- お役立ち記事
- Selection Criteria for Cabinet and Rack Manufacturers by Major Buyers
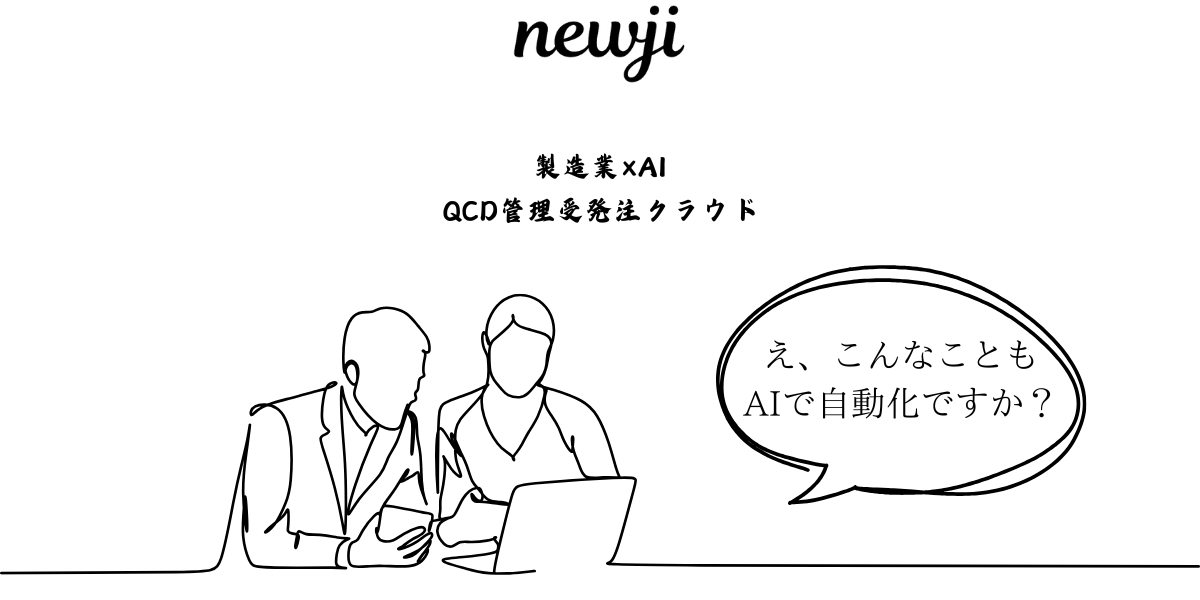
Selection Criteria for Cabinet and Rack Manufacturers by Major Buyers
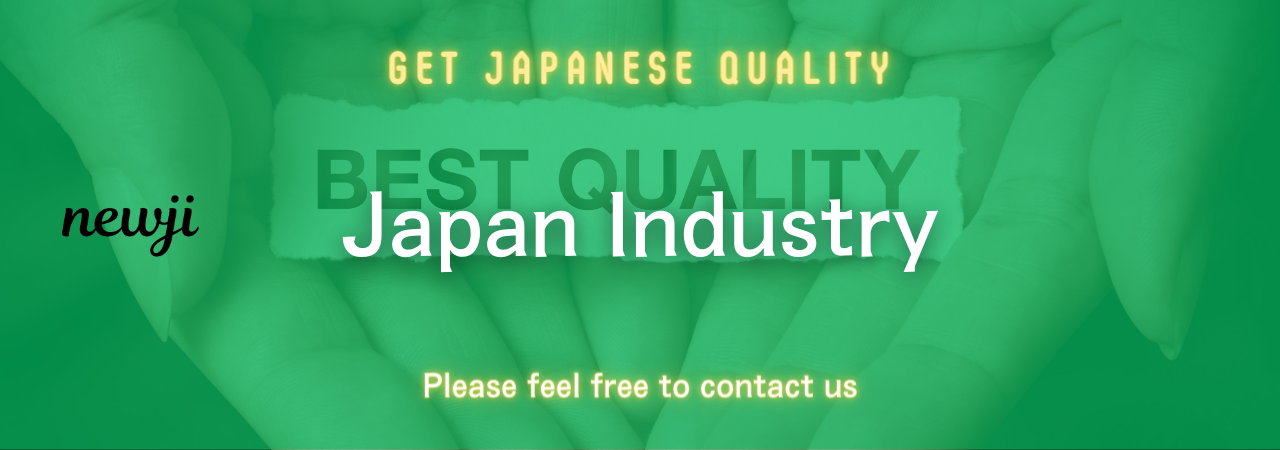
目次
Introduction
Choosing the right cabinet and rack manufacturer can be crucial for major buyers.
The quality of these products can significantly impact the efficiency and organization of a business, whether it’s in retail, warehousing, or manufacturing.
Therefore, it’s important to use clear selection criteria when evaluating different manufacturers.
This guide aims to provide a comprehensive overview of key factors to consider, ensuring that buyers make informed decisions.
Quality of Materials
One of the first criteria to consider is the quality of materials used by the manufacturer.
High-quality cabinets and racks are often made from durable metals like steel or high-grade aluminum.
These materials not only ensure the longevity of the products but also offer greater resistance to wear and tear.
Ask for material specifications and, if possible, visit the manufacturer to inspect the materials firsthand.
Durability
Durability is another essential aspect.
Products that are resistant to corrosion, scratches, and impacts are more likely to last longer.
Inquire about the manufacturer’s tests for durability and request product samples to evaluate this aspect yourself.
Sustainability
Sustainability is increasingly important in today’s market.
Check if the manufacturer uses eco-friendly materials and processes.
Many companies now prefer to work with manufacturers that meet environmental standards and certifications.
Manufacturing Capabilities
Manufacturing capabilities are crucial when selecting a manufacturer.
These include the technology they use, their production capacity, and the skill level of their workforce.
A manufacturer with advanced technology, like computer-aided design (CAD) and automated production lines, is more likely to produce high-quality products consistently.
Production Capacity
It’s essential to ensure that the manufacturer can meet your demand within the agreed timeframe.
Large-scale buyers require manufacturers capable of handling bulk orders without compromising on quality.
Evaluate their production capacity and lead times to make an informed decision.
Innovative Technology
Technology plays a crucial role in modern manufacturing.
Manufacturers who keep up with the latest technology trends are often more efficient and produce better-quality products.
Check if the manufacturer invests in innovation and employs advanced technologies in their production processes.
Customization Options
Customization is another critical factor.
Every business has unique needs, and a one-size-fits-all approach rarely works.
A manufacturer that offers custom design options can provide tailored solutions to meet your specific requirements.
Design Flexibility
Evaluate whether the manufacturer can modify designs based on your specifications.
This includes different sizes, colors, and configurations.
Customizable options add value and functionality to the final product, making it more suited to your needs.
Prototyping Services
Prototyping services are invaluable when you need custom solutions.
Manufacturers that offer prototyping can create sample units based on your specifications, allowing you to evaluate the design and make necessary adjustments before placing a large order.
Compliance and Certifications
Compliance with industry standards and regulations is non-negotiable.
Ensure that the manufacturer adheres to relevant quality and safety standards.
Valid certifications are proof that the manufacturer is committed to maintaining high standards.
ISO Certification
ISO certification is a good indicator that the manufacturer follows international standards for quality management.
ISO 9001 is the most widely recognized certification, ensuring that the products meet customer and regulatory requirements consistently.
Safety Standards
Safety is paramount in any industry.
Ensure that the manufacturer complies with relevant safety standards, particularly if the cabinets or racks will be used in environments with specific safety requirements.
Check for certifications like OSHA or CE marking, which indicate compliance with safety regulations.
Cost and Pricing
While quality and customization options are crucial, pricing cannot be ignored.
Balancing cost with quality is essential to get the best value for your money.
Compare prices from multiple manufacturers to gauge market rates and ensure you’re getting a fair deal.
Transparent Pricing
Transparency in pricing helps avoid hidden costs.
Ensure that the manufacturer provides a detailed breakdown of costs, including materials, labor, and any additional services like shipping or installation.
Transparent pricing makes it easier to budget and plan your purchase.
Payment Terms
Flexible payment terms can also be a deciding factor.
Large-scale purchases can be expensive, and manufacturers that offer installment plans or deferred payment options can make the financial aspect more manageable.
Customer Service and Support
Good customer service is indicative of a manufacturer’s reliability.
It’s important to evaluate their responsiveness, problem-solving skills, and overall customer support.
Communication
Effective communication is crucial throughout the production and delivery process.
Ensure that the manufacturer is easily reachable and provides regular updates about your order status.
After-Sales Support
After-sales support is equally important.
A manufacturer that offers support services like installation, maintenance, and troubleshooting adds value to your purchase.
Good after-sales support ensures that any issues are resolved promptly, minimizing disruptions to your operations.
Reputation and Track Record
The reputation of a manufacturer can provide valuable insights into their reliability and quality.
Customer Reviews
Checking customer reviews and testimonials can give you an idea of the manufacturer’s strengths and weaknesses.
Look for reviews on independent platforms to get an unbiased perspective.
References
Ask the manufacturer for references from previous clients.
Speaking directly with other buyers can provide insights into their experiences and help you gauge the manufacturer’s reliability.
Conclusion
Selecting the right cabinet and rack manufacturer involves a careful evaluation of several factors.
By considering the quality of materials, manufacturing capabilities, customization options, compliance and certifications, cost, customer service, and reputation, major buyers can make informed decisions that align with their organizational needs.
Make sure to perform thorough research and due diligence before finalizing your choice to ensure you partner with a manufacturer that meets your expectations.
資料ダウンロード
QCD調達購買管理クラウド「newji」は、調達購買部門で必要なQCD管理全てを備えた、現場特化型兼クラウド型の今世紀最高の購買管理システムとなります。
ユーザー登録
調達購買業務の効率化だけでなく、システムを導入することで、コスト削減や製品・資材のステータス可視化のほか、属人化していた購買情報の共有化による内部不正防止や統制にも役立ちます。
NEWJI DX
製造業に特化したデジタルトランスフォーメーション(DX)の実現を目指す請負開発型のコンサルティングサービスです。AI、iPaaS、および先端の技術を駆使して、製造プロセスの効率化、業務効率化、チームワーク強化、コスト削減、品質向上を実現します。このサービスは、製造業の課題を深く理解し、それに対する最適なデジタルソリューションを提供することで、企業が持続的な成長とイノベーションを達成できるようサポートします。
オンライン講座
製造業、主に購買・調達部門にお勤めの方々に向けた情報を配信しております。
新任の方やベテランの方、管理職を対象とした幅広いコンテンツをご用意しております。
お問い合わせ
コストダウンが利益に直結する術だと理解していても、なかなか前に進めることができない状況。そんな時は、newjiのコストダウン自動化機能で大きく利益貢献しよう!
(Β版非公開)