- お役立ち記事
- Shot Size Management Methods and Success Stories SMEs Should Know
月間76,176名の
製造業ご担当者様が閲覧しています*
*2025年3月31日現在のGoogle Analyticsのデータより
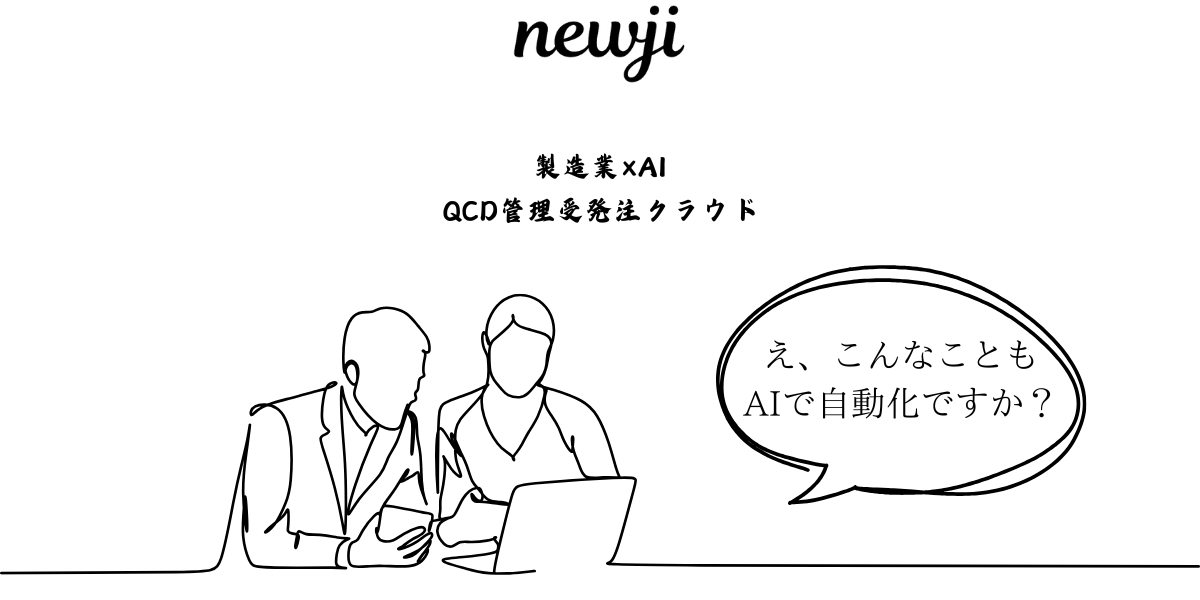
Shot Size Management Methods and Success Stories SMEs Should Know
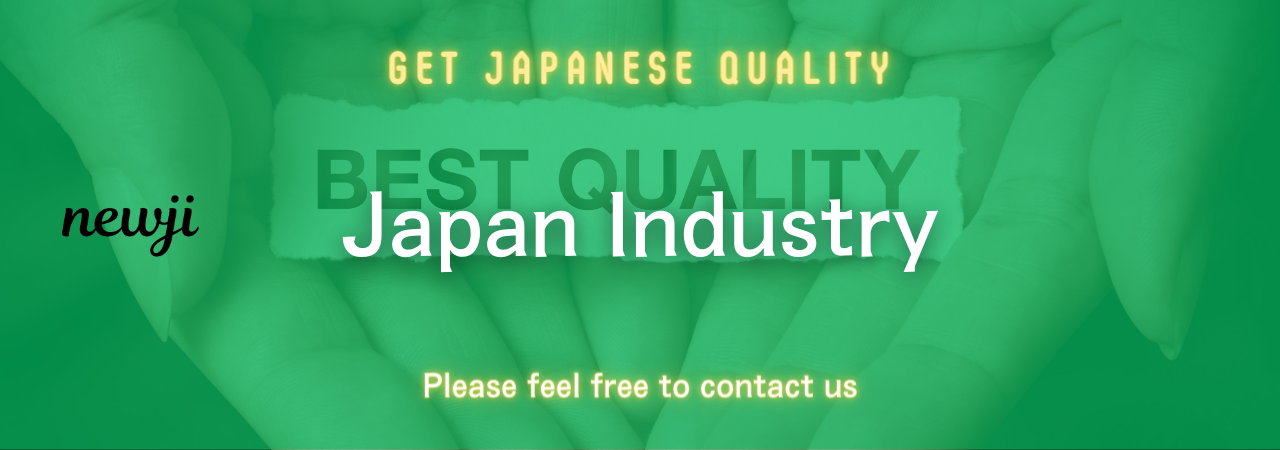
目次
Understanding Shot Size Management
Shot size management is an integral aspect of manufacturing and production, particularly in industries dealing with molding processes like plastic injection molding.
The term ‘shot size’ refers to the volume of material injected into a mold during a single cycle.
Managing this aspect effectively can contribute significantly to product quality, resource efficiency, and cost-effectiveness.
For small and medium-sized enterprises (SMEs), mastering shot size management can be a game-changer in enhancing productivity and sustainability.
The Importance of Shot Size Management
Effective shot size management can reduce material wastage significantly.
When the right amount of material is injected, problems such as overflows or defects are minimized, leading to better-quality products.
This is crucial for SMEs, where resources may be limited, and minimizing waste directly translates to cost savings.
Additionally, proper shot size management can extend the lifespan of machinery.
Over-injection can exert unnecessary pressure on molds and machines, leading to wear and tear.
By injecting just enough material, SMEs can maintain their equipment better, reducing downtime and repair costs.
Key Strategies for Effective Shot Size Management
Accurate Calibration
For accurate shot size management, precision is key.
Regularly calibrating your machinery ensures that the shot size remains consistent across production cycles.
This involves checking the injection pressure and adjusting it to accommodate changes in material and production requirements.
Calibration should be part of routine machine maintenance to avoid discrepancies that can affect product quality and increase wastage.
Employee Training
Ensuring that your team is well-versed in shot size management techniques is vital.
Employees should understand the machinery settings, various materials, and their properties.
Training programs can enhance their capability to adjust shot sizes correctly, diagnose issues, and implement corrective measures promptly.
A skilled workforce can recognize patterns that indicate potential problems and take preventive actions, allowing for smoother operations.
Utilize Technology and Automation
Adopting technology can streamline shot size management for SMEs.
Automated systems can provide real-time data about current operations, identifying inefficiencies and deviations in shot sizes.
Advanced software solutions can predict the optimal shot size based on historical and current data, ensuring precision.
Automation not only minimizes human error but also frees up staff to focus on more strategic tasks, improving overall productivity.
Success Stories in Shot Size Management
Several SMEs have implemented successful shot size management strategies, resulting in improved efficiency and product quality.
Case Study: Precision Plastics, Inc.
Precision Plastics, a small manufacturing enterprise, faced challenges with inconsistencies in product quality.
Through diligent calibration and employee training, they managed to standardize their production process.
The company also invested in an automated system that monitored injection cycles, leading to a 20% reduction in material waste.
This initiative not only cut down costs significantly but also enhanced their reputation for producing high-quality products.
Case Study: Green Molds Co.
Green Molds Co., an SME specializing in eco-friendly products, aimed to reduce their environmental footprint.
They adopted a comprehensive shot size management strategy that included material selection, advanced calibration techniques, and leveraging automation.
Through these efforts, they achieved a remarkable 30% decrease in energy consumption and reduced their scrap rate by 25%.
The improvements allowed them to reinvest savings into new technologies that further boosted their green initiatives.
Conclusion
Shot size management is a critical component for SMEs looking to optimize their manufacturing processes.
By focusing on accurate calibration, employee training, and embracing technology, businesses can achieve lower waste levels, better product quality, and enhanced cost-effectiveness.
Drawing from the success stories of companies like Precision Plastics and Green Molds Co., SMEs can find inspiration and practical approaches to improve their processes.
As industries continue to evolve, those who pay close attention to the details of shot size management will stand out for their efficiency, innovation, and sustainability.
資料ダウンロード
QCD管理受発注クラウド「newji」は、受発注部門で必要なQCD管理全てを備えた、現場特化型兼クラウド型の今世紀最高の受発注管理システムとなります。
ユーザー登録
受発注業務の効率化だけでなく、システムを導入することで、コスト削減や製品・資材のステータス可視化のほか、属人化していた受発注情報の共有化による内部不正防止や統制にも役立ちます。
NEWJI DX
製造業に特化したデジタルトランスフォーメーション(DX)の実現を目指す請負開発型のコンサルティングサービスです。AI、iPaaS、および先端の技術を駆使して、製造プロセスの効率化、業務効率化、チームワーク強化、コスト削減、品質向上を実現します。このサービスは、製造業の課題を深く理解し、それに対する最適なデジタルソリューションを提供することで、企業が持続的な成長とイノベーションを達成できるようサポートします。
製造業ニュース解説
製造業、主に購買・調達部門にお勤めの方々に向けた情報を配信しております。
新任の方やベテランの方、管理職を対象とした幅広いコンテンツをご用意しております。
お問い合わせ
コストダウンが利益に直結する術だと理解していても、なかなか前に進めることができない状況。そんな時は、newjiのコストダウン自動化機能で大きく利益貢献しよう!
(β版非公開)