- お役立ち記事
- Selection and implementation know-how of processing processes suitable for prototyping
月間76,176名の
製造業ご担当者様が閲覧しています*
*2025年3月31日現在のGoogle Analyticsのデータより
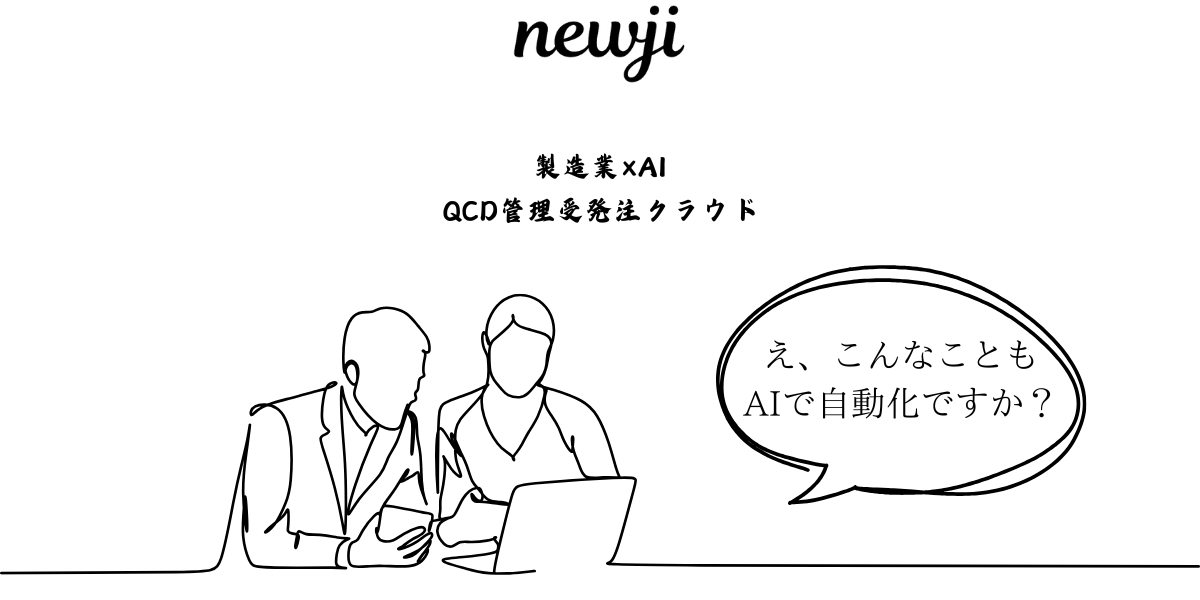
Selection and implementation know-how of processing processes suitable for prototyping
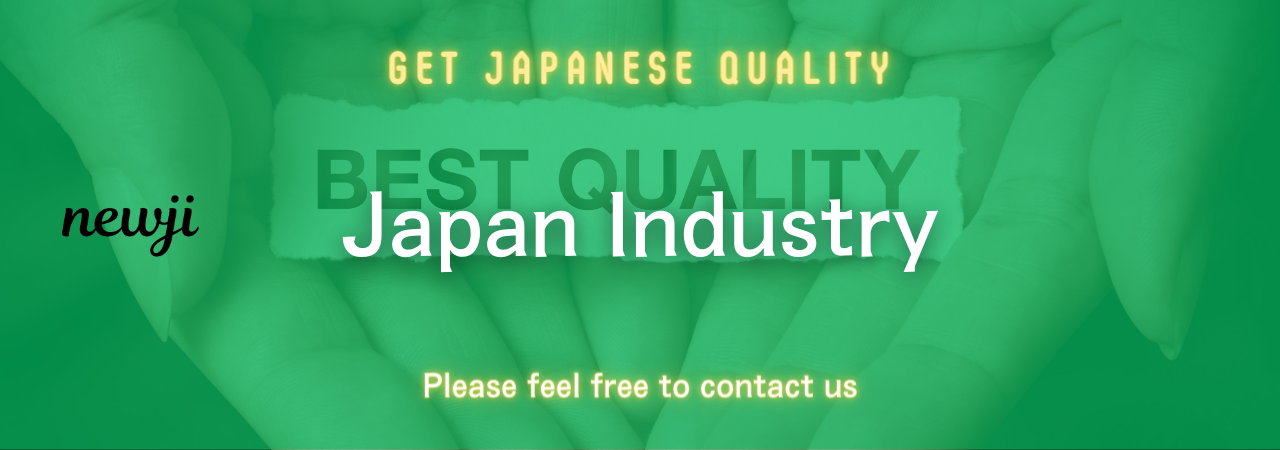
目次
Understanding Prototyping and its Importance
Prototyping is a crucial step in the process of product development.
It involves creating an early model or sample of a product to test concepts, design features, and functionality.
For businesses and innovators, prototyping offers an opportunity to explore ideas and visualize how a final product might look or work.
The process can significantly impact the success of a project.
By identifying potential issues early, businesses can save time, reduce costs, and ultimately improve the final product.
Why Choose the Right Processing Process?
Selecting an appropriate processing process for prototyping is vital for several reasons.
Firstly, it ensures that the prototype accurately represents the intended design and function of the final product.
Secondly, the right process can improve efficiency and reduce the time required to develop a prototype.
Finally, using an optimal process can minimize material waste and associated costs, making the project more economically viable.
Common Processing Processes for Prototyping
3D Printing
3D printing, also known as additive manufacturing, is one of the most popular methods for creating prototypes.
This process involves adding material layer by layer to build a three-dimensional object.
It is highly versatile, allowing for the creation of complex shapes that would be difficult to achieve with traditional manufacturing methods.
3D printing is ideal for rapid prototyping because it is cost-effective and allows for quick iterations.
CNC Machining
CNC (Computer Numerical Control) machining is a subtractive manufacturing process where unwanted material is removed from a solid block to create the desired shape.
This method is highly precise and is often used for metal prototypes.
CNC machining is favored for its ability to produce parts with high dimensional accuracy and excellent surface finishes.
Though it can be more expensive than 3D printing, it’s highly effective for durable and functional prototypes.
Injection Molding
Injection molding involves injecting molten material into a mold to form parts.
This method is great for prototypes that require testing for mass production processes.
While the initial setup for injection molding can be high, it is cost-effective for large runs due to the rapid production speed and consistent quality.
The method is ideal for prototypes that need to closely mimic the properties of the final product.
Vacuum Casting
Vacuum casting is a process that uses silicone molds to replicate parts with plastic-like properties.
It is best suited for producing small quantities of prototypes, often used in applications like consumer electronics or automotive components.
This process is advantageous for its ability to produce detailed parts with fine surface finishes at a relatively low cost and time investment.
Factors to Consider in Selection
Material Requirements
One of the key considerations when selecting a processing process for prototyping is the material requirements.
Different processes support different types of materials.
For example, 3D printing works well with plastics, resins, and metals, while CNC machining is better suited for metals and high-precision materials.
Understanding the material needs of your prototype is crucial to choosing an appropriate processing method.
Design Complexity
The complexity of the design significantly influences the choice of prototyping process.
Some methods, like 3D printing, are better suited for intricate designs with complex geometries.
Other processes, like injection molding, might require more straightforward designs due to the limitations of the mold.
Evaluating the complexity of your design can help in selecting a process capable of meeting the design criteria.
Production Volume
The anticipated volume of prototype production also impacts the choice of process.
Methods such as injection molding become more cost-effective as the production volume increases due to the high initial setup costs but low per-unit cost.
On the other hand, 3D printing is more economical for low-volume production runs.
Determining the number of prototypes required can guide the decision-making process.
Timeline Constraints
Time constraints play a vital role in process selection.
If a rapid turnaround is needed, methods like 3D printing or CNC machining offer quicker lead times compared to setting up an injection mold.
Considering the project timeline can help in choosing a process that meets deadlines without compromising on quality.
Implementing the Selected Process
Once the appropriate processing process is selected, the implementation phase begins.
This stage involves setting up the necessary equipment, selecting the right materials, and scheduling the process to meet project timelines.
Working closely with engineers and designers is crucial to ensure that every aspect of the prototype’s specifications is met.
Testing and Iteration
It is essential to test the prototype after it has been produced.
This step helps identify any shortcomings or areas for improvement.
Prototyping is an iterative process, where repeated testing and refining lead to a better final product.
Gathering feedback from stakeholders during this phase is invaluable, as it provides insights that can enhance design and functionality.
Documenting the Process
Documentation throughout the prototyping process is critical for future reference and for scaling production.
Recording details such as material types, process settings, and test results provide a comprehensive history that guides future projects.
A well-documented process can improve efficiency and ensure consistency in production.
It also aids in identifying successful strategies or areas that may require adjustment.
Conclusion
Selecting and implementing the right processing process suitable for prototyping is key to successful product development.
By understanding the needs of the project and evaluating different manufacturing methods, businesses can create high-quality prototypes efficiently.
The right process not only delivers on design and functional expectations but also aligns with budget and timeline constraints, ultimately leading to successful product realization.
資料ダウンロード
QCD管理受発注クラウド「newji」は、受発注部門で必要なQCD管理全てを備えた、現場特化型兼クラウド型の今世紀最高の受発注管理システムとなります。
ユーザー登録
受発注業務の効率化だけでなく、システムを導入することで、コスト削減や製品・資材のステータス可視化のほか、属人化していた受発注情報の共有化による内部不正防止や統制にも役立ちます。
NEWJI DX
製造業に特化したデジタルトランスフォーメーション(DX)の実現を目指す請負開発型のコンサルティングサービスです。AI、iPaaS、および先端の技術を駆使して、製造プロセスの効率化、業務効率化、チームワーク強化、コスト削減、品質向上を実現します。このサービスは、製造業の課題を深く理解し、それに対する最適なデジタルソリューションを提供することで、企業が持続的な成長とイノベーションを達成できるようサポートします。
製造業ニュース解説
製造業、主に購買・調達部門にお勤めの方々に向けた情報を配信しております。
新任の方やベテランの方、管理職を対象とした幅広いコンテンツをご用意しております。
お問い合わせ
コストダウンが利益に直結する術だと理解していても、なかなか前に進めることができない状況。そんな時は、newjiのコストダウン自動化機能で大きく利益貢献しよう!
(β版非公開)