- お役立ち記事
- Selection criteria for quality management certification bodies and the certification process
Selection criteria for quality management certification bodies and the certification process
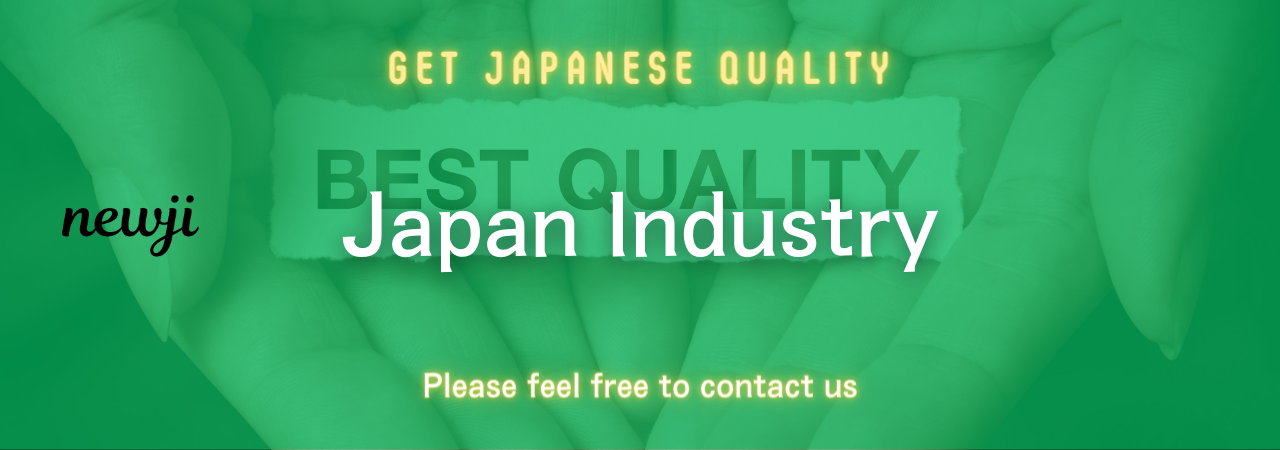
Embarking on the journey of achieving quality management certification is pivotal for organizations aiming to enhance their operational standards and gain a competitive edge in the market. Central to this endeavor is the selection of a competent certification body and navigating the certification process effectively. This article elucidates the essential criteria to consider when choosing a quality management certification body and outlines the steps involved in the certification process to ensure comprehensive understanding and successful completion.
Importance of Quality Management Certification
Quality management certification, such as ISO 9001, acts as a testament to an organization’s commitment to maintaining high standards and continuous improvement in its operations. It enhances customer trust, operational efficiency, and compliance with industry regulations. Therefore, selecting the right certification body to oversee this process is critical.
Key Criteria for Selecting a Certification Body
1. Accreditation Status:
– Ensure the certification body is accredited by a recognized national or international accreditation body. Accreditation signifies that the certification body follows strict guidelines and maintains high standards in its auditing process.
2. Industry Experience:
– Consider the certification body’s experience in your specific industry. Familiarity with industry-specific standards and challenges ensures that the audit process is relevant and practical.
3. Reputation and Track Record:
– Investigate the certification body’s reputation and track record. Reliable bodies often have testimonials, case studies, or references that demonstrate their credibility and effectiveness.
4. Audit Process:
– Understand the thoroughness of the certification body’s audit process. A detailed and rigorous audit ensures that all aspects of the quality management system are evaluated comprehensively.
5. Geographical Reach:
– If your organization operates internationally, selecting a certification body with a global presence ensures consistent standards across different locations.
6. Cost:
– While cost should not be the sole determining factor, it is essential to consider the overall fee structure and ensure it reflects the scope and depth of the audit services provided.
7. Customer Support:
– Consider the level of support and communication the certification body offers. Effective communication throughout the certification process can streamline operations and clarify any procedural uncertainties.
8. Post-Certification Services:
– Evaluate the additional services offered post-certification, such as regular surveillance audits, training, and support in maintaining compliance. These services ensure continuous adherence to standards and improvement in quality management systems.
The Certification Process
Achieving quality management certification involves a series of steps designed to assess and validate an organization’s adherence to established quality standards. Here’s an overview of the typical certification process:
1. Pre-Assessment:
– Organizations may opt for a pre-assessment or gap analysis where the certification body reviews the existing quality management system against the required standards. This step identifies areas that need improvement before the formal audit.
2. Application and Contract:
– Submit an application to the selected certification body. Upon acceptance, both parties enter into a contractual agreement detailing the scope of certification, audit plans, and costs.
3. Stage 1 Audit (Documentation Review):
– During this initial audit phase, the certification body reviews the organization’s documentation, including quality manuals, procedures, and records, to ensure they meet the required standards. This may be conducted on-site or remotely.
4. Stage 2 Audit (Implementation Review):
– This on-site audit involves evaluating the practical implementation of the quality management system. Auditors will review practices, interview staff, and observe operational processes to ensure compliance with standards.
5. Audit Report and Corrective Actions:
– Post-audit, the certification body provides a detailed report highlighting any non-conformities. Organizations must address these non-conformities through corrective actions within a specified timeframe.
6. Certification Decision:
– Upon successful resolution of non-conformities and satisfactory implementation of corrective actions, the certification body reviews the audit findings and makes a decision on certification.
7. Issuance of Certification:
– Upon approval, the certification body issues the quality management certificate, signifying compliance with the relevant standards.
8. Surveillance Audits:
– Periodic surveillance audits (typically annual) are conducted to ensure the organization maintains compliance with quality standards. These audits are less comprehensive than the initial certification audit but are crucial for continual adherence.
9. Recertification Audit:
– Organizations must undergo a recertification audit, usually every three years, to renew their certification. This process is similar to the initial certification audit, ensuring ongoing compliance and improvements in the quality management system.
Achieving quality management certification is a strategic move towards demonstrating an organization’s commitment to excellence and customer satisfaction. By carefully selecting a competent certification body and adhering to a structured certification process, organizations can successfully attain and maintain certification, thereby reaping the numerous benefits it offers.
Evaluating accreditation status, industry experience, reputation, and audit process of certification bodies, along with a clear understanding of the certification steps, empowers organizations to make informed decisions and approaches the certification journey with confidence and clarity. By doing so, businesses not only comply with industry standards but also foster a culture of continuous improvement and quality excellence.
資料ダウンロード
QCD調達購買管理クラウド「newji」は、調達購買部門で必要なQCD管理全てを備えた、現場特化型兼クラウド型の今世紀最高の購買管理システムとなります。
ユーザー登録
調達購買業務の効率化だけでなく、システムを導入することで、コスト削減や製品・資材のステータス可視化のほか、属人化していた購買情報の共有化による内部不正防止や統制にも役立ちます。
NEWJI DX
製造業に特化したデジタルトランスフォーメーション(DX)の実現を目指す請負開発型のコンサルティングサービスです。AI、iPaaS、および先端の技術を駆使して、製造プロセスの効率化、業務効率化、チームワーク強化、コスト削減、品質向上を実現します。このサービスは、製造業の課題を深く理解し、それに対する最適なデジタルソリューションを提供することで、企業が持続的な成長とイノベーションを達成できるようサポートします。
オンライン講座
製造業、主に購買・調達部門にお勤めの方々に向けた情報を配信しております。
新任の方やベテランの方、管理職を対象とした幅広いコンテンツをご用意しております。
お問い合わせ
コストダウンが利益に直結する術だと理解していても、なかなか前に進めることができない状況。そんな時は、newjiのコストダウン自動化機能で大きく利益貢献しよう!
(Β版非公開)