- お役立ち記事
- Selection criteria for insulating paste coating equipment for chip parts
月間77,185名の
製造業ご担当者様が閲覧しています*
*2025年2月28日現在のGoogle Analyticsのデータより
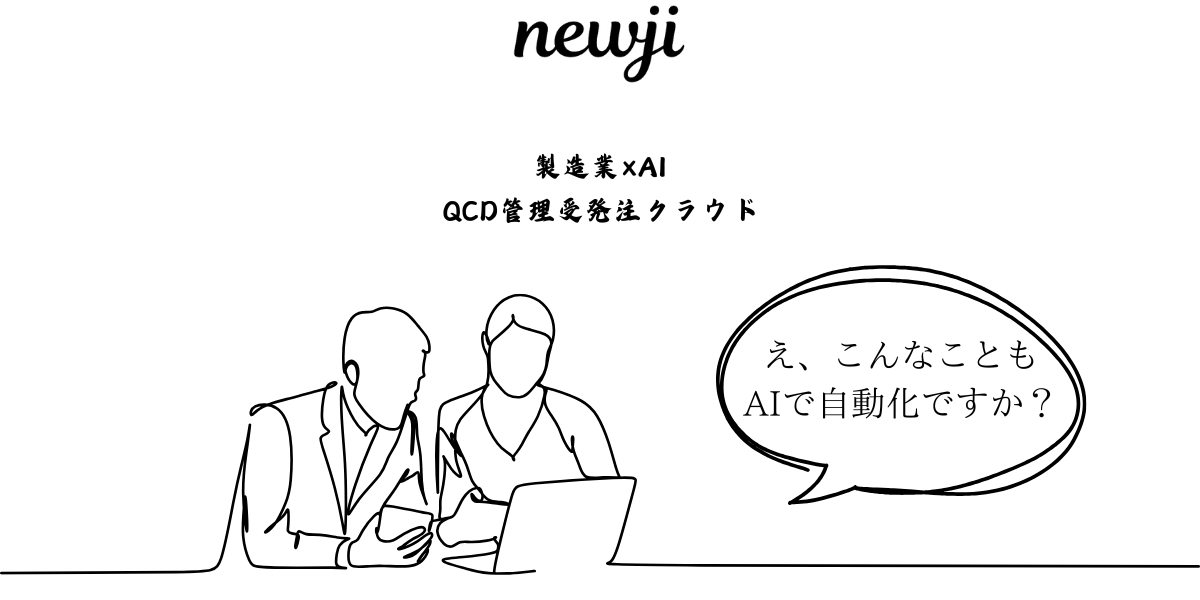
Selection criteria for insulating paste coating equipment for chip parts
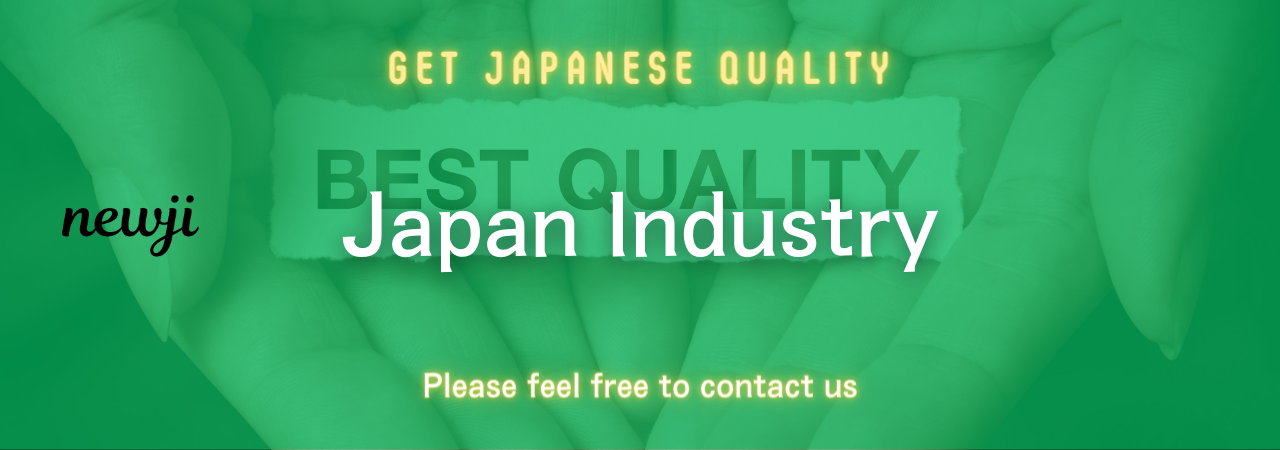
目次
Understanding Insulating Paste Coating Equipment
Selecting the right insulating paste coating equipment for chip parts is crucial for ensuring the optimal performance and longevity of electronic components.
These coatings are designed to protect chip parts from external factors such as moisture, dust, and other contaminants that can affect their utility.
To make an informed decision, it is essential to have a comprehensive understanding of what insulating paste coating equipment entails and its role in electronic manufacturing.
What is Insulating Paste Coating?
Insulating paste coatings are specialized substances applied to electronic chip parts to create a protective barrier.
This barrier helps to prevent short circuits and ensures that the components remain functional in various environmental conditions.
The coating process involves meticulous application techniques that require precise machinery, thereby making the choice of equipment critically important.
Key Selection Criteria for Equipment
When selecting insulating paste coating equipment, several factors need to be considered to ensure that the machinery used will meet the production needs effectively.
1. Type of Coating Material
The type of insulating paste being used has a significant impact on the choice of equipment.
Different materials have varying viscosities and require different application methods.
For instance, some coatings may need specialized nozzles to ensure uniform application, while others might require specific temperature settings to maintain their properties during the coating process.
2. Precision and Consistency in Application
Advanced electronic components demand high precision in coating application.
The equipment chosen should provide consistent results across all parts manufactured.
It should enable fine control over the thickness and evenness of the coating layer, ensuring no area is left unprotected.
Precision in application not only affects the performance of chip parts but also influences the reliability and durability of the devices in which they are used.
3. Production Volume and Throughput
Another crucial factor is the production volume or throughput of the coating equipment.
Manufacturers should consider their current and future needs to choose equipment that can handle the desired number of units within the available time frame.
High-volume production requires machines that can operate reliably over long periods without significant downtime or maintenance.
4. Equipment Versatility and Flexibility
The ability of the coating equipment to adapt to different chip sizes and designs is essential.
The rapid advancement in electronics technology often sees changes in component design, which may necessitate modifications in the coating application.
Choosing versatile equipment that can accommodate various designs without extensive adjustments can save time and resources in adapting to new production demands.
5. Ease of Operation and Maintenance
Operating and maintaining the coating equipment should be manageable for the existing workforce.
Machines that are user-friendly and require minimal intervention enhance productivity.
Furthermore, ease of maintenance ensures that any downtime is minimized, directly impacting the efficiency of the manufacturing process.
6. Cost Efficiency
The initial cost of acquiring coating equipment can be substantial.
However, balancing purchase costs with operational efficiency and maintenance expenses provides a clearer picture of long-term investment.
Manufacturers should consider not only the upfront price but also the cost of operation, including energy consumption, repairs, and part replacements, to evaluate the true cost efficiency of the equipment.
Advancements in Coating Technologies
In recent years, there have been significant advancements in insulating paste coating technologies.
These innovations offer enhanced protection and improved application methodologies, paving the way for even more sophisticated electronic applications.
Robotic Automation
One of the most notable advancements is the integration of robotic automation.
Robotic systems offer unparalleled precision and consistency, reducing human error in the coating process.
They are capable of multitasking, such as handling and coating, thereby streamlining production lines and improving output quality.
Real-time Monitoring and Adjustment
Contemporary coating machines often come equipped with sensors that allow for real-time monitoring of the coating process.
These sensors can detect variations in application and make automatic adjustments to ensure uniformity and adherence to specifications.
This capability leads to higher yield rates and fewer rejects, further optimizing manufacturing efficiency.
Environmentally Friendly Practices
As environmental concerns grow, the demand for eco-friendly manufacturing practices increases.
Modern coating equipment often supports sustainable practices, including the use of less harmful materials, efficient energy use, and recycling options for waste materials.
Choosing eco-conscious machinery can enhance a manufacturer’s reputation and ensure compliance with environmental regulations.
Conclusion
The selection of insulating paste coating equipment for chip parts is a multi-faceted process.
By carefully considering factors such as material compatibility, precision requirements, production needs, and cost efficiency, manufacturers can make informed decisions that align with their operational goals.
Staying abreast of technological advancements, such as automation and eco-friendly options, ensures that the chosen equipment not only meets current standards but also is future-ready.
A thorough evaluation of these criteria facilitates the optimal choice of coating equipment, ultimately contributing to high-quality electronic manufacturing outcomes.
資料ダウンロード
QCD管理受発注クラウド「newji」は、受発注部門で必要なQCD管理全てを備えた、現場特化型兼クラウド型の今世紀最高の受発注管理システムとなります。
ユーザー登録
受発注業務の効率化だけでなく、システムを導入することで、コスト削減や製品・資材のステータス可視化のほか、属人化していた受発注情報の共有化による内部不正防止や統制にも役立ちます。
NEWJI DX
製造業に特化したデジタルトランスフォーメーション(DX)の実現を目指す請負開発型のコンサルティングサービスです。AI、iPaaS、および先端の技術を駆使して、製造プロセスの効率化、業務効率化、チームワーク強化、コスト削減、品質向上を実現します。このサービスは、製造業の課題を深く理解し、それに対する最適なデジタルソリューションを提供することで、企業が持続的な成長とイノベーションを達成できるようサポートします。
製造業ニュース解説
製造業、主に購買・調達部門にお勤めの方々に向けた情報を配信しております。
新任の方やベテランの方、管理職を対象とした幅広いコンテンツをご用意しております。
お問い合わせ
コストダウンが利益に直結する術だと理解していても、なかなか前に進めることができない状況。そんな時は、newjiのコストダウン自動化機能で大きく利益貢献しよう!
(β版非公開)