- お役立ち記事
- [Sintering] Speedy prototype development using powder metallurgy
月間76,176名の
製造業ご担当者様が閲覧しています*
*2025年3月31日現在のGoogle Analyticsのデータより
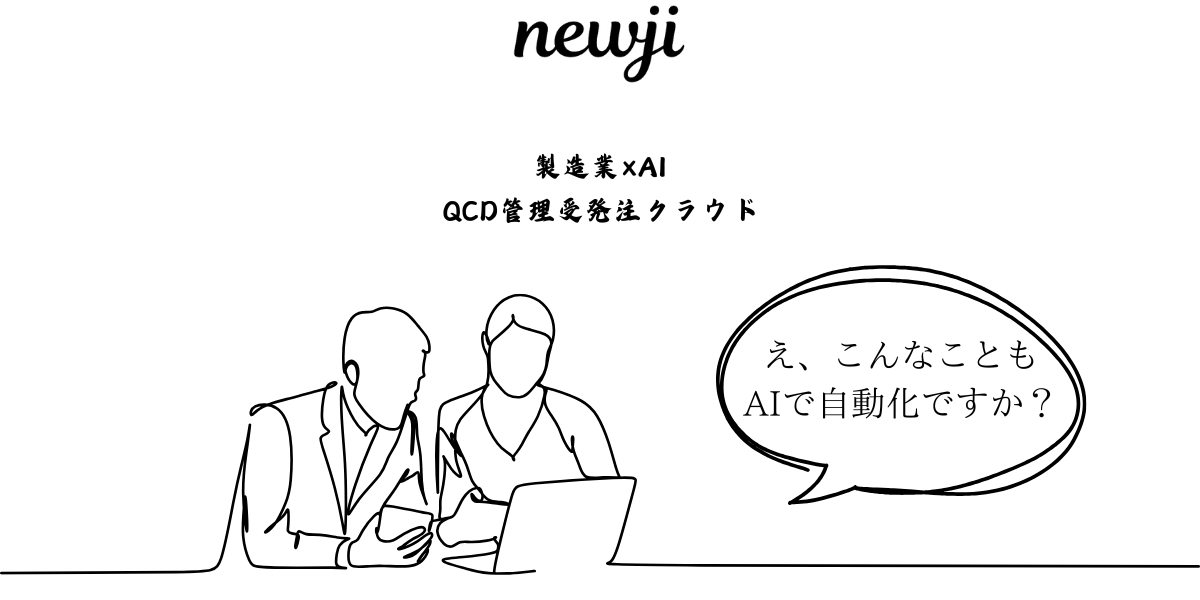
[Sintering] Speedy prototype development using powder metallurgy
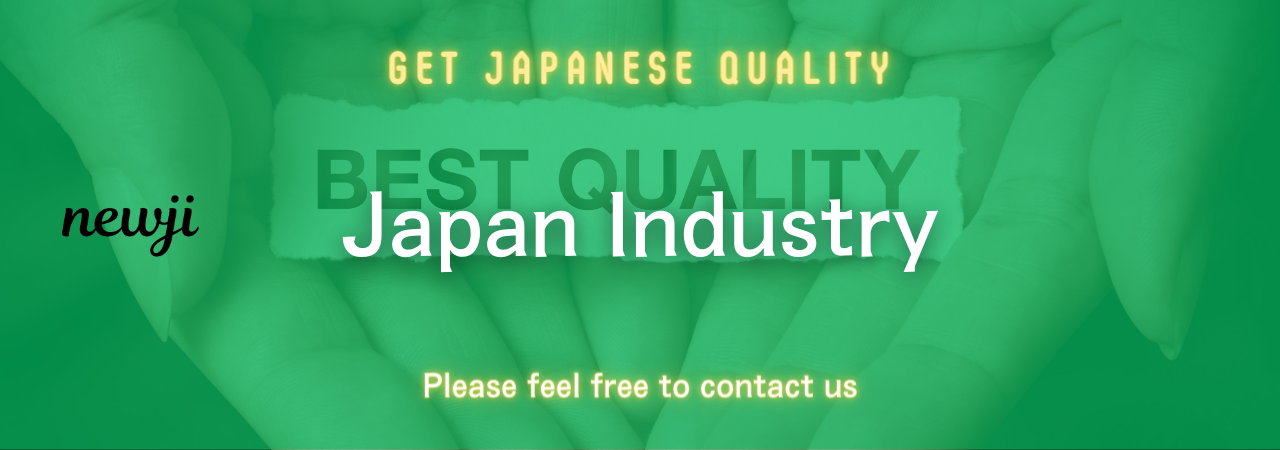
Sintering is an essential process used in the field of powder metallurgy.
The technique is widely adopted for the production of prototypes because it allows for speedy and cost-effective manufacturing of complex parts.
Whether you are a student, educator, or professional engineer, understanding sintering and its role in powder metallurgy can be highly beneficial.
Here, we will explore how this process works and why it’s so critical for rapid prototype development.
目次
What is Sintering?
Sintering is a method used to create solid materials from powders.
It involves heating the powdered material below its melting point until the particles adhere to each other.
This results in a single, solid piece.
The process enhances the strength and integrity of the material, making it highly suitable for prototyping purposes.
The Basics of Powder Metallurgy
Powder metallurgy is a manufacturing process that involves three primary steps: powder production, compaction, and sintering.
Let’s break down each step:
Powder Production
The initial step involves the creation of metal powders.
These powders are typically produced through atomization, where molten metal is fragmented into fine droplets and solidified quickly.
Alternatively, mechanical comminution and chemical reduction techniques may be used.
Compaction
In the compaction stage, metal powders are compressed to form a desired shape.
The powders are placed into a die and subjected to high pressure.
This produces a green compact — an unsolidified shape that closely resembles the final object but lacks strength.
Sintering
The sintering process completes the transformation of the green compact into a solid, durable object.
This involves heating the compact in a controlled atmosphere furnace.
During this phase, the particles bond without completely melting, which retains the shape formed during compaction.
Why Use Sintering for Prototype Development?
The role of sintering in powder metallurgy is crucial, especially when it comes to rapid prototype development.
Below are several reasons why this process is valuable for prototyping:
Cost-Effective
Sintering is less expensive compared to traditional methods like casting or forging.
Since it uses powder, which can be sourced from recycled metals, the raw material cost is reduced.
Moreover, sintering allows for the efficient use of materials with minimal waste.
Complex Geometries
One of the significant advantages of sintering is its capacity to create complex shapes and intricate geometries that are challenging for other manufacturing methods.
Designers can exploit this feature to produce prototypes that include delicate details and precise measurements.
Material Properties
The sintering process preserves the original properties of the powders, such as high thermal and electrical conductivity.
Additionally, by adjusting the sintering parameters, specific mechanical properties like hardness and tensile strength can be tailored to suit the prototype’s requirements.
Applications of Sintered Parts in Prototyping
Numerous industries take advantage of the sintering process for prototype development. Here’s how different sectors use sinter-based prototypes:
Automotive
In the automotive industry, sintered parts are used for engine components, transmission assemblies, and other precision parts.
By using sintered prototypes, engineers can assess performance before committing to mass production.
Aerospace
Aerospace engineers benefit from sintering by creating lightweight yet durable components that withstand high temperatures and stress.
It’s ideal for testing parts such as turbine blades and structural components.
Medical
The medical industry employs sintering for creating prototypes of surgical instruments and implantable devices.
The process allows for customization, ensuring that items fit specific anatomical requirements.
Limitations and Considerations
Despite its advantages, some limitations need to be considered when evaluating the use of sintering for prototype development.
Surface Finish
The surface finish of sintered parts may not be as smooth as those created using other manufacturing methods.
Secondary operations, like machining or polishing, may be necessary to achieve the desired texture.
Dimensional Accuracy
Although sintering is excellent for maintaining complex geometries, achieving tight dimensional tolerances might require precise control of the process parameters.
This could necessitate additional fine-tuning.
Conclusion
Sintering plays a critical role in the field of powder metallurgy, particularly for rapid prototype development.
This cost-effective and versatile process allows for the creation of high-quality, complex parts that serve as prototypes across various industries, including automotive, aerospace, and medical fields.
While there are limitations such as surface finish and dimensional accuracy, these can often be mitigated with supplementary procedures.
Ultimately, understanding sintering is essential for anyone involved in modern manufacturing and prototyping.
It provides an efficient gateway from conceptual design to tangible product, setting the stage for further innovations in material processing and part fabrication.
資料ダウンロード
QCD管理受発注クラウド「newji」は、受発注部門で必要なQCD管理全てを備えた、現場特化型兼クラウド型の今世紀最高の受発注管理システムとなります。
ユーザー登録
受発注業務の効率化だけでなく、システムを導入することで、コスト削減や製品・資材のステータス可視化のほか、属人化していた受発注情報の共有化による内部不正防止や統制にも役立ちます。
NEWJI DX
製造業に特化したデジタルトランスフォーメーション(DX)の実現を目指す請負開発型のコンサルティングサービスです。AI、iPaaS、および先端の技術を駆使して、製造プロセスの効率化、業務効率化、チームワーク強化、コスト削減、品質向上を実現します。このサービスは、製造業の課題を深く理解し、それに対する最適なデジタルソリューションを提供することで、企業が持続的な成長とイノベーションを達成できるようサポートします。
製造業ニュース解説
製造業、主に購買・調達部門にお勤めの方々に向けた情報を配信しております。
新任の方やベテランの方、管理職を対象とした幅広いコンテンツをご用意しております。
お問い合わせ
コストダウンが利益に直結する術だと理解していても、なかなか前に進めることができない状況。そんな時は、newjiのコストダウン自動化機能で大きく利益貢献しよう!
(β版非公開)