- お役立ち記事
- Selection of Motors for AGVs and Their Applications in Manufacturing
Selection of Motors for AGVs and Their Applications in Manufacturing
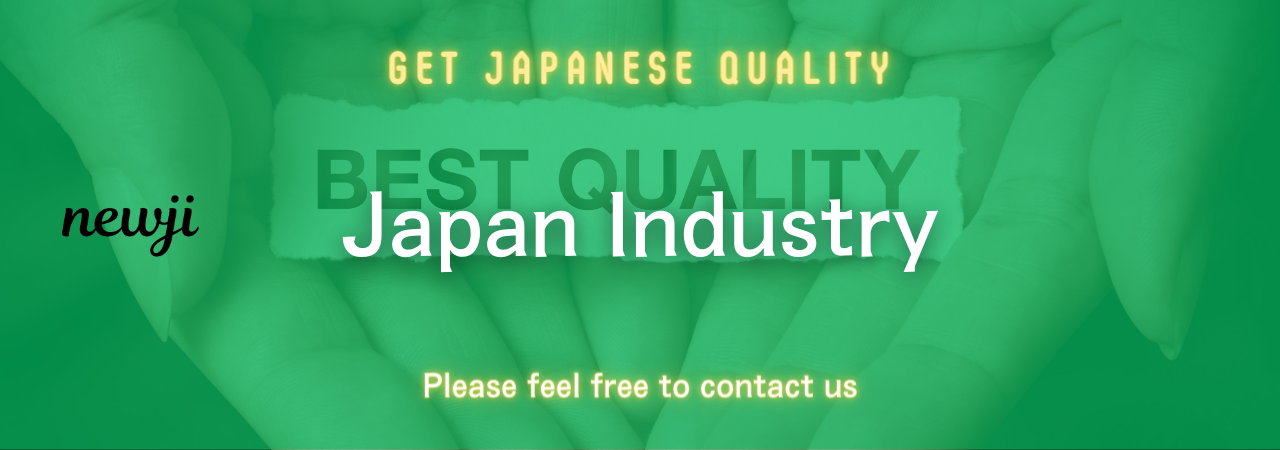
Automated Guided Vehicles (AGVs) have revolutionized the manufacturing industry by automating material handling processes, improving efficiency, and reducing labor costs.
A critical component of AGVs is the motor, which drives their movement and functionality.
Choosing the right motor is paramount to ensure the reliable performance of AGVs.
This article will explore the selection criteria for motors in AGVs and their applications within the manufacturing sector.
目次
Understanding AGVs and Their Importance
AGVs are automated vehicles used widely in manufacturing and warehousing to transport materials.
They navigate via various technologies, including lasers, cameras, and specially marked lines on the factory floor.
The primary advantage of AGVs is their ability to work continuously without human intervention, significantly boosting productivity.
In the fast-paced manufacturing world, the reliance on AGVs has become more prominent.
They offer flexibility in handling different types of materials, reduce the likelihood of errors, and enhance the overall safety of the workplace, as they strictly follow predefined paths and rules.
Key Considerations When Selecting Motors for AGVs
Selecting the appropriate motor for an AGV involves several key considerations, ensuring optimal performance and durability.
Let’s delve into these factors that will guide you in making an informed choice.
Load Capacity
The first factor to consider is the load capacity of the AGV.
The motor must be powerful enough to handle the weight of the materials being transported.
Undersized motors can lead to inefficiencies, overheating, and mechanical failures.
Conversely, using oversized motors can be an unnecessary cost burden without significant performance improvements.
Torque and Speed Requirements
The required torque and speed greatly influence motor selection.
Torque is essential for moving loads and overcoming resistance, while speed determines how quickly the AGV can transport materials from one point to another.
Different manufacturing environments have varying requirements for torque and speed.
High-torque motors are crucial for heavy-duty applications, whereas high-speed motors are ideal for tasks that demand swift movement of lighter loads.
Power Supply and Efficiency
AGVs typically rely on batteries for their power supply.
Selecting an energy-efficient motor can extend battery life and reduce downtime for recharging.
Consider motors designed for low power consumption without sacrificing performance.
Brushless DC motors are known for their efficiency and are often preferred in AGV applications.
Control Systems Compatibility
Ensuring the motor is compatible with the AGV’s control systems is vital for seamless integration.
Modern AGVs are equipped with sophisticated control systems that manage navigation, speed, and obstacle avoidance.
The motor should support these functionalities by offering precise control over its operations, often through advanced feedback mechanisms.
Environmental Conditions
Manufacturing environments can vary widely in terms of temperature, humidity, and exposure to dust or chemicals.
Select a motor designed to withstand these conditions without degradation in performance.
Special coatings, sealed constructions, and robust materials can enhance motor durability in harsh environments.
Common Types of Motors Used in AGVs
Different types of motors serve various purposes in AGV applications, each with its own set of advantages.
Let’s explore the most commonly used motor types.
DC Motors
DC (Direct Current) motors are widely used in AGVs due to their simplicity and ease of control.
They offer good torque at low speeds and can be directly driven by battery power.
DC motors are ideal for applications where precise speed control and reliability are paramount.
AC Motors
AC (Alternating Current) motors are less common in AGVs but are used in specific scenarios where high power and efficiency are required.
They are known for their durability and ability to handle heavy loads.
AC motors, typically three-phase induction motors, require an inverter to convert battery DC power to AC.
Though costlier and more complex, they are perfect for high-capacity AGVs.
Brushless DC Motors (BLDC)
Brushless DC motors have become the preferred choice for many AGV applications.
They offer high efficiency, reliability, and a longer lifespan due to the absence of brushes, which wear out over time.
BLDC motors provide excellent speed and torque control, making them suitable for a wide range of tasks within a manufacturing environment.
Stepper Motors
Stepper motors are not as commonly used in AGVs but can be valuable for specific applications requiring precise positioning and controlled movements.
They offer excellent repeatability and can hold their position without the need for feedback sensors, making them ideal for applications where precision is crucial.
Applications of Motors in AGVs within Manufacturing
Motors in AGVs play a vital role in various manufacturing applications.
Let’s look at how these motors contribute to different tasks within the industry.
Material Transport
One of the primary applications of AGVs in manufacturing is the transport of raw materials, components, and finished products.
Motors that provide consistent and reliable performance enable AGVs to handle these tasks efficiently, reducing manual labor and enhancing productivity.
Assembly Line Integration
In many manufacturing facilities, AGVs are integrated into assembly lines to move parts between different workstations.
Motors with precise control and high reliability ensure smooth and timely transfers, maintaining the flow of the assembly process without interruptions.
Warehouse Management
In warehousing operations within manufacturing, AGVs equipped with efficient motors are used for tasks such as inventory management, picking and placing items, and rearranging goods.
Motors that offer a balance of speed and torque are essential for these tasks to ensure quick and accurate movements.
Quality Assurance and Inspection
AGVs also play a role in transporting products through quality assurance and inspection areas.
Motors that provide smooth and controlled movements help maintain the integrity of products during inspections, ensuring they meet quality standards before leaving the facility.
Conclusion: Selecting the Right Motor for AGVs
Choosing the right motor for AGVs is critical for optimizing their performance and reliability in manufacturing applications.
Factors such as load capacity, torque and speed requirements, power efficiency, control system compatibility, and environmental conditions must be carefully considered.
Depending on the specific needs of the application, different types of motors such as DC motors, AC motors, brushless DC motors, and stepper motors offer unique advantages.
Ensuring that the selected motor is well-suited for the intended tasks will enhance the overall efficiency and productivity of AGVs, contributing significantly to the success of manufacturing operations.
資料ダウンロード
QCD調達購買管理クラウド「newji」は、調達購買部門で必要なQCD管理全てを備えた、現場特化型兼クラウド型の今世紀最高の購買管理システムとなります。
ユーザー登録
調達購買業務の効率化だけでなく、システムを導入することで、コスト削減や製品・資材のステータス可視化のほか、属人化していた購買情報の共有化による内部不正防止や統制にも役立ちます。
NEWJI DX
製造業に特化したデジタルトランスフォーメーション(DX)の実現を目指す請負開発型のコンサルティングサービスです。AI、iPaaS、および先端の技術を駆使して、製造プロセスの効率化、業務効率化、チームワーク強化、コスト削減、品質向上を実現します。このサービスは、製造業の課題を深く理解し、それに対する最適なデジタルソリューションを提供することで、企業が持続的な成長とイノベーションを達成できるようサポートします。
オンライン講座
製造業、主に購買・調達部門にお勤めの方々に向けた情報を配信しております。
新任の方やベテランの方、管理職を対象とした幅広いコンテンツをご用意しております。
お問い合わせ
コストダウンが利益に直結する術だと理解していても、なかなか前に進めることができない状況。そんな時は、newjiのコストダウン自動化機能で大きく利益貢献しよう!
(Β版非公開)