- お役立ち記事
- Safety Management in Semiconductor Factories and Employee Roles
月間76,176名の
製造業ご担当者様が閲覧しています*
*2025年3月31日現在のGoogle Analyticsのデータより
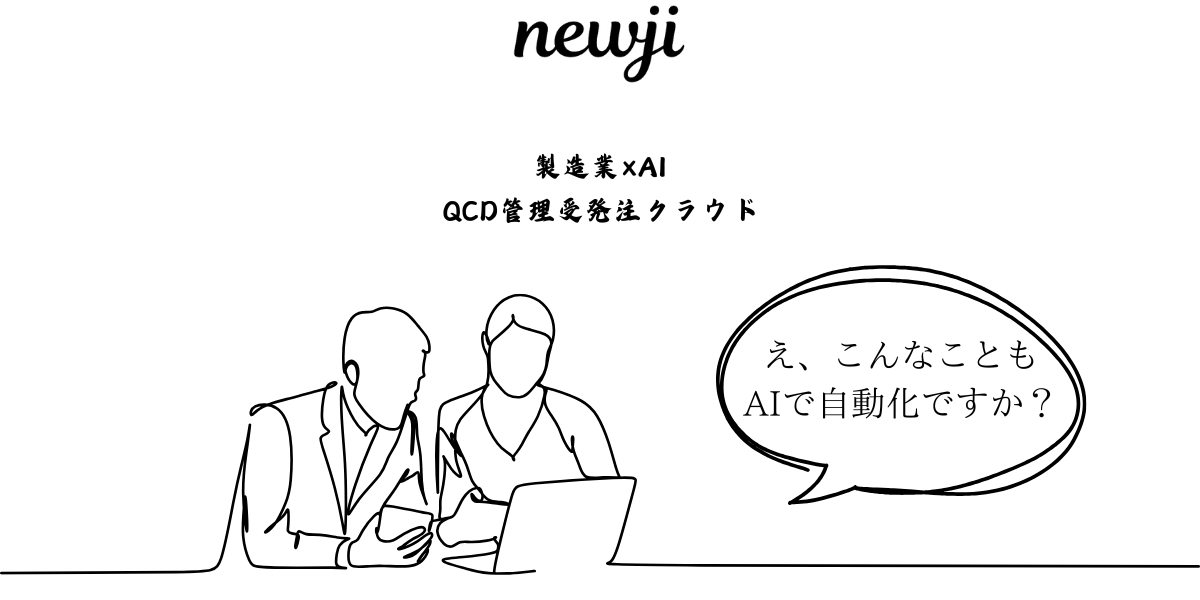
Safety Management in Semiconductor Factories and Employee Roles
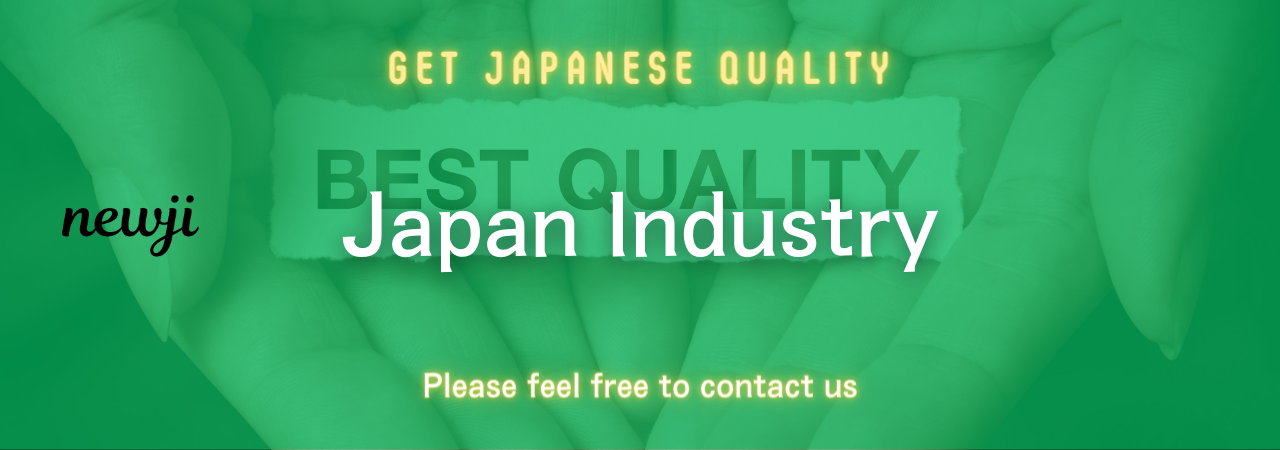
目次
Introduction to Semiconductor Safety
The world of semiconductor manufacturing is intricate and highly technical.
With the increasing demand for semiconductor chips, ensuring the safety and well-being of employees in these factories is paramount.
Effective safety management not only protects workers but also ensures a stable manufacturing process.
Understanding the roles employees play in safety management can lead to a safer and more productive workplace.
Potential Hazards in Semiconductor Factories
Semiconductor factories are bustling hubs of activity with numerous potential hazards.
These hazards can include chemical exposure, electrical risks, and physical dangers.
Employees must be aware of these risks to take proactive measures to mitigate them.
Chemical Exposure
One of the significant risks in semiconductor manufacturing is exposure to hazardous chemicals used in the production process.
These chemicals, such as solvents and acids, are essential but dangerous if not handled properly.
Workers must use personal protective equipment (PPE) and follow strict protocols to minimize exposure.
Electrical Risks
The intricate equipment and machinery used in semiconductor production require significant electrical power.
This presents risks of electric shocks or even fires if mishandled.
Employees need regular training to safely operate and maintain this equipment.
Physical Dangers
With the constant movement of machines and materials, physical safety is a concern in semiconductor factories.
Injuries from machinery or accidental slips and falls can happen if safety protocols are not followed.
Routine safety checks and awareness can drastically reduce these risks.
Employee Roles in Safety Management
Safety in the semiconductor industry isn’t solely the responsibility of the management.
All employees play a vital role in ensuring their safety and that of their colleagues.
Understanding these roles is crucial to establish a safe working environment.
Management’s Role
Management’s primary responsibility is to set comprehensive safety protocols and ensure compliance.
They facilitate the necessary training and oversee the implementation of safety measures.
Creating a culture that prioritizes safety starts from the top, with management demonstrating commitment to all safety initiatives.
Supervisors’ Responsibilities
Supervisors act as the bridge between management and the workforce.
They must ensure that safety protocols are clearly communicated and adhered to by the team.
Supervisors also conduct routine safety audits and respond to any safety-related incidents promptly.
Employees’ Involvement
Every employee has the responsibility to follow safety guidelines and protocols without exception.
They must wear appropriate PPE and report any safety hazards immediately.
Active participation in safety training sessions is necessary to stay updated on the best safety practices.
Implementing Effective Safety Measures
For semiconductor factories to maintain an optimal level of safety, several measures should be implemented.
Regular Training Programs
Ongoing safety training programs for employees are essential.
These programs should cover handling chemicals, operating machinery safely, and emergency response procedures.
Regular refresher courses ensure that all employees are knowledgeable about the latest safety practices.
Comprehensive Safety Protocols
Developing detailed safety protocols tailored to the specific factory environment is essential.
These protocols must include guidelines for safe handling of materials, operating equipment, and procedures for dealing with emergencies.
Protocols should be reviewed and updated regularly to reflect any changes in operations or safety standards.
Effective Communication
Clear and open communication is crucial for effective safety management.
Employees should feel comfortable reporting safety issues or suggesting improvements.
Regular meetings can help reinforce safety culture and keep safety discussions ongoing.
Promoting a Culture of Safety
Creating a culture that prioritizes safety involves everyone in the organization, from management to entry-level workers.
Recognizing and rewarding safe behavior can encourage adherence to safety guidelines.
A strong safety culture not only protects employees but also enhances overall productivity and morale.
Leadership Commitment
For a true safety culture to develop, leadership must fully commit to integrating safety into every aspect of operations.
This means not just focusing on compliance but embracing safety as a core value of the organization.
Employee Engagement
Engaging employees in safety initiatives fosters a sense of ownership and accountability.
Encouraging feedback and suggestions from employees can lead to improvements in safety protocols.
Conclusion
Safety management in semiconductor factories is a critical component of successful operations.
By understanding and implementing effective safety protocols and encouraging employee participation in safety measures, semiconductor factories can protect their workers and maintain production efficiency.
Through continuous training, open communication, and a dedicated commitment to safety, everyone plays a crucial role in creating a safe manufacturing environment.
資料ダウンロード
QCD管理受発注クラウド「newji」は、受発注部門で必要なQCD管理全てを備えた、現場特化型兼クラウド型の今世紀最高の受発注管理システムとなります。
ユーザー登録
受発注業務の効率化だけでなく、システムを導入することで、コスト削減や製品・資材のステータス可視化のほか、属人化していた受発注情報の共有化による内部不正防止や統制にも役立ちます。
NEWJI DX
製造業に特化したデジタルトランスフォーメーション(DX)の実現を目指す請負開発型のコンサルティングサービスです。AI、iPaaS、および先端の技術を駆使して、製造プロセスの効率化、業務効率化、チームワーク強化、コスト削減、品質向上を実現します。このサービスは、製造業の課題を深く理解し、それに対する最適なデジタルソリューションを提供することで、企業が持続的な成長とイノベーションを達成できるようサポートします。
製造業ニュース解説
製造業、主に購買・調達部門にお勤めの方々に向けた情報を配信しております。
新任の方やベテランの方、管理職を対象とした幅広いコンテンツをご用意しております。
お問い合わせ
コストダウンが利益に直結する術だと理解していても、なかなか前に進めることができない状況。そんな時は、newjiのコストダウン自動化機能で大きく利益貢献しよう!
(β版非公開)