- お役立ち記事
- Selecting and Using Sensors in Manufacturing
Selecting and Using Sensors in Manufacturing
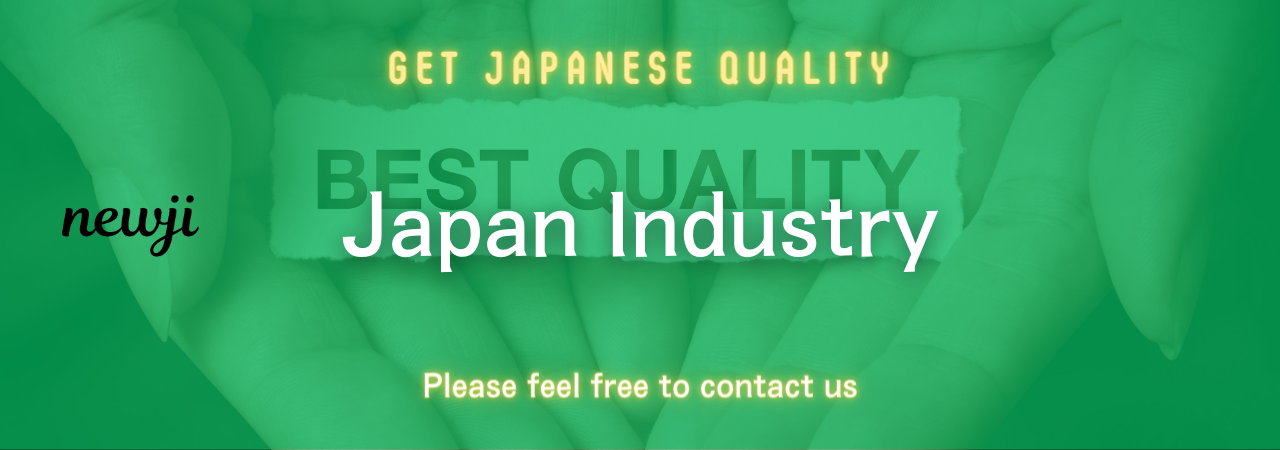
In today’s rapidly evolving manufacturing landscape, the integration of sensors has become a cornerstone for ensuring efficiency, quality, and safety.
Understanding how to select and use these technological aids can significantly impact the productivity and overall success of manufacturing operations.
This article will guide you through the essential steps and considerations for selecting and using sensors in manufacturing.
目次
Understanding the Role of Sensors in Manufacturing
Sensors are crucial components in modern manufacturing systems.
They gather data from various stages of the production process and translate it into actionable insights.
From monitoring temperature and humidity to tracking the movement of machinery, sensors help maintain optimal operating conditions, thereby enhancing product quality and reducing waste.
Why Are Sensors Important?
Sensors contribute to multiple facets of manufacturing:
* **Efficiency**: By providing real-time data, sensors enable swift adjustments to maintain optimal production conditions.
* **Quality Control**: They ensure that products meet stringent quality standards by constantly monitoring critical parameters.
* **Safety**: Sensors help in detecting hazardous conditions and preventing accidents, thus ensuring a safer work environment.
Types of Sensors Used in Manufacturing
Various types of sensors can be utilized depending on the specific needs of the manufacturing process.
Some common types include:
* **Temperature Sensors**: These measure the heat levels in manufacturing equipment and materials.
* **Pressure Sensors**: Needed for processes involving liquids or gases, they monitor the pressure to ensure safety and efficiency.
* **Proximity Sensors**: Used to detect the presence or absence of an object within a certain distance.
* **Vibration Sensors**: These monitor the health of machinery by detecting any unusual vibrations that could indicate a problem.
* **Optical Sensors**: They leverage light to detect changes in a manufacturing process, useful for quality control and precision machining.
Factors to Consider When Selecting Sensors
Choosing the right sensor requires a careful analysis of several factors to ensure that it fits the demands of the manufacturing process effectively.
Compatibility
Ensure the sensor is compatible with your existing systems.
Check whether it can easily integrate with your current machinery and data-processing systems.
Accuracy and Precision
Depending on the tolerance levels of your manufacturing process, the accuracy and precision of the sensor are critical.
For high-precision tasks, even a small margin of error can lead to significant defects.
Environmental Conditions
The operating environment can significantly impact the performance of a sensor.
Consider factors such as temperature, humidity, and exposure to chemicals or dust when selecting sensors.
Range
Different sensors have varying working ranges.
Make sure the sensor you choose can operate effectively within the range required for your specific application.
Durability
Manufacturing environments can be harsh.
Select sensors that are rugged and can withstand physical wear and tear over time.
Installation and Integration
Once you have selected the appropriate sensors, the next step is proper installation and integration into your manufacturing system.
Placement
Choosing the right location for sensor placement is crucial.
Position them where they can most effectively monitor the necessary parameters.
Calibration
Ensure that the sensors are calibrated correctly before use.
Improper calibration can lead to inaccurate readings and affect the entire manufacturing process.
Data Integration
Make sure that the sensors can seamlessly transmit data to your monitoring systems.
Proper data integration ensures that you can make real-time decisions based on accurate and current information.
Interpreting Sensor Data
Collecting data is just the first step.
The ability to interpret this data and act upon it is what ultimately enhances manufacturing efficiency.
Real-Time Monitoring
The foremost advantage of sensors is real-time monitoring.
By continuously tracking the conditions of the manufacturing process, you can make prompt adjustments as necessary.
Data Analytics
Utilize advanced data analytics platforms to interpret the vast amounts of data collected by sensors.
These platforms can provide you with actionable insights and trends that you may not notice manually.
Setting Alerts
To manage manufacturing processes efficiently, set up automated alerts for key parameters.
For instance, if a temperature sensor detects a reading outside the preset range, it should immediately notify the responsible personnel.
Maintenance and Troubleshooting
Regular maintenance and timely troubleshooting ensure that your sensors continue to function effectively.
Periodic Checks
Perform routine checks and maintenance to ensure sensors are in good working condition.
This includes cleaning, recalibration, and replacing any worn-out components.
Troubleshooting
Develop a troubleshooting guide specific to each type of sensor used in your manufacturing process.
This will help quickly diagnose and resolve issues should they arise.
Documentation
Maintain detailed documentation of sensor performance, maintenance activities, and any issues encountered.
This documentation can be invaluable for future troubleshooting and for optimizing the manufacturing process.
Conclusion
Selecting and using sensors in manufacturing is not just about choosing the latest technology.
It’s about finding the proper fit for your specific needs, ensuring seamless integration, and interpreting the data effectively.
By considering factors such as compatibility, accuracy, and durability, and by maintaining a rigorous maintenance routine, you can significantly enhance the efficiency, quality, and safety of your manufacturing operations.
With the right approach, sensors can serve as the backbone of a smart, efficient manufacturing process.
資料ダウンロード
QCD調達購買管理クラウド「newji」は、調達購買部門で必要なQCD管理全てを備えた、現場特化型兼クラウド型の今世紀最高の購買管理システムとなります。
ユーザー登録
調達購買業務の効率化だけでなく、システムを導入することで、コスト削減や製品・資材のステータス可視化のほか、属人化していた購買情報の共有化による内部不正防止や統制にも役立ちます。
NEWJI DX
製造業に特化したデジタルトランスフォーメーション(DX)の実現を目指す請負開発型のコンサルティングサービスです。AI、iPaaS、および先端の技術を駆使して、製造プロセスの効率化、業務効率化、チームワーク強化、コスト削減、品質向上を実現します。このサービスは、製造業の課題を深く理解し、それに対する最適なデジタルソリューションを提供することで、企業が持続的な成長とイノベーションを達成できるようサポートします。
オンライン講座
製造業、主に購買・調達部門にお勤めの方々に向けた情報を配信しております。
新任の方やベテランの方、管理職を対象とした幅広いコンテンツをご用意しております。
お問い合わせ
コストダウンが利益に直結する術だと理解していても、なかなか前に進めることができない状況。そんな時は、newjiのコストダウン自動化機能で大きく利益貢献しよう!
(Β版非公開)