- お役立ち記事
- Sharing Digital Twins with Suppliers: Collaboration and Simulation in a Virtual Environment
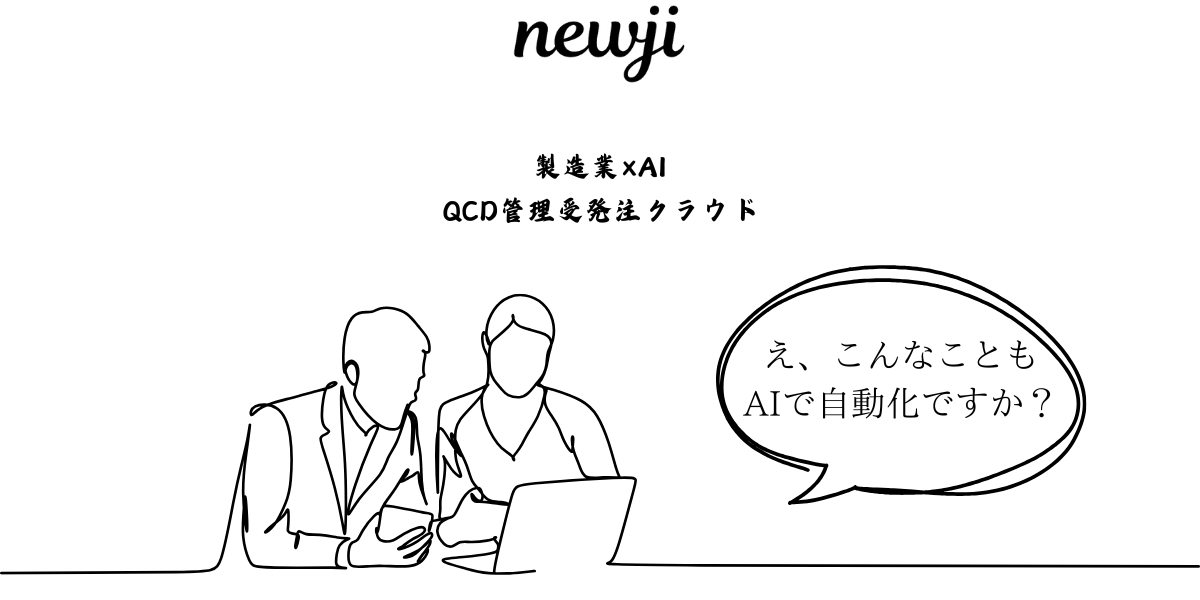
Sharing Digital Twins with Suppliers: Collaboration and Simulation in a Virtual Environment
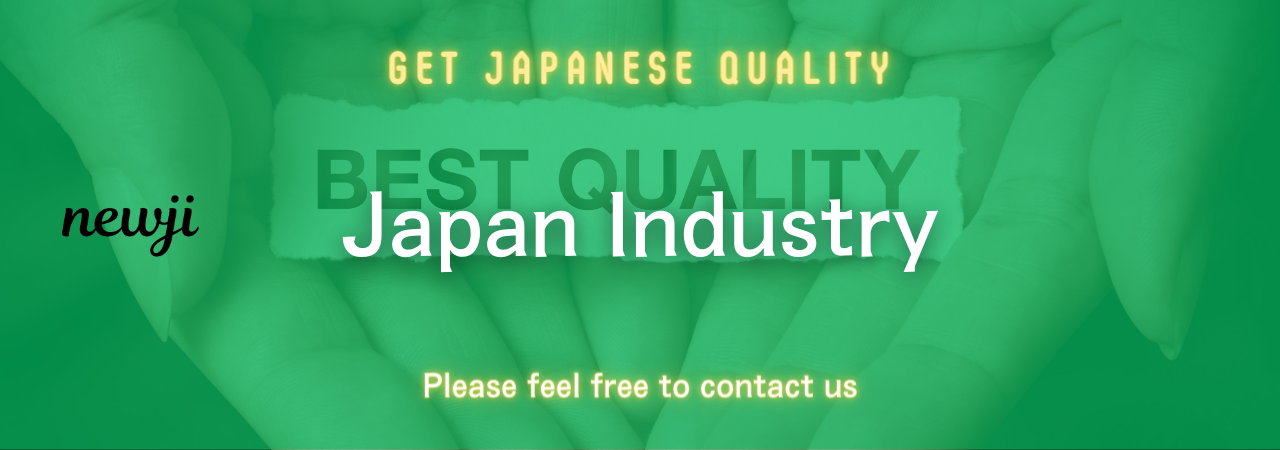
In today’s fast-paced technological world, successful business operations often hinge on efficient collaboration and precise simulations.
Sharing digital twins with suppliers can be a game-changing approach to achieve this.
Digital twins essentially provide a virtual representation of physical products, enabling real-time monitoring and simulation.
This article delves into the myriad benefits and practical applications of sharing digital twins with suppliers.
目次
What Are Digital Twins?
Digital twins are virtual replicas of physical entities, processes, or systems.
They integrate real-time data to mirror their real-world counterparts accurately.
Using sensors and IoT devices, digital twins collect and transmit data to offer a comprehensive insight into the operational dynamics of an asset.
The concept is akin to having a living digital model that evolves alongside the physical object, improving accuracy, and predictive capabilities.
Why Share Digital Twins with Suppliers?
Synchronized Collaboration
Sharing digital twins with suppliers fosters synchronized collaboration.
Both parties access the same up-to-date information, ensuring everyone is aligned.
This shared knowledge base facilitates more informed decision-making and reduces the likelihood of miscommunication or oversight.
Enhanced Development Cycles
In product development, sharing digital twins accelerates the design, testing, and improvement phases.
Suppliers can access the virtual models to identify potential issues, suggest enhancements, and adapt their processes accordingly.
This real-time feedback loop drastically cuts down development times and improves overall product quality.
Cost Efficiency
By identifying potential problems early, digital twins can save significant costs.
Suppliers can run various simulations and predictive analyses, preempting issues that might arise during production or logistics.
This proactive approach minimizes costly disruptions and inefficiencies, translating to more financial savings for both manufacturers and suppliers.
Improved Supply Chain Transparency
Suppliers gain comprehensive insights into the entire supply chain network through digital twins, fostering greater transparency.
They can track inventory levels, forecast demand more accurately, and optimize their production schedules to meet deadlines.
This transparency enhances trust and accountability within the supply chain, improving overall efficiency.
Implementing Digital Twins in Supplier Collaboration
Choose the Right Technology
The first step in implementing digital twins is selecting the right technology.
Consider platforms compatible with existing systems and offering scalability.
Integrating IoT devices, AI insights, and machine learning capabilities is essential for generating accurate and actionable data.
Data Integration and Management
Effective data integration is pivotal for harnessing the full potential of digital twins.
Ensure seamless data flow between manufacturers and suppliers.
Utilize secure cloud-based solutions to safeguard sensitive information and enable real-time data access.
Foster Open Communication
Establishing clear communication channels is crucial for successful collaboration.
Foster a culture of openness and transparency, where both manufacturers and suppliers can freely share insights and feedback.
Regular virtual meetings and workshops can enhance understanding and cohesion among all stakeholders.
Training and Support
Training is vital for the smooth adoption of digital twin technology.
Ensure all parties understand how to use the tools effectively.
Offer continuous support and updates to keep everyone abreast of the latest advancements and best practices.
Case Studies: Success Stories of Sharing Digital Twins
Automotive Industry
A leading automotive manufacturer implemented digital twin technology and shared it with its suppliers.
The results were impressive, with a significant reduction in development times and costs.
Suppliers could simulate component performance under different conditions, enabling better quality control and innovation.
Healthcare Sector
In the healthcare sector, digital twins have revolutionized the supply chain for medical devices.
Manufacturers collaborate closely with suppliers to ensure precision and reliability.
Through virtual simulations, they identify potential faults early, ensuring that the final products meet stringent safety standards.
Aerospace Industry
A major aerospace company utilized digital twins to streamline its production and supply chain processes.
Suppliers gained real-time insights into part performance and reliability, aiding in the timely identification of inefficiencies.
This collaboration led to improved product quality and timely deliveries, enhancing customer satisfaction.
Future Prospects of Digital Twins in Supply Chain Management
The future of digital twins in supply chain management looks promising.
As technology advances, the integration of augmented reality (AR) and virtual reality (VR) will further enhance virtual simulations and interactions.
Blockchain technology may provide even more secure data sharing, increasing trust between manufacturers and suppliers.
AI and machine learning will offer deeper predictive insights, preempting potential issues with even greater accuracy.
Ultimately, the adoption of digital twin technology will drive innovation, agility, and resilience in supply chain management.
Sharing digital twins with suppliers proves invaluable for effective collaboration and precise simulations.
By embracing this innovative approach, businesses can reduce costs, enhance product quality, and achieve greater transparency in their supply chain operations.
As technology continues to evolve, the potential for digital twins promises to revolutionize the way we collaborate and innovate.
資料ダウンロード
QCD調達購買管理クラウド「newji」は、調達購買部門で必要なQCD管理全てを備えた、現場特化型兼クラウド型の今世紀最高の購買管理システムとなります。
ユーザー登録
調達購買業務の効率化だけでなく、システムを導入することで、コスト削減や製品・資材のステータス可視化のほか、属人化していた購買情報の共有化による内部不正防止や統制にも役立ちます。
NEWJI DX
製造業に特化したデジタルトランスフォーメーション(DX)の実現を目指す請負開発型のコンサルティングサービスです。AI、iPaaS、および先端の技術を駆使して、製造プロセスの効率化、業務効率化、チームワーク強化、コスト削減、品質向上を実現します。このサービスは、製造業の課題を深く理解し、それに対する最適なデジタルソリューションを提供することで、企業が持続的な成長とイノベーションを達成できるようサポートします。
オンライン講座
製造業、主に購買・調達部門にお勤めの方々に向けた情報を配信しております。
新任の方やベテランの方、管理職を対象とした幅広いコンテンツをご用意しております。
お問い合わせ
コストダウンが利益に直結する術だと理解していても、なかなか前に進めることができない状況。そんな時は、newjiのコストダウン自動化機能で大きく利益貢献しよう!
(Β版非公開)