- お役立ち記事
- “Safety stock optimization”—Inventory levels and risk responses that should be adjusted by the purchasing department
“Safety stock optimization”—Inventory levels and risk responses that should be adjusted by the purchasing department
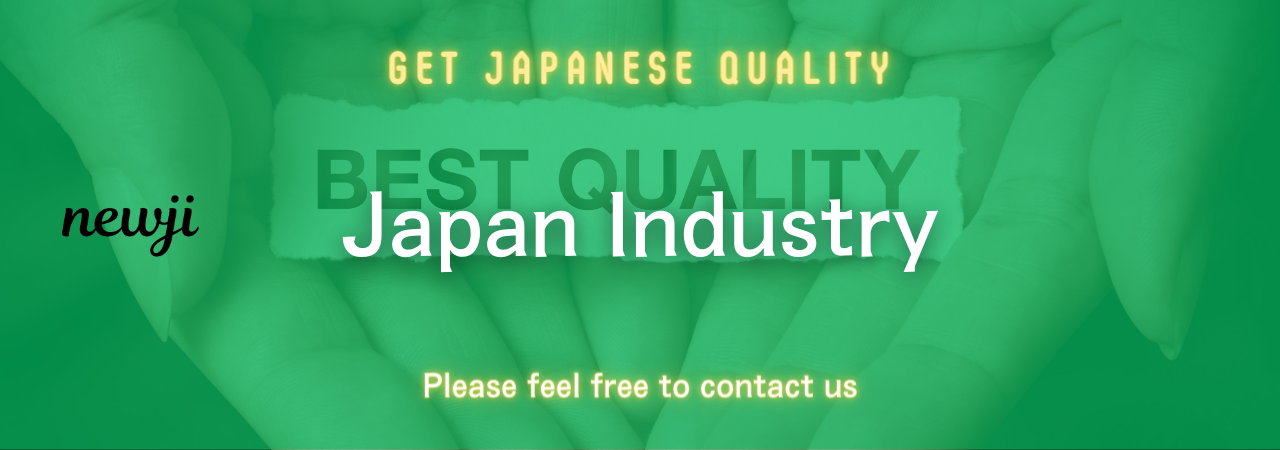
目次
Understanding Safety Stock
Safety stock is a critical component in inventory management.
It acts as a buffer to protect against uncertainties in supply and demand.
These uncertainties can include delays from suppliers, sudden spikes in customer demand, or inaccuracies in demand forecasting.
To optimize safety stock levels, businesses must strike a balance.
If the safety stock is too high, it could lead to excess holding costs and reduced cash flow.
Conversely, if it is too low, the business may face stockouts, leading to lost sales and customer dissatisfaction.
The Role of the Purchasing Department
The purchasing department plays a significant role in managing safety stock.
They are responsible for ensuring that the inventory levels meet the company’s current and anticipated needs.
One of their tasks is to communicate effectively with suppliers to ensure timely deliveries.
This communication helps in reducing lead time variability, thus minimizing the need for high safety stock levels.
Moreover, purchasing departments often analyze demand forecasts and adjust orders accordingly.
This proactive approach contributes to maintaining optimal inventory levels.
Calculating Safety Stock
Accurate safety stock calculation is vital for optimization.
The calculation considers factors such as lead time variability, demand variability, and the desired service level.
A common formula used is:
Safety Stock = Z-score * Standard deviation of lead time demand
The Z-score corresponds to the desired service level.
A higher service level results in a higher Z-score, which increases the safety stock level.
Calculating standard deviation requires historical data on lead time and demand.
Purchasing departments must regularly review and update these calculations to reflect any changes in supply chain dynamics.
Risk Management and Safety Stock
A well-optimized safety stock is a crucial element of risk management.
It helps businesses mitigate the risks associated with fluctuations in demand and supply disruptions.
When unexpected events occur, such as natural disasters or supply chain interruptions, safety stock acts as a buffer.
It ensures continued operations without immediate impact on the production or sales processes.
Adjusting Safety Stock Levels
Safety stock levels should not remain static.
The purchasing department needs to regularly assess and adjust these levels based on changes in market conditions, supply chain reliability, and business objectives.
For example, during promotional campaigns or seasonal peaks, higher safety stock may be required to meet increased demand.
On the other hand, in times of stable demand with reliable suppliers, the safety stock levels can be adjusted downward.
Tools and Technology in Safety Stock Optimization
Advances in technology have made safety stock optimization more precise.
Inventory management systems and demand forecasting software aid in more accurate predictions of sales patterns and supply chain fluctuations.
These tools provide real-time data and analytics capabilities, allowing for quicker and more informed decision-making.
The purchasing department should leverage these technologies to refine safety stock levels continually.
The Impact of Safety Stock on Business Performance
Optimizing safety stock directly impacts a company’s overall performance.
Efficient inventory management can lead to cost savings, higher customer satisfaction, and improved cash flow.
When a business avoids stockouts, it enhances its reputation and retains customer trust.
Conversely, reducing excess inventory reduces storage costs and waste, positively affecting the bottom line.
Conclusion
Safety stock optimization is a crucial strategy for any business looking to improve its inventory management.
By understanding the dynamics of supply and demand, actively engaging with suppliers, and utilizing advanced technology, purchasing departments can effectively adjust safety stock levels.
In turn, this optimization supports the company’s risk management strategies and enhances overall business performance.
Regular assessments and adjustments to safety stock ensure the company remains agile and responsive in a fluctuating market environment.
資料ダウンロード
QCD調達購買管理クラウド「newji」は、調達購買部門で必要なQCD管理全てを備えた、現場特化型兼クラウド型の今世紀最高の購買管理システムとなります。
ユーザー登録
調達購買業務の効率化だけでなく、システムを導入することで、コスト削減や製品・資材のステータス可視化のほか、属人化していた購買情報の共有化による内部不正防止や統制にも役立ちます。
NEWJI DX
製造業に特化したデジタルトランスフォーメーション(DX)の実現を目指す請負開発型のコンサルティングサービスです。AI、iPaaS、および先端の技術を駆使して、製造プロセスの効率化、業務効率化、チームワーク強化、コスト削減、品質向上を実現します。このサービスは、製造業の課題を深く理解し、それに対する最適なデジタルソリューションを提供することで、企業が持続的な成長とイノベーションを達成できるようサポートします。
オンライン講座
製造業、主に購買・調達部門にお勤めの方々に向けた情報を配信しております。
新任の方やベテランの方、管理職を対象とした幅広いコンテンツをご用意しております。
お問い合わせ
コストダウンが利益に直結する術だと理解していても、なかなか前に進めることができない状況。そんな時は、newjiのコストダウン自動化機能で大きく利益貢献しよう!
(Β版非公開)