- お役立ち記事
- Selecting and Using Ducts in Manufacturing
Selecting and Using Ducts in Manufacturing
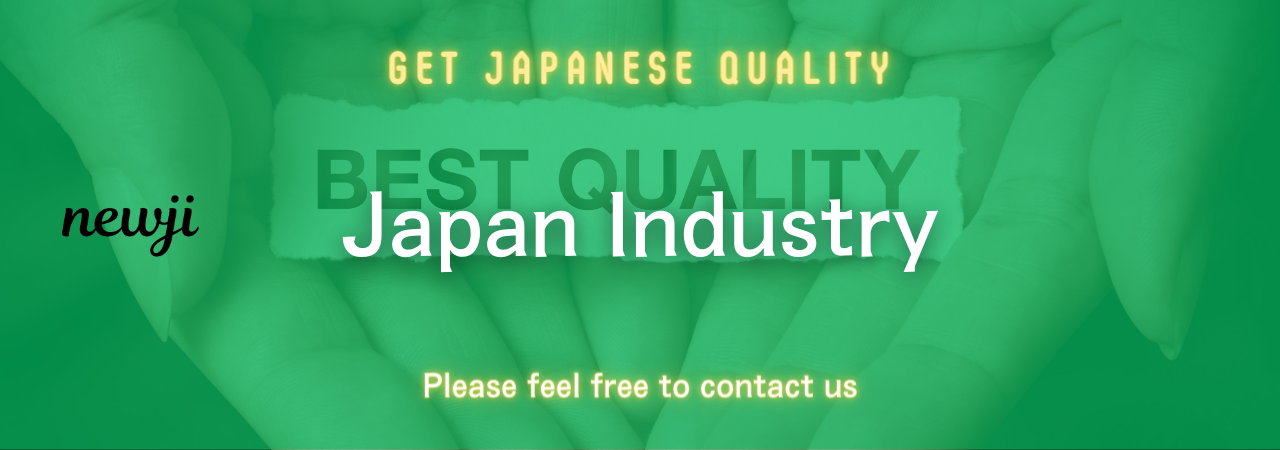
Manufacturing involves various processes, and an important one is the proper selection and use of ducts.
Ducts are crucial for ventilation, heating, and air conditioning systems within factories and other industrial settings.
Choosing the right duct can significantly improve a manufacturing plant’s efficiency, safety, and overall environment.
目次
Why Proper Duct Selection Matters
Having the right duct system is not just about moving air from one place to another.
It plays a vital role in maintaining indoor air quality, controlling temperature, and removing contaminants.
Using the wrong ducts can lead to poor air circulation, higher energy costs, and increased health risks for workers.
Moreover, regulations and industry standards require proper ventilation for worker safety.
Without the right ducts, a manufacturing facility might not comply with these standards, leading to potential fines and operational shutdowns.
Efficiency and Performance
In manufacturing, efficiency is key.
Ducts contribute significantly to the overall performance of ventilation systems.
Choosing high-quality ducts can ensure that air moves efficiently, reducing the load on HVAC systems and lowering energy consumption.
Furthermore, well-selected ducts can minimize noise levels and vibrations, creating a more comfortable working environment.
This improves workforce productivity and ensures that machines operate within their optimal conditions.
Safety and Compliance
The right ducts help in controlling airborne contaminants such as dust, fumes, and chemicals.
These can pose severe health risks if not properly managed.
Duct systems designed to handle specific materials and airflow rates can prevent the buildup of hazardous substances, protecting both workers and equipment.
Compliance with industry regulations is another critical aspect.
Manufacturing facilities must adhere to Occupational Safety and Health Administration (OSHA) standards and other local guidelines.
Proper duct selection ensures these regulations are met, avoiding legal issues and potential shutdowns.
Types of Ducts Used in Manufacturing
Different manufacturing processes require different types of ducts.
Understanding these various options can help in making informed selections.
Flexible Ducts
Flexible ducts are often made from a combination of materials like metal and plastic.
They are highly adaptable, making them ideal for spaces that require complex duct routes.
Despite their versatility, they are best used in low-pressure applications as they can be prone to leaks and wear.
Rigid Ducts
Rigid ducts are made from sturdy materials like galvanized steel, aluminum, or copper.
They provide robust and reliable performance, even under high-pressure conditions.
Their durability makes them an excellent choice for heavy-duty industrial applications, although installation can be more complex and costly.
Fabric Ducts
Fabric ducts are gaining popularity for their lightweight and easy-to-install features.
They are often used in areas requiring evenly distributed airflow.
While they may not be as durable as rigid ducts, they offer impressive efficiency for specific applications, especially in non-hazardous environments.
Key Considerations for Duct Selection
When selecting ducts for a manufacturing facility, several factors need to be considered to ensure optimal performance and safety.
Material
The material of the duct significantly impacts its durability, efficiency, and suitability for different environments.
For instance, stainless steel ducts are resistant to corrosion and are a good choice for facilities dealing with high moisture or chemical exposure.
Plastic ducts, though less durable, can be useful in systems dealing with non-hazardous materials due to their cost-effectiveness and ease of installation.
Airflow Requirements
Understanding the airflow requirements is essential.
This includes the volume, speed, and direction of the air requiring movement.
Ducts must be capable of handling the specific airflow needs without causing excessive pressure drops or losses.
Consulting with HVAC professionals can provide accurate calculations and recommendations tailored to the facility’s needs.
Installation and Maintenance
Ease of installation and maintenance is another critical factor.
Some ducts may require specialized labor or tools for installation, adding to the initial setup costs.
Additionally, considering the maintenance needs ensures that the ducts can be easily cleaned, inspected, and repaired without causing significant disruptions.
Regular maintenance checks help in identifying potential issues early, prolonging the duct system’s lifespan and efficiency.
Best Practices for Using Ducts in Manufacturing
Proper installation and usage of ducts are just as crucial as their selection.
Implementing best practices ensures that the ducts perform optimally throughout their lifespan.
Regular Inspections
Conducting regular inspections can help in identifying issues such as leaks, blockages, or wear and tear.
These inspections should be part of a scheduled maintenance routine, allowing for timely repairs and adjustments.
Cleaning and Upkeep
Keeping ducts clean is essential for maintaining air quality and system efficiency.
Dust, debris, and contaminants can accumulate over time, obstructing airflow and increasing wear.
Regular cleaning helps in preventing these build-ups, ensuring smooth operation.
Monitoring System Performance
Monitoring the performance of the ventilation system can provide insights into how well the ducts are functioning.
This might include observing airflow patterns, checking pressure levels, and assessing the overall environmental conditions within the facility.
Technology such as IoT sensors can be employed for real-time monitoring, making it easier to detect and address issues promptly.
Conclusion
The selection and proper use of ducts in manufacturing are integral to the facility’s environmental control, safety, and efficiency.
By understanding the types of ducts available and considering factors like material, airflow requirements, and maintenance needs, manufacturing plants can achieve optimal performance.
Regular inspections, cleaning, and performance monitoring further ensure that the duct system remains in good condition, providing a safe and productive environment for all.
Careful planning and adherence to best practices in duct selection and usage can lead to significant enhancements in manufacturing operations, ultimately contributing to the facility’s success.
資料ダウンロード
QCD調達購買管理クラウド「newji」は、調達購買部門で必要なQCD管理全てを備えた、現場特化型兼クラウド型の今世紀最高の購買管理システムとなります。
ユーザー登録
調達購買業務の効率化だけでなく、システムを導入することで、コスト削減や製品・資材のステータス可視化のほか、属人化していた購買情報の共有化による内部不正防止や統制にも役立ちます。
NEWJI DX
製造業に特化したデジタルトランスフォーメーション(DX)の実現を目指す請負開発型のコンサルティングサービスです。AI、iPaaS、および先端の技術を駆使して、製造プロセスの効率化、業務効率化、チームワーク強化、コスト削減、品質向上を実現します。このサービスは、製造業の課題を深く理解し、それに対する最適なデジタルソリューションを提供することで、企業が持続的な成長とイノベーションを達成できるようサポートします。
オンライン講座
製造業、主に購買・調達部門にお勤めの方々に向けた情報を配信しております。
新任の方やベテランの方、管理職を対象とした幅広いコンテンツをご用意しております。
お問い合わせ
コストダウンが利益に直結する術だと理解していても、なかなか前に進めることができない状況。そんな時は、newjiのコストダウン自動化機能で大きく利益貢献しよう!
(Β版非公開)