- お役立ち記事
- Safety Design and Collision Detection Systems for Collaborative Robots
月間76,176名の
製造業ご担当者様が閲覧しています*
*2025年3月31日現在のGoogle Analyticsのデータより
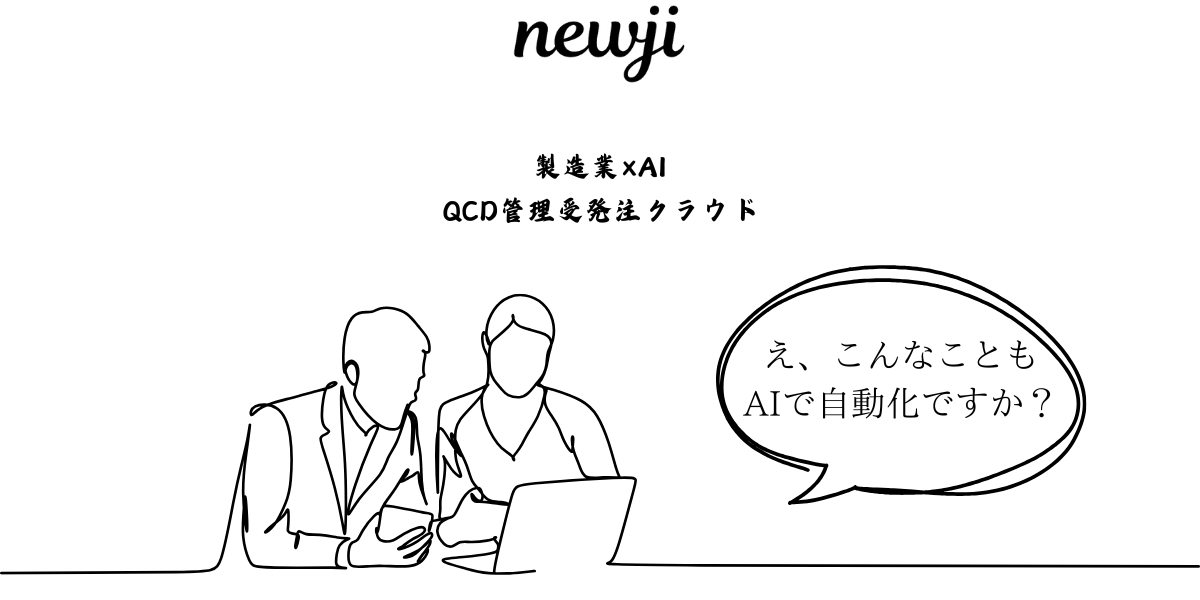
Safety Design and Collision Detection Systems for Collaborative Robots
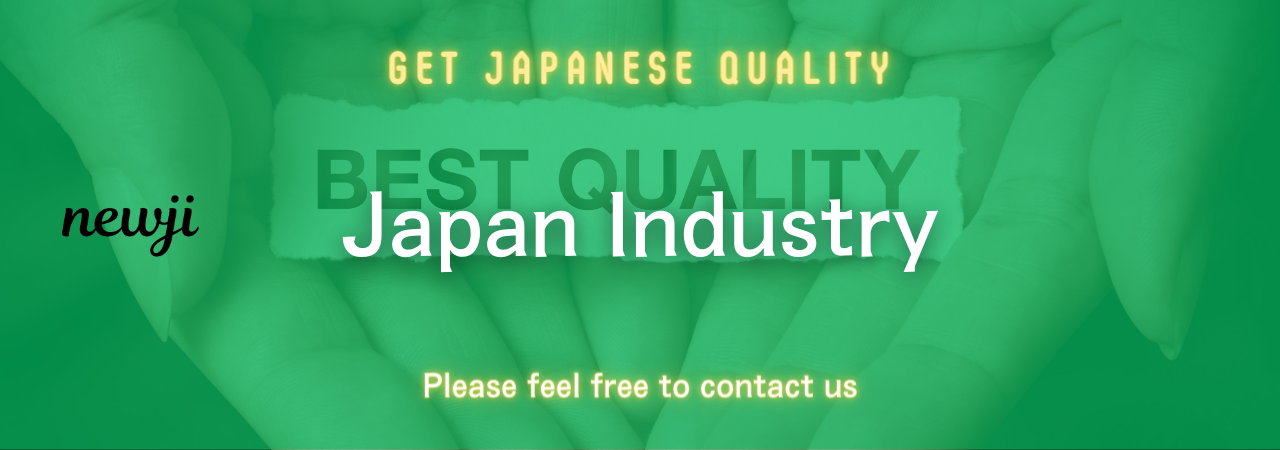
Collaborative robots, also known as cobots, have emerged as a revolutionary force in industrial processes.
Unlike traditional robots designed to operate in isolation, these cobots are engineered to work alongside human operators.
Their integration into production lines has necessitated a strong focus on safety features and collision detection systems to ensure that they operate without causing harm.
目次
Understanding Collaborative Robots
Cobots are designed to assist human workers in a shared workspace.
They are used in a variety of tasks, from assembly lines to packaging and logistics.
One of their standout features is their ability to safely interact with humans, thanks to advanced safety systems and sensors.
The Importance of Safety in Cobots
When humans and machines share a workspace, the margin for error must be minimized.
Safety becomes a paramount concern because any mishap can lead to serious injury or operational downtime.
Therefore, manufacturers have invested heavily in designing cobots with built-in safety mechanisms.
Intrinsic Safety Design
One of the primary design principles of cobots is intrinsic safety.
This means that the cobot is designed to be inherently safe from the ground up.
Materials, software, and hardware are selected and engineered to reduce risk factors.
For example, cobots often have rounded edges and are constructed from materials that are less likely to cause injury.
Force and Speed Limits
Another key aspect of safety design in cobots is the careful regulation of force and speed.
These robots are programmed to stop if they encounter unexpected resistance.
In addition, their operational speed is controlled to prevent them from moving too quickly in tight spaces where humans are present.
Collision Detection Systems
Even with these safety features, the potential for accidental collisions exists.
Therefore, collision detection systems are critical.
These systems use various sensors and algorithms to monitor the robot’s environment and predict collisions before they happen.
Types of Sensors
Several types of sensors are used in cobots for collision detection:
– **Proximity Sensors:** These detect objects close to the robot without physical contact.
They use technologies like infrared, ultrasonic, and capacitive sensing.
– **Touch Sensors:** These sensors detect actual contact with objects or humans.
They often use technology similar to that found in touchscreens.
– **Vision Systems:** Cameras and image recognition software allow cobots to ‘see’ their surroundings.
These systems can identify objects and people, helping the robot navigate safely.
Predictive Algorithms
Sensor data alone is not enough.
Advanced algorithms process this data in real-time to predict potential collisions.
Machine learning and artificial intelligence (AI) are increasingly being used to improve the accuracy of these predictions.
The cobot can then take immediate action to avoid a collision, such as stopping or rerouting its path.
Regulatory Standards
Various regulatory bodies have established standards to ensure the safe operation of cobots.
These standards cover everything from the design and construction of the robots to their operational procedures.
ISO 10218
The International Organization for Standardization (ISO) has published ISO 10218, which provides guidelines for the safety of industrial robots.
Particular attention is given to collaborative operations, ensuring that cobots meet rigorous safety requirements.
ANSI/RIA R15.06
In the United States, the American National Standards Institute (ANSI) and the Robotic Industries Association (RIA) have developed the ANSI/RIA R15.06 standard.
This document outlines safety requirements for industrial robots and robotic systems, including collaborative robots.
The Future of Cobots
As technology advances, the safety and efficiency of cobots will continue to improve.
Future developments may include even more sophisticated sensors and AI algorithms that can better predict and prevent collisions.
Additionally, materials with enhanced safety properties will likely be developed, further minimizing risks.
Integration with IoT
The Internet of Things (IoT) will play a significant role in the future of cobots.
By integrating cobots with IoT systems, real-time data can be collected and analyzed, providing insights that can further enhance safety protocols.
Human-Robot Collaboration
The ultimate goal is seamless human-robot collaboration.
By continuously improving safety and collision detection systems, manufacturers can ensure that cobots become even more reliable partners in the workplace.
In summary, the safety design and collision detection systems of collaborative robots are critical components that enable their successful operation alongside humans.
As technology and regulatory standards evolve, these systems will only become more sophisticated, paving the way for safer and more efficient industrial processes.
資料ダウンロード
QCD管理受発注クラウド「newji」は、受発注部門で必要なQCD管理全てを備えた、現場特化型兼クラウド型の今世紀最高の受発注管理システムとなります。
ユーザー登録
受発注業務の効率化だけでなく、システムを導入することで、コスト削減や製品・資材のステータス可視化のほか、属人化していた受発注情報の共有化による内部不正防止や統制にも役立ちます。
NEWJI DX
製造業に特化したデジタルトランスフォーメーション(DX)の実現を目指す請負開発型のコンサルティングサービスです。AI、iPaaS、および先端の技術を駆使して、製造プロセスの効率化、業務効率化、チームワーク強化、コスト削減、品質向上を実現します。このサービスは、製造業の課題を深く理解し、それに対する最適なデジタルソリューションを提供することで、企業が持続的な成長とイノベーションを達成できるようサポートします。
製造業ニュース解説
製造業、主に購買・調達部門にお勤めの方々に向けた情報を配信しております。
新任の方やベテランの方、管理職を対象とした幅広いコンテンツをご用意しております。
お問い合わせ
コストダウンが利益に直結する術だと理解していても、なかなか前に進めることができない状況。そんな時は、newjiのコストダウン自動化機能で大きく利益貢献しよう!
(β版非公開)