- お役立ち記事
- Sharing Digital Twins with Suppliers: Virtual Collaboration and Simulation
Sharing Digital Twins with Suppliers: Virtual Collaboration and Simulation
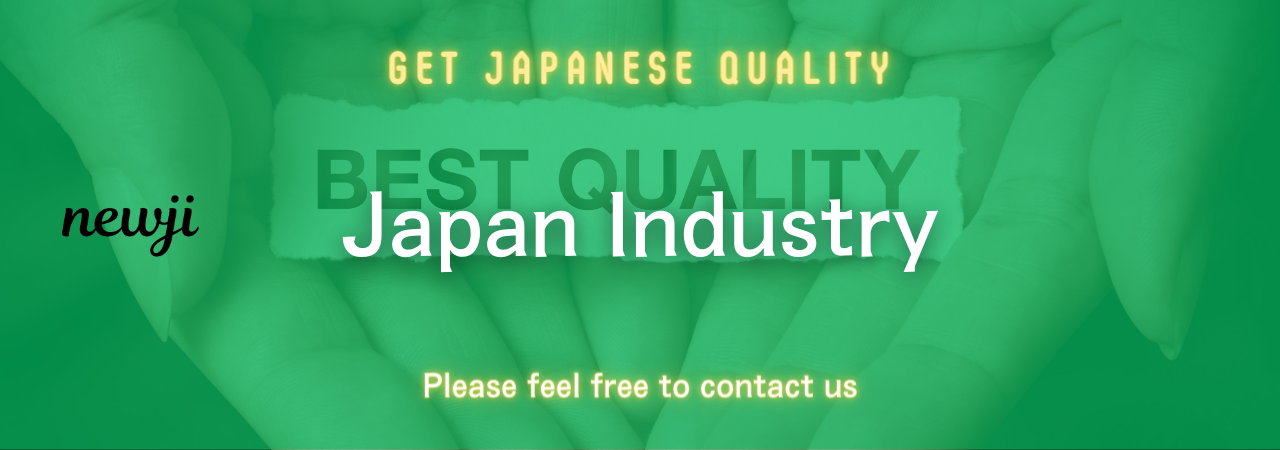
In today’s fast-paced industrial environment, companies are constantly looking for ways to streamline operations and enhance collaboration with suppliers.
One of the emerging technologies playing a pivotal role in this transformation is digital twins.
Digital twins are virtual replicas of physical assets, systems, or processes.
Through advanced simulation and data analytics, digital twins allow businesses to optimize and monitor their operations in real-time.
Sharing digital twins with suppliers is revolutionizing how companies collaborate, fostering a new era of virtual teamwork and simulation.
目次
What are Digital Twins?
A digital twin is a comprehensive digital duplicate of a physical entity.
This could range from machinery to entire production systems.
The digital twin integrates data from sensors, Internet of Things (IoT) devices, and other sources to model real-world conditions accurately.
Through this virtual representation, companies can perform advanced simulations, predict outcomes, and diagnose issues before they occur.
The concept hinges on collecting massive amounts of real-time data.
Once this data is analyzed, it is used to create an exact digital counterpart.
This counterpart not only mirrors the current state of its physical version but also evolves over time as new data comes in.
The results are more informed decision-making, increased operational efficiency, and reduced downtime.
Enhancing Supplier Collaboration
By sharing digital twins with suppliers, companies can significantly improve their supply chain dynamics.
Suppliers gain unprecedented visibility into the production process, enabling them to align their operations more closely with the company’s needs.
Better Communication and Transparency
In conventional settings, suppliers often have to rely on periodic updates or fragmented data to understand their client’s requirements.
With access to digital twins, suppliers can see real-time data and monitor the state of the production equipment.
This transparency ensures they are always aware of any potential issues or changes in demand.
Enhanced communication ensures both parties are on the same page, reducing the chances of misunderstandings and delays.
Optimized Production Scheduling
When suppliers have access to a company’s digital twin, they can better schedule their own production runs.
Instead of guessing and working with outdated information, suppliers can forecast the need for raw materials and other supplies with higher precision.
This proactive approach means less time wasted on waiting for resources and more efficient production cycles.
Consequently, it leads to better resource management and reduces the likelihood of overproduction or stockouts.
Proactive Maintenance and Issue Resolution
One of the significant advantages of digital twins is predictive maintenance.
By analyzing real-time data and identifying patterns, it is possible to predict when a machine is likely to fail.
With suppliers understanding these predictions, they can plan timely maintenance or supply necessary parts even before an issue arises.
Addressing potential problems before they escalate prevents costly downtimes and improves overall production efficiency.
Advanced Simulation Capabilities
Digital twins offer robust simulation capabilities, which can be an invaluable asset when shared with suppliers.
Testing New Methods and Materials
Suppliers can use digital twins to simulate and test new manufacturing methods or materials without risking disruptions in actual production lines.
This virtual testing environment allows for experimentation and optimization without the associated risks of real-world trials.
Assessing the feasibility and performance of new approaches virtually ensures that any changes implemented are well-vetted and likely to succeed.
Improving Design and Innovation
Digital twins facilitate better design processes by allowing iterations and modifications in a virtual realm.
Suppliers collaborating on design projects can use digital twins to visualize how a new product component will interact with existing systems.
This leads to more innovative solutions and shorter design cycles.
Accelerated innovation fosters a competitive edge and can result in more market-ready products in a shorter timeframe.
Implementing Digital Twin Technology
While the benefits of digital twins are impressive, their successful implementation involves a few critical steps.
Choosing the Right Tools and Platforms
A variety of software platforms are available for creating and managing digital twins.
When selecting a tool, consider the specific needs of your industry and the compatibility with existing systems.
Ensure the platform integrates seamlessly with IoT devices, data analytic tools, and other technological infrastructure in place.
Data Management and Security
The effectiveness of digital twins largely depends on the quality and timeliness of the data they utilize.
Establishing robust data management practices is crucial.
This includes ensuring data accuracy, completeness, and timeliness.
Equally important is securing this data.
Since digital twins handle sensitive and proprietary information, implementing strong cybersecurity measures is essential to protect against data breaches and unauthorized access.
Training and Change Management
Introducing any new technology requires adequate staff training.
Ensuring that both your internal team and suppliers are proficient in using digital twin technology enhances its effectiveness.
Alongside training, change management strategies are necessary to ease the transition.
Clear communication about the benefits and step-by-step guidance can mitigate resistance and promote smoother adoption.
Future Prospects of Digital Twins in Supplier Collaboration
As digital twin technology continues to evolve, its applications in supplier collaboration are expected to grow.
Advancements in artificial intelligence and machine learning will further enhance predictive capabilities, making digital twins even more powerful in preempting issues and optimizing performance.
The future may see even more seamless integration between company operations and supplier activities, with digital twins serving as a central hub for real-time collaboration and decision-making.
In conclusion, sharing digital twins with suppliers paves the way for more effective virtual collaboration and robust simulation capabilities.
From enhancing communication and transparency to enabling predictive maintenance and driving innovation, digital twins are a game-changer for industrial operations.
By embracing this technology, companies and their suppliers can achieve new levels of efficiency, agility, and competitiveness in a rapidly evolving marketplace.
資料ダウンロード
QCD調達購買管理クラウド「newji」は、調達購買部門で必要なQCD管理全てを備えた、現場特化型兼クラウド型の今世紀最高の購買管理システムとなります。
ユーザー登録
調達購買業務の効率化だけでなく、システムを導入することで、コスト削減や製品・資材のステータス可視化のほか、属人化していた購買情報の共有化による内部不正防止や統制にも役立ちます。
NEWJI DX
製造業に特化したデジタルトランスフォーメーション(DX)の実現を目指す請負開発型のコンサルティングサービスです。AI、iPaaS、および先端の技術を駆使して、製造プロセスの効率化、業務効率化、チームワーク強化、コスト削減、品質向上を実現します。このサービスは、製造業の課題を深く理解し、それに対する最適なデジタルソリューションを提供することで、企業が持続的な成長とイノベーションを達成できるようサポートします。
オンライン講座
製造業、主に購買・調達部門にお勤めの方々に向けた情報を配信しております。
新任の方やベテランの方、管理職を対象とした幅広いコンテンツをご用意しております。
お問い合わせ
コストダウンが利益に直結する術だと理解していても、なかなか前に進めることができない状況。そんな時は、newjiのコストダウン自動化機能で大きく利益貢献しよう!
(Β版非公開)