- お役立ち記事
- Sandwich Molding Process: A Practical Guide to Multi-Layer Molding
月間76,176名の
製造業ご担当者様が閲覧しています*
*2025年3月31日現在のGoogle Analyticsのデータより
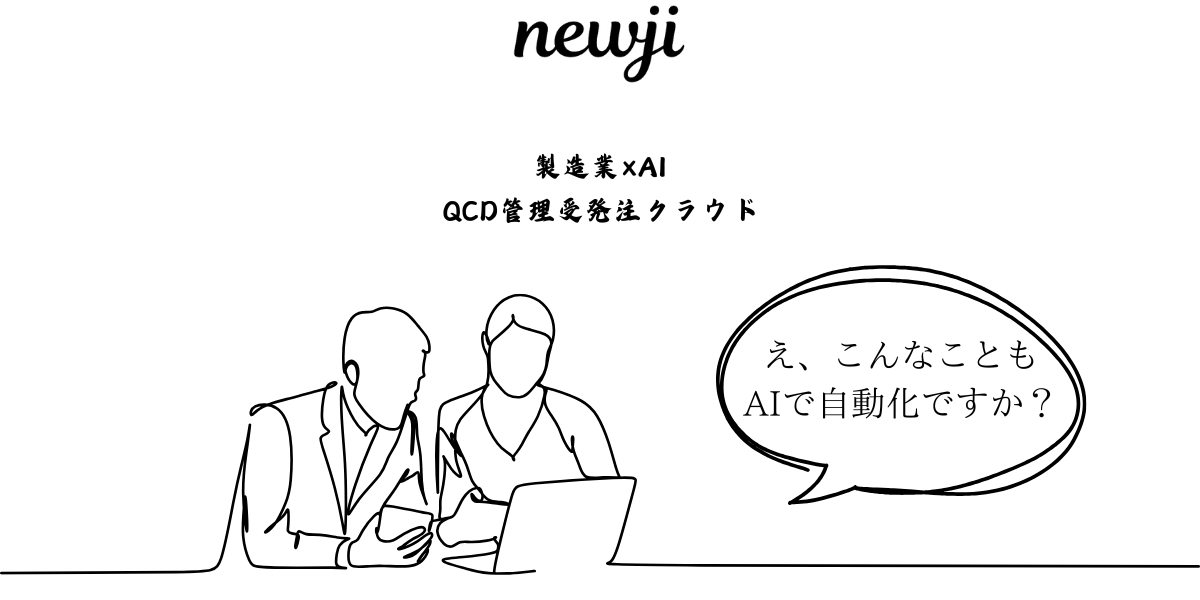
Sandwich Molding Process: A Practical Guide to Multi-Layer Molding
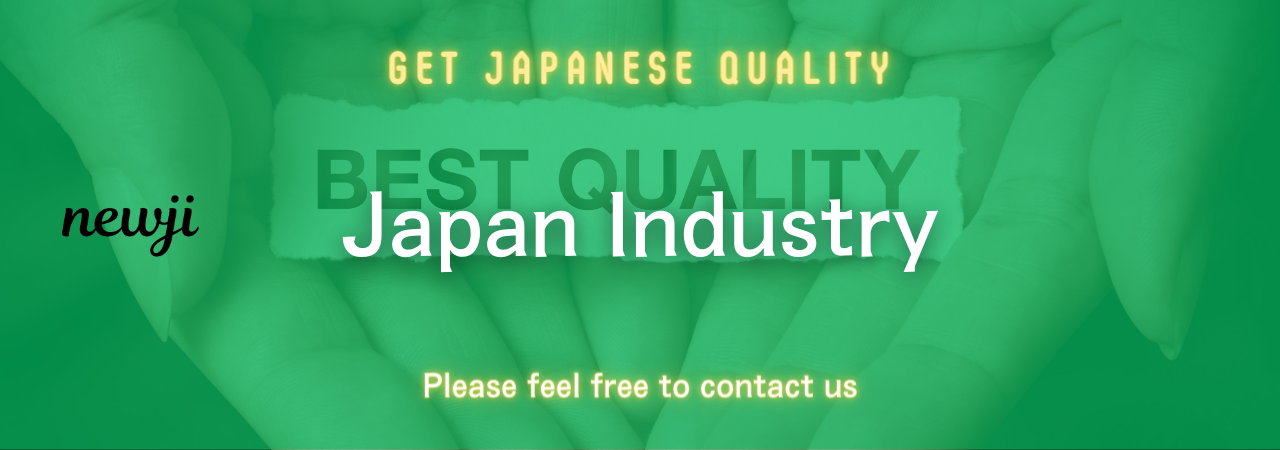
The sandwich molding process is an innovative technique in the field of plastic manufacturing. It allows for the production of multi-layered plastic products that boast improved mechanical properties and cost efficiencies. This article will take an in-depth look at the sandwich molding process, highlighting its benefits, applications, and the steps involved. This guide aims to provide clarity for anyone interested in understanding this advanced manufacturing method.
目次
Introduction to Sandwich Molding
At its core, sandwich molding involves creating a product with multiple layers of different materials. It’s named “sandwich” because the process typically involves a core layer of less expensive or recycled material sandwiched between two outer layers of higher-quality material.
This method can produce items with enhanced strength, reduced weight, or distinct surface qualities.
By optimizing material usage, sandwich molding significantly reduces manufacturing costs while maintaining or even improving product quality.
Benefits of Sandwich Molding
Material Efficiency
One of the primary benefits of sandwich molding is material efficiency.
By using a less expensive material for the core, manufacturers can reduce the amount of more costly outer materials.
This not only cuts manufacturing costs but also maximizes the usage of recycled materials, contributing to environmental sustainability.
Enhanced Product Strength
Sandwich-molded products can show improved mechanical properties. The combination of different materials allows for a final product that might be stronger, lighter, or more flexible than one made entirely from a single material. This enhancement is especially useful in industries that require strong, durable products, such as automotive and construction.
Cost Savings
By reducing the quantity of high-quality materials required, sandwich molding can lead to significant cost savings. Additionally, the use of recycled or cheaper materials for the core can further bring down production expenses. This cost efficiency makes it an attractive option for manufacturers aiming to maintain competitive pricing.
Applications of Sandwich Molding
Automotive Industry
The automotive industry extensively uses sandwich molding to produce lightweight yet strong components. Car manufacturers seek every possible method to reduce the vehicle’s weight to improve fuel efficiency and performance. Using sandwich molding, parts like dashboards, door panels, and other interior components can be produced with lighter core materials without compromising on strength or appearance.
Packaging
In the packaging industry, sandwich molding offers a way to create strong, lightweight packaging products. This method is ideal for producing items such as protective packaging for electronic devices, where weight is a significant consideration. Moreover, the outer layers can be customized to provide a high-quality finish, improving the product’s visual appeal.
Construction
In construction, sandwich-molded materials are used for insulation panels, structural components, and other elements requiring strength and durability. These materials are beneficial in creating energy-efficient buildings, as the multilayer composition can enhance thermal insulation properties.
Consumer Goods
From household items to sports equipment, sandwich molding finds widespread application in producing consumer goods. Manufacturers can design products that are not only lightweight and durable but also aesthetically pleasing. This versatility makes sandwich molding an excellent choice for a variety of consumer markets.
The Sandwich Molding Process
Mold Preparation
The first step in sandwich molding involves preparing the mold. The mold must be designed to accommodate the multi-layer structure. It should include channels for injecting both core and skin materials. Proper mold design is crucial for ensuring even distribution of materials and avoiding defects in the final product.
Material Selection
Selecting the right materials is paramount in sandwich molding. The core material is typically chosen based on cost and mechanical properties, while the outer layers are selected for their surface quality and strength. Common choices include polyolefins for the core and high-strength polymers like ABS or polycarbonate for the outer layers.
Injection of Core Material
Once the mold is ready, the injection process begins. The core material is injected into the mold first. This material fills the mold cavity, forming the base structure of the product. The core material is usually injected at a lower pressure, allowing it to flow and fill the mold properly.
Injection of Skin Material
After the core material is in place, the outer layer or skin material is injected. This material is injected at a higher pressure to ensure it encapsulates the core entirely. The higher pressure helps achieve a smooth and uniform surface, critical for the aesthetic and functional quality of the final product.
Cooling and Demolding
Following the injection of both materials, the mold is cooled to solidify the product. The cooling process must be even to prevent warping or other defects. Once the product has sufficiently cooled, it can be demolded. Careful handling during this step ensures that the finished product maintains its intended shape and quality.
Quality Control in Sandwich Molding
Quality control is crucial in the sandwich molding process to ensure that the final products meet the required specifications. Regular inspections and tests are conducted to check for defects, such as warping, surface blemishes, or incomplete filling. Advanced techniques, like ultrasonic testing or X-ray inspection, may be used to verify the integrity of the product’s inner core and outer layers.
Consistency Checks
Consistent thickness and uniform material distribution are vital factors in ensuring product quality. Variations can lead to weaknesses or defects in the final product. Regular checks should be performed to guarantee uniformity across the batch.
Mechanical Testing
Mechanical tests, such as tensile strength, flexibility, and impact resistance, are performed to ensure that the product meets the required performance criteria. These tests help to verify that the sandwich molding process has successfully enhanced the product’s mechanical properties as intended.
Conclusion
The sandwich molding process offers a practical solution for producing high-quality, cost-effective, multi-layer plastic products. Its benefits extend across various industries, from automotive to consumer goods, thanks to its ability to combine different materials efficiently.
Through careful planning, material selection, and rigorous quality control, manufacturers can leverage sandwich molding to deliver products that meet modern manufacturing demands for efficiency, strength, and cost-effectiveness. Understanding this process brings forth numerous opportunities and offers a competitive edge in producing advanced plastic components.
資料ダウンロード
QCD管理受発注クラウド「newji」は、受発注部門で必要なQCD管理全てを備えた、現場特化型兼クラウド型の今世紀最高の受発注管理システムとなります。
ユーザー登録
受発注業務の効率化だけでなく、システムを導入することで、コスト削減や製品・資材のステータス可視化のほか、属人化していた受発注情報の共有化による内部不正防止や統制にも役立ちます。
NEWJI DX
製造業に特化したデジタルトランスフォーメーション(DX)の実現を目指す請負開発型のコンサルティングサービスです。AI、iPaaS、および先端の技術を駆使して、製造プロセスの効率化、業務効率化、チームワーク強化、コスト削減、品質向上を実現します。このサービスは、製造業の課題を深く理解し、それに対する最適なデジタルソリューションを提供することで、企業が持続的な成長とイノベーションを達成できるようサポートします。
製造業ニュース解説
製造業、主に購買・調達部門にお勤めの方々に向けた情報を配信しております。
新任の方やベテランの方、管理職を対象とした幅広いコンテンツをご用意しております。
お問い合わせ
コストダウンが利益に直結する術だと理解していても、なかなか前に進めることができない状況。そんな時は、newjiのコストダウン自動化機能で大きく利益貢献しよう!
(β版非公開)