- お役立ち記事
- Secrets to improving operational efficiency learned from process improvement cases in the manufacturing industry
月間76,176名の
製造業ご担当者様が閲覧しています*
*2025年3月31日現在のGoogle Analyticsのデータより
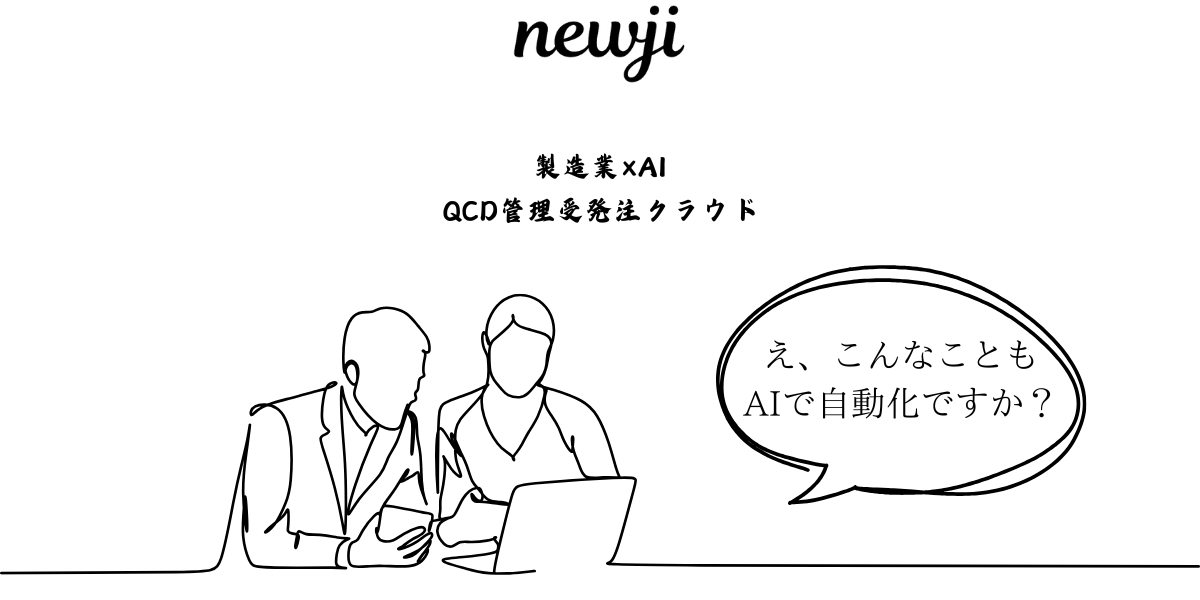
Secrets to improving operational efficiency learned from process improvement cases in the manufacturing industry
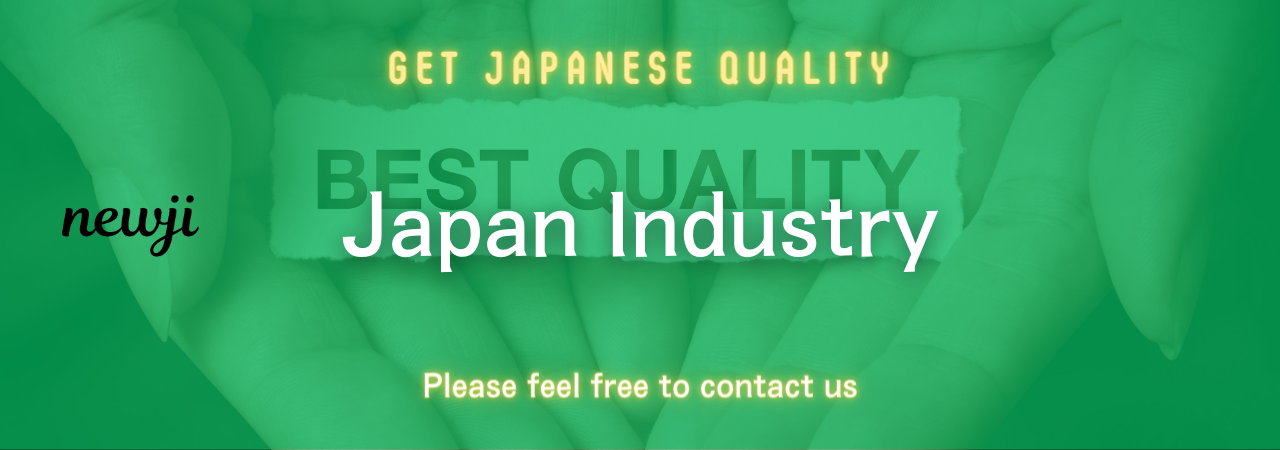
目次
Understanding Operational Efficiency
Operational efficiency is a measure of how well an organization utilizes its resources to produce goods or services.
In the manufacturing industry, improving operational efficiency can lead to reduced costs, increased productivity, and enhanced competitiveness.
This involves optimizing processes, reducing waste, and utilizing resources effectively.
Why Operational Efficiency Matters in Manufacturing
Manufacturing companies face constant pressure to produce high-quality goods at lower costs.
Achieving operational efficiency is crucial because it directly impacts a company’s bottom line, customer satisfaction, and market position.
Efficient operations allow manufacturers to respond swiftly to market changes, meet customer demands, and provide products at competitive prices.
The Role of Process Improvement
Process improvement is a systematic approach to enhancing the efficiency and effectiveness of a company’s operations.
In the manufacturing industry, process improvement often involves reevaluating production processes, eliminating bottlenecks, and implementing new technologies.
By continuously refining processes, manufacturers can achieve smoother operations and better overall performance.
Key Techniques for Process Improvement
There are several proven techniques that manufacturing companies use to enhance their operational efficiency.
Here, we explore some of these methods:
1. Lean Manufacturing
Lean manufacturing focuses on minimizing waste without sacrificing productivity.
The core principles of lean revolve around value creation and eliminating anything that doesn’t contribute to it.
This method can significantly enhance operational efficiency by streamlining processes and optimizing resource utilization.
2. Six Sigma
Six Sigma is a data-driven methodology aimed at improving the quality of processes by identifying and removing causes of defects and minimizing variability.
By employing Six Sigma strategies, manufacturers can reduce errors, improve quality control, and enhance customer satisfaction.
3. Total Quality Management (TQM)
TQM is a holistic approach that involves every member of an organization in the continuous improvement of product quality, customer satisfaction, and productivity.
Incorporating TQM principles in manufacturing ensures that quality is maintained at every stage of production.
4. Automation and Robotics
Automation and the use of robotics in manufacturing help streamline operations, increase speed, and reduce human error.
By integrating advanced technologies, companies can significantly boost efficiency and productivity, ultimately leading to better operational performance.
Real-World Examples of Process Improvement
Let’s look at some real-world examples of how manufacturing companies have improved their operational efficiency through process improvements:
Example 1: Toyota
Toyota is renowned for its efficient production system, known as the Toyota Production System (TPS).
This system incorporates lean manufacturing techniques to eliminate waste, improve quality, and optimize processes.
By focusing on continuous improvement (Kaizen), Toyota has set a global benchmark for operational efficiency in the manufacturing sector.
Example 2: GE Appliances
GE Appliances implemented Lean Six Sigma methodologies to enhance its manufacturing processes.
By focusing on data-driven decision-making and waste reduction, the company managed to improve product quality, reduce costs, and increase productivity.
The integration of these strategies has allowed GE Appliances to remain competitive in a rapidly evolving market.
Example 3: Nike
Nike incorporated advanced automation technologies and robotics to enhance its footwear manufacturing processes.
By reducing reliance on manual labor and optimizing production lines, Nike achieved significant increases in efficiency and production speed.
This shift not only improved their operational capacity but also contributed to time and cost savings.
Steps to Implement Process Improvement
For companies looking to improve their operational efficiency, the following strategic steps are recommended:
Step 1: Analyze Current Processes
Begin by thoroughly examining existing production processes to identify areas of inefficiency.
This step involves collecting data, observing workflows, and consulting with team members.
Step 2: Set Clear Goals
Define clear and achievable goals for what you want to accomplish through process improvement.
Setting targets helps guide the improvement strategy and measure success.
Step 3: Choose the Right Tools and Techniques
Select suitable process improvement methods that align with the company’s goals and industry demands.
This could include lean manufacturing, Six Sigma, automation, or a combination of different strategies.
Step 4: Implement Changes
Take actionable steps to implement the chosen strategies, ensuring that team members are trained and resources are allocated effectively.
Monitor the process closely to ensure smooth transitions and identify any potential challenges.
Step 5: Measure and Adjust
Evaluate the effectiveness of the changes made by measuring results against the goals set.
Be open to making necessary adjustments to optimize processes further and strive for continuous improvement.
Benefits of Improved Operational Efficiency
The benefits of improving operational efficiency extend beyond cost reduction.
They include enhanced productivity, better utilization of resources, improved product quality, and increased customer satisfaction.
Companies that prioritize efficiency are better positioned to adapt to changes in the market and meet customer demands swiftly and effectively.
By learning from successful case studies and implementing proven process improvement methods, manufacturing companies can significantly enhance their operational efficiency.
This not only benefits the organization but also contributes positively to the industry as a whole.
資料ダウンロード
QCD管理受発注クラウド「newji」は、受発注部門で必要なQCD管理全てを備えた、現場特化型兼クラウド型の今世紀最高の受発注管理システムとなります。
ユーザー登録
受発注業務の効率化だけでなく、システムを導入することで、コスト削減や製品・資材のステータス可視化のほか、属人化していた受発注情報の共有化による内部不正防止や統制にも役立ちます。
NEWJI DX
製造業に特化したデジタルトランスフォーメーション(DX)の実現を目指す請負開発型のコンサルティングサービスです。AI、iPaaS、および先端の技術を駆使して、製造プロセスの効率化、業務効率化、チームワーク強化、コスト削減、品質向上を実現します。このサービスは、製造業の課題を深く理解し、それに対する最適なデジタルソリューションを提供することで、企業が持続的な成長とイノベーションを達成できるようサポートします。
製造業ニュース解説
製造業、主に購買・調達部門にお勤めの方々に向けた情報を配信しております。
新任の方やベテランの方、管理職を対象とした幅広いコンテンツをご用意しております。
お問い合わせ
コストダウンが利益に直結する術だと理解していても、なかなか前に進めることができない状況。そんな時は、newjiのコストダウン自動化機能で大きく利益貢献しよう!
(β版非公開)