- お役立ち記事
- Selecting and Utilizing Clean Room Supplies in Manufacturing
月間76,176名の
製造業ご担当者様が閲覧しています*
*2025年3月31日現在のGoogle Analyticsのデータより
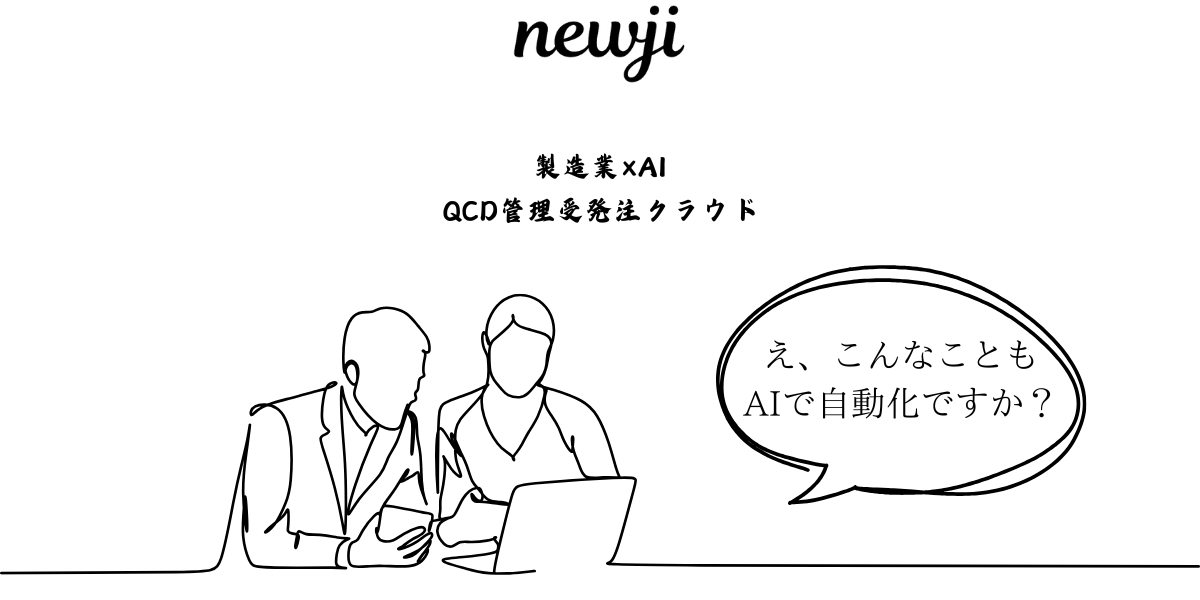
Selecting and Utilizing Clean Room Supplies in Manufacturing
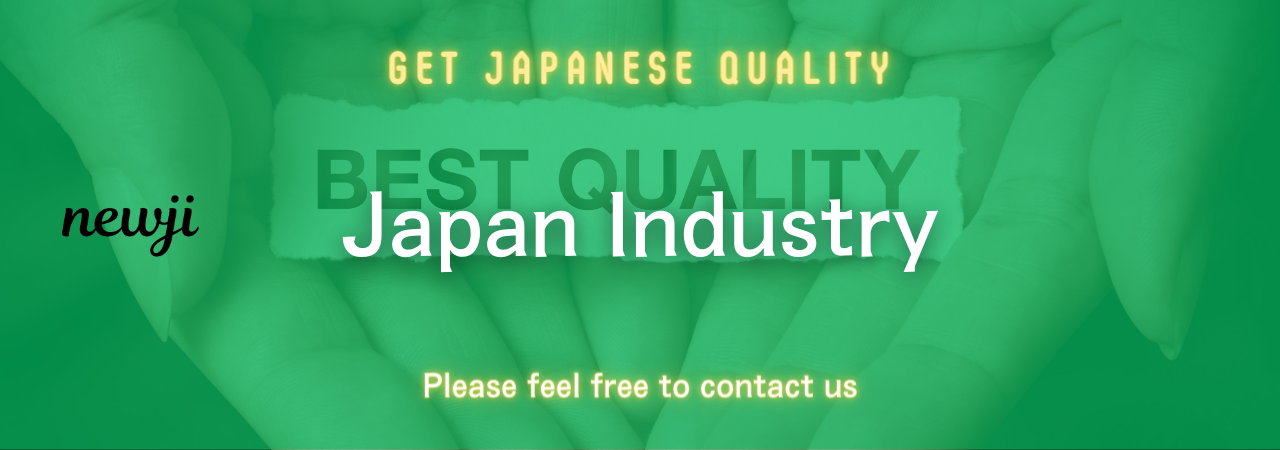
In today’s competitive manufacturing landscape, maintaining a pristine production environment is more important than ever.
Clean rooms play a crucial role in minimizing pollutants such as dust, airborne microbes, and chemical vapors, which can significantly affect product quality.
Choosing the right clean room supplies and using them efficiently can ensure that your manufacturing operations remain both productive and compliant with industry standards.
目次
Why Clean Rooms are Essential in Manufacturing
Different industries, such as pharmaceuticals, biotechnology, electronics, and aerospace, require stringent environmental controls to manufacture high-quality products.
Even the smallest contaminants can severely compromise the integrity and functionality of the end product.
By investing in clean rooms and the necessary supplies, manufacturers can minimize contamination risks and meet regulatory requirements.
Clean rooms are designed to control specific environmental parameters such as air particle levels, temperature, humidity, and pressure.
These controlled environments are essential for minimizing contamination and ensuring consistent product quality.
Moreover, clean rooms help in maintaining stringent manufacturing standards and achieving compliance with regulatory bodies such as the FDA in the pharmaceutical and medical device industries.
Types of Clean Room Supplies
To keep your clean room in optimal condition, you’ll need a variety of supplies.
These supplies can be broadly categorized into protective apparel, cleaning products, and equipment.
Protective Apparel
One of the most critical elements in maintaining a clean room is ensuring that personnel adhere to strict dress codes.
Common protective apparel includes:
– **Gloves**: Prevent germs and contaminants from transferring from hands to products.
– **Face Masks**: Reduce the emission of airborne contaminants from breathing and talking.
– **Coveralls**: Full-body suits designed to offer maximum protection from contaminants.
– **Shoe Covers**: Prevent dirt and contaminants from entering the clean room on footwear.
Cleaning Products
Regular cleaning is essential for maintaining a contaminant-free clean room.
Here are some indispensable cleaning supplies:
– **Disinfectant Wipes**: Effective for quick decontamination of surfaces.
– **Mops and Buckets**: Designed specifically for clean rooms, to clean floors without adding contaminants.
– **Clean Room Cloths**: Non-linting cloths that are perfect for wiping down surfaces and equipment.
– **HEPA Vacuums**: Capture and trap small particles that traditional vacuums might miss.
Equipment
In addition to protective apparel and cleaning supplies, specialized equipment is needed to maintain a clean room environment.
Some essential equipment includes:
– **Air Showers**: Enclosed spaces that use high-velocity air to remove contaminants from personnel before they enter the clean room.
– **Laminar Flow Cabinets**: Provide a particle-free working environment by directing filtered air over the workspace.
– **Particle Counters**: Measure the concentration of airborne particles to help maintain clean room standards.
– **Autoclaves**: Sterilize tools and materials to kill any potential contaminants.
Choosing the Right Supplies
When selecting clean room supplies, it is crucial to consider the specific requirements of your industry and the level of cleanliness needed.
Here are some tips to guide your choice:
Understand Clean Room Classifications
Clean rooms are classified based on the number and size of particles permitted per volume of air.
For example, ISO Class 5 allows fewer particles than ISO Class 7.
Know your clean room classification to choose supplies that meet or exceed those standards.
Evaluate Supplier Credibility
Choose a supplier known for high-quality, reliable clean room supplies.
Read reviews, ask for recommendations, and evaluate the supplier’s industry reputation.
Prioritize Compatibility
Ensure that the supplies you choose are compatible with your clean room’s operational requirements and materials.
For example, some chemicals in disinfectants can react negatively with certain surfaces or equipment.
Cost vs. Quality
While it might be tempting to go for cheaper alternatives, cutting costs on clean room supplies can lead to higher contamination risks.
Prioritize quality over cost to ensure long-term efficiency and compliance.
Best Practices for Utilizing Clean Room Supplies
Even the best clean room supplies are only as effective as the protocols and practices in place to use them.
Below are some best practices to maximize their effectiveness:
Regular Training
Regular training sessions for your staff on proper clean room protocols can mitigate contamination risks.
Training ensures that everyone knows how to properly don and doff protective apparel and use cleaning supplies effectively.
Scheduled Maintenance
Proactive maintenance schedules help keep clean room equipment like HEPA filters and autoclaves functioning optimally.
Regular audits and inspections can catch potential issues before they become major problems.
Monitoring and Documentation
Consistent monitoring and documentation of your clean room environment help you stay compliant with industry standards.
Use particle counters and other monitoring tools to track cleanliness levels and document all cleaning protocols for accountability.
Effective Communication
Clear lines of communication between all staff members ensure that everyone is aware of their responsibilities.
Effective communication helps in quickly addressing any contamination issues that may arise.
Conclusion
Maintaining a clean room in a manufacturing environment is no small feat, but it is essential for ensuring high-quality product output.
Selecting the right clean room supplies, from protective apparel to specialized equipment, plays a crucial role in this process.
Understanding how to utilize these supplies effectively can make the difference between success and failure in highly regulated industries.
By adhering to clean room protocols, investing in high-quality supplies, and continually educating your team, you can uphold stellar manufacturing standards and remain compliant with industry regulations.
Such rigorous measures not only protect your products but also enhance your company’s reputation for quality and reliability.
資料ダウンロード
QCD管理受発注クラウド「newji」は、受発注部門で必要なQCD管理全てを備えた、現場特化型兼クラウド型の今世紀最高の受発注管理システムとなります。
ユーザー登録
受発注業務の効率化だけでなく、システムを導入することで、コスト削減や製品・資材のステータス可視化のほか、属人化していた受発注情報の共有化による内部不正防止や統制にも役立ちます。
NEWJI DX
製造業に特化したデジタルトランスフォーメーション(DX)の実現を目指す請負開発型のコンサルティングサービスです。AI、iPaaS、および先端の技術を駆使して、製造プロセスの効率化、業務効率化、チームワーク強化、コスト削減、品質向上を実現します。このサービスは、製造業の課題を深く理解し、それに対する最適なデジタルソリューションを提供することで、企業が持続的な成長とイノベーションを達成できるようサポートします。
製造業ニュース解説
製造業、主に購買・調達部門にお勤めの方々に向けた情報を配信しております。
新任の方やベテランの方、管理職を対象とした幅広いコンテンツをご用意しております。
お問い合わせ
コストダウンが利益に直結する術だと理解していても、なかなか前に進めることができない状況。そんな時は、newjiのコストダウン自動化機能で大きく利益貢献しよう!
(β版非公開)