- お役立ち記事
- Setting appropriate inventory amounts of raw materials for manufacturing to improve production efficiency
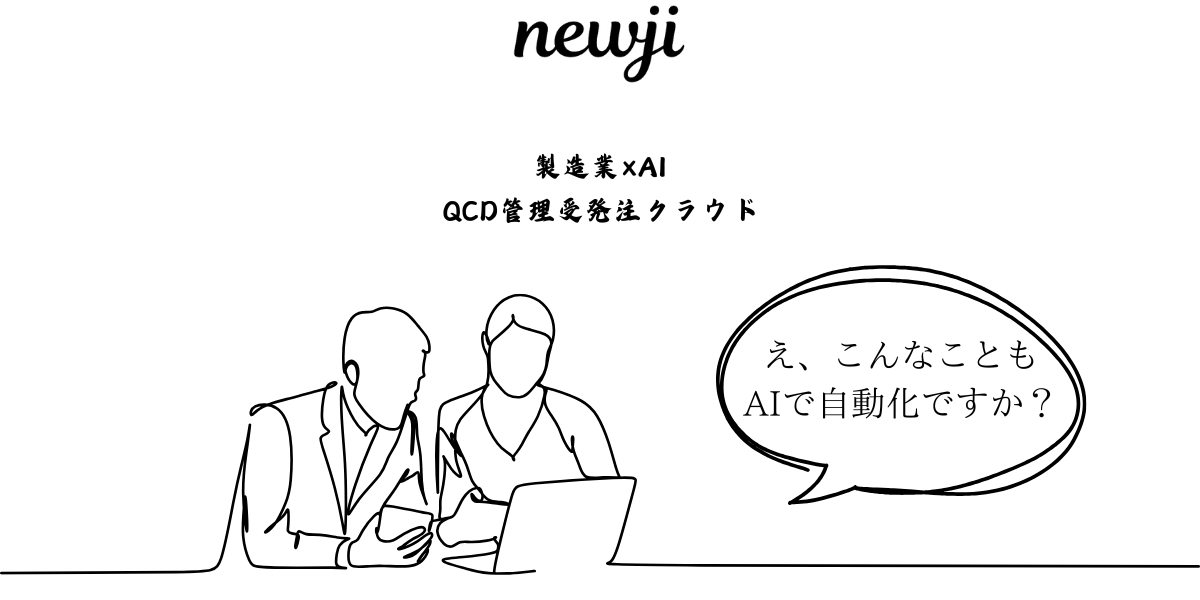
Setting appropriate inventory amounts of raw materials for manufacturing to improve production efficiency
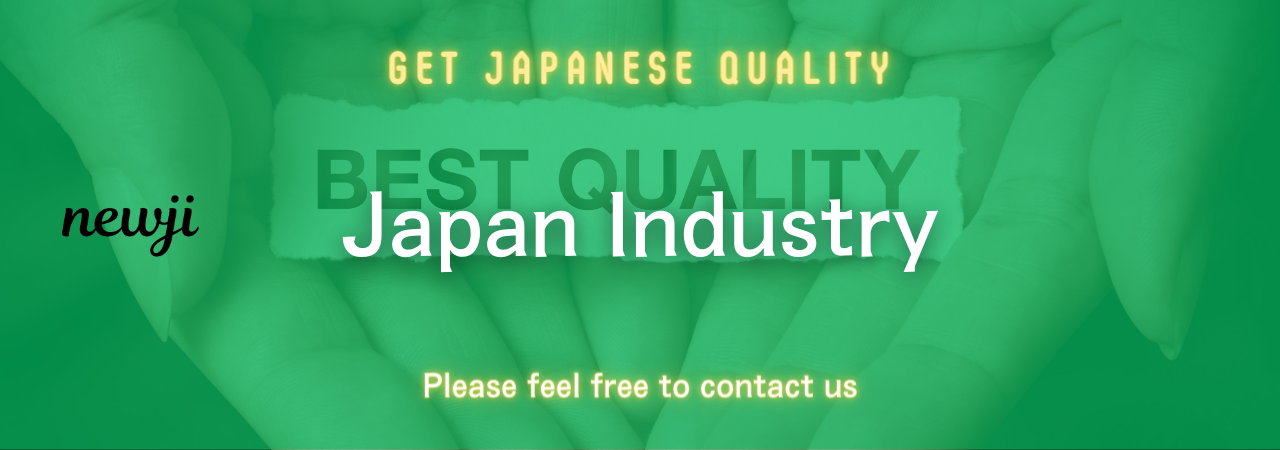
目次
Understanding Raw Material Inventory
Managing raw material inventory is a critical component of any manufacturing process.
It involves determining the appropriate amount of materials needed to meet production demands.
This process requires careful planning and a deep understanding of the production cycle.
By maintaining the right balance of inventory, manufacturers can avoid potential pitfalls such as production delays and increased costs.
Understanding raw material inventory starts with analyzing the types of materials used in production, their supplier lead times, and the production schedule.
The Importance of Accurate Inventory Management
Having the right amount of inventory on hand can significantly impact a manufacturer’s production efficiency.
If the inventory is too low, a company might face production halts, leading to unmet deadlines and dissatisfied customers.
Conversely, excessive inventory can tie up valuable resources, increasing storage costs and the risk of material obsolescence.
Accurate inventory management ensures that the manufacturing process runs smoothly without interruptions, while also minimizing costs associated with excess inventory.
Factors Influencing Raw Material Inventory Levels
Several factors influence how much raw material should be kept in inventory.
The primary factors include production rates, supplier lead times, and forecasted demand.
Production Rates
Production rates refer to the speed at which products are manufactured.
A company with a high production rate will require a larger inventory on hand to meet its needs.
Conversely, a company with a slower production rate may be able to maintain a lower inventory level.
Understanding your production rates helps determine the optimal amount of raw materials needed at any given time.
Supplier Lead Times
Supplier lead times are the time intervals required for suppliers to deliver materials after an order is placed.
Longer lead times might necessitate holding more inventory to avoid running out of materials.
Manufacturers should cultivate good relationships with their suppliers to ensure timely deliveries and potentially reduce lead times.
Forecasted Demand
Forecasted demand predicts the amount of product that will be needed in the future.
It is essential for adjusting inventory levels accordingly.
Accurate demand forecasting reduces the risk of stockouts or excessive inventory.
Advanced forecasting methods, such as using historical data and market analysis, can provide more precise demand estimates.
Strategies for Optimizing Inventory
To improve production efficiency, manufacturers should employ strategies for optimizing raw material inventory.
Just-In-Time (JIT) Inventory
The Just-In-Time inventory approach seeks to reduce waste by receiving goods only as they are needed in the production process.
This method decreases inventory holding costs but requires precise demand forecasting and reliable suppliers.
JIT can enhance production efficiency by minimizing the resources tied up in inventory.
Economic Order Quantity (EOQ)
EOQ is a formula used to determine the optimal order quantity that minimizes total inventory costs.
This approach takes into account ordering costs, carrying costs, and demand rate.
By using EOQ, manufacturers can calculate the most cost-effective order size, helping maintain an ideal balance of inventory.
Automated Inventory Systems
Implementing automated inventory systems can provide real-time data on stock levels, lead times, and demand fluctuations.
These systems can trigger automatic reorders and prevent shortages, ensuring a seamless production process.
Automation minimizes human error and increases the accuracy of inventory management.
Benefits of Optimized Inventory Levels
Setting the appropriate inventory levels offers several benefits to manufacturers, enhancing overall production efficiency.
Improved Cash Flow
Maintaining optimal inventory levels frees up capital that would otherwise be tied up in excess stock.
This improved cash flow allows businesses to invest in other critical areas like innovation and expansion.
Enhanced Production Planning
Optimized inventory provides the predictability needed for effective production planning.
With the right materials available, manufacturers can schedule production runs without interruptions, leading to higher productivity.
Increased Customer Satisfaction
By avoiding delays and ensuring timely delivery of finished products, businesses can meet customer expectations more consistently.
Satisfied customers are more likely to return for repeat purchases and recommend the company to others.
Challenges in Inventory Management
Despite the clear benefits, managing raw material inventory comes with its set of challenges.
Fluctuating Demand
Unexpected changes in demand can make accurate forecasting difficult.
Manufacturers need to remain flexible and responsive to market changes to avoid inventory imbalances.
Supply Chain Disruptions
Supplier issues, such as delayed shipments or quality problems, can lead to disruptions in the production schedule.
Building a diverse supplier base and having contingency plans can mitigate these risks.
Technological Integration
Implementing and integrating new technologies for inventory management can be costly and time-consuming.
However, the long-term benefits often justify the initial investment.
Conclusion
Setting the appropriate inventory levels for raw materials is crucial for enhancing manufacturing efficiency.
By understanding the factors that influence inventory needs and implementing strategies like JIT, EOQ, and automated systems, manufacturers can achieve better cost management and production planning.
Though challenges exist, overcoming them with flexibility and innovation can lead to substantial improvements in both operational efficiency and customer satisfaction.
資料ダウンロード
QCD調達購買管理クラウド「newji」は、調達購買部門で必要なQCD管理全てを備えた、現場特化型兼クラウド型の今世紀最高の購買管理システムとなります。
ユーザー登録
調達購買業務の効率化だけでなく、システムを導入することで、コスト削減や製品・資材のステータス可視化のほか、属人化していた購買情報の共有化による内部不正防止や統制にも役立ちます。
NEWJI DX
製造業に特化したデジタルトランスフォーメーション(DX)の実現を目指す請負開発型のコンサルティングサービスです。AI、iPaaS、および先端の技術を駆使して、製造プロセスの効率化、業務効率化、チームワーク強化、コスト削減、品質向上を実現します。このサービスは、製造業の課題を深く理解し、それに対する最適なデジタルソリューションを提供することで、企業が持続的な成長とイノベーションを達成できるようサポートします。
オンライン講座
製造業、主に購買・調達部門にお勤めの方々に向けた情報を配信しております。
新任の方やベテランの方、管理職を対象とした幅広いコンテンツをご用意しております。
お問い合わせ
コストダウンが利益に直結する術だと理解していても、なかなか前に進めることができない状況。そんな時は、newjiのコストダウン自動化機能で大きく利益貢献しよう!
(Β版非公開)