- お役立ち記事
- Significance of 100% inspection in the manufacturing industry and its implementation procedures
Significance of 100% inspection in the manufacturing industry and its implementation procedures
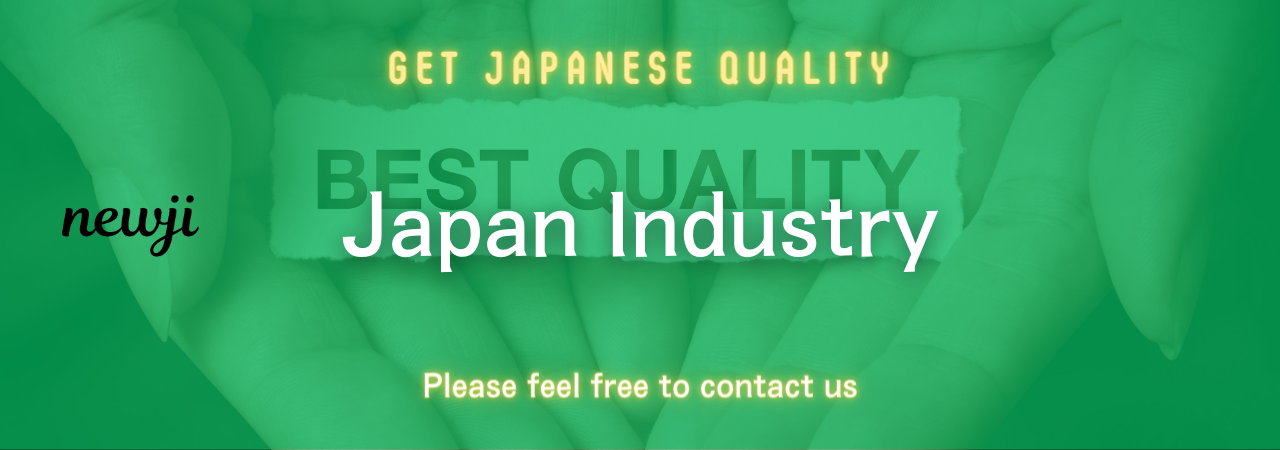
In today’s ever-evolving manufacturing industry, maintaining product quality is paramount.
Customers demand flawless products, and companies strive to meet these expectations to maintain their reputation and competitive edge.
One of the most effective ways to ensure high-quality products is through 100% inspection.
This method involves scrutinizing every single item produced to ensure that each one meets the required standards.
In this article, we will explore the significance of 100% inspection in the manufacturing industry and the procedures for its successful implementation.
目次
Why 100% Inspection is Important
Ensuring Product Quality
Product quality is a critical factor in customer satisfaction and business success.
By examining every unit produced, manufacturers can identify and eliminate defects, ensuring that only top-quality products reach the market.
This not only boosts customer confidence but also minimizes the risk of product recalls and associated costs.
Maintaining Brand Reputation
A brand’s reputation is built on the consistent delivery of high-quality products.
Any defect that reaches the customer can tarnish a brand’s image, leading to loss of trust and potential revenue.
100% inspection helps in preserving and enhancing brand reputation by ensuring that defective products are intercepted before they leave the production line.
Compliance with Standards and Regulations
Many industries are subject to stringent standards and regulations.
Failure to comply can result in hefty fines and other legal ramifications.
Through 100% inspection, companies can ensure that their products meet all necessary standards and regulations, thereby avoiding legal issues and maintaining compliance.
Reducing Waste and Maximizing Resources
Identifying defects early in the production process can help in reducing waste.
When defective products are identified quickly, they can be addressed and corrected without consuming additional resources.
This not only maximizes the efficiency of the production process but also contributes to sustainable manufacturing practices.
Implementing 100% Inspection
Identifying Key Quality Criteria
Before starting the inspection process, it is essential to identify the key quality criteria that the products must meet.
These criteria should be based on customer requirements, industry standards, and regulatory guidelines.
Clearly defining these criteria ensures that the inspection process is focused and effective.
Choosing the Right Inspection Tools
The selection of appropriate inspection tools is crucial for the success of 100% inspection.
Depending on the nature of the product, different tools may be required.
For instance, visual inspection tools, electronic gauges, and automated systems can be employed to detect defects accurately.
Investing in advanced inspection technology can enhance the precision and efficiency of the inspection process.
Training the Inspection Team
A well-trained inspection team is vital for the successful implementation of 100% inspection.
Employees should be provided with comprehensive training on the use of inspection tools, identification of defects, and proper documentation of findings.
Regular training sessions can help in keeping the team updated with the latest inspection techniques and industry best practices.
Integrating Inspection into the Production Line
For 100% inspection to be effective, it must be seamlessly integrated into the production line.
This involves designing the production process in a way that allows for continuous inspection without causing delays.
Automated inspection systems can be particularly useful in achieving this integration, as they can inspect products in real-time while the production line is running.
Documenting and Analyzing Inspection Data
Proper documentation of inspection data is essential for tracking product quality and identifying recurring issues.
By analyzing this data, manufacturers can pinpoint areas of improvement and take corrective actions.
Implementing a robust data management system can assist in efficiently storing, retrieving, and analyzing inspection data.
Continuous Improvement
The goal of 100% inspection is not just to detect defects but also to foster continuous improvement.
Regularly reviewing inspection results and feedback from the inspection team can provide valuable insights into the production process.
By addressing the root causes of defects and making necessary adjustments, manufacturers can enhance the overall quality and efficiency of their operations.
Challenges in Implementing 100% Inspection
High Costs
One of the primary challenges of 100% inspection is the associated cost.
Investing in advanced inspection tools and technology can be expensive.
Moreover, the need for continuous inspection may require additional manpower and resources.
However, considering the long-term benefits, such as reduced recalls and improved product quality, the investment can be justified.
Time-Consuming Process
Inspecting every single product can be time-consuming, potentially slowing down the production process.
This is particularly challenging for industries with high production volumes.
To mitigate this, integrating automated inspection systems can help in speeding up the process while maintaining accuracy.
Potential for Human Error
In manual inspection processes, there is always a risk of human error.
Inspectors may overlook defects or inconsistently apply quality criteria.
Implementing regular training, employing automated systems, and double-checking critical points are effective strategies to minimize human error.
Conclusion
In the manufacturing industry, 100% inspection plays a vital role in ensuring product quality, maintaining brand reputation, and complying with standards and regulations.
Despite the challenges, the benefits of implementing this rigorous inspection method are substantial.
By identifying key quality criteria, choosing the right tools, training the inspection team, integrating inspection into the production line, documenting and analyzing data, and fostering continuous improvement, manufacturers can effectively implement 100% inspection.
Ultimately, this leads to the production of high-quality products that meet customer expectations and drive business success.
資料ダウンロード
QCD調達購買管理クラウド「newji」は、調達購買部門で必要なQCD管理全てを備えた、現場特化型兼クラウド型の今世紀最高の購買管理システムとなります。
ユーザー登録
調達購買業務の効率化だけでなく、システムを導入することで、コスト削減や製品・資材のステータス可視化のほか、属人化していた購買情報の共有化による内部不正防止や統制にも役立ちます。
NEWJI DX
製造業に特化したデジタルトランスフォーメーション(DX)の実現を目指す請負開発型のコンサルティングサービスです。AI、iPaaS、および先端の技術を駆使して、製造プロセスの効率化、業務効率化、チームワーク強化、コスト削減、品質向上を実現します。このサービスは、製造業の課題を深く理解し、それに対する最適なデジタルソリューションを提供することで、企業が持続的な成長とイノベーションを達成できるようサポートします。
オンライン講座
製造業、主に購買・調達部門にお勤めの方々に向けた情報を配信しております。
新任の方やベテランの方、管理職を対象とした幅広いコンテンツをご用意しております。
お問い合わせ
コストダウンが利益に直結する術だと理解していても、なかなか前に進めることができない状況。そんな時は、newjiのコストダウン自動化機能で大きく利益貢献しよう!
(Β版非公開)