- お役立ち記事
- Selection of the basics of material mechanics and processing methods that new employees in the mechanical design department should learn
Selection of the basics of material mechanics and processing methods that new employees in the mechanical design department should learn
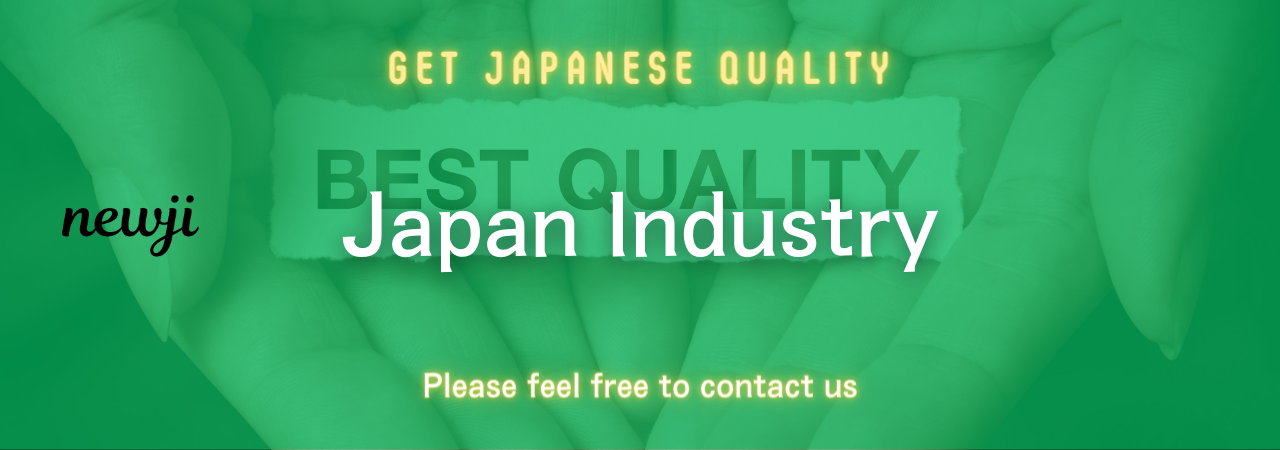
目次
Understanding Material Mechanics
When stepping into a mechanical design role, one of the foundational concepts every new employee should grasp is material mechanics.
This branch of engineering focuses on understanding how materials behave under various forces and environmental conditions.
Central to material mechanics are the concepts of stress and strain.
Stress refers to the internal resistance a material exhibits when subjected to a force, while strain is the deformation or displacement it undergoes.
By understanding these two notions, new employees can predict how materials will react when used in different applications.
Material mechanics also involves studying material properties such as elasticity, plasticity, and toughness.
Elasticity is the ability of a material to return to its original shape after deformation, whereas plasticity refers to a material’s capacity to undergo permanent deformation.
Toughness is a measure of how much energy a material can absorb before fracturing.
By familiarizing themselves with these properties, new employees can determine which materials will meet the performance requirements of a given design.
The Importance of Young’s Modulus
Young’s Modulus, often known as the elastic modulus, is a critical parameter when working with materials.
It quantifies a material’s ability to resist elastic (reversible) deformation under stress.
Knowing the Young’s Modulus is essential because it helps determine whether a material will undergo significant deformation when used in a mechanical component.
For instance, materials with a high Young’s Modulus, like steel, are stiffer and do not deform easily, making them ideal for structural applications where rigidity is crucial.
Conversely, materials with a low Young’s Modulus, such as rubber, are more flexible and are used where elasticity is desired.
Understanding Hardness and Ductility
Hardness and ductility are additional attributes critical to selecting suitable materials for mechanical design.
Hardness is a material’s resistance to indentation or surface deformation, making it crucial for components subject to wear and tear, like gears and cutting tools.
On the other hand, ductility refers to a material’s ability to undergo significant plastic deformation before rupture.
Materials that exhibit high ductility, such as gold and copper, can be stretched into wires without breaking, a property valuable in applications requiring significant shape changes.
Exploring Material Processing Methods
Once the basics of material mechanics are understood, the next step for new employees is to familiarize themselves with material processing methods.
These methods help transform raw materials into useful products and are pivotal in determining the final properties of mechanical components.
Common Shaping Processes
An essential aspect of material processing involves shaping raw materials into desired forms.
This includes techniques such as casting, forging, and machining.
– **Casting** involves pouring liquid material into a mold to achieve a specific shape once the material solidifies.
This process is particularly beneficial for creating complex shapes and is used for metal and plastic components.
– **Forging** utilizes compressive forces to shape the material, usually metals.
This process enhances the mechanical properties of the resulting components by aligning the internal grain structures, making them stronger and more reliable.
– **Machining** encompasses various subtractive operations such as drilling, turning, and milling.
It is used to refine the dimensions and surface finish of a part by removing excess material.
Understanding Joining Methods
In addition to shaping, new employees in mechanical design need to think about how individual components are assembled.
Joining methods play an integral role here, with common techniques including welding, bolting, and riveting.
– **Welding** is a method where two materials, usually metals, are joined by melting their edges and fusing them together, often using additional filler material.
It creates a permanent, strong bond and is prevalent in structural applications.
– **Bolting** involves using threaded fasteners to hold components together.
It offers the advantage of easy disassembly, ideal for scenarios where maintenance or repairs are frequent.
– **Riveting** is another permanent joining method where a rivet is placed through the components and mechanically deformed to hold them together.
This method is typically used in joining thin sheets, like in aerospace applications.
Surface Treatment and Coatings
The integrity and longevity of mechanical components can often be enhanced through surface treatment and coatings.
These processes add protective layers or alter the surface characteristics to improve resistance against corrosion, wear, and fatigue.
– **Plating** involves coating a metal with a thin layer of another metal to enhance its properties.
Common techniques include chrome plating for wear resistance and gold plating for electrical conductivity.
– **Anodizing** is typically used for aluminum to increase corrosion resistance and allow for dyeing the surface.
This electrochemical process forms a protective oxide layer, enhancing both aesthetic and functional qualities.
– **Heat treatment** like quenching and tempering alters the microstructure of metals, especially steels, to improve their strength and toughness.
By controlling the cooling rate of a heated metal, different mechanical properties can be achieved, suiting various applications.
Conclusion
In summary, new employees in the mechanical design department should ensure they have a comprehensive understanding of both material mechanics and the numerous processing methods available.
By mastering principles such as stress, strain, and material properties like elasticity and ductility, they can make informed decisions on material selection.
Familiarity with shaping techniques such as casting, forging, and machining, along with joining methods like welding and bolting, will empower them to create efficient and reliable designs.
Likewise, knowledge of surface treatments can enhance the performance and durability of mechanical components.
By acquiring these essential skills, new employees will be well-equipped to contribute to innovative and practical mechanical designs that meet both performance and cost criteria.
資料ダウンロード
QCD調達購買管理クラウド「newji」は、調達購買部門で必要なQCD管理全てを備えた、現場特化型兼クラウド型の今世紀最高の購買管理システムとなります。
ユーザー登録
調達購買業務の効率化だけでなく、システムを導入することで、コスト削減や製品・資材のステータス可視化のほか、属人化していた購買情報の共有化による内部不正防止や統制にも役立ちます。
NEWJI DX
製造業に特化したデジタルトランスフォーメーション(DX)の実現を目指す請負開発型のコンサルティングサービスです。AI、iPaaS、および先端の技術を駆使して、製造プロセスの効率化、業務効率化、チームワーク強化、コスト削減、品質向上を実現します。このサービスは、製造業の課題を深く理解し、それに対する最適なデジタルソリューションを提供することで、企業が持続的な成長とイノベーションを達成できるようサポートします。
オンライン講座
製造業、主に購買・調達部門にお勤めの方々に向けた情報を配信しております。
新任の方やベテランの方、管理職を対象とした幅広いコンテンツをご用意しております。
お問い合わせ
コストダウンが利益に直結する術だと理解していても、なかなか前に進めることができない状況。そんな時は、newjiのコストダウン自動化機能で大きく利益貢献しよう!
(Β版非公開)