- お役立ち記事
- Selection of suppliers for flip-up gates
月間76,176名の
製造業ご担当者様が閲覧しています*
*2025年3月31日現在のGoogle Analyticsのデータより
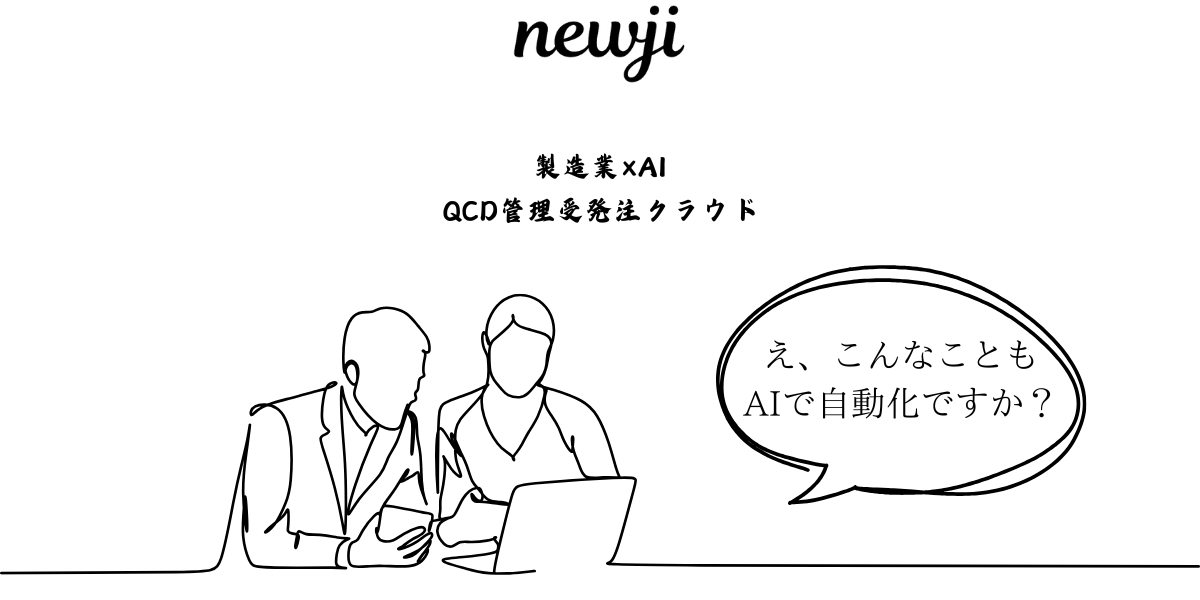
Selection of suppliers for flip-up gates
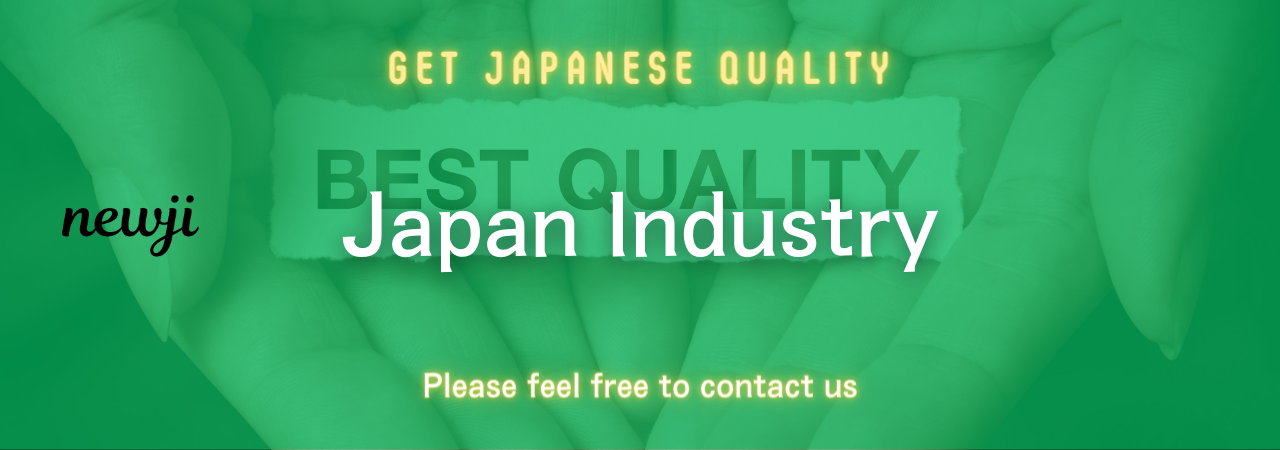
When it comes to selecting the right suppliers for flip-up gates, there are several important factors to consider.
The process involves evaluating various aspects of potential suppliers to ensure that the final decision contributes to the quality, reliability, and cost-effectiveness of the flip-up gates produced.
In this article, we’ll explore key considerations for selecting suppliers and provide insights into how to make informed decisions.
目次
Understanding Flip-Up Gates
Flip-up gates are commonly used in various applications, including warehouse management, automotive industries, and residential properties.
They are designed to provide easy access and secure closure in different settings.
Due to their versatile applications, quality and functionality are crucial factors that need to be assured during the manufacturing process.
Importance of Supplier Selection
Choosing the right supplier is vital because it can significantly impact the quality and cost of the final product.
A reliable supplier can ensure the delivery of high-quality components on time, which is crucial for maintaining production schedules and customer satisfaction.
On the other hand, a poor selection can lead to delayed projects, increased costs, and lower product standards.
Key Considerations for Supplier Selection
1. Quality Standards
The supplier’s commitment to quality should be the top priority.
Check whether they conform to international quality standards, such as ISO certifications.
Inspect their quality assurance processes and consider requesting samples to assess the quality of their components.
Make sure they have a reputation for maintaining high standards consistently.
2. Cost-Effectiveness
While quality is essential, the cost is also a crucial factor.
Evaluate the pricing models of potential suppliers and compare them with industry standards.
It’s important to find a balance between cost and quality to ensure the profitability of your projects.
Avoid suppliers that offer prices significantly lower than the market as they might compromise on quality or have hidden costs.
3. Reliability and Timeliness
Timely delivery is critical to ensure that your production schedules are not disrupted.
Investigate the supplier’s track record for on-time deliveries and their capacity to meet deadlines under various circumstances.
A reliable supplier should have contingency plans for unforeseen events that could affect delivery times.
4. Technical Capability
Ensure that the supplier has the technical expertise and equipment necessary to produce flip-up gate components at the required specifications.
Evaluate their manufacturing capabilities and inquire about the technologies they use.
Suppliers who invest in modern technology are often more capable of meeting complex requirements efficiently.
5. Financial Stability
A supplier’s financial health is a good indicator of their ability to fulfill long-term contracts.
Check their financial background to ensure they have the resources to invest in any necessary upgrades or expansions.
This stability reduces the risk of a supplier going out of business midway through a project.
Building Strong Supplier Relationships
Beyond selecting the right supplier, fostering a strong relationship is equally important.
Good communication is key to understanding each other’s needs and expectations.
Establish regular meetings and updates to ensure both parties are aligned with objectives and deadlines.
Visit supplier facilities if possible to build a better understanding of their operations and capabilities.
This can also facilitate trust and openness between both parties, leading to long-term partnerships.
Leveraging Technology for Supplier Selection
In today’s digital age, technology can significantly enhance the supplier selection process.
Using supplier management software can help streamline evaluations, track performance, and ensure compliance with agreed-upon standards.
These tools also provide comprehensive analytics that can be used to drive improvement in the supplier selection process.
Conclusion
Selecting the right suppliers for flip-up gates is a multifaceted process involving careful consideration of quality standards, cost-effectiveness, reliability, technical capabilities, and financial stability.
Remember, the goal is to build a mutually beneficial relationship that ensures the consistent supply of quality components.
By focusing on these key areas and leveraging technology, you can make informed decisions that positively affect the success of your projects.
資料ダウンロード
QCD管理受発注クラウド「newji」は、受発注部門で必要なQCD管理全てを備えた、現場特化型兼クラウド型の今世紀最高の受発注管理システムとなります。
ユーザー登録
受発注業務の効率化だけでなく、システムを導入することで、コスト削減や製品・資材のステータス可視化のほか、属人化していた受発注情報の共有化による内部不正防止や統制にも役立ちます。
NEWJI DX
製造業に特化したデジタルトランスフォーメーション(DX)の実現を目指す請負開発型のコンサルティングサービスです。AI、iPaaS、および先端の技術を駆使して、製造プロセスの効率化、業務効率化、チームワーク強化、コスト削減、品質向上を実現します。このサービスは、製造業の課題を深く理解し、それに対する最適なデジタルソリューションを提供することで、企業が持続的な成長とイノベーションを達成できるようサポートします。
製造業ニュース解説
製造業、主に購買・調達部門にお勤めの方々に向けた情報を配信しております。
新任の方やベテランの方、管理職を対象とした幅広いコンテンツをご用意しております。
お問い合わせ
コストダウンが利益に直結する術だと理解していても、なかなか前に進めることができない状況。そんな時は、newjiのコストダウン自動化機能で大きく利益貢献しよう!
(β版非公開)