- お役立ち記事
- Rubber Molding Techniques and Practices in Manufacturing
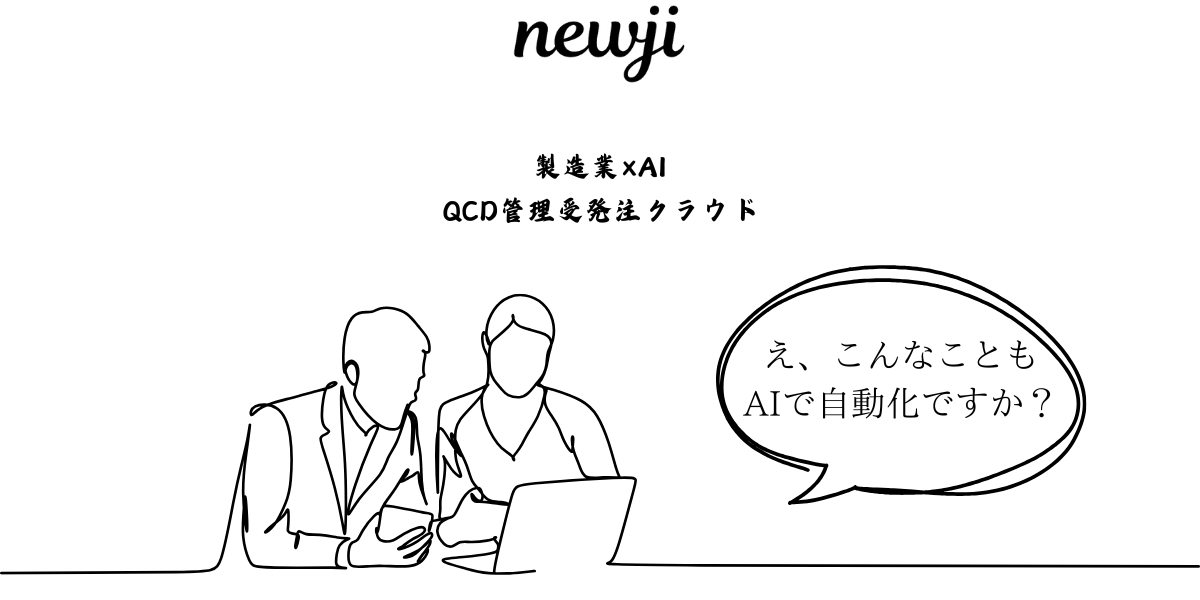
Rubber Molding Techniques and Practices in Manufacturing
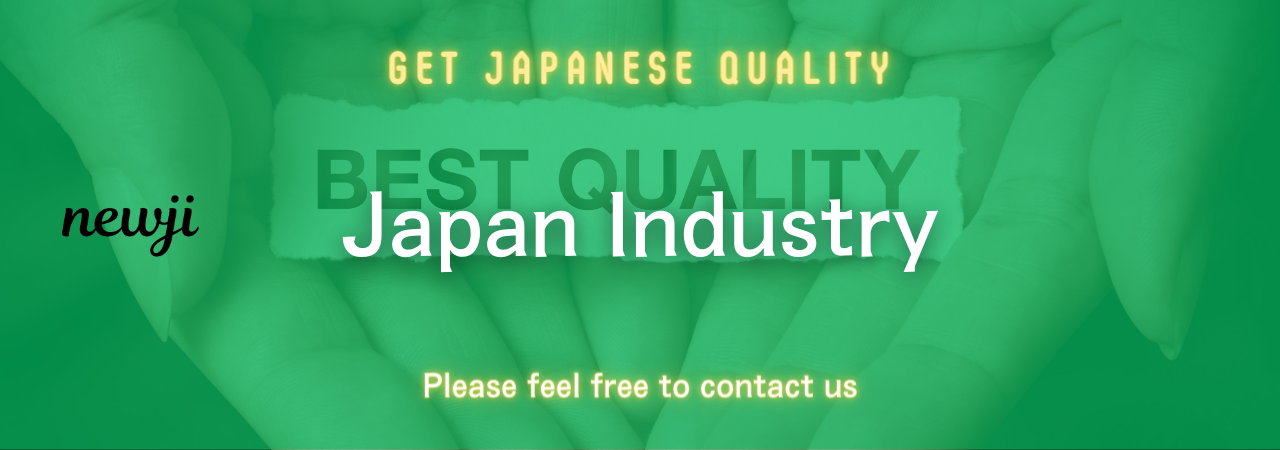
Rubber molding is a fascinating process that transforms raw rubber into useful products we use in our daily lives.
From car tires to rubber bands, the principles behind rubber molding ensure that these items are durable and effective.
In this article, we’ll walk through the various techniques and practices involved in rubber molding in manufacturing.
We’ll explore what makes these processes efficient and how they contribute to the variety and quality of rubber products available today.
目次
What is Rubber Molding?
Rubber molding is a manufacturing process that shapes raw rubber material into finished products.
This process uses heat, pressure, and molds to create specific shapes and features in the rubber material.
The end product can be anything from a simple o-ring to a complex automotive part.
Types of Rubber Molding Techniques
There are several rubber molding techniques commonly used in the industry.
Each method has its benefits and is chosen based on the type of product being made and the specific requirements of that product.
Compression Molding
Compression molding is one of the oldest and most straightforward techniques used in rubber molding.
It involves placing a pre-measured amount of raw rubber in a mold cavity.
The mold is then closed, and heat and pressure are applied, causing the rubber to shape into the mold form.
This method is excellent for producing large, durable parts and is often used for making seals, gaskets, and other heavy-duty components.
Injection Molding
Injection molding is a more sophisticated approach that allows for high precision and repeatability.
In this process, raw rubber is heated until it becomes a liquid and then injected into a mold.
Once in the mold, it is cooled and solidified into the final part.
This method is highly efficient and excellent for producing large volumes of small, detailed parts like o-rings and medical devices.
Transfer Molding
Transfer molding is similar to compression molding but with added complexity.
In this method, raw rubber is placed in a chamber connected to the mold cavity.
When pressure is applied, the rubber is pushed into the mold where it takes on the desired shape.
Transfer molding is ideal for creating intricate parts with metal inserts and is frequently used in the production of electronic components and connectors.
Materials Used in Rubber Molding
Different types of rubber materials are used depending on the requirements of the final product.
Each type of rubber has its own set of properties that make it suitable for specific applications.
Natural Rubber
Natural rubber, derived from the latex of rubber trees, is highly flexible and durable.
It is commonly used for products that require high elasticity like balloons and rubber bands.
Synthetic Rubber
Synthetic rubber is made through chemical processes and includes types such as SBR (Styrene-Butadiene Rubber), NBR (Nitrile Butadiene Rubber), and EPDM (Ethylene Propylene Diene Monomer).
These materials are engineered to offer specific properties like oil resistance, heat resistance, and durability.
Synthetic rubbers are widely used in automotive parts, industrial seals, and gaskets.
Silicone Rubber
Silicone rubber is known for its exceptional heat resistance and flexibility.
It is often used in high-temperature applications like baking molds and medical devices.
Silicone rubber is also highly resistant to environmental conditions, making it ideal for outdoor applications.
Advantages of Rubber Molding
Rubber molding offers several advantages that make it a preferred choice in many industries.
Customizable Designs
One of the main benefits of rubber molding is the ability to create highly customized designs.
Complex shapes and intricate details can be achieved through precise mold engineering and sophisticated molding techniques.
This allows for the production of parts that meet very exact specifications.
Cost Efficiency
When producing large volumes of parts, rubber molding can be highly cost-efficient.
Once the molds are created, they can be used repeatedly to produce many parts, reducing the overall cost per unit.
Strength and Durability
Products made through rubber molding are known for their strength and durability.
The process ensures that the material is evenly distributed and cured, resulting in parts that can withstand harsh conditions and heavy use.
Challenges in Rubber Molding
Despite its many advantages, rubber molding also presents some challenges that manufacturers must be aware of.
Tooling Costs
Creating the molds used in rubber molding can be expensive, especially for complex parts.
These tooling costs can be a barrier for small production runs or custom one-off parts.
Material Waste
During the molding process, excess rubber may be trimmed away, resulting in material waste.
Efficient material management and recycling practices are essential to minimize waste and reduce costs.
Quality Control
Maintaining consistent quality can be challenging, especially with complex parts.
Rigorous testing and inspection processes are necessary to ensure that each part meets the required standards.
Future Trends in Rubber Molding
The rubber molding industry continues to evolve with new technologies and materials.
Automation
Automation is playing an increasingly important role in rubber molding.
Robotic systems and advanced software are being used to improve precision, reduce labor costs, and enhance production efficiency.
Eco-friendly Materials
There is a growing demand for eco-friendly materials in the rubber industry.
Developments in bio-based rubbers and recycling techniques are helping to reduce the environmental impact of rubber products.
3D Printing
3D printing technology is being explored as a potential complement to traditional rubber molding.
It offers the ability to create prototypes quickly and could revolutionize the production of custom parts.
Rubber molding remains a crucial process in manufacturing, offering the ability to create durable and customizable products.
By understanding the various techniques and materials involved, manufacturers can continue to innovate and meet the diverse needs of different industries.
The future of rubber molding looks bright, with advancements in technology and a focus on sustainability promising to further enhance this already versatile manufacturing process.
資料ダウンロード
QCD調達購買管理クラウド「newji」は、調達購買部門で必要なQCD管理全てを備えた、現場特化型兼クラウド型の今世紀最高の購買管理システムとなります。
ユーザー登録
調達購買業務の効率化だけでなく、システムを導入することで、コスト削減や製品・資材のステータス可視化のほか、属人化していた購買情報の共有化による内部不正防止や統制にも役立ちます。
NEWJI DX
製造業に特化したデジタルトランスフォーメーション(DX)の実現を目指す請負開発型のコンサルティングサービスです。AI、iPaaS、および先端の技術を駆使して、製造プロセスの効率化、業務効率化、チームワーク強化、コスト削減、品質向上を実現します。このサービスは、製造業の課題を深く理解し、それに対する最適なデジタルソリューションを提供することで、企業が持続的な成長とイノベーションを達成できるようサポートします。
オンライン講座
製造業、主に購買・調達部門にお勤めの方々に向けた情報を配信しております。
新任の方やベテランの方、管理職を対象とした幅広いコンテンツをご用意しております。
お問い合わせ
コストダウンが利益に直結する術だと理解していても、なかなか前に進めることができない状況。そんな時は、newjiのコストダウン自動化機能で大きく利益貢献しよう!
(Β版非公開)