- お役立ち記事
- Search and proposal of metal wire material that can be microfabricated
月間77,185名の
製造業ご担当者様が閲覧しています*
*2025年2月28日現在のGoogle Analyticsのデータより
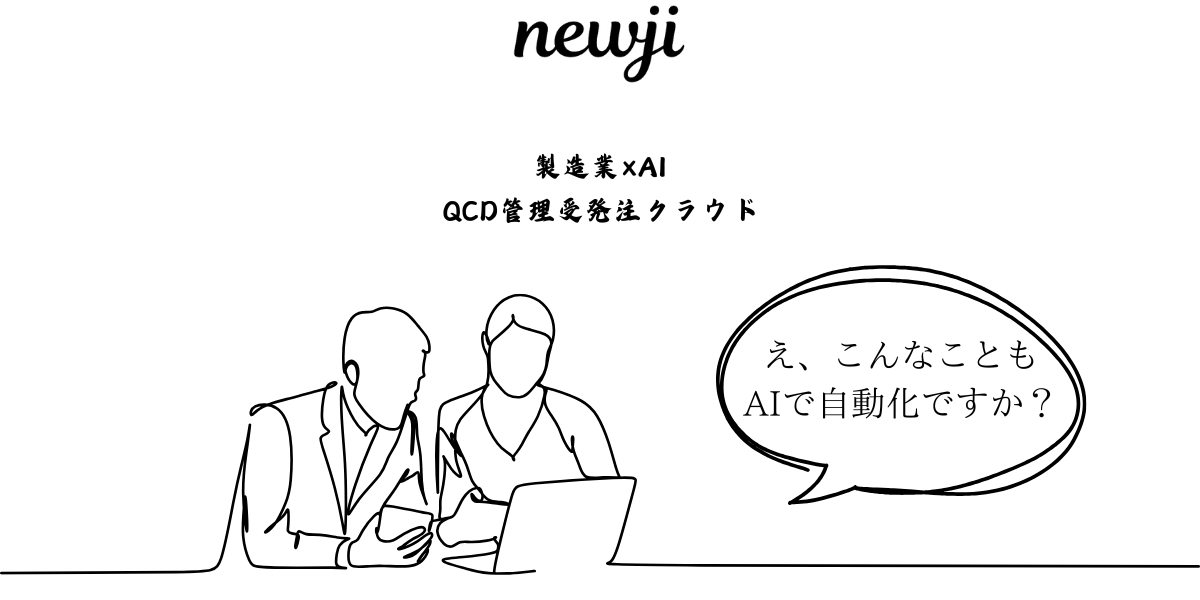
Search and proposal of metal wire material that can be microfabricated
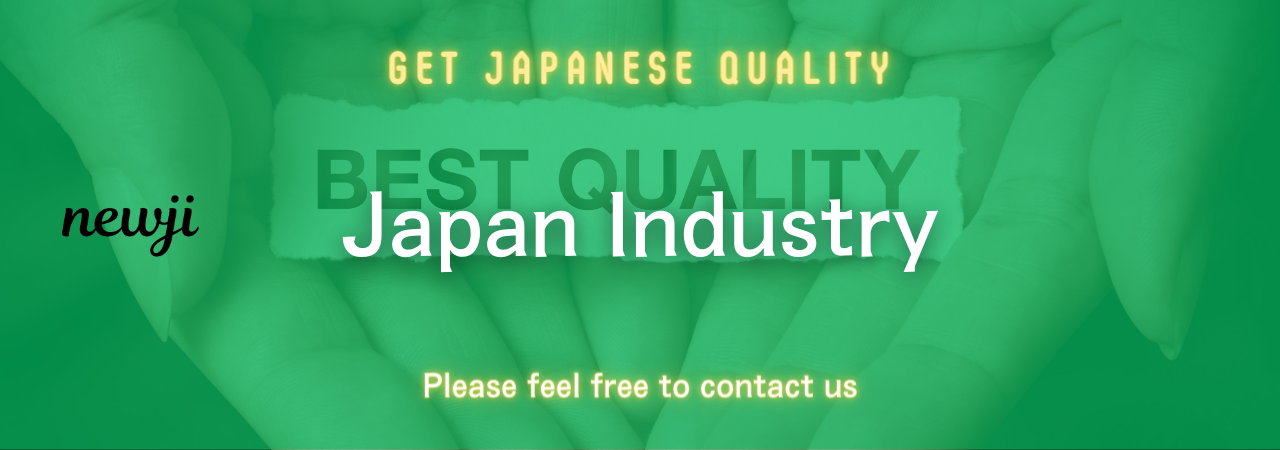
目次
Understanding the Importance of Metal Wire Materials
In the world of material science, discovering and utilizing materials that can be precisely shaped and fabricated at a micro level is crucial for advancing technology and innovation.
One such material often sought after is metal wire.
These materials are key components in developing electronics, medical devices, and numerous other applications that depend on compact and efficient design.
Being able to microfabricate metal wire materials opens up a world of possibilities.
As technology advances, the need for smaller components increases.
Electronics and medical equipment, for example, require intricate, compact parts that can perform efficiently without taking up much space.
Characteristics of Ideal Metal Wire Materials for Microfabrication
When searching for the perfect metal wire material for microfabrication, several characteristics make them suitable for various applications.
Firstly, the wire must exhibit excellent conductivity if it is to be used in electronics.
This means the material should allow electricity to flow through it with minimal resistance.
Copper and silver, for instance, are renowned for their superb conductivity.
However, the choice might change depending on specific needs and compatibility with other materials.
Durability is another vital characteristic.
A microfabricated metal wire should withstand different environmental conditions and mechanical stress without losing integrity.
This ensures that the devices using such materials are reliable and have a long lifespan.
Additionally, the material should be flexible enough to endure bending or twisting without breaking.
This flexibility is particularly important in applications like wearable technology or medical devices that need to conform to different shapes.
Microfabrication Techniques for Metal Wire Materials
Achieving the desired microfabrication of metal wires involves utilizing advanced techniques that allow precise shaping and structuring.
One of the most common methods is photolithography.
This technique uses light to transfer patterns onto a photosensitive material, which can then be etched to form detailed metal wire structures.
Photolithography is often favored for its precision and the ability to create intricate patterns over large surfaces.
Another prominent method is laser cutting, where lasers are used to slice through metals with high precision.
Laser cutting can achieve fine details and is suitable for customization since it can be adjusted to create different shapes and sizes.
However, it requires precise control to ensure high-quality results.
Chemical etching is another alternative.
This process involves using chemicals to remove unwanted parts of the metal wire, leaving behind the desired pattern or shape.
Chemical etching can be very effective for thin wires, allowing for complex designs.
It is important to choose the right technique depending on the specifics of the project, including the type of metal involved and the level of precision required.
Applications of Microfabricated Metal Wire Materials
The ability to microfabricate metal wire materials has led to significant advancements across various industries.
In the medical field, microfabricated wires are used to create stents and catheters, essential for minimally invasive procedures.
These applications require precise, reliable, and biocompatible materials.
Moreover, such wires are instrumental in creating implants that must work seamlessly within the human body.
Within electronics, microfabricated wires have revolutionized the development of PCBs (Printed Circuit Boards) and connectors.
The reduced size and increased efficiency of electronic components have made devices more compact while enhancing their performance capabilities.
Technological advancements like smartphones, smartwatches, and other wearables heavily rely on these microfabricated components.
In the automotive sector, microfabricated wires aid in producing sensors and control systems used in modern vehicles, helping improve safety, efficiency, and functionality.
Additionally, aerospace technology benefits from microfabricated wires, where weight, space, and reliability are critical factors.
Future Prospects and Challenges
The field of microfabrication continues to evolve, with researchers working diligently to uncover new materials and technologies that further push the boundaries of what’s possible.
One area of exploration involves finding sustainable metal wire materials.
As industries move towards eco-friendly solutions, there’s a growing interest in developing materials that meet high-performance standards without negatively impacting the environment.
The integration of nanotechnology with metal wire materials presents another promising future direction.
Nanotechnology could allow for even smaller and more efficient components, opening up new application possibilities.
However, these advancements come with challenges, such as ensuring cost-effectiveness and overcoming technical limitations related to manufacturing at such small scales.
Another challenge is maintaining the balance between size reduction and maintaining or even enhancing performance.
Innovations must not result in compromised durability or functionality, which requires ongoing research and development.
Conclusion
The search and proposal of metal wire materials that can be microfabricated hold immense significance for various industries.
With meticulous selection based on characteristics like conductivity, durability, and flexibility, and by employing advanced microfabrication techniques, these wires can meet the needs of modern technologies.
The wide range of applications, coupled with the potential for future innovations, underscores the critical role played by microfabricated metal wire materials in shaping our technological landscape.
資料ダウンロード
QCD管理受発注クラウド「newji」は、受発注部門で必要なQCD管理全てを備えた、現場特化型兼クラウド型の今世紀最高の受発注管理システムとなります。
ユーザー登録
受発注業務の効率化だけでなく、システムを導入することで、コスト削減や製品・資材のステータス可視化のほか、属人化していた受発注情報の共有化による内部不正防止や統制にも役立ちます。
NEWJI DX
製造業に特化したデジタルトランスフォーメーション(DX)の実現を目指す請負開発型のコンサルティングサービスです。AI、iPaaS、および先端の技術を駆使して、製造プロセスの効率化、業務効率化、チームワーク強化、コスト削減、品質向上を実現します。このサービスは、製造業の課題を深く理解し、それに対する最適なデジタルソリューションを提供することで、企業が持続的な成長とイノベーションを達成できるようサポートします。
製造業ニュース解説
製造業、主に購買・調達部門にお勤めの方々に向けた情報を配信しております。
新任の方やベテランの方、管理職を対象とした幅広いコンテンツをご用意しております。
お問い合わせ
コストダウンが利益に直結する術だと理解していても、なかなか前に進めることができない状況。そんな時は、newjiのコストダウン自動化機能で大きく利益貢献しよう!
(β版非公開)