- お役立ち記事
- Selection and Use of Samplers in Manufacturing
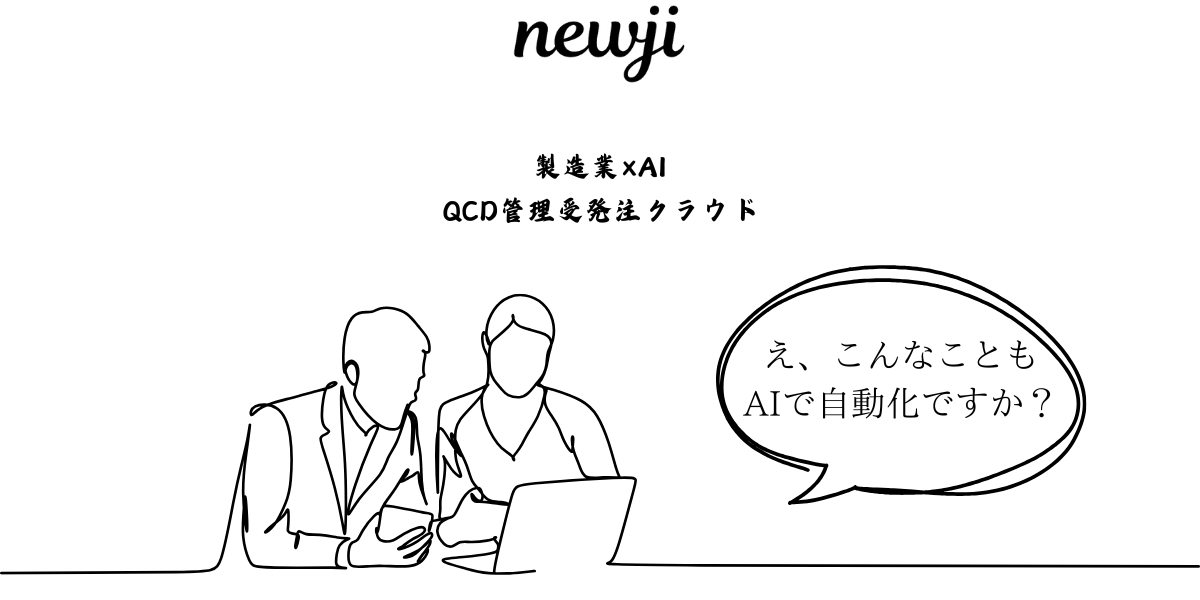
Selection and Use of Samplers in Manufacturing
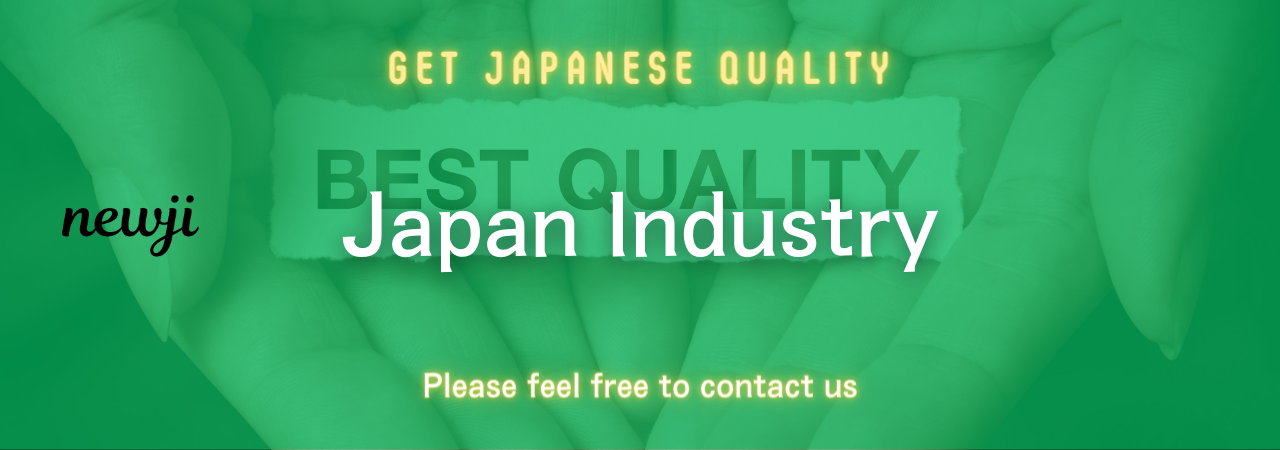
In the world of manufacturing, ensuring quality control is paramount. One of the essential tools in this process is the sampler. Samplers help gather representative samples of materials, products, or goods to verify compliance with set standards. This article will explore the selection and use of samplers in manufacturing, shedding light on why they are critical and how to choose the right one for your needs.
目次
Understanding Samplers
The primary purpose of samplers in manufacturing is to obtain a portion of material or product that accurately represents the whole. This representative sample can then be tested to ensure it meets the required specifications and standards. This step is crucial in detecting any inconsistencies or defects early in production, allowing for timely corrections.
Types of Samplers
Liquid Samplers
Liquid samplers are designed specifically for collecting samples of liquids. These samplers come in various types, including dip samplers, bottle samplers, and pump samplers. Dip samplers involve dipping a container into the liquid, while bottle samplers usually have a syringe-like mechanism for drawing the liquid into a bottle. Pump samplers typically use a pump to transfer the liquid sample into a container.
Solid Samplers
Solid samplers are used for collecting samples of solid materials, such as powders, granules, or chunks. Scoops, spoons, and augers are common tools in this category. Scoops and spoons are designed for manual sampling, while augers are more suitable for hard or compacted materials, as they can drill into the material to obtain a sample.
Gas Samplers
Gas samplers collect samples of gases from a given environment. These are typically used in industries where monitoring the quality or composition of gases is critical, such as chemical manufacturing and environmental monitoring. Common types include grab samplers, which capture a single sample at a given moment, and continuous samplers, which collect gas samples over a period of time.
Factors to Consider When Selecting a Sampler
Material Compatibility
One of the first things to consider when selecting a sampler is the compatibility of the sampler material with the sample being collected. Some samples may react with certain materials, leading to contamination or degradation. For instance, stainless steel samplers are generally recommended for chemical-resistant applications, while plastic samplers may be suitable for less volatile substances.
Sampling Accuracy
The accuracy of the sample you collect directly impacts the quality of your quality control process. Ensure that the sampler you select can collect a truly representative sample. This can depend on the sampler’s design, the method of sample collection, and the material being sampled. Consult the manufacturer’s guidelines for specific recommendations on achieving optimal sampling accuracy.
Ease of Use
Consider the ease of use of the sampler. A user-friendly design will save time and reduce the risk of errors during the sampling process. Features such as ergonomic handles, clear markings, and straightforward mechanisms can make a big difference in the efficiency of sample collection.
Sample Size
The required sample size can vary depending on the type of analysis being conducted. Ensure the sampler you choose can collect the volume of material needed for accurate testing. Be mindful of the minimum and maximum sampling capacities of the tool.
Cleaning and Maintenance
Frequent sampling requires that samplers be easy to clean and maintain. Choose samplers designed for easy disassembly and cleaning to prevent cross-contamination between samples. Stainless steel samplers, for instance, are known for their ease of cleaning and durability.
Best Practices for Using Samplers
Proper Training
Ensure that all personnel involved in sample collection are adequately trained in the proper use of the chosen samplers. Training should cover the correct technique for using the sampler, maintaining hygiene to avoid contamination, and understanding the significance of obtaining a representative sample.
Regular Calibration
Regularly calibrate and maintain samplers to ensure they perform accurately. Calibration should be done according to the manufacturer’s guidelines, and any signs of wear and tear should be addressed promptly.
Documenting the Procedure
Documenting the sampling process can help maintain consistency and traceability. It is essential to record details such as the date and time of sampling, the sampler used, the person performing the sampling, and any observations made during the process. This documentation can be invaluable in audits and quality control assessments.
Preventing Contamination
Contamination can severely impact the accuracy of a sample. Always use clean, sterilized equipment and follow strict hygiene protocols. If using a reusable sampler, ensure it is thoroughly cleaned between uses. In some cases, single-use disposable samplers may be more appropriate to avoid cross-contamination.
Following Regulatory Standards
Compliance with industry and regulatory standards is crucial. Stay updated on the relevant guidelines and standards applicable to your industry and ensure your sampling procedures align with these requirements. This compliance boosts credibility and helps avoid legal and financial repercussions.
The Impact of Effective Sampling on Manufacturing
Effective sampling in manufacturing extends beyond merely ensuring product quality. It plays a critical role in optimizing production efficiency, reducing waste, and improving overall customer satisfaction. By identifying defects early, manufacturers can make necessary adjustments, thereby saving time and resources in the production process. This proactive approach leads to more reliable products and enhances the company’s reputation for delivering high-quality goods.
In conclusion, the selection and use of samplers in manufacturing are pivotal aspects of quality control. By understanding the different types of samplers, considering key factors in their selection, and following best practices, manufacturers can ensure they collect accurate and representative samples. This commitment to precision and quality not only meets industry standards but also drives efficiency and customer satisfaction in the long run.
資料ダウンロード
QCD調達購買管理クラウド「newji」は、調達購買部門で必要なQCD管理全てを備えた、現場特化型兼クラウド型の今世紀最高の購買管理システムとなります。
ユーザー登録
調達購買業務の効率化だけでなく、システムを導入することで、コスト削減や製品・資材のステータス可視化のほか、属人化していた購買情報の共有化による内部不正防止や統制にも役立ちます。
NEWJI DX
製造業に特化したデジタルトランスフォーメーション(DX)の実現を目指す請負開発型のコンサルティングサービスです。AI、iPaaS、および先端の技術を駆使して、製造プロセスの効率化、業務効率化、チームワーク強化、コスト削減、品質向上を実現します。このサービスは、製造業の課題を深く理解し、それに対する最適なデジタルソリューションを提供することで、企業が持続的な成長とイノベーションを達成できるようサポートします。
オンライン講座
製造業、主に購買・調達部門にお勤めの方々に向けた情報を配信しております。
新任の方やベテランの方、管理職を対象とした幅広いコンテンツをご用意しております。
お問い合わせ
コストダウンが利益に直結する術だと理解していても、なかなか前に進めることができない状況。そんな時は、newjiのコストダウン自動化機能で大きく利益貢献しよう!
(Β版非公開)