- お役立ち記事
- Secrets to Completing Procurement Tasks in 3 Seconds in Manufacturing
Secrets to Completing Procurement Tasks in 3 Seconds in Manufacturing
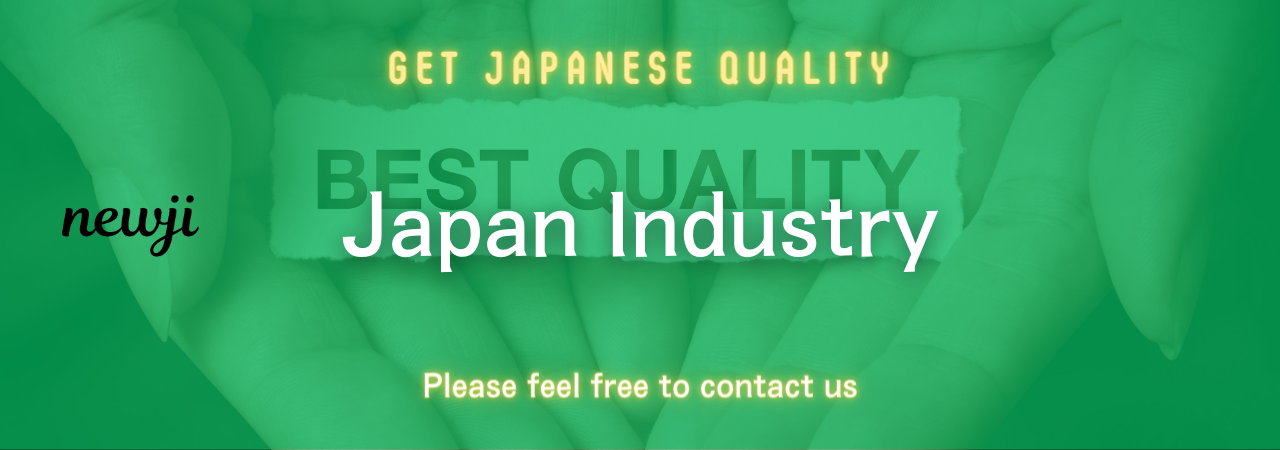
目次
Understanding Procurement in Manufacturing
Procurement is a vital component of the manufacturing process.
It involves sourcing and acquiring the materials necessary to produce goods that meet customer demands.
To ensure smooth operations, it’s crucial to complete procurement tasks efficiently.
To achieve this, manufacturers must first have a thorough understanding of their specific procurement needs.
This involves identifying what materials are needed, how much must be sourced, and when they must arrive to meet production timelines.
The Strategic Role of Procurement
Procurement is not just about purchasing goods and raw materials.
It’s a strategic function that involves selecting the right suppliers, negotiating prices and contracts, and managing relationships with vendors.
Making informed decisions about procurement can help manufacturing businesses save time and money while maintaining quality standards.
To streamline procurement tasks, companies often invest in technologies like enterprise resource planning (ERP) systems.
These systems provide integrated solutions for managing a company’s financials, supply chain, operations, commerce, reporting, manufacturing, and human resource activities.
ERP systems enhance visibility across processes, enabling businesses to quickly adapt to changing markets and demands.
Leveraging Technology for Quick Procurement
In modern manufacturing, technology plays a pivotal role in speeding up procurement tasks.
One of the most effective technologies is automation.
Automation in procurement involves using software to perform routine tasks, such as sending purchase orders, tracking shipments, and managing inventory levels.
For example, automated systems can be set up to trigger a reorder when stock levels reach a predetermined threshold.
This helps in preventing stockouts and ensures that production continues without interruptions.
Automation reduces human error, streamlines processes, and significantly cuts down on time-consuming manual tasks.
Understanding the Importance of Data
Data is king when it comes to completing procurement tasks efficiently.
Analysis of past procurement data can help manufacturers understand patterns and predict future needs.
Tools powered by artificial intelligence (AI) and machine learning (ML) can analyze mountains of data far more quickly than humans can.
These insights can lead to smarter decision-making, better forecasting, and timely procurement actions.
Moreover, data provides valuable insights into supplier performance, allowing manufacturers to identify which suppliers meet quality standards and deliver on time.
This information is critical for maintaining reliable supplier relationships and ensuring a consistent supply of materials.
Developing Strong Supplier Relationships
A solid relationship with suppliers can drastically reduce procurement time.
When manufacturers maintain strong ties with suppliers, they are more likely to benefit from preferential treatment, such as priority delivery or access to limited stock.
Effective communication is key to developing these relationships.
Regular meetings, negotiations, and transparent communication help build trust between manufacturers and suppliers.
This trust can be leveraged in times of need, ensuring that procurement tasks are handled swiftly and efficiently.
Additionally, embracing a partnership approach rather than a transactional one can create a win-win scenario for both parties.
Suppliers who feel valued and understood are more likely to go the extra mile to meet manufacturers’ needs promptly.
Streamlining Internal Processes
The efficiency of procurement tasks is also affected by internal processes.
It’s essential for manufacturers to streamline their internal workflows to ensure quick decision-making.
Reducing bureaucratic hurdles and empowering employees to make informed purchasing decisions can speed up the procurement process.
Training and education should be a priority to ensure that all procurement staff are up-to-date with the latest tools and practices.
Regular workshops and training sessions can enhance skills and encourage a more agile approach to procurement tasks.
Implementing Just-In-Time (JIT) Procurement
Just-In-Time (JIT) procurement is a strategy to improve efficiency and reduce waste by receiving goods only as they are needed in the production process.
This approach helps manufacturers minimize inventory costs and avoid the pitfalls of overstocking, which can tie up valuable capital and storage space.
To successfully implement JIT, manufacturers must have reliable partnerships with suppliers who can deliver materials quickly and consistently.
Additionally, manufacturers need an accurate forecasting system to align procurement schedules with production demands.
Ensuring Quality Control
While speed is important, quality should never be compromised in procurement tasks.
Ensuring that materials meet quality standards is critical in maintaining the integrity of the final product.
Manufacturers can employ quality control measures to check the materials at various stages of procurement.
This might involve inspecting samples before mass orders are made or setting quality benchmarks that suppliers must meet.
By integrating quality control into the procurement process, manufacturers can catch potential issues early and make necessary adjustments to avoid costly rework or product recalls.
Conclusion
The manufacturing industry is fast-paced and competitive.
To succeed, manufacturers must harness the techniques and strategies that allow for rapid completion of procurement tasks.
By leveraging technology, building strong supplier relationships, streamlining internal processes, and ensuring quality, manufacturers can effectively meet their procurement needs in record time.
Ultimately, efficient procurement contributes to the overall success of manufacturing operations, ensuring that businesses remain competitive and profitable in an ever-evolving market.
資料ダウンロード
QCD調達購買管理クラウド「newji」は、調達購買部門で必要なQCD管理全てを備えた、現場特化型兼クラウド型の今世紀最高の購買管理システムとなります。
ユーザー登録
調達購買業務の効率化だけでなく、システムを導入することで、コスト削減や製品・資材のステータス可視化のほか、属人化していた購買情報の共有化による内部不正防止や統制にも役立ちます。
NEWJI DX
製造業に特化したデジタルトランスフォーメーション(DX)の実現を目指す請負開発型のコンサルティングサービスです。AI、iPaaS、および先端の技術を駆使して、製造プロセスの効率化、業務効率化、チームワーク強化、コスト削減、品質向上を実現します。このサービスは、製造業の課題を深く理解し、それに対する最適なデジタルソリューションを提供することで、企業が持続的な成長とイノベーションを達成できるようサポートします。
オンライン講座
製造業、主に購買・調達部門にお勤めの方々に向けた情報を配信しております。
新任の方やベテランの方、管理職を対象とした幅広いコンテンツをご用意しております。
お問い合わせ
コストダウンが利益に直結する術だと理解していても、なかなか前に進めることができない状況。そんな時は、newjiのコストダウン自動化機能で大きく利益貢献しよう!
(Β版非公開)