- お役立ち記事
- Selection and implementation of automatic loading systems that new employees in the equipment technology department of the metal processing industry should know.
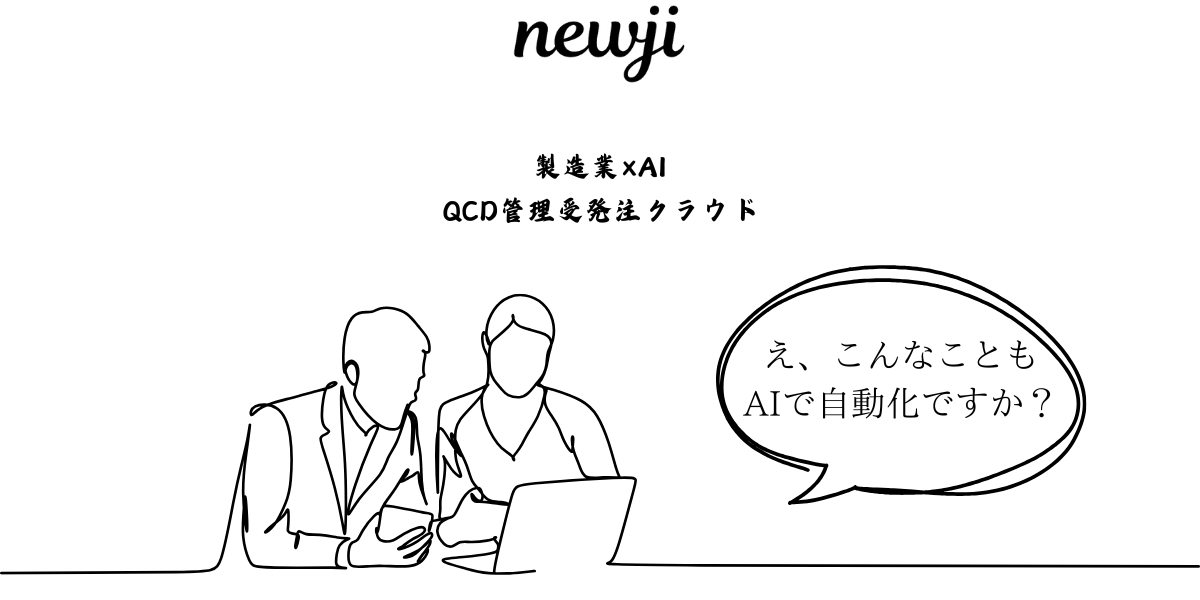
Selection and implementation of automatic loading systems that new employees in the equipment technology department of the metal processing industry should know.
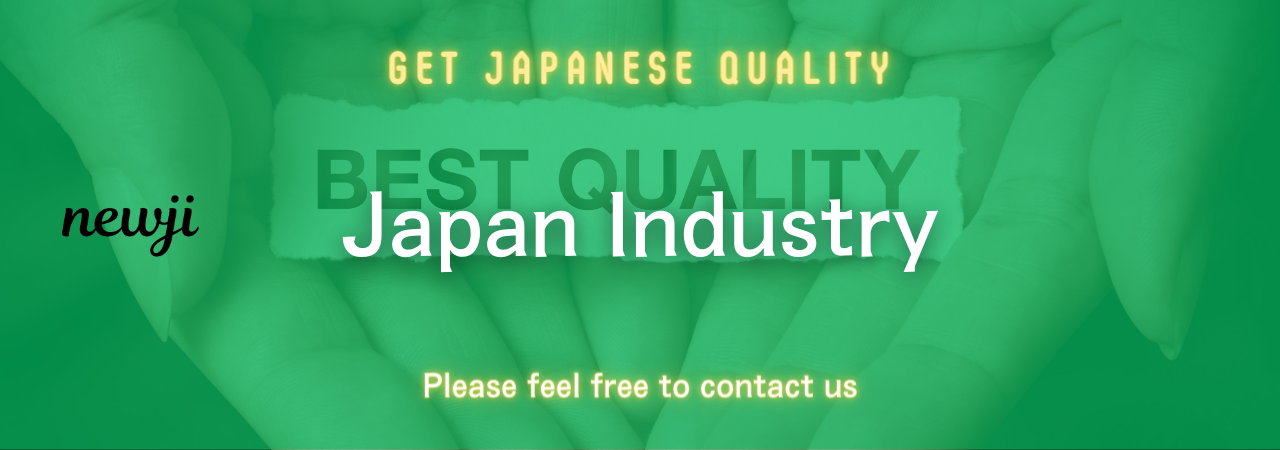
目次
Understanding Automatic Loading Systems
Automatic loading systems play a crucial role in the metal processing industry.
These systems are designed to increase efficiency, reduce manual errors, and optimize the workflow within manufacturing plants.
For new employees in the equipment technology department, gaining a solid understanding of these systems is essential to ensure smooth operations.
What Are Automatic Loading Systems?
Automatic loading systems are machinery and software setups that automatically load and unload materials from various machines within a production line.
They are often integrated with conveyors, robots, or automated guided vehicles (AGVs) to handle materials, parts, and products efficiently.
These systems are tailored to meet the needs of different manufacturing processes, making them indispensable in today’s highly competitive industrial environment.
Benefits of Implementing Automatic Loading Systems
The adoption of automatic loading systems offers numerous benefits for metal processing plants.
Primarily, they significantly increase operational efficiency by minimizing manual intervention, which in turn reduces the risk of human error.
This leads to a smoother production line and less downtime.
Moreover, these systems contribute to improved safety in the workplace.
By automating the loading and unloading tasks, workers are less exposed to potential hazards associated with manual material handling.
This creates a safer working environment, reducing the likelihood of workplace injuries.
Automatic loading systems also enhance the overall quality of the production process.
With precise material handling, the chances of damage to the materials or products are minimized, resulting in higher-quality outputs.
Furthermore, these systems facilitate quicker turnaround times, enabling metal processing plants to meet deadlines and boost productivity.
Types of Automatic Loading Systems
Understanding the different types of automatic loading systems is key for new employees who wish to choose and implement the best system for their facility.
Below are some common types used in the metal processing industry.
Robotic Loading Systems
Robotic loading systems utilize industrial robots to handle the loading and unloading tasks.
These robots can be programmed to perform repetitive tasks with high precision and speed.
They are ideal for environments where accuracy and consistency are critical.
Robotic systems are extremely versatile, capable of performing a variety of functions such as pick-and-place operations, sorting, and stacking.
They can be easily integrated into existing production lines, providing a flexible solution for manufacturers looking to enhance their automation capabilities.
Conveyor-Based Systems
Conveyor-based systems are designed to transport materials from one point to another automatically.
These systems are commonly used in facilities with a high volume of material movement.
They consist of a series of belts, rollers, or chains powered by motors to move materials efficiently.
Conveyor systems can be customized to fit the specific needs of a production line.
They can handle different material types and sizes, making them widely adaptable in the metal processing industry.
Additionally, incorporating sensors and controls can further optimize the flow and reduce bottlenecks in the production process.
Automated Guided Vehicles (AGVs)
Automated guided vehicles (AGVs) are mobile robots used to transport materials within a manufacturing plant.
They are equipped with advanced navigation systems that allow them to move along predefined paths without human intervention.
AGVs offer flexibility in material handling and can be programmed to follow specific routes based on production demands.
They are ideal for facilities with dynamic production lines or layouts where materials need to be moved over varying distances.
Critical Considerations for Implementation
When implementing automatic loading systems, there are several critical considerations that new employees should keep in mind.
Assessing Plant Requirements
The first step in selecting the right automatic loading system is to assess the specific requirements of the manufacturing plant.
New employees need to understand the type of materials being processed, the production volumes, and the layout of the facility.
This information helps in determining which system will best suit the plant’s needs, contributing to a successful implementation.
Scalability and Flexibility
Scalability and flexibility are key factors to consider when choosing an automatic loading system.
As production demands change, the system should be capable of adapting to new requirements without the need for extensive reconfigurations.
Selecting systems that are modular and easily upgradable can save significant time and costs in the long run.
Integration with Existing Systems
Another important factor is the integration of the automatic loading system with the existing machinery and software in the plant.
New employees should ensure that the chosen system can seamlessly communicate with other systems to create a cohesive production environment.
Compatibility with existing equipment is crucial for achieving maximum efficiency and productivity.
Training and Maintenance
Once the automatic loading system is implemented, proper training and maintenance are vital for its continued success.
Comprehensive Training
New employees must undergo comprehensive training to understand the operation, troubleshooting, and basic maintenance of automatic loading systems.
This knowledge enables them to operate the systems efficiently and effectively, minimizing the potential for operational disruptions.
Regular Maintenance
Regular maintenance of the automatic loading systems is crucial to ensure their longevity and optimal performance.
Establishing routine checks and servicing schedules can help identify potential issues before they escalate, preventing costly downtime.
In conclusion, automatic loading systems are integral to the metal processing industry, offering numerous benefits such as increased efficiency, improved safety, and enhanced product quality.
Understanding different system types and implementation considerations are essential for new employees in the equipment technology department.
With proper training and maintenance, these systems can significantly contribute to the success of manufacturing operations.
資料ダウンロード
QCD調達購買管理クラウド「newji」は、調達購買部門で必要なQCD管理全てを備えた、現場特化型兼クラウド型の今世紀最高の購買管理システムとなります。
ユーザー登録
調達購買業務の効率化だけでなく、システムを導入することで、コスト削減や製品・資材のステータス可視化のほか、属人化していた購買情報の共有化による内部不正防止や統制にも役立ちます。
NEWJI DX
製造業に特化したデジタルトランスフォーメーション(DX)の実現を目指す請負開発型のコンサルティングサービスです。AI、iPaaS、および先端の技術を駆使して、製造プロセスの効率化、業務効率化、チームワーク強化、コスト削減、品質向上を実現します。このサービスは、製造業の課題を深く理解し、それに対する最適なデジタルソリューションを提供することで、企業が持続的な成長とイノベーションを達成できるようサポートします。
オンライン講座
製造業、主に購買・調達部門にお勤めの方々に向けた情報を配信しております。
新任の方やベテランの方、管理職を対象とした幅広いコンテンツをご用意しております。
お問い合わせ
コストダウンが利益に直結する術だと理解していても、なかなか前に進めることができない状況。そんな時は、newjiのコストダウン自動化機能で大きく利益貢献しよう!
(Β版非公開)