- お役立ち記事
- Significance and Practice of SPC: Statistical Methods for Product Quality Control and Process Improvement
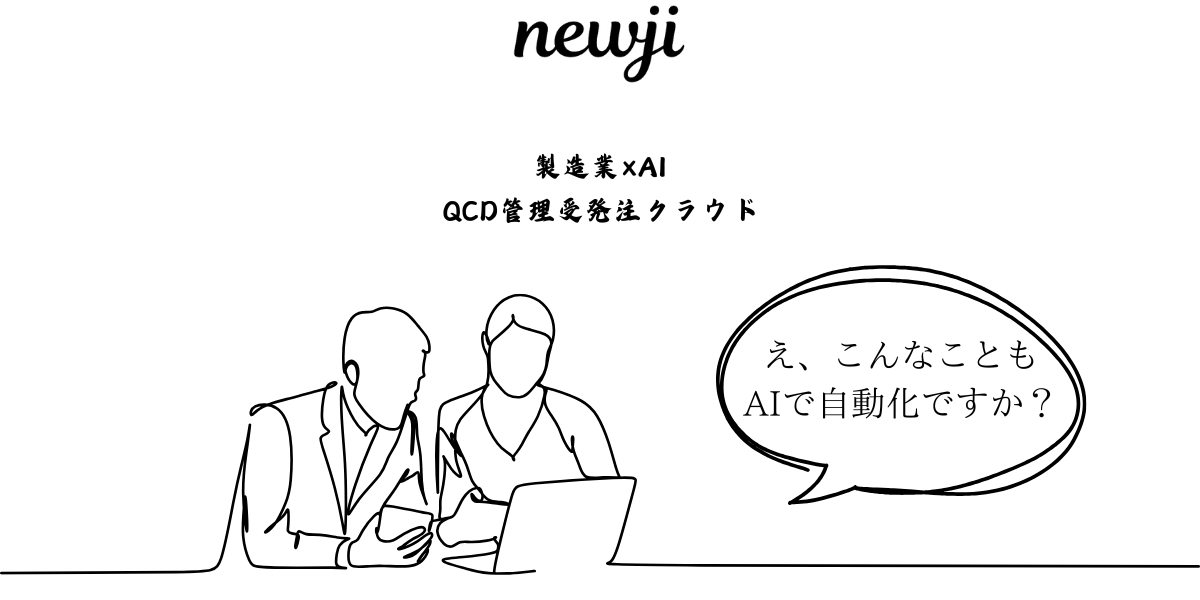
Significance and Practice of SPC: Statistical Methods for Product Quality Control and Process Improvement
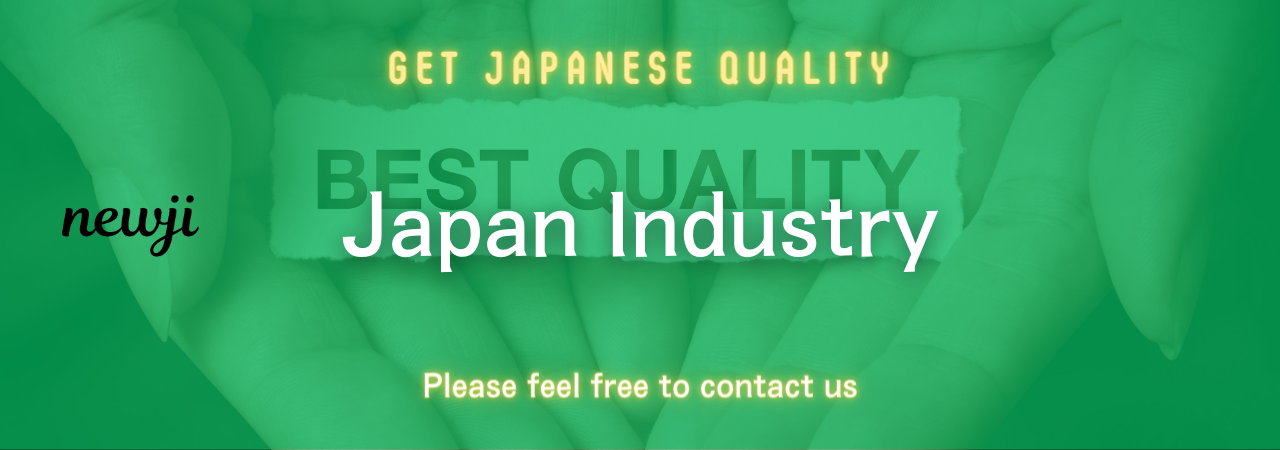
目次
Understanding SPC: Statistical Process Control
Statistical Process Control, commonly referred to as SPC, is a method used to monitor and control a process to ensure that it operates at its full potential.
At its core, SPC utilizes statistical methods to analyze data, helping organizations maintain consistent product quality and identify any deviations or irregularities in a process.
This technique plays a crucial role in manufacturing environments where maintaining the quality of products is paramount.
Why is SPC Important?
The importance of SPC cannot be overstated when it comes to maintaining and improving product quality.
Employing SPC techniques allows businesses to produce high-quality products consistently.
Here are some key reasons why SPC is significant:
Prevention of Defects
SPC helps in identifying and addressing problems in a process before they result in defects.
By analyzing data collected from different stages of the production process, potential issues can be detected early.
This proactive approach ensures that defects are minimized, reducing waste and costs.
Efficiency Improvement
Using SPC can help streamline processes and eliminate unnecessary steps.
By understanding process variations and their causes, businesses can fine-tune their operations to enhance efficiency.
This often leads to reduced production time and costs, ultimately improving the bottom line.
Consistency in Quality
One of the primary goals of SPC is to achieve and maintain consistency in product quality.
Consistent quality builds trust with customers and enhances brand reputation.
Regular monitoring ensures that the manufacturing process stays within predefined control limits, leading to uniform products.
Essential Components of SPC
For SPC to be effective, there are several key components that need to be in place.
Understanding these elements helps in implementing SPC efficiently.
Control Charts
Control charts are fundamental tools in SPC.
These graphical representations of process data over time show any variations from the normal process.
Control charts typically have a central line representing the average, along with upper and lower control limits.
Any data points outside these limits indicate a potential problem.
Process Capability Analysis
Process capability analysis assesses whether a process can produce products within specified limits consistently.
It involves calculating process capability indices, which provide a measure of how well a process is performing.
If the capability indices are within acceptable ranges, it indicates that the process is capable of meeting quality standards.
Data Collection and Analysis
Accurate data collection is crucial for effective SPC.
The data collected from various stages of the production process must be precise and reliable.
Once collected, statistical techniques are used to analyze the data, identifying patterns, trends, and potential issues.
Implementing SPC in Your Organization
Implementing SPC in an organization involves a series of steps that need to be followed meticulously.
Here is a guide to help you get started:
Define Objectives
The first step is to define the objectives for using SPC.
This includes identifying key areas of the production process that need monitoring and specifying the desired outcomes.
Clear objectives help in focusing efforts and resources on critical areas.
Collect Data
Next, gather data from the processes you wish to monitor.
Ensure that the data collection methods are accurate and consistent.
This initial data serves as a baseline for comparison and helps in establishing control limits.
Create Control Charts
Based on the collected data, create control charts.
These charts will help in visualizing process variations and identifying any deviations from the norm.
Regularly update these charts with new data to maintain an ongoing analysis.
Analyze and Interpret Data
Analyze the data represented in the control charts to identify any trends or patterns.
Interpreting this data correctly is crucial for spotting potential issues.
If any points fall outside the control limits, investigate the causes and take corrective actions.
Implement Corrective Actions
When deviations or irregularities are detected, it’s essential to implement corrective measures promptly.
These actions should address the root causes of the problems to prevent recurrence.
Regularly reviewing and updating these measures helps in refining the process continuously.
Train Employees
For SPC to be effective, employees must be trained in the principles and techniques of SPC.
Ensure that your team understands the importance of data collection, how to read control charts, and the steps to take when deviations occur.
A well-trained workforce is vital for the successful implementation of SPC.
Common Challenges in SPC
While SPC is a powerful tool, its implementation can come with challenges.
Recognizing and addressing these challenges ensures smoother application.
Data Quality Issues
One of the main challenges is ensuring the quality and accuracy of the data collected.
Inconsistent or inaccurate data can lead to incorrect analysis and conclusions.
Investing in reliable data collection methods and regular quality checks helps mitigate this issue.
Resistance to Change
Introducing new processes or methodologies often meets resistance from employees.
There may be reluctance to adopt SPC due to unfamiliarity or perceived complexity.
Addressing this requires effective communication, training, and demonstrating the benefits of SPC.
Maintaining Consistency
Once SPC is implemented, maintaining consistency in monitoring and analysis is critical.
Regular reviews, updates to control charts, and continuous employee training help ensure that SPC remains effective over time.
Conclusion
SPC is an invaluable tool for any organization aiming to enhance product quality and process efficiency.
Through consistent monitoring and analysis, it enables businesses to detect and resolve issues proactively.
While challenges exist, they can be overcome with proper planning, training, and commitment.
Implementing SPC not only leads to improved product quality but also fosters a culture of continuous improvement within the organization.
資料ダウンロード
QCD調達購買管理クラウド「newji」は、調達購買部門で必要なQCD管理全てを備えた、現場特化型兼クラウド型の今世紀最高の購買管理システムとなります。
ユーザー登録
調達購買業務の効率化だけでなく、システムを導入することで、コスト削減や製品・資材のステータス可視化のほか、属人化していた購買情報の共有化による内部不正防止や統制にも役立ちます。
NEWJI DX
製造業に特化したデジタルトランスフォーメーション(DX)の実現を目指す請負開発型のコンサルティングサービスです。AI、iPaaS、および先端の技術を駆使して、製造プロセスの効率化、業務効率化、チームワーク強化、コスト削減、品質向上を実現します。このサービスは、製造業の課題を深く理解し、それに対する最適なデジタルソリューションを提供することで、企業が持続的な成長とイノベーションを達成できるようサポートします。
オンライン講座
製造業、主に購買・調達部門にお勤めの方々に向けた情報を配信しております。
新任の方やベテランの方、管理職を対象とした幅広いコンテンツをご用意しております。
お問い合わせ
コストダウンが利益に直結する術だと理解していても、なかなか前に進めることができない状況。そんな時は、newjiのコストダウン自動化機能で大きく利益貢献しよう!
(Β版非公開)