- お役立ち記事
- Rubber Mold OEM: Precision Molding Solutions
Rubber Mold OEM: Precision Molding Solutions
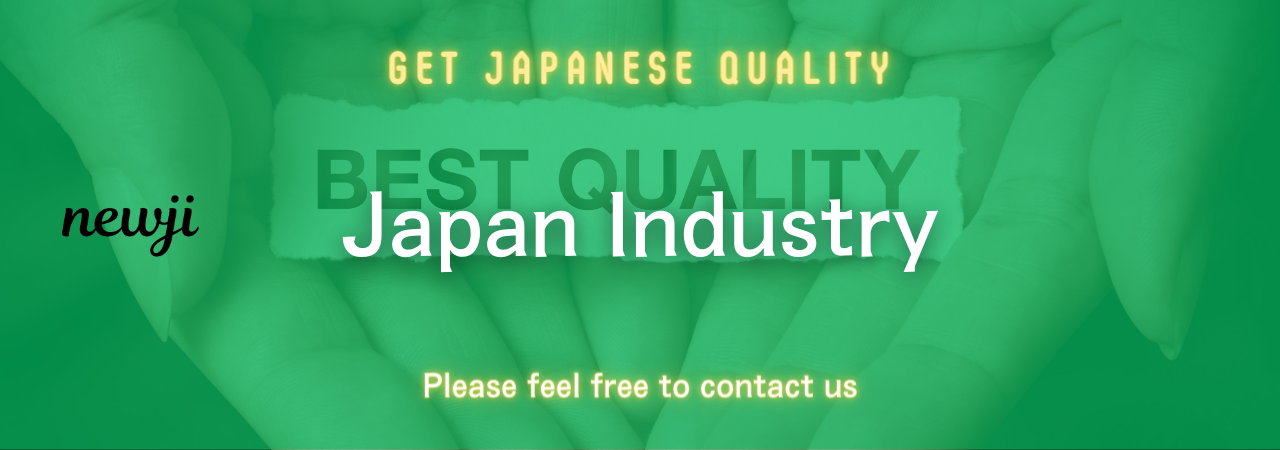
目次
What is Rubber Mold OEM?
Rubber Mold OEM, or Original Equipment Manufacturer, refers to companies that design and produce high-quality rubber molds tailored to specific industrial needs.
These molds are crucial components in various manufacturing processes, including automotive, aerospace, electronics, and medical industries.
The precision and customization of these molds play a significant role in the overall quality and efficiency of the products being manufactured.
Why Precision Matters in Rubber Molding
In the world of manufacturing, precision is paramount.
Rubber molding is a complex process that requires exact specifications to ensure that the final product meets stringent quality standards.
A slight deviation from the intended design can lead to product failure, increased waste, and higher production costs.
Precision molds ensure that each piece fits perfectly in its designated spot, maintaining consistency across production batches and reducing the risk of defects.
The Importance of Customization in Rubber Mold OEM
Every industry has unique requirements, and standard molds often fail to meet these specific needs.
Custom rubber molds are designed to match the exact specifications and demands of the product, ensuring optimal performance and quality.
OEMs collaborate closely with clients to understand their specific challenges and deliver solutions that enhance their product’s functionality and aesthetic appeal.
Customization not only improves performance but also provides manufacturers with a competitive edge in the market.
Materials Used in Rubber Molding
The choice of material is crucial in rubber molding as it directly impacts the mold’s durability and the product’s performance.
Common materials used in rubber mold OEM include natural rubber, silicone, EPDM, and nitrile, each offering distinct properties suitable for different applications.
For example, silicone rubber is known for its heat resistance and flexibility, making it ideal for automotive and aerospace components.
On the other hand, nitrile rubber is preferred in the automotive industry for its excellent oil and fuel resistance.
The Rubber Molding Process
The rubber molding process comprises several stages, each critical to achieving a high-quality final product.
The process generally follows these steps:
1. Design and Prototyping
The initial stage involves designing the mold based on the client’s specifications.
Prototypes may be created to validate the design and make necessary adjustments before full-scale production begins.
This stage is crucial for identifying potential issues and ensuring that the mold will function as intended.
2. Material Selection
Selecting the appropriate material is essential to meet the specific requirements of the application.
Factors such as temperature resistance, flexibility, and durability are considered during this phase.
The right material ensures that the mold can withstand the manufacturing conditions and deliver consistent performance.
3. Mold Production
Once the design is finalized and materials chosen, the mold production begins.
This involves shaping the chosen material into the desired mold design using specialized machinery and techniques.
The precision of the machinery ensures that the mold meets exact measurements and tolerances.
4. Quality Control
Quality control is a vital part of the rubber molding process.
Each mold undergoes thorough inspection and testing to ensure it meets the required specifications and quality standards.
This step helps identify any defects or inconsistencies before the mold is used in mass production.
5. Mass Production
After passing quality control, the molds are moved into mass production.
This phase involves using the molds to create multiple copies of the final product.
Efficiency and speed are critical during this phase to meet production deadlines and minimize costs.
Advantages of Working with a Rubber Mold OEM
Collaborating with a reliable rubber mold OEM offers several advantages to manufacturers, including:
1. Expertise and Experience
OEMs have extensive knowledge and experience in creating high-quality molds tailored to specific industry needs.
Their expertise ensures that clients receive superior products that meet or exceed their expectations.
2. Cost-Effectiveness
While custom molds may require an initial investment, they often result in long-term cost savings.
Precision molds reduce waste, minimize defects, and lower production costs, leading to significant savings over time.
3. Improved Product Quality
High-quality molds result in superior products.
Manufacturers can deliver consistent, reliable products that enhance their brand reputation and customer satisfaction.
4. Innovation and Creativity
Working with an OEM allows manufacturers to explore innovative solutions and designs tailored to their specific needs.
OEMs can offer unique insights and creative ideas that improve product functionality and appeal.
Choosing the Right Rubber Mold OEM Partner
Selecting the right OEM partner is crucial to achieving the best results.
Here are a few factors to consider when choosing a rubber mold OEM:
1. Reputation and Experience
Research potential OEM partners and their reputation in the industry.
Experience and positive reviews from previous clients are reliable indicators of quality and reliability.
2. Technical Capabilities
Evaluate the OEM’s technical abilities, including their machinery, technology, and the skills of their team.
A company with advanced technology and skilled engineers will likely produce superior molds.
3. Customization Options
Ensure that the OEM offers customization services to meet your unique specifications.
A partner willing to work closely with you to understand your needs will deliver the best solutions.
4. Quality Assurance Processes
Confirm that the OEM has stringent quality control measures in place to ensure consistent product quality.
Their commitment to quality is vital for the success of your project.
Conclusion
Rubber Mold OEM plays a crucial role in the manufacturing industry by providing precision and customized molding solutions.
Through collaboration with OEMs, manufacturers can improve product quality, reduce costs, and gain a competitive edge in the market.
By considering factors such as expertise, technical capabilities, and customization options, you can choose the right OEM partner for your specific needs.
資料ダウンロード
QCD調達購買管理クラウド「newji」は、調達購買部門で必要なQCD管理全てを備えた、現場特化型兼クラウド型の今世紀最高の購買管理システムとなります。
ユーザー登録
調達購買業務の効率化だけでなく、システムを導入することで、コスト削減や製品・資材のステータス可視化のほか、属人化していた購買情報の共有化による内部不正防止や統制にも役立ちます。
NEWJI DX
製造業に特化したデジタルトランスフォーメーション(DX)の実現を目指す請負開発型のコンサルティングサービスです。AI、iPaaS、および先端の技術を駆使して、製造プロセスの効率化、業務効率化、チームワーク強化、コスト削減、品質向上を実現します。このサービスは、製造業の課題を深く理解し、それに対する最適なデジタルソリューションを提供することで、企業が持続的な成長とイノベーションを達成できるようサポートします。
オンライン講座
製造業、主に購買・調達部門にお勤めの方々に向けた情報を配信しております。
新任の方やベテランの方、管理職を対象とした幅広いコンテンツをご用意しております。
お問い合わせ
コストダウンが利益に直結する術だと理解していても、なかなか前に進めることができない状況。そんな時は、newjiのコストダウン自動化機能で大きく利益貢献しよう!
(Β版非公開)