- お役立ち記事
- Secrets to Improving Surface Finish Quality in Roll Forming
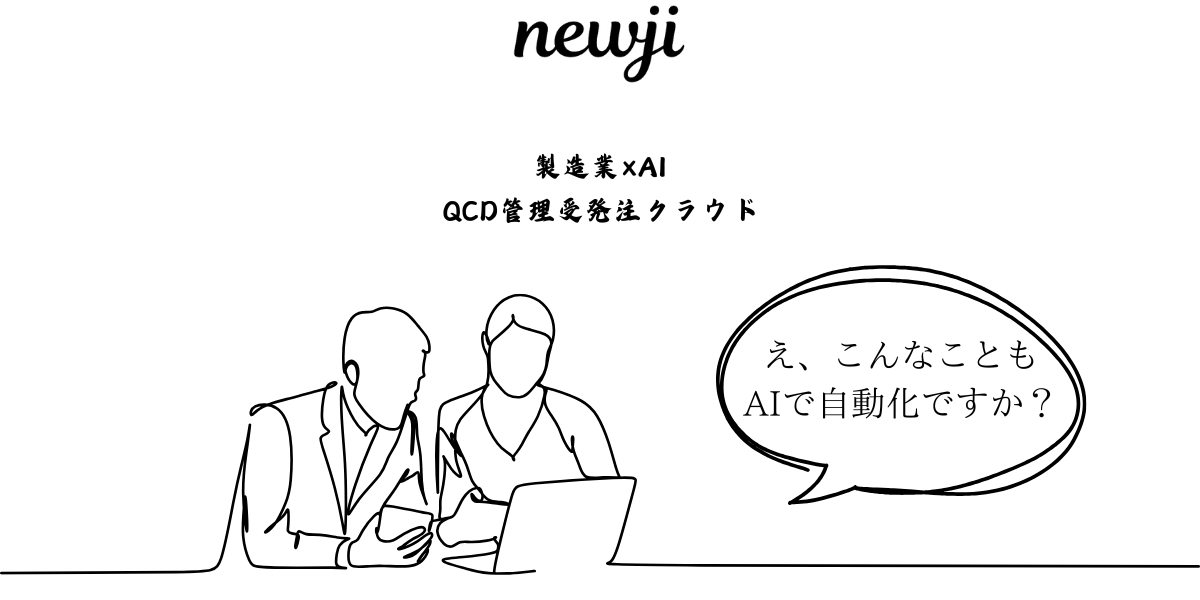
Secrets to Improving Surface Finish Quality in Roll Forming
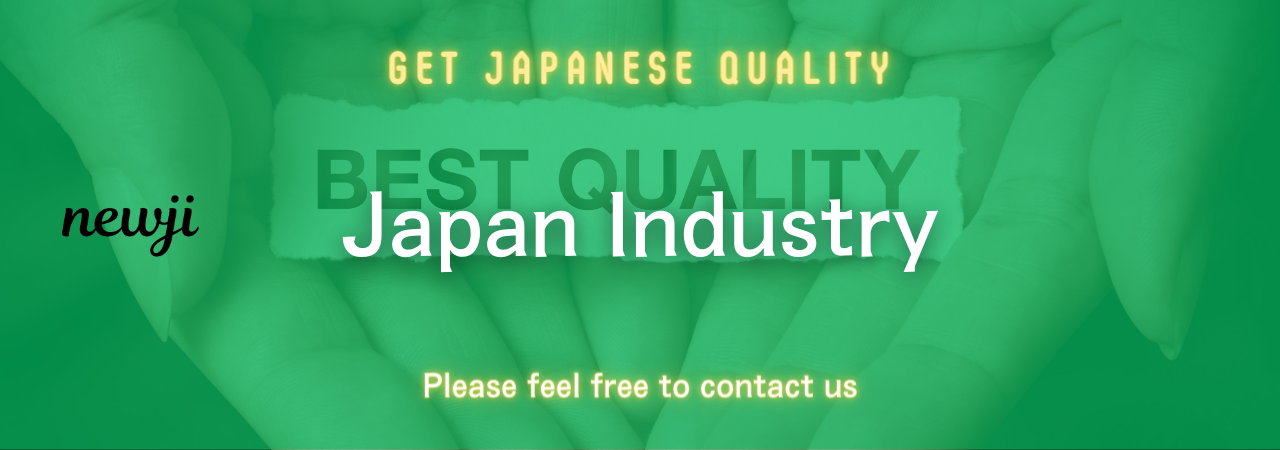
Roll forming is an essential process in manufacturing industries such as automotive, construction, and home appliances.
The quality of the surfaces produced can significantly impact the final product’s aesthetic and functional aspects.
Achieving a high-quality surface finish is not merely a matter of material selection and machine settings; it entails a comprehensive understanding of multiple influencing factors.
目次
Understanding Roll Forming
What is Roll Forming?
Roll forming is a continuous bending operation used to produce long strips of metal, plastic, or other materials.
This process employs rotating rolls to shape the material into desired profiles and shapes.
The primary advantage of roll forming is its ability to create uniform cross-sectional shapes efficiently and consistently while minimizing material wastage.
Why Surface Finish Matters
The surface finish quality in roll forming is critical for several reasons.
First, it directly affects the product’s appearance.
For consumer-facing applications, such as automotive panels or appliance housings, a smooth and defect-free surface is crucial.
Additionally, the surface finish impacts functionality by influencing factors like wear resistance, friction, and susceptibility to corrosion.
Factors Influencing Surface Finish Quality
Material Selection
The type of material used in roll forming significantly affects the surface finish.
Materials with good formability, such as aluminum, stainless steel, and high-strength steels, generally produce better surface finishes.
Choosing materials with consistent thickness and uniform properties can also help minimize surface defects.
Roll Design and Alignment
Rolls play a crucial role in determining the surface quality of the finished product.
Proper roll design ensures an even distribution of forces, reducing the chances of surface defects like waviness, scratches, or dents.
It’s equally important to align the rolls accurately to prevent any misalignment, which can cause surface irregularities.
Lubrication
Lubrication is an often-overlooked aspect that dramatically influences surface finish quality.
Proper lubrication reduces the friction between the material and the rolls, minimizing the risk of surface damage.
High-quality lubricants specifically designed for roll forming should be used to achieve the best results.
Machine Settings and Calibration
Precise machine settings and regular calibration play vital roles in maintaining a high-quality surface finish.
Parameters such as roll gap, speed, and temperature must be carefully controlled.
Inconsistent settings can lead to defects like ripples, scratches, and uneven thickness distribution.
Regular maintenance and calibration of the roll forming machine ensure it operates within the optimal parameters, reducing the risk of surface defects.
Techniques to Improve Surface Finish
Pre-cleaning the Material
Cleaning the material before the roll forming process can significantly improve the surface finish.
Dirt, dust, and other contaminants on the material’s surface can cause scratches and other defects during rolling.
Using appropriate cleaning agents and techniques ensures a clean material surface, leading to a smoother finish.
Implementing Quality Control Measures
Establishing stringent quality control measures throughout the roll forming process can help identify and rectify potential issues early.
Frequent inspections and testing detect surface defects before they become significant problems.
Utilizing advanced techniques like 3D scanning and surface profilometry provides detailed insights into surface finish quality.
Use of Protective Films and Coatings
Applying protective films and coatings can help preserve the surface finish during and after the roll forming process.
These films create a barrier between the material and the rolling equipment, reducing the risk of surface damage.
Additionally, coatings can enhance the material’s resistance to wear, corrosion, and other environmental factors.
Optimizing Roll Forming Speed
While higher speeds can increase production efficiency, they can also negatively impact surface finish quality.
Higher speeds can lead to more friction, heat, and potential for surface defects.
Finding the optimal balance between speed and surface quality ensures efficient production without compromising finish quality.
Innovative Technologies and Trends
Advanced Roll Design and Materials
Innovations in roll design and materials have led to the development of rolls with enhanced wear resistance and improved performance.
Advanced roll materials, such as tool steels and coatings like chrome or tungsten carbide, offer better durability and contribute to superior surface finishes.
Automation and Smart Manufacturing
Automation and the integration of smart manufacturing technologies are transforming the roll forming industry.
Automated systems offer precise control over machine settings, reducing human error and improving consistency.
Smart sensors and monitoring technologies provide real-time data on surface quality, enabling prompt adjustments and maintenance.
Simulation and Analysis Tools
Computer-aided design (CAD) and finite element analysis (FEA) tools are increasingly being used to simulate and analyze the roll-forming process.
These tools help predict potential surface defects and optimize roll design and machine settings.
Simulation technologies enable manufacturers to experiment with different parameters virtually, reducing the need for costly trial-and-error adjustments.
Conclusion
Improving surface finish quality in roll forming requires a holistic approach considering material selection, roll design, lubrication, machine settings, and innovative technologies.
By implementing these strategies, manufacturers can enhance the surface finish quality, ensuring their products meet aesthetic and functional requirements.
Continuous improvement, investment in advanced technologies, and stringent quality control measures are essential for achieving and maintaining high-quality surface finishes in roll forming operations.
資料ダウンロード
QCD調達購買管理クラウド「newji」は、調達購買部門で必要なQCD管理全てを備えた、現場特化型兼クラウド型の今世紀最高の購買管理システムとなります。
ユーザー登録
調達購買業務の効率化だけでなく、システムを導入することで、コスト削減や製品・資材のステータス可視化のほか、属人化していた購買情報の共有化による内部不正防止や統制にも役立ちます。
NEWJI DX
製造業に特化したデジタルトランスフォーメーション(DX)の実現を目指す請負開発型のコンサルティングサービスです。AI、iPaaS、および先端の技術を駆使して、製造プロセスの効率化、業務効率化、チームワーク強化、コスト削減、品質向上を実現します。このサービスは、製造業の課題を深く理解し、それに対する最適なデジタルソリューションを提供することで、企業が持続的な成長とイノベーションを達成できるようサポートします。
オンライン講座
製造業、主に購買・調達部門にお勤めの方々に向けた情報を配信しております。
新任の方やベテランの方、管理職を対象とした幅広いコンテンツをご用意しております。
お問い合わせ
コストダウンが利益に直結する術だと理解していても、なかなか前に進めることができない状況。そんな時は、newjiのコストダウン自動化機能で大きく利益貢献しよう!
(Β版非公開)