- お役立ち記事
- Servo Motor Precision Testing and Tuning in Machine Tools
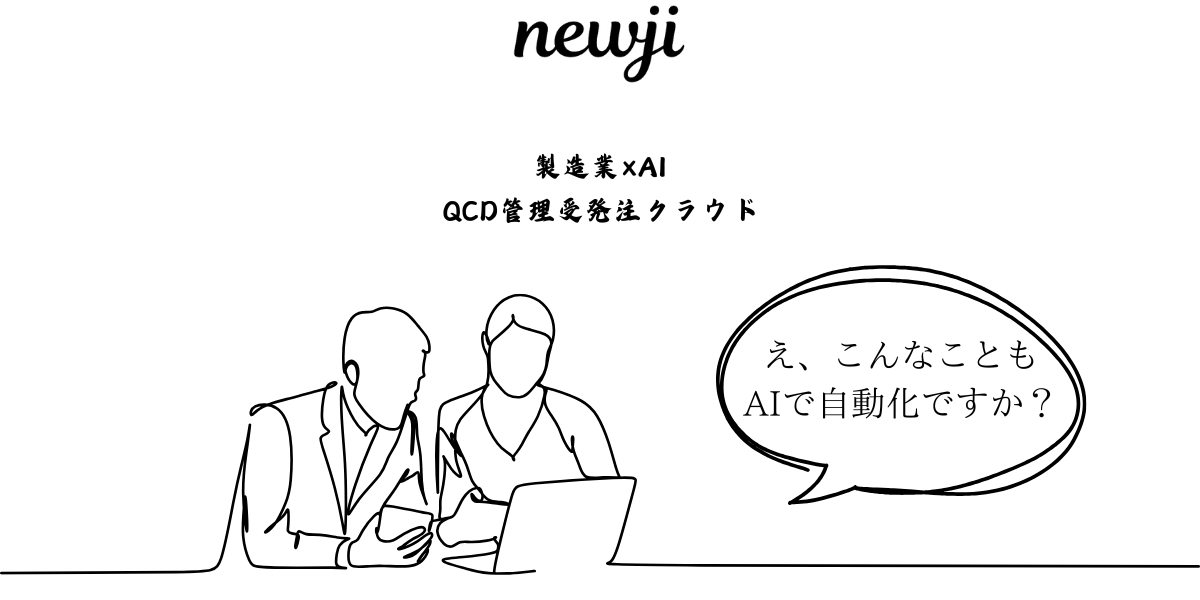
Servo Motor Precision Testing and Tuning in Machine Tools
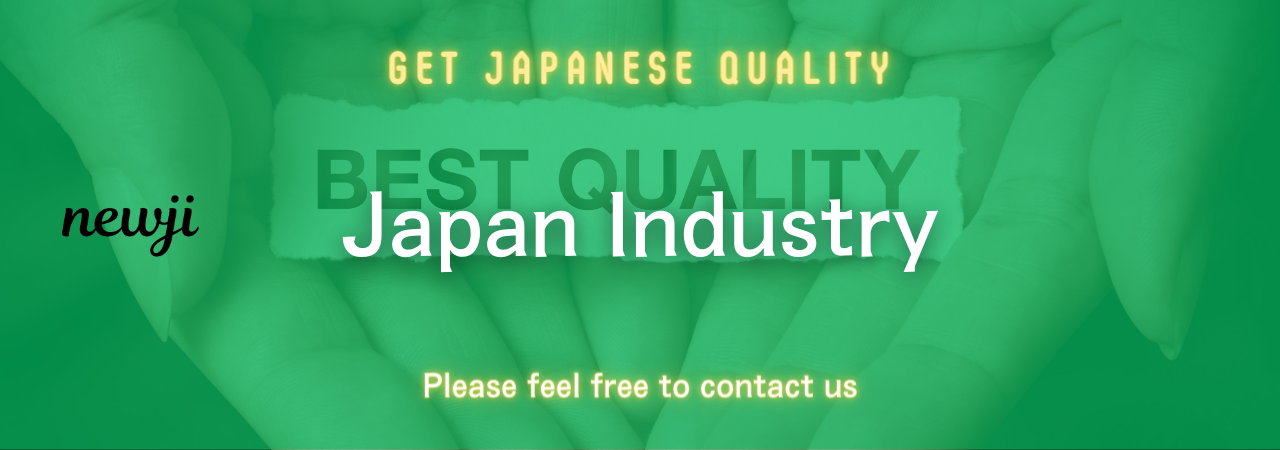
目次
Understanding Servo Motors in Machine Tools
Servo motors are integral in the operation of modern machine tools, playing a critical role in ensuring precision and accuracy.
They are electromechanical devices that translate electrical commands into precise physical movements.
The unique advantage of servo motors is their ability to provide controlled motion.
This makes them indispensable in tasks that require high precision, such as CNC machining, robotics, and automated manufacturing processes.
Components of Servo Motors
A typical servo motor consists of several key components: a DC motor, a feedback sensor, a controller, and a drive system.
Each component plays a vital role in maintaining the desired level of precision.
The DC motor is the core part that provides the rotational movement.
The feedback sensor is essential for monitoring the motor’s actual position, speed, or torque.
This sensor can either be an encoder or a resolver, depending on the specific application and precision requirements.
The controller processes the feedback from the sensor and compares it with the desired output.
It continuously adjusts the motor’s operations to correct any discrepancies, ensuring the motor’s output matches the input commands.
Finally, the drive system provides the necessary power to the motor, converting input electricity into mechanical motion.
The Importance of Precision Testing
Precision testing of servo motors in machine tools is crucial to ensure they perform optimally without deviations.
Such testing is fundamental in industries where minute errors can lead to significant product flaws or reduced efficiency.
Testing Procedures and Equipment
Several standardized testing procedures exist to evaluate servo motor performance.
1. **Static Testing**: This method involves testing the motor without any load to assess its functionality and the effectiveness of the control systems.
Static testing checks the electrical properties, insulation resistance, and continuity of the motor.
2. **Dynamic Testing**: This is carried out under operational conditions with loads applied.
Dynamic testing evaluates the motor’s performance in real-time scenarios, including speed, torque, and feedback accuracy.
3. **Thermal Testing**: This checks the motor’s temperature tolerance and its ability to disperse heat during operation.
Overheating can lead to failures, so thermal testing ensures the motor can operate efficiently under various conditions.
Advanced equipment, like oscilloscopes, spectrum analyzers, and thermal imaging cameras, are used to undertake these tests.
These tools help in accurately measuring various parameters, ensuring motors are functioning within the desired specifications.
Tuning Servo Motors for Optimal Performance
Once precision testing is done, tuning servo motors is the next essential step to optimize their performance.
Steps in Servo Motor Tuning
1. **System Identification**: Begin by identifying the system’s dynamics.
This involves understanding the motion requirements and the environment in which the motor operates.
Knowing these allows for appropriate parameter adjustments.
2. **Parameter Setting**: Adjusting control parameters, such as proportional gain, integral gain, and derivative gain, is crucial.
These parameters influence how the motor responds to control commands, potentially impacting speed, stability, and precision.
3. **Feedback Adjustment**: Fine-tuning the feedback system ensures that the motor’s movements accurately follow the input commands.
The feedback must be aligned accurately to synchronize the command signal and actual motor movement.
4. **Test Runs and Validation**: Perform test runs with the adjusted parameters in place.
Continuous monitoring is crucial during these runs to observe the motor’s performance and make any necessary tweaks.
Validation ensures that the tuned motor meets all operational expectations and safety standards.
Challenges in Servo Motor Precision Tuning
Despite technological advancements, several challenges remain in precision testing and tuning of servo motors.
Common Issues
1. **Environmental Factors**: External factors like temperature changes, humidity, and dust can impact motor performance.
Protective measures and regular maintenance are essential to mitigate these effects.
2. **Wear and Tear**: Over time, motors undergo mechanical wear which can reduce precision and efficiency.
Regular inspections and replacements of worn-out parts are crucial to maintain optimal performance.
3. **Electrical Noise**: Interference from other electronic devices can affect the motor’s electronic systems.
Effective shielding and grounding can help reduce noise, ensuring accurate signal processing.
4. **Complexity in Integration**: Integrating servo motors with other systems in machine tools can be challenging.
This requires a deep understanding of both the motor and the machine, often necessitating specialized skills and knowledge.
The Future of Servo Motors in Machine Tools
As technology evolves, so do servo motors.
Newer models are being developed with enhanced features, such as improved energy efficiency, reduced size, and intelligent control systems.
These advancements are paving the way for even more precise and versatile applications in machine tools.
Embracing Innovations
The use of artificial intelligence and machine learning is starting to play a role in servo motor technology.
By using data analytics, motors can learn and adapt to optimize performance over time, minimizing the need for manual tuning.
Furthermore, innovations in materials and design are striving to improve durability and reduce costs.
This makes servo motors more accessible and beneficial to a broader range of industries.
In conclusion, precision testing and tuning of servo motors in machine tools are critical processes that ensure everything from efficiency to product quality.
Despite the challenges, continuous advancement in technology and methods promises a future where these motors are more precise, reliable, and versatile than ever before.
資料ダウンロード
QCD調達購買管理クラウド「newji」は、調達購買部門で必要なQCD管理全てを備えた、現場特化型兼クラウド型の今世紀最高の購買管理システムとなります。
ユーザー登録
調達購買業務の効率化だけでなく、システムを導入することで、コスト削減や製品・資材のステータス可視化のほか、属人化していた購買情報の共有化による内部不正防止や統制にも役立ちます。
NEWJI DX
製造業に特化したデジタルトランスフォーメーション(DX)の実現を目指す請負開発型のコンサルティングサービスです。AI、iPaaS、および先端の技術を駆使して、製造プロセスの効率化、業務効率化、チームワーク強化、コスト削減、品質向上を実現します。このサービスは、製造業の課題を深く理解し、それに対する最適なデジタルソリューションを提供することで、企業が持続的な成長とイノベーションを達成できるようサポートします。
オンライン講座
製造業、主に購買・調達部門にお勤めの方々に向けた情報を配信しております。
新任の方やベテランの方、管理職を対象とした幅広いコンテンツをご用意しております。
お問い合わせ
コストダウンが利益に直結する術だと理解していても、なかなか前に進めることができない状況。そんな時は、newjiのコストダウン自動化機能で大きく利益貢献しよう!
(Β版非公開)