- お役立ち記事
- Selection and implementation of automatic loading systems that new employees in the equipment technology department of the metal processing industry should know.
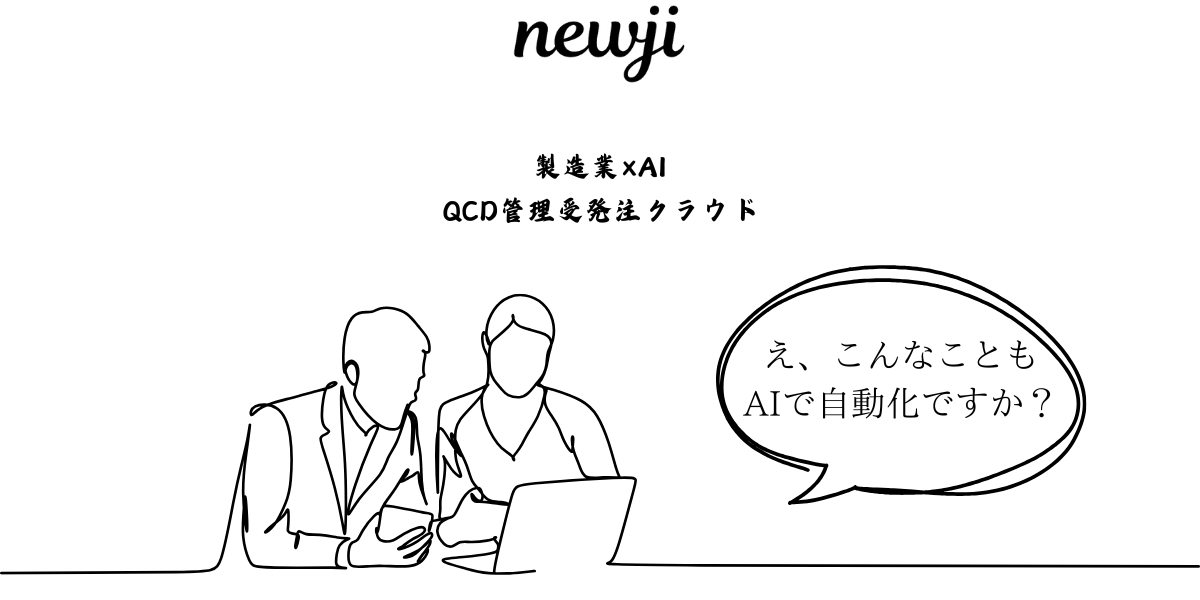
Selection and implementation of automatic loading systems that new employees in the equipment technology department of the metal processing industry should know.
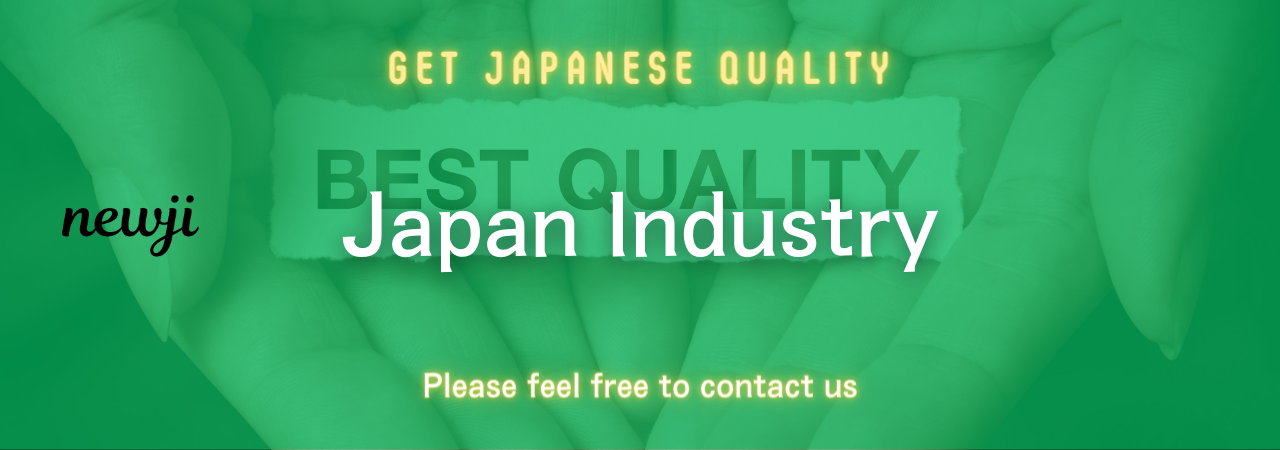
目次
Introduction to Automatic Loading Systems
In the metal processing industry, efficiency and precision are crucial for maintaining competitive edge and meeting production demands.
One of the tools that help achieve these goals is the automatic loading system.
For new employees in the equipment technology department, understanding the basics of selecting and implementing these systems is essential.
Understanding Automatic Loading Systems
Automatic loading systems are devices or mechanisms designed to load workpieces or materials into machines without manual intervention.
These systems enhance productivity by reducing downtime and streamlining operations.
They are particularly valuable in environments where repetitive tasks and high-volume production are common.
Types of Automatic Loading Systems
There are several types of automatic loading systems, each suited to different applications in the metal processing industry.
Understanding these types will aid new employees in making informed decisions during selection and implementation:
Conveyor Systems
Conveyor systems use belts, rollers, or chains to transport materials between different stages of production.
They are versatile and can be customized to fit various spatial arrangements.
Robotic Arms
Robotic arms are highly flexible and can be programmed to handle diverse tasks, from loading materials into machines to assembling components.
They are ideal for precision tasks and environments requiring adaptability.
AGV (Automated Guided Vehicles)
AGVs are mobile robots that transport materials autonomously within a facility.
They follow pre-defined paths and are suitable for operations requiring frequent material movement.
Pallet Systems
Pallet systems provide a platform for holding multiple workpieces, allowing efficient loading and unloading.
These systems are beneficial for batch production processes.
Factors to Consider When Selecting an Automatic Loading System
Selecting the right automatic loading system involves several considerations:
To help guide new employees, here are key factors to assess:
Production Requirements
Understanding production volumes and cycle times is essential.
The system should match the facility’s throughput needs, ensuring it can handle current and future demands.
Type of Materials
Different materials have unique handling requirements.
The system should accommodate material sizes, weights, and fragility to prevent damage and ensure smooth operations.
Space Constraints
Evaluate the physical space available for the loading system.
Some systems require more space, so understanding facility layout constraints is vital in selecting an appropriate system.
Integration with Existing Equipment
The chosen system should seamlessly integrate with existing machines.
Assess compatibility with current infrastructure to ensure smooth operations and avoid disruptions.
Budget Considerations
Automatic loading systems can represent a significant investment.
It’s crucial to balance cost with benefits, ensuring the selected system aligns with budgetary constraints while still meeting operational needs.
Steps for Implementing Automatic Loading Systems
Once the appropriate system is selected, it’s time for implementation.
Here are the key steps new employees should follow:
Conduct a Site Assessment
Begin with a thorough assessment of the facility to identify potential challenges and layout considerations.
This step ensures the chosen system fits into the available space and supports production flow.
Develop a Detailed Implementation Plan
Create a comprehensive plan outlining timelines, roles, and responsibilities.
This plan should cover every stage, from installation to testing, ensuring a structured approach to implementation.
Training and Staff Preparation
Prepare staff for the transition by providing training on the operation and maintenance of the new system.
This helps in reducing resistance, building acceptance, and ensuring smooth integration with daily activities.
Monitor and Adjust
During initial operations, closely monitor the system’s performance.
Gather feedback from operators and make necessary adjustments to optimize performance and address any emerging issues.
Regular Maintenance and Upgrades
Implement a schedule for regular maintenance to ensure the system operates efficiently.
Stay informed about potential upgrades or improvements that can further enhance productivity.
Conclusion
Automatic loading systems are an integral component in the metal processing industry, contributing to increased efficiency and productivity.
For new employees in the equipment technology department, gaining a clear understanding of how to select and implement these systems is crucial.
By considering production requirements, material types, space constraints, and integration needs, they can make informed decisions that benefit the entire operation.
Furthermore, following a structured implementation process ensures a successful transition to automated systems, providing long-term benefits and supporting the organization’s growth.
資料ダウンロード
QCD調達購買管理クラウド「newji」は、調達購買部門で必要なQCD管理全てを備えた、現場特化型兼クラウド型の今世紀最高の購買管理システムとなります。
ユーザー登録
調達購買業務の効率化だけでなく、システムを導入することで、コスト削減や製品・資材のステータス可視化のほか、属人化していた購買情報の共有化による内部不正防止や統制にも役立ちます。
NEWJI DX
製造業に特化したデジタルトランスフォーメーション(DX)の実現を目指す請負開発型のコンサルティングサービスです。AI、iPaaS、および先端の技術を駆使して、製造プロセスの効率化、業務効率化、チームワーク強化、コスト削減、品質向上を実現します。このサービスは、製造業の課題を深く理解し、それに対する最適なデジタルソリューションを提供することで、企業が持続的な成長とイノベーションを達成できるようサポートします。
オンライン講座
製造業、主に購買・調達部門にお勤めの方々に向けた情報を配信しております。
新任の方やベテランの方、管理職を対象とした幅広いコンテンツをご用意しております。
お問い合わせ
コストダウンが利益に直結する術だと理解していても、なかなか前に進めることができない状況。そんな時は、newjiのコストダウン自動化機能で大きく利益貢献しよう!
(Β版非公開)