- お役立ち記事
- Safety Management and Employee Roles in Wood Processing Factories
月間76,176名の
製造業ご担当者様が閲覧しています*
*2025年3月31日現在のGoogle Analyticsのデータより
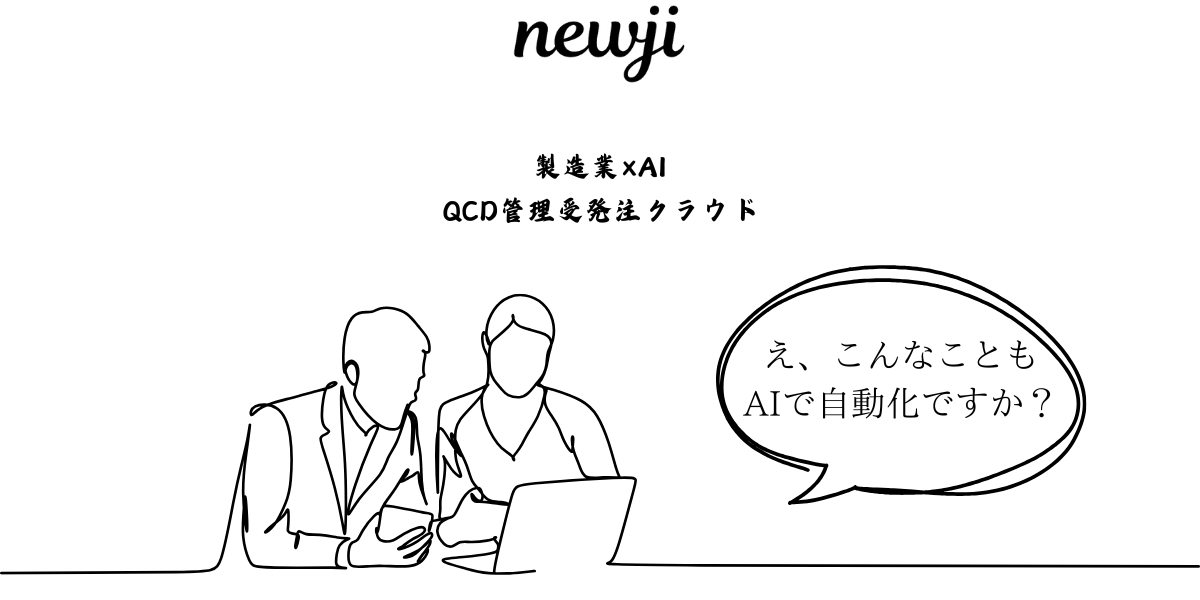
Safety Management and Employee Roles in Wood Processing Factories
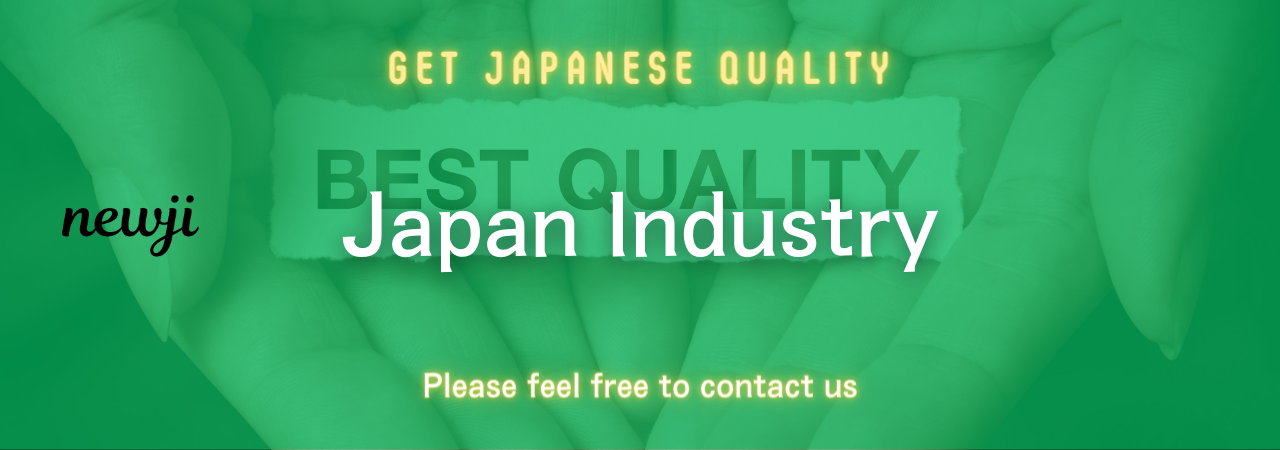
目次
Understanding Safety Management in Wood Processing Factories
Safety management is a crucial aspect of operations in wood processing factories.
It involves a systematic approach to ensuring the health and safety of workers while maintaining productivity.
In the context of such factories, it includes the identification of potential hazards, risk assessment, the establishment of safety protocols, and continuous monitoring.
Wood processing factories deal with various materials and machinery that can be hazardous if not managed properly.
Common risks include dust explosions, machine-related injuries, and exposure to chemicals used in the processing of wood.
Effective safety management requires addressing each of these issues comprehensively.
One of the cornerstones of safety management is the implementation of safety protocols and regulations.
These are guidelines and procedures that dictate how workers should conduct their tasks to minimize risks.
Following these protocols ensures that workers are aware of safety measures and consistently adhere to them.
Regular safety training for employees is another integral part of safety management.
Training sessions should provide comprehensive knowledge on how to handle machinery, use personal protective equipment (PPE), and respond to emergencies.
This education empowers employees with the skills necessary to maintain a safe work environment.
The Role of Equipment and Technology in Safety
Technology plays a significant role in enhancing safety management systems in wood processing factories.
Machines equipped with advanced safety features, such as automatic shut-offs and emergency brakes, are vital.
These technological advancements help reduce the occurrence of accidents.
Moreover, dust collection systems are essential in preventing dust-related explosions.
Wood dust is highly combustible, and without proper collection systems, it can pose a significant hazard.
Factories must ensure that these systems are regularly maintained and functioning optimally.
The use of technology in monitoring environmental conditions within the factory is also crucial.
Temperature and humidity monitoring systems help maintain optimal working conditions, reducing the likelihood of accidents related to machinery overheating or humidity affecting wood properties.
The Importance of Maintenance
Routine maintenance of equipment and machinery is vital in the prevention of accidents.
Factories should establish a schedule for regular inspections and maintenance tasks.
These should include checking the condition of machines, determining if any repairs are needed, and ensuring that all safety features are operational.
Well-maintained equipment is less likely to malfunction, which reduces the risk of workplace injuries.
Additionally, maintenance helps extend the lifespan of machinery, making it a cost-effective strategy for factory operations.
Employee Roles in Ensuring Safety
Employees play a critical role in maintaining safety in wood processing factories.
Every employee has a responsibility to follow safety protocols and report any unsafe conditions to their supervisors.
This proactive approach helps identify potential hazards before they lead to accidents.
Workers should be encouraged to wear personal protective equipment at all times.
This includes items like helmets, eye protection, gloves, and masks.
PPE serves as the first line of defense against common workplace hazards.
Supervisors and managers have an added responsibility to ensure that safety policies are enforced.
Regular safety audits and inspections are crucial.
These assessments help identify areas where safety can be improved and ensure compliance with established protocols.
There should be an open line of communication between employees and management regarding safety concerns.
Encouraging employees to speak up about their concerns without fear of reprimand creates a culture of safety.
The Role of Safety Committees
Safety committees, composed of workers from various departments within the factory, are instrumental in promoting a safe work environment.
These committees focus on evaluating current safety measures, making recommendations for improvements, and organizing safety training initiatives.
Safety committees act as a bridge between employees and management.
They provide valuable insights into the practical challenges faced on the floor and help tailor safety practices to better meet the needs of all workers.
Continuous Improvement in Safety Practices
Safety management in wood processing factories is not a one-time effort but a continuous process.
Implementing a system for ongoing evaluation and improvement of safety practices is essential.
This involves staying updated with industry standards, technological advancements, and new safety equipment.
Regular feedback from employees can offer insights into how processes can be improved.
Adopting a continuous improvement mindset ensures that the factory remains proactive in addressing safety concerns.
Accidents and near-misses should be documented and investigated.
Understanding the root causes of these incidents can provide valuable lessons, helping prevent similar occurrences in the future.
The Benefits of Effective Safety Management
Implementing an effective safety management system has numerous benefits for wood processing factories.
A safer workplace leads to higher employee morale and productivity, as workers feel more secure and valued.
This can result in reduced absenteeism and turnover, further benefiting the company’s operations.
Additionally, a factory known for its strong safety record may experience fewer legal and regulatory issues.
Compliance with safety regulations reduces the likelihood of facing fines and penalties.
An excellent safety reputation can enhance the factory’s standing in the industry, attracting skilled workers and potential clients who value safety as a key operational consideration.
In summary, safety management and employee roles in wood processing factories are paramount for ensuring a safe and productive environment.
By implementing effective safety measures and engaging all employees in the process, factories can mitigate risks and enhance their operational efficiency.
資料ダウンロード
QCD管理受発注クラウド「newji」は、受発注部門で必要なQCD管理全てを備えた、現場特化型兼クラウド型の今世紀最高の受発注管理システムとなります。
ユーザー登録
受発注業務の効率化だけでなく、システムを導入することで、コスト削減や製品・資材のステータス可視化のほか、属人化していた受発注情報の共有化による内部不正防止や統制にも役立ちます。
NEWJI DX
製造業に特化したデジタルトランスフォーメーション(DX)の実現を目指す請負開発型のコンサルティングサービスです。AI、iPaaS、および先端の技術を駆使して、製造プロセスの効率化、業務効率化、チームワーク強化、コスト削減、品質向上を実現します。このサービスは、製造業の課題を深く理解し、それに対する最適なデジタルソリューションを提供することで、企業が持続的な成長とイノベーションを達成できるようサポートします。
製造業ニュース解説
製造業、主に購買・調達部門にお勤めの方々に向けた情報を配信しております。
新任の方やベテランの方、管理職を対象とした幅広いコンテンツをご用意しております。
お問い合わせ
コストダウンが利益に直結する術だと理解していても、なかなか前に進めることができない状況。そんな時は、newjiのコストダウン自動化機能で大きく利益貢献しよう!
(β版非公開)