- お役立ち記事
- Securing human resources to cover manufacturing sites by training multi-skilled workers
Securing human resources to cover manufacturing sites by training multi-skilled workers
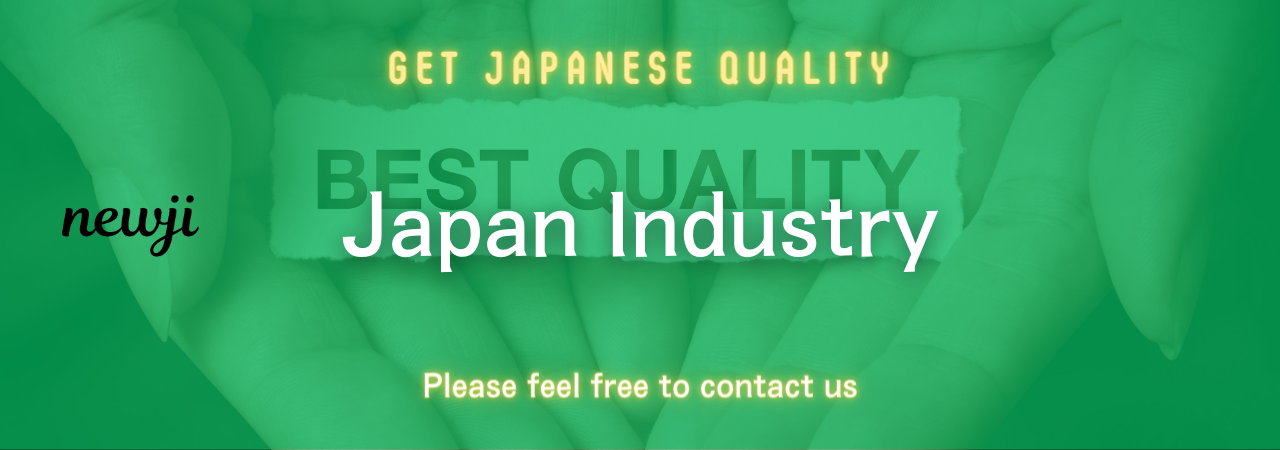
In today’s fast-paced manufacturing industry, adapting to new challenges is crucial for success.
One effective strategy is training multi-skilled workers.
By having a workforce that’s versatile, companies can cover various roles, ensuring smooth operations and efficiency.
This article delves into the importance of securing human resources and how training multi-skilled workers can benefit manufacturing sites.
目次
Why Multi-Skilled Workers Are Essential
Manufacturing relies heavily on precision and productivity.
Single-skilled workers, while experts in their specific tasks, may not provide the flexibility needed in unpredictable situations.
Multi-skilled workers, however, can adapt to different roles as needed.
This adaptability reduces downtime and ensures that production lines keep moving, even when unexpected challenges arise.
Fostering a team that can handle multiple tasks significantly boosts a company’s resilience and efficiency.
Flexibility in the Workplace
A flexible workforce is a significant asset.
When employees can cover various roles, it minimizes the disruption caused by absences or sudden surges in demand.
For example, if one worker is unable to perform their duties, a multi-skilled colleague can step in seamlessly, ensuring that production doesn’t come to a halt.
This flexibility not only smooths operations but also enhances job satisfaction among employees who feel more empowered and valued.
Cost Savings
Training multi-skilled workers can lead to substantial cost savings.
Instead of hiring additional staff for different tasks, companies can invest in training existing employees.
This reduces the need for extra payroll expenses and benefits.
Moreover, having a versatile team can decrease overtime costs, as workers can step in to manage extra tasks without relying solely on specialists.
Improving Productivity
Productivity is the backbone of manufacturing success.
Multi-skilled workers often bring fresh perspectives and improvements to various processes, as they understand multiple aspects of production.
This holistic view can lead to more efficient workflows and innovative problem-solving.
Enhanced productivity means better use of resources and higher output, contributing to a competitive edge in the market.
Training Programs for Multi-Skilling
Implementing a successful multi-skilling program requires a strategic approach.
Here are some effective steps to develop a robust training program:
Identify Key Skills
Start by identifying essential skills needed across various roles in the company.
Create a comprehensive list of tasks and the skills required to execute them efficiently.
This will serve as the foundation for your training program.
Assess Current Workforce Skills
Evaluate the existing skill levels of your employees.
By understanding their strengths and areas for improvement, you can tailor training programs to address specific needs.
Encourage employees to participate in self-assessment to gain insights into their interests and capabilities.
Develop a Training Plan
Craft a structured training plan that includes both theoretical knowledge and practical application.
Consider leveraging online courses, workshops, and hands-on training.
Ensure that training sessions are engaging and interactive to facilitate better learning experiences.
Continuous Learning Environment
Foster a culture of continuous learning within the organization.
Encourage employees to seek new knowledge and skills regularly.
Provide opportunities for them to practice and apply what they’ve learned on the job.
A supportive learning environment motivates employees to stay engaged and committed to their professional development.
Implementing the Training Plan
A well-developed training plan is only effective if implemented correctly.
Here are steps to ensure smooth execution:
Kickoff Meeting
Hold a kickoff meeting to communicate the importance and objectives of the multi-skilling program.
Explain how it aligns with the company’s goals and the benefits it offers to employees.
Address any concerns and answer questions to build enthusiasm and buy-in.
Designate Trainers and Mentors
Select experienced employees to serve as trainers and mentors.
Their expertise and guidance will be invaluable in helping trainees develop new skills.
Ensure that the trainers receive proper training themselves to effectively impart knowledge.
Monitor Progress
Track the progress of each employee through regular assessments.
Use feedback from trainers and trainees to identify areas that need further attention.
Adjust the training plan as necessary to address any gaps or challenges encountered.
Recognize and Reward
Acknowledge the efforts and achievements of employees who successfully acquire new skills.
Recognition can come in various forms, such as certificates, bonuses, or public acknowledgment.
Rewarding employees not only boosts morale but also reinforces the value of continuous learning.
Case Studies and Examples
Several companies have successfully implemented multi-skilling programs with positive outcomes.
Here are a couple of examples:
Company A
Company A, a leading automotive manufacturer, faced a shortage of specialized technicians.
By training their existing workforce in additional skills, they reduced their dependency on external hires.
This led to a more agile production line and a notable decrease in operational costs.
Company B
Company B in the electronics sector experienced frequent production halts due to absenteeism.
By investing in multi-skilling, they created a dynamic workforce capable of stepping into various roles as needed.
This minimized downtime and improved overall production efficiency.
Securing human resources in manufacturing by training multi-skilled workers is a powerful strategy.
It offers numerous benefits, from increased flexibility and cost savings to enhanced productivity.
By implementing a well-structured training program and fostering a culture of continuous learning, companies can build a resilient and dynamic workforce.
This adaptability ensures that manufacturing sites can meet challenges head-on and maintain a competitive edge in the market.
資料ダウンロード
QCD調達購買管理クラウド「newji」は、調達購買部門で必要なQCD管理全てを備えた、現場特化型兼クラウド型の今世紀最高の購買管理システムとなります。
ユーザー登録
調達購買業務の効率化だけでなく、システムを導入することで、コスト削減や製品・資材のステータス可視化のほか、属人化していた購買情報の共有化による内部不正防止や統制にも役立ちます。
NEWJI DX
製造業に特化したデジタルトランスフォーメーション(DX)の実現を目指す請負開発型のコンサルティングサービスです。AI、iPaaS、および先端の技術を駆使して、製造プロセスの効率化、業務効率化、チームワーク強化、コスト削減、品質向上を実現します。このサービスは、製造業の課題を深く理解し、それに対する最適なデジタルソリューションを提供することで、企業が持続的な成長とイノベーションを達成できるようサポートします。
オンライン講座
製造業、主に購買・調達部門にお勤めの方々に向けた情報を配信しております。
新任の方やベテランの方、管理職を対象とした幅広いコンテンツをご用意しております。
お問い合わせ
コストダウンが利益に直結する術だと理解していても、なかなか前に進めることができない状況。そんな時は、newjiのコストダウン自動化機能で大きく利益貢献しよう!
(Β版非公開)