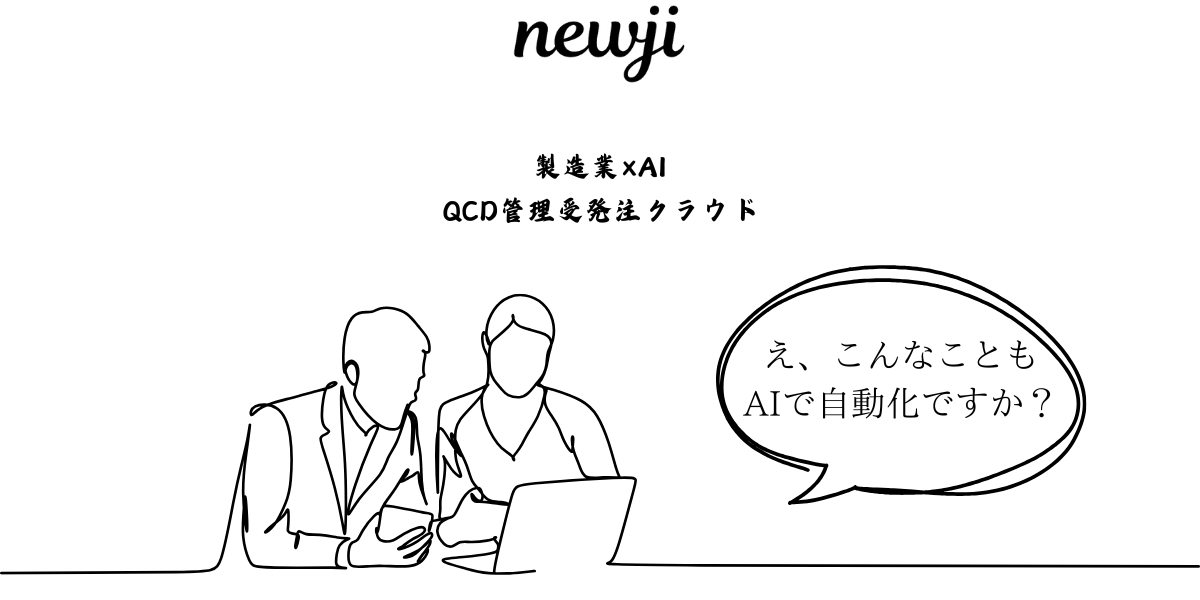
Role and selection of master sample in product inspection
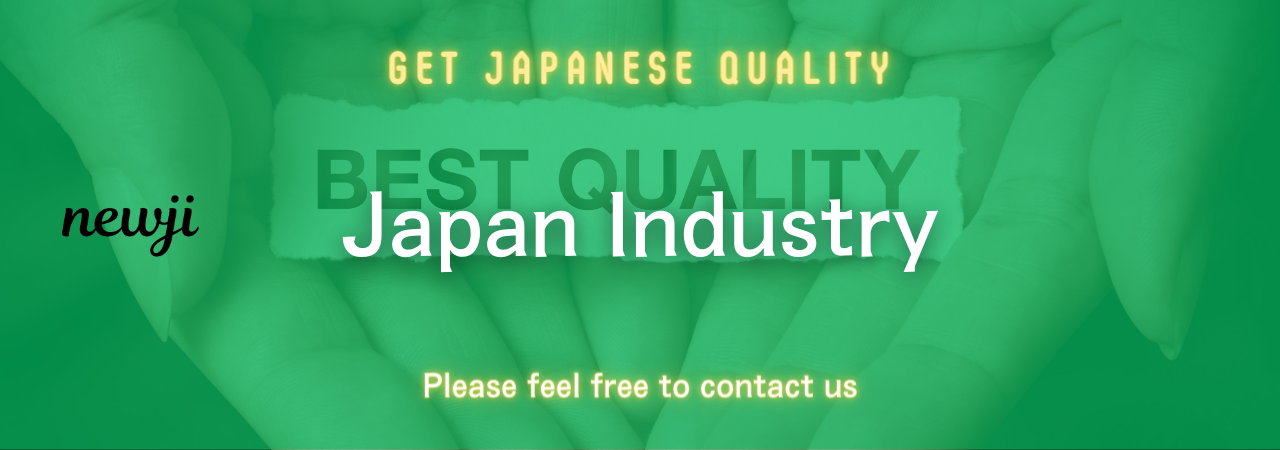
When it comes to ensuring the quality and reliability of products, one crucial aspect that often gets overlooked is the role of the master sample in product inspection. This essential component ensures that every item manufactured meets the necessary standards and specifications, guaranteeing customer satisfaction and consistency. In this article, we’ll explore the role of master samples in product inspection and how to select and maintain them effectively.
目次
What is a Master Sample?
A master sample, sometimes referred to as a golden sample or reference sample, is a product or component that has been thoroughly inspected and certified to meet all specified requirements. This sample serves as the benchmark against which all other products in a production batch are compared to ensure they conform to quality standards. It embodies the precise characteristics desired in the final product, including dimensions, functionality, and appearance.
The Role of Master Samples in Product Inspection
Master samples play several vital roles in the product inspection process. They serve as the definitive standard for quality control, providing a concrete example of what a final product should look like. Here’s a closer look at their key functions:
Quality Benchmark
The primary role of a master sample is to act as a quality benchmark. Inspectors use it to compare each production item against this benchmark to verify that all aspects of quality are met. This ensures that any variations or defects in the manufacturing process are identified and addressed swiftly.
Consistency Across Batches
Consistency is crucial in manufacturing, especially when it comes to large-scale production. Master samples help maintain uniformity across all batches, ensuring that each product produced matches the approved sample. This consistency builds trust among customers and maintains the brand’s reputation.
Inspection Reference
During various stages of production, inspectors reference the master sample to ensure ongoing quality. It acts as a tangible standard, making it easier for inspectors to identify deviations from the norm. This is particularly important for visual inspections where subjective judgments may vary between inspectors.
Criteria for Selecting a Master Sample
Choosing the right master sample is a critical step in the product inspection process. The selected sample should represent the highest quality achievable and be a true reflection of the desired final product. Here are some key criteria to consider:
Accuracy
The master sample must accurately represent the final product’s specifications. Any deviations in dimensions, materials, or color should be minimal or non-existent. This accuracy ensures that the sample matches the product’s intended design and functionality.
Representativeness
It’s essential that the master sample is a representative example of the entire production batch. If the sample doesn’t accurately reflect the overall production, it won’t effectively serve as a benchmark. In some cases, multiple master samples may be needed if there are significant variations within the product range.
Documentation
Detailed documentation should accompany the master sample, outlining all relevant specifications, tolerances, and inspection criteria. This documentation provides a comprehensive reference that can be used by inspectors to verify the sample’s accuracy and quality.
Maintaining the Integrity of Master Samples
Once a master sample is selected, maintaining its integrity is crucial to ensuring ongoing quality control. Here are some best practices for keeping your master samples in top condition:
Storage Conditions
Master samples should be stored in a controlled environment to prevent damage or deterioration. Environmental factors such as temperature, humidity, and light can affect the sample’s condition over time. Proper storage ensures that the sample remains in its original, unaltered state.
Regular Verification
Periodic re-verification of master samples is essential. Regularly inspecting the sample ensures that it still meets the required standards and hasn’t changed due to long-term storage or handling. Any discrepancies should be addressed promptly to maintain the sample’s reliability.
Controlled Access
Limiting access to master samples is another important step in maintaining their integrity. Only authorized personnel should handle these samples to prevent accidental damage or contamination. Clear procedures for handling and using the sample should be established and followed.
Conclusion
Master samples play a vital role in product inspection by acting as the definitive standard for quality. By providing a benchmark for comparison, they ensure consistency across production batches and help identify any deviations from the desired specifications.
Selecting an accurate and representative master sample, accompanied by thorough documentation, is crucial to effective quality control.
Maintaining the integrity of these samples through proper storage, regular verification, and controlled access further ensures that they continue to serve as reliable benchmarks. In doing so, businesses can uphold the highest standards of product quality and ensure customer satisfaction.
資料ダウンロード
QCD調達購買管理クラウド「newji」は、調達購買部門で必要なQCD管理全てを備えた、現場特化型兼クラウド型の今世紀最高の購買管理システムとなります。
ユーザー登録
調達購買業務の効率化だけでなく、システムを導入することで、コスト削減や製品・資材のステータス可視化のほか、属人化していた購買情報の共有化による内部不正防止や統制にも役立ちます。
NEWJI DX
製造業に特化したデジタルトランスフォーメーション(DX)の実現を目指す請負開発型のコンサルティングサービスです。AI、iPaaS、および先端の技術を駆使して、製造プロセスの効率化、業務効率化、チームワーク強化、コスト削減、品質向上を実現します。このサービスは、製造業の課題を深く理解し、それに対する最適なデジタルソリューションを提供することで、企業が持続的な成長とイノベーションを達成できるようサポートします。
オンライン講座
製造業、主に購買・調達部門にお勤めの方々に向けた情報を配信しております。
新任の方やベテランの方、管理職を対象とした幅広いコンテンツをご用意しております。
お問い合わせ
コストダウンが利益に直結する術だと理解していても、なかなか前に進めることができない状況。そんな時は、newjiのコストダウン自動化機能で大きく利益貢献しよう!
(Β版非公開)