- お役立ち記事
- Sales Strategy to Meet New Market Needs: Proposed Introduction of Automated Machining Lines
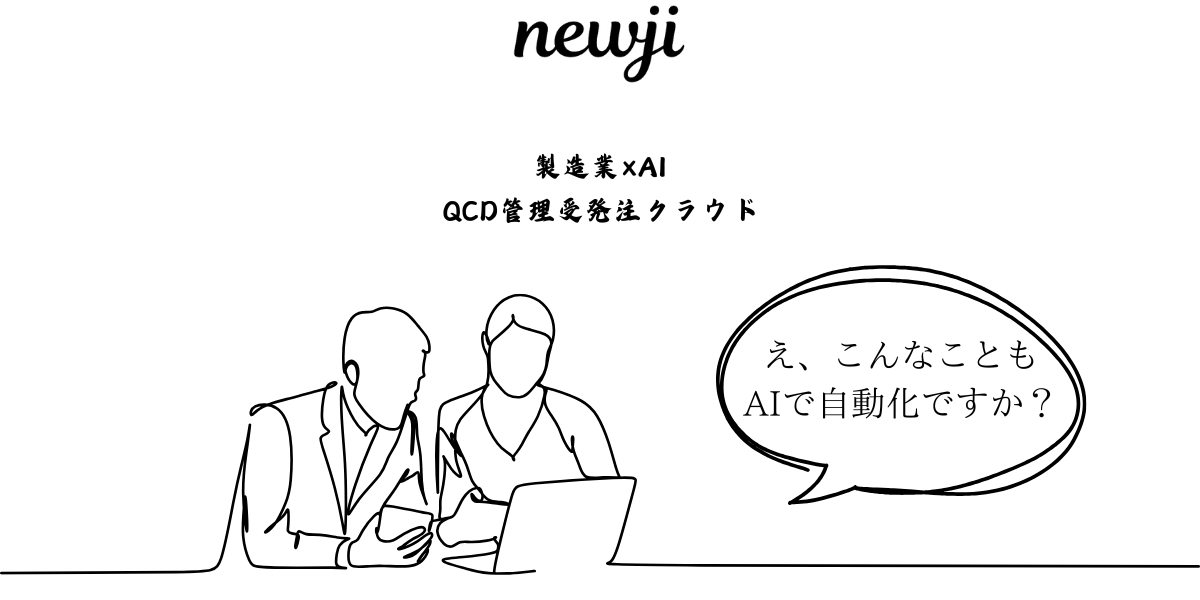
Sales Strategy to Meet New Market Needs: Proposed Introduction of Automated Machining Lines
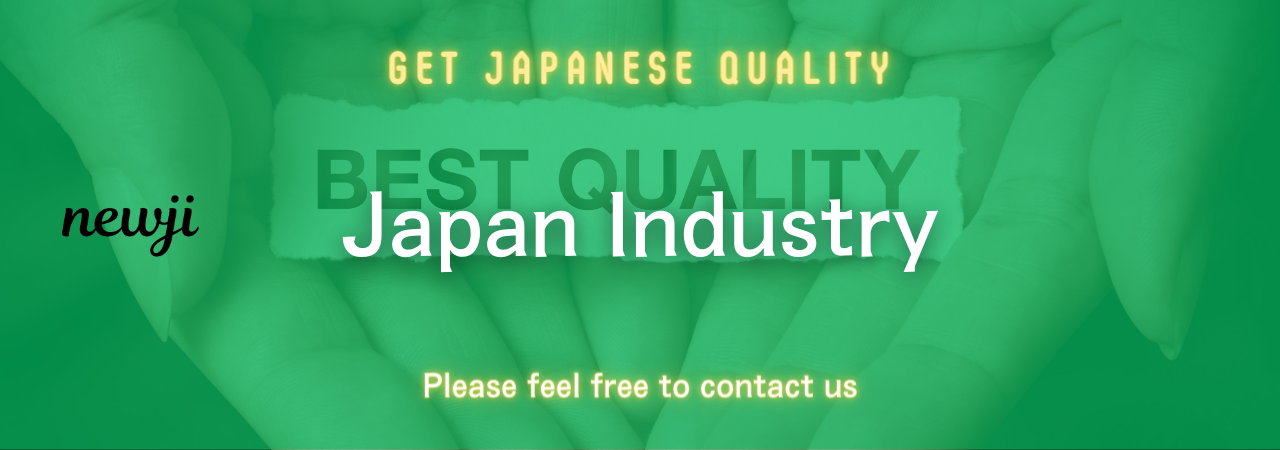
In today’s rapidly evolving market, successful companies often differentiate themselves by quickly adapting to new demands and harnessing the latest technologies.
One such strategy is the introduction of automated machining lines, which are becoming increasingly essential for meeting new market needs.
This article delves into the comprehensive benefits of automated machining lines and how businesses can effectively implement them to stay ahead of the competition.
目次
Understanding Automated Machining Lines
Automated machining lines are advanced manufacturing systems that utilize robots and computer-controlled processes to create products with high precision.
These systems are designed to perform repetitive tasks with exceptional accuracy and consistency.
They integrate software, machinery, and robotic elements to streamline production processes, reduce human error, and increase output efficiency.
Components of an Automated Machining Line
Understanding the key components that comprise these systems is fundamental.
Primary components typically include:
– **CNC (Computer Numerical Control) Machines**: These machines use pre-programmed software to dictate movement and operations, ensuring meticulous precision.
– **Robotic Arms**: They handle tasks like assembly, sorting, and welding.
– **Conveyor Systems**: Transport materials between different production stages, reducing manual handling and increasing process speed.
– **Safety Systems**: Ensuring worker safety with sensors, barriers, and automated shutdowns in case of malfunctions.
– **Software**: Integration software controlling and harmonizing the operations and interactions of all components.
Benefits of Automating Machining Lines
Employing automated machining lines can result in several significant advantages for manufacturers.
Efficiency and Productivity
One of the most notable benefits is the increase in production efficiency.
Automated systems can operate 24/7 without breaks, thereby significantly boosting productivity.
This nonstop operation equates to more products being created in less time, helping businesses meet high consumer demand swiftly.
Cost Savings
While the initial investment in automation technology might appear steep, the long-term cost savings are substantial.
Automating production reduces the reliance on human labor, slashes operational costs, and diminishes waste owing to higher precision.
It also lowers energy consumption due to optimized and streamlined processes.
Quality Consistency
Automated machining lines ensure uniformity and accuracy in product manufacturing.
Unlike human workers, robots and machines do not suffer from fatigue or inconsistencies.
As a result, there is a substantial reduction in defects and a consistent quality of output.
This consistency builds trust and satisfaction among consumers, enhancing brand reputation.
Flexibility
Modern automated systems are designed to be flexible and adaptable.
They can be reprogrammed quickly to handle different tasks and product types, making it easier to respond to market changes.
This flexibility is essential in a dynamic marketplace where consumer preferences and technology evolve rapidly.
Steps to Implement Automated Machining Lines
Transitioning to an automated machining line requires a well-thought-out plan.
Here are essential steps businesses should consider:
Assessing Current Capabilities
Before implementing any new technology, it is crucial to thoroughly assess the current production capabilities and identify areas where automation would be most beneficial.
This involves analyzing existing production bottlenecks, labor-intensive tasks, and quality control challenges.
Setting Clear Objectives
Establishing clear objectives for the automation process is vital.
These might include increasing production speed, reducing costs, or enhancing product quality.
Having concrete goals helps in measuring the success of the automation project and aligning it with the overall business strategy.
Selecting the Right Technology
Choosing the appropriate machinery and software for the specific needs of the business is critical.
This selection process should consider factors such as the type of products being manufactured, production volume, and integration capabilities with existing systems.
Consulting with industry experts and conducting thorough research can assist in making an informed decision.
Training and Development
Even though automation reduces the need for manual labor, it does not eliminate the necessity for a skilled workforce.
Employees must be trained to operate and maintain the new systems.
Investing in training programs prepares the workforce for the transition and mitigates the risk of operational disruptions.
Pilot Testing
Before full-scale implementation, conducting pilot tests is advisable.
These tests help identify potential issues and allow for adjustments without impacting the broader production process.
Pilot testing ensures that the system works efficiently and meets the desired objectives.
Full-Scale Implementation
After successful pilot testing, the next step is to gradually implement the automated systems across the entire production line.
It is crucial to monitor the process closely during this phase and be ready to address any challenges promptly.
Challenges and Solutions
Despite the benefits, the introduction of automated machining lines may come with several challenges.
High Initial Investment
The cost of procuring and installing automated systems can be daunting.
However, businesses can overcome this by exploring financing options, seeking government grants or subsidies for technological advancements, and performing a detailed cost-benefit analysis to justify the investment.
Integration with Existing Systems
Integrating new technology with legacy systems can be challenging.
It requires meticulous planning and possibly partnering with technology vendors who specialize in such integrations.
Upgrading existing infrastructure may also be necessary to ensure compatibility.
Workforce Resistance
Employees may resist automation due to fear of job loss or disruption.
Addressing these concerns through transparent communication, engaging employees in the transition process, and focusing on upskilling and reskilling can mitigate resistance.
The Future of Automated Machining Lines
The future holds immense potential for automated machining lines as they continue to evolve with advancements in robotics, AI, and IoT (Internet of Things).
Upcoming trends may include even greater integration of AI for predictive maintenance, highly autonomous manufacturing units, and enhanced data analytics for real-time process optimization.
As businesses strive to meet new market needs, adopting automated machining lines can pave the way for sustained growth, efficiency, and competitiveness.
Embracing this technology helps manufacturers not only cope with current demands but also position themselves advantageously for future market dynamics.
The shift towards automation is indeed a strategic move to thrive in an increasingly automated and fast-paced world.
資料ダウンロード
QCD調達購買管理クラウド「newji」は、調達購買部門で必要なQCD管理全てを備えた、現場特化型兼クラウド型の今世紀最高の購買管理システムとなります。
ユーザー登録
調達購買業務の効率化だけでなく、システムを導入することで、コスト削減や製品・資材のステータス可視化のほか、属人化していた購買情報の共有化による内部不正防止や統制にも役立ちます。
NEWJI DX
製造業に特化したデジタルトランスフォーメーション(DX)の実現を目指す請負開発型のコンサルティングサービスです。AI、iPaaS、および先端の技術を駆使して、製造プロセスの効率化、業務効率化、チームワーク強化、コスト削減、品質向上を実現します。このサービスは、製造業の課題を深く理解し、それに対する最適なデジタルソリューションを提供することで、企業が持続的な成長とイノベーションを達成できるようサポートします。
オンライン講座
製造業、主に購買・調達部門にお勤めの方々に向けた情報を配信しております。
新任の方やベテランの方、管理職を対象とした幅広いコンテンツをご用意しております。
お問い合わせ
コストダウンが利益に直結する術だと理解していても、なかなか前に進めることができない状況。そんな時は、newjiのコストダウン自動化機能で大きく利益貢献しよう!
(Β版非公開)