- お役立ち記事
- Secrets of contract management and material supply stabilization recommended by the purchasing department
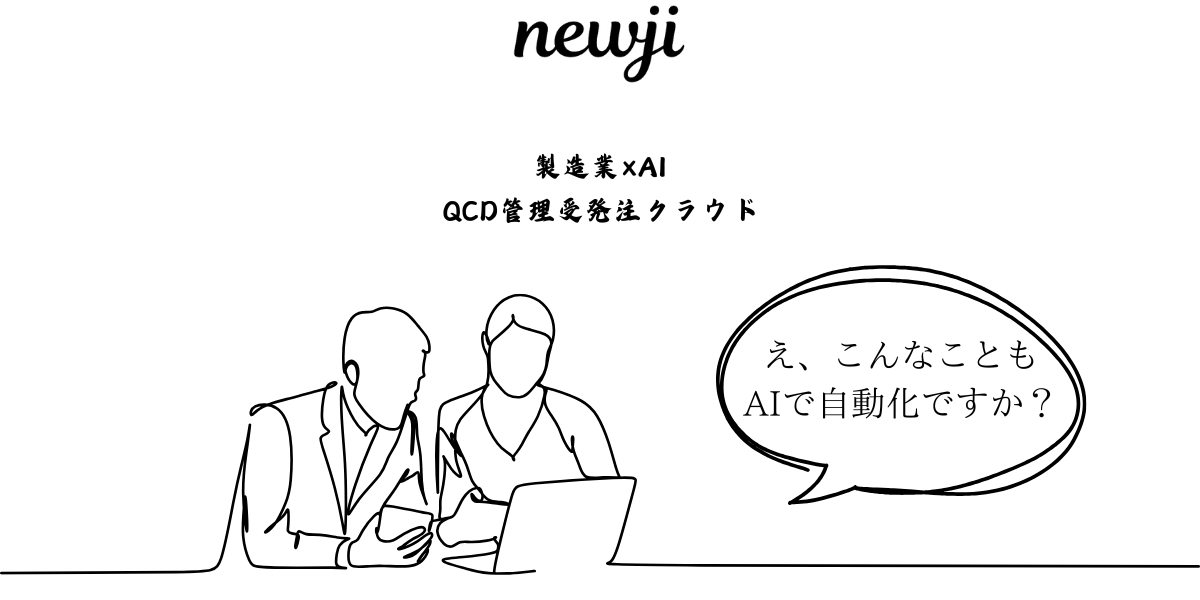
Secrets of contract management and material supply stabilization recommended by the purchasing department
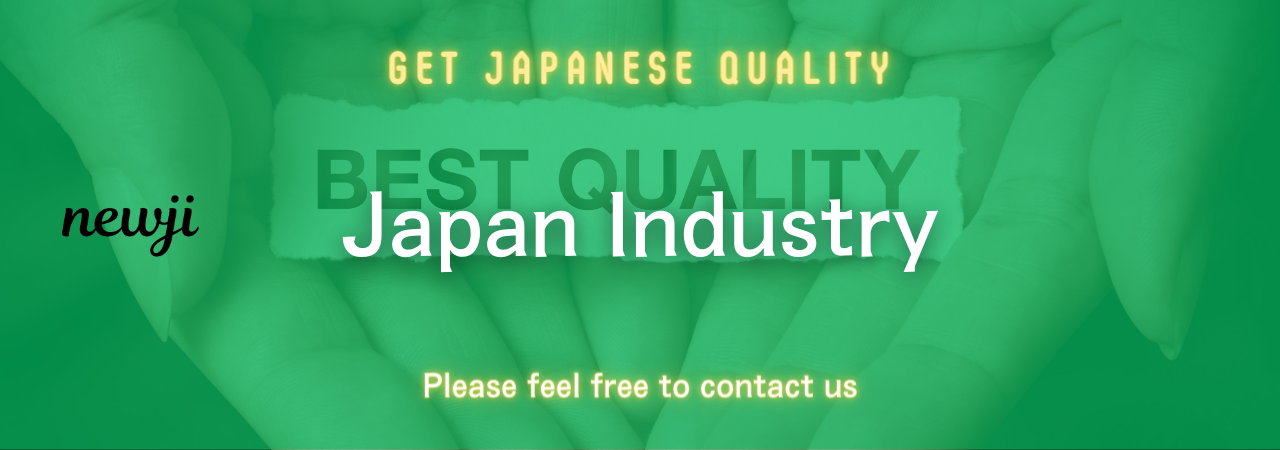
目次
Understanding Contract Management
Contract management is a crucial part of any organization’s procurement strategy.
It involves the active and systematic management of contract creation, execution, and analysis to maximize financial and operational performance.
The purchasing department often spearheads this process, ensuring that contracts align with the organization’s goals and deliver value.
Contracts serve as the foundation for relationships between an organization and its vendors.
They outline expectations, deliverables, and payment terms, reducing ambiguity and providing a clear framework for collaboration.
Effective contract management can significantly impact a company’s bottom line and operational efficiency.
Key Elements of Contract Management
Successful contract management involves several key elements.
Firstly, clear communication must be established from the onset.
This ensures that both parties understand their obligations and expectations.
Secondly, it is essential to identify the specific goals of the contract.
These goals should align with the overall objectives of the organization, providing a roadmap for the relationship between the entity and the vendor.
Thirdly, regular monitoring and evaluation are necessary to track performance.
This helps in identifying any areas of concern and allows for timely intervention.
Finally, contingency planning should not be overlooked.
Having a strategy in place for unforeseen circumstances protects the organization from potential risks and ensures continuity of operations.
The Importance of Supply Stabilization
Material supply stabilization is another vital aspect of the purchasing department’s responsibilities.
It involves ensuring a consistent and reliable flow of materials necessary for business operations.
A stable supply chain helps mitigate risks associated with supply disruptions.
These disruptions can lead to production delays, increased costs, and potential revenue loss.
Thus, maintaining a steady supply of materials is crucial for any organization’s success.
Strategies for Achieving Supply Stabilization
Achieving supply stabilization requires proactive strategies and robust planning.
One effective approach is developing strong relationships with multiple suppliers.
This diversification ensures that the organization is not overly reliant on a single source and can quickly pivot to alternative options if needed.
Another strategy involves implementing a robust inventory management system.
This system helps monitor stock levels, predict demand, and optimize purchasing cycles, thereby preventing stockouts or overstock situations.
Additionally, forecasting and demand planning are critical components of supply stabilization.
By analyzing historical data and market trends, organizations can better anticipate future material needs and adjust their procurement strategies accordingly.
Finally, investing in technology can significantly enhance supply chain visibility and optimization.
Digital tools and platforms provide real-time data and analytics, enabling better decision-making and more efficient management of the supply chain.
The Role of the Purchasing Department
The purchasing department plays a pivotal role in contract management and supply stabilization.
Their expertise ensures that the organization secures the best value from its vendors while maintaining a reliable supply of materials.
Negotiating and Drafting Contracts
One of the primary responsibilities of the purchasing department is to negotiate and draft contracts.
This involves understanding the organization’s needs and collaborating with vendors to develop mutually beneficial agreements.
Negotiation skills are crucial in this process, as they help secure favorable terms and prices.
Purchasing professionals work closely with legal experts to ensure all contract elements comply with regulations and industry standards.
Monitoring Supplier Performance
The purchasing department is also responsible for monitoring supplier performance.
This includes evaluating whether vendors are meeting their contractual obligations and performance metrics.
Regular assessments and feedback sessions with suppliers help maintain strong relationships and continuously improve service delivery.
Implementing Risk Management Practices
Risk management is another critical function of the purchasing department.
By identifying potential risks in the supply chain and developing contingency plans, they help minimize disruption impacts.
This proactive approach enables the organization to swiftly address issues without compromising operational efficiency or financial stability.
Conclusion
Contract management and material supply stabilization are essential components of the purchasing department’s role in any organization.
By fostering strong vendor relationships, implementing effective strategies, and utilizing technology, purchasing professionals can enhance their organization’s operational performance and profitability.
Understanding these concepts can empower organizations to build more resilient supply chains and derive greater value from their contracts, ultimately contributing to long-term success.
資料ダウンロード
QCD調達購買管理クラウド「newji」は、調達購買部門で必要なQCD管理全てを備えた、現場特化型兼クラウド型の今世紀最高の購買管理システムとなります。
ユーザー登録
調達購買業務の効率化だけでなく、システムを導入することで、コスト削減や製品・資材のステータス可視化のほか、属人化していた購買情報の共有化による内部不正防止や統制にも役立ちます。
NEWJI DX
製造業に特化したデジタルトランスフォーメーション(DX)の実現を目指す請負開発型のコンサルティングサービスです。AI、iPaaS、および先端の技術を駆使して、製造プロセスの効率化、業務効率化、チームワーク強化、コスト削減、品質向上を実現します。このサービスは、製造業の課題を深く理解し、それに対する最適なデジタルソリューションを提供することで、企業が持続的な成長とイノベーションを達成できるようサポートします。
オンライン講座
製造業、主に購買・調達部門にお勤めの方々に向けた情報を配信しております。
新任の方やベテランの方、管理職を対象とした幅広いコンテンツをご用意しております。
お問い合わせ
コストダウンが利益に直結する術だと理解していても、なかなか前に進めることができない状況。そんな時は、newjiのコストダウン自動化機能で大きく利益貢献しよう!
(Β版非公開)