- お役立ち記事
- Significant Cost Reduction Effects SMEs Can Achieve Through Procurement Optimization
月間77,185名の
製造業ご担当者様が閲覧しています*
*2025年2月28日現在のGoogle Analyticsのデータより
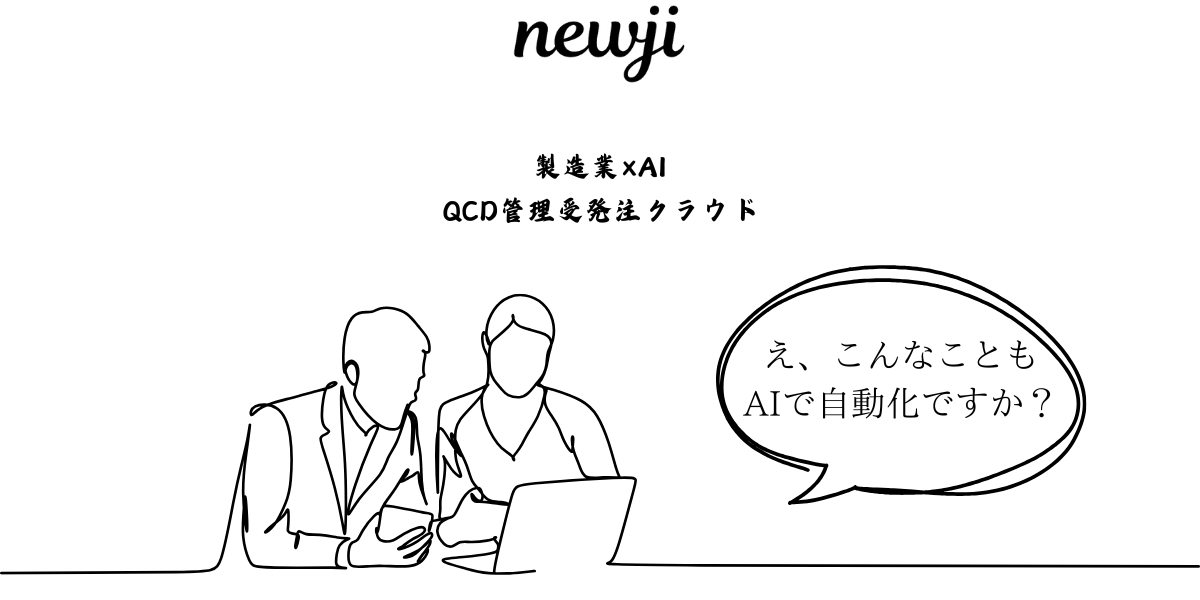
Significant Cost Reduction Effects SMEs Can Achieve Through Procurement Optimization
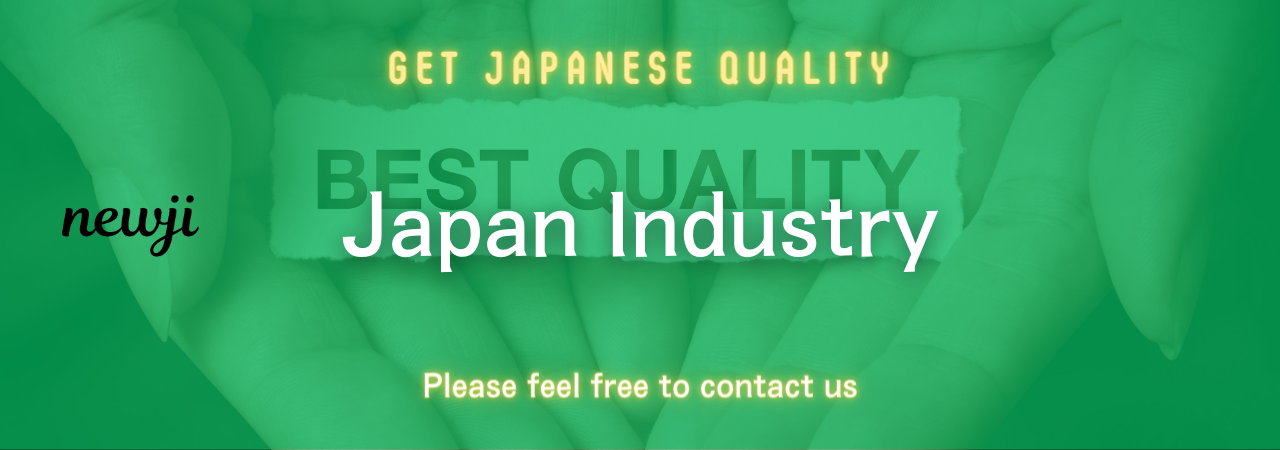
目次
Why Procurement Optimization is Important for SMEs
Small and medium-sized enterprises (SMEs) are the backbone of many economies.
However, they often operate on tight budgets.
As a result, finding ways to reduce costs without sacrificing quality becomes crucial.
One effective way to achieve this is through procurement optimization.
By streamlining the procurement process, SMEs can reduce expenses significantly.
Procurement optimization involves improving the way goods and services are acquired.
This can lead to better prices, faster delivery times, and fewer errors.
Let’s explore the significant cost reduction effects that SMEs can achieve through this approach.
Identifying Areas for Improvement
To optimize procurement, it’s essential first to identify areas where improvements can be made.
Start by analyzing your current procurement process.
Look for inefficiencies that may be causing unnecessary expenses.
Common issues include:
– Over-ordering or under-ordering of supplies.
– Paying higher prices due to lack of negotiation.
– Delays caused by poor supplier relationships.
– Inaccurate inventory management.
Once you’ve identified the problem areas, you can begin to set goals for improvement.
This could include reducing costs, improving supplier relationships, and increasing efficiency.
Using Data for Better Decision-Making
One of the most effective ways to optimize procurement is by utilizing data analytics.
Data can provide valuable insights into your procurement process.
It helps you understand spending patterns, identify trends, and forecast future needs.
For example, data can reveal which suppliers consistently offer the best prices.
It can also show which products are over-ordered, leading to excess inventory costs.
By making data-driven decisions, SMEs can significantly reduce procurement costs.
Leveraging Technology for Procurement
Technology plays a crucial role in procurement optimization.
There are various tools and platforms available that can help streamline the procurement process.
These tools can automate many of the manual tasks involved, saving time and reducing errors.
For instance, e-procurement platforms allow SMEs to manage purchasing electronically.
This can include everything from supplier selection to order placement and invoicing.
Automation can ensure orders are placed on time and with the correct quantities, reducing the risk of over or under-ordering.
Building Strong Supplier Relationships
Another critical aspect of procurement optimization is building strong relationships with suppliers.
By working closely with suppliers, SMEs can negotiate better prices and terms.
It also allows for more efficient communication and faster resolution of issues.
Negotiating Better Terms
Negotiation is an essential skill in procurement.
SMEs should not hesitate to negotiate with suppliers to get the best possible deals.
This can include asking for discounts, extended payment terms, or bulk purchasing options.
In many cases, suppliers are willing to offer better terms to loyal customers or to secure long-term contracts.
By negotiating effectively, SMEs can reduce costs and improve cash flow.
Fostering Collaboration
Collaboration with suppliers can lead to better outcomes for both parties.
For example, sharing forecasts and sales data can help suppliers plan their production schedules more accurately.
This can lead to more reliable deliveries and potentially lower costs.
Additionally, collaborating on product development and innovation can lead to cost savings.
Suppliers may be able to suggest more cost-effective materials or manufacturing processes.
Assessing Supplier Performance
Regularly assessing supplier performance is crucial for maintaining an optimized procurement process.
This can involve evaluating factors such as delivery times, product quality, and responsiveness.
By holding suppliers accountable, SMEs can ensure they are getting the best value for their money.
If a supplier consistently underperforms, it may be necessary to seek alternatives.
Switching to a more reliable supplier can prevent delays and reduce costs associated with poor quality or late deliveries.
Implementing Best Practices in Procurement
To achieve significant cost reductions through procurement optimization, SMEs should implement best practices.
These practices can help standardize the procurement process and ensure consistency.
Standardizing Processes
Standardizing processes can reduce errors and increase efficiency.
This can include creating standardized templates for purchase orders, contracts, and other documents.
Standardized processes also make it easier to train new employees and ensure compliance with company policies.
Conducting Regular Audits
Regular audits of the procurement process can help identify areas for improvement.
Audits can reveal issues such as unauthorized purchases, incorrect pricing, or discrepancies in inventory levels.
By addressing these issues promptly, SMEs can reduce costs and improve accuracy.
Continuous Improvement
Procurement optimization is an ongoing process.
It’s essential to continuously seek ways to improve and adapt to changing conditions.
This could include adopting new technologies, updating procurement policies, or finding new suppliers.
By fostering a culture of continuous improvement, SMEs can remain competitive and achieve long-term cost savings.
Conclusion
Procurement optimization offers significant cost reduction benefits for SMEs.
By analyzing data, leveraging technology, building strong supplier relationships, and implementing best practices, SMEs can achieve more efficient and cost-effective procurement processes.
While the journey to procurement optimization may require an initial investment of time and resources, the long-term benefits make it a worthwhile endeavor.
Reducing costs through procurement optimization can help SMEs achieve greater financial stability and focus on growth and innovation.
資料ダウンロード
QCD管理受発注クラウド「newji」は、受発注部門で必要なQCD管理全てを備えた、現場特化型兼クラウド型の今世紀最高の受発注管理システムとなります。
ユーザー登録
受発注業務の効率化だけでなく、システムを導入することで、コスト削減や製品・資材のステータス可視化のほか、属人化していた受発注情報の共有化による内部不正防止や統制にも役立ちます。
NEWJI DX
製造業に特化したデジタルトランスフォーメーション(DX)の実現を目指す請負開発型のコンサルティングサービスです。AI、iPaaS、および先端の技術を駆使して、製造プロセスの効率化、業務効率化、チームワーク強化、コスト削減、品質向上を実現します。このサービスは、製造業の課題を深く理解し、それに対する最適なデジタルソリューションを提供することで、企業が持続的な成長とイノベーションを達成できるようサポートします。
製造業ニュース解説
製造業、主に購買・調達部門にお勤めの方々に向けた情報を配信しております。
新任の方やベテランの方、管理職を対象とした幅広いコンテンツをご用意しております。
お問い合わせ
コストダウンが利益に直結する術だと理解していても、なかなか前に進めることができない状況。そんな時は、newjiのコストダウン自動化機能で大きく利益貢献しよう!
(β版非公開)