- お役立ち記事
- Searching for mass production destinations for large injection molding: How to optimize injection molding and build a mass production system
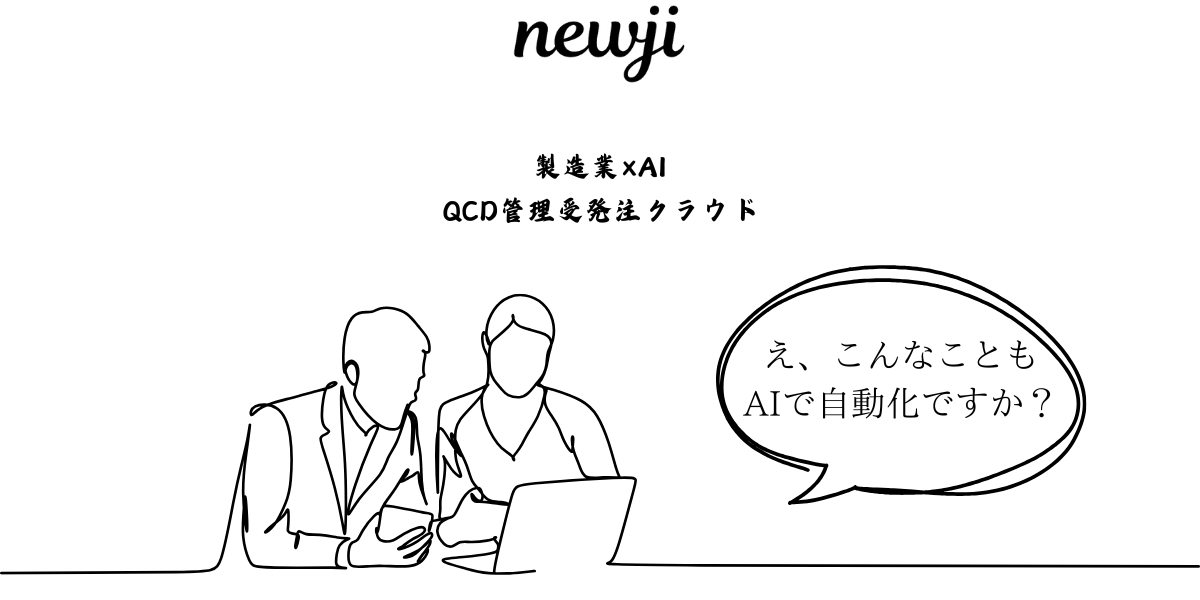
Searching for mass production destinations for large injection molding: How to optimize injection molding and build a mass production system
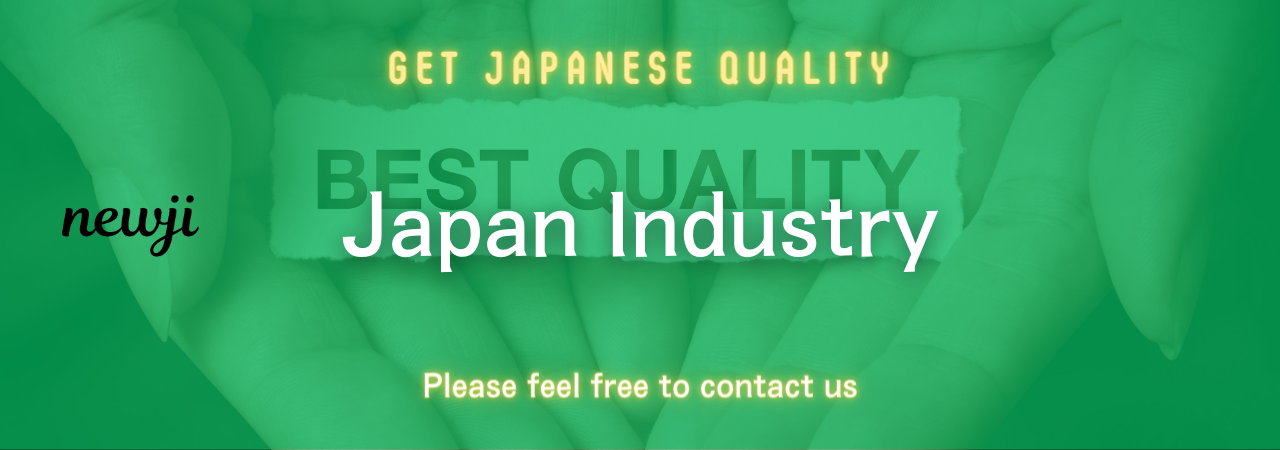
目次
Understanding Large Injection Molding
Injection molding is a popular manufacturing process used for producing parts by injecting molten material into a mold.
It is widely recognized for its ability to mass-produce items with precision and efficiency.
When we talk about large injection molding, we refer to the production of bigger items or parts in significant quantities.
This process involves a higher degree of complexity and requires more advanced machinery and techniques.
To optimize this process, manufacturers must focus on several key areas: the quality of the molds, the materials used, and the efficiency of the production system.
The Importance of Quality Molds
In large injection molding, the quality of the mold is crucial.
A well-designed and constructed mold ensures that each part conforms to the desired specifications.
Any flaws or inaccuracies in the mold design can lead to defects in the finished product, which can be costly.
Investing in high-quality molds not only improves product quality but also extends the mold’s lifespan, reducing the need for frequent replacements.
This, in turn, contributes to a more efficient mass production system.
Choosing the Right Material
Selecting the appropriate material for large injection molding is critical for achieving optimal results.
Different materials have varying properties and behaviors when melted and molded.
To ensure durability and functionality, manufacturers must choose materials that are compatible with the intended use of the final product.
Common materials used in injection molding include thermoplastics, thermosets, and elastomers.
Each material offers unique advantages, so understanding their characteristics allows manufacturers to make informed decisions that enhance the production process.
Optimizing the Injection Molding Process
Optimizing the injection molding process for large-scale production involves several strategies.
One crucial aspect is process consistency.
Maintaining consistent temperatures, pressures, and cycle times ensures uniformity across all produced items.
Automation plays a vital role here, as it minimizes human error and increases the speed and reliability of the production process.
Additionally, regular maintenance of machinery helps in keeping the production line running smoothly, avoiding costly downtimes.
Enhancing Production Efficiency
Manufacturers strive for high efficiency when setting up a mass production system for large injection molding.
Lean manufacturing techniques are often employed to eliminate waste and improve productivity.
Setting up an efficient workflow involves optimizing layout and logistics, reducing the distance materials travel between each stage of production.
Furthermore, constantly monitoring key performance indicators (KPIs) helps in identifying areas for improvement.
By analyzing these metrics, manufacturers can implement changes that enhance overall efficiency and output.
The Role of Technology
Technology significantly influences the optimization of the injection molding process.
Advanced software solutions are now available to simulate the molding process before production begins.
These simulations predict potential issues and allow for adjustments to improve the mold design and process parameters.
Technological advancements also encourage the use of smart machines equipped with sensors and feedback systems, providing real-time data on machine performance.
Such innovations facilitate proactive maintenance and adjustments, ensuring that production systems remain at peak efficiency.
Building a Mass Production System
Establishing a mass production system for large injection molding involves strategic planning and organization.
Manufacturers must consider not only the technical aspects but also the logistics, market demands, and regulatory requirements.
Collaborating with experienced professionals during the planning phase can streamline the process, reducing potential obstacles that could hinder production.
Logistical Considerations
Logistics play a crucial role in establishing a mass production system.
Key factors include transportation, inventory management, and supply chain coordination.
An efficient supply chain ensures that raw materials are readily available, minimizing delays in production.
Warehousing solutions must also be considered to store finished products before distribution.
By addressing these logistical concerns, manufacturers can build a robust production system that meets market demands efficiently.
Adapting to Market Demands
Understanding market demands is essential when setting up a mass production system.
Manufacturers must be agile and responsive to changes in consumer needs and trends.
This necessitates flexibility in production capabilities, allowing for quick modifications to the molding process or materials used.
Continual research and development help keep the production system aligned with the latest market requirements, ensuring competitiveness and potential expansion into new markets.
Meeting Regulatory Standards
Compliance with regulatory standards is mandatory in the manufacturing industry.
Different industries and regions have specific requirements regarding product safety, quality, and environmental impact.
When building a mass production system, manufacturers must ensure that every stage of the process meets these standards.
Efficient documentation and quality control processes are integral to maintaining compliance and avoiding potential legal issues.
Conclusion
Optimizing large injection molding for mass production involves a comprehensive approach that encompasses quality mold design, proper material selection, and efficient process management.
Technology, logistics, and regulatory compliance also play pivotal roles in building an effective production system.
With careful planning and strategic implementation, manufacturers can achieve high-quality output and meet market demands effectively.
The future of large injection molding holds promising potential for innovation and expansion, paving the way for increased production capabilities across various industries.
資料ダウンロード
QCD調達購買管理クラウド「newji」は、調達購買部門で必要なQCD管理全てを備えた、現場特化型兼クラウド型の今世紀最高の購買管理システムとなります。
ユーザー登録
調達購買業務の効率化だけでなく、システムを導入することで、コスト削減や製品・資材のステータス可視化のほか、属人化していた購買情報の共有化による内部不正防止や統制にも役立ちます。
NEWJI DX
製造業に特化したデジタルトランスフォーメーション(DX)の実現を目指す請負開発型のコンサルティングサービスです。AI、iPaaS、および先端の技術を駆使して、製造プロセスの効率化、業務効率化、チームワーク強化、コスト削減、品質向上を実現します。このサービスは、製造業の課題を深く理解し、それに対する最適なデジタルソリューションを提供することで、企業が持続的な成長とイノベーションを達成できるようサポートします。
オンライン講座
製造業、主に購買・調達部門にお勤めの方々に向けた情報を配信しております。
新任の方やベテランの方、管理職を対象とした幅広いコンテンツをご用意しております。
お問い合わせ
コストダウンが利益に直結する術だと理解していても、なかなか前に進めることができない状況。そんな時は、newjiのコストダウン自動化機能で大きく利益貢献しよう!
(Β版非公開)