- お役立ち記事
- Six Sigma Success: Unveiling the Secret Behind Japanese Manufacturing Excellence
Six Sigma Success: Unveiling the Secret Behind Japanese Manufacturing Excellence
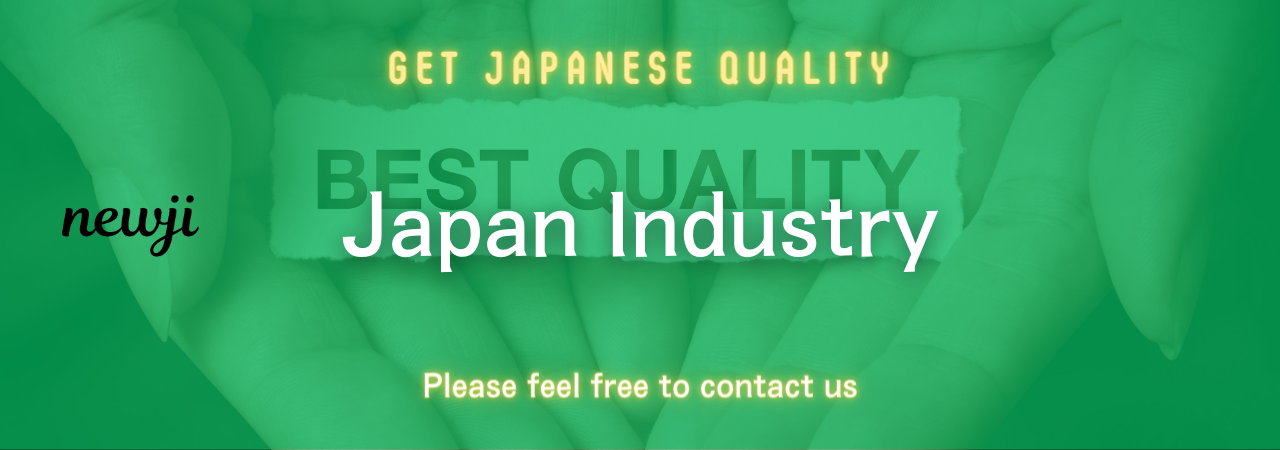
目次
Introduction to Six Sigma in Japanese Manufacturing
Six Sigma has revolutionized the manufacturing industry globally.
Its adoption by Japanese manufacturers has set a benchmark for excellence.
This methodology focuses on reducing defects and improving processes.
Japanese companies have integrated Six Sigma into their core operations.
The result is enhanced quality and customer satisfaction.
Understanding how Six Sigma contributes to Japanese manufacturing excellence is crucial.
This article delves into the secrets behind their success.
It explores practical aspects from procurement and purchasing.
Advantages and disadvantages are also discussed.
Additionally, supplier negotiation techniques and market conditions are examined.
Finally, best practices for implementing Six Sigma are highlighted.
The Essence of Six Sigma
Six Sigma is a data-driven methodology aimed at process improvement.
It seeks to identify and eliminate defects in manufacturing.
The goal is to achieve near-perfection in production processes.
Six Sigma employs statistical tools to analyze and refine workflows.
It emphasizes continuous improvement and customer satisfaction.
By minimizing variability, Six Sigma ensures consistent quality.
Japanese manufacturers have embraced this philosophy wholeheartedly.
Their commitment to Six Sigma has been instrumental in their success.
Understanding its principles is the first step towards replicating their achievements.
Integration of Six Sigma in Japanese Manufacturing
Japanese manufacturers have seamlessly integrated Six Sigma into their operations.
This integration starts from the top management down to the shop floor.
Leadership plays a pivotal role in driving Six Sigma initiatives.
Training and education are provided to all employees.
This ensures everyone is aligned with the Six Sigma objectives.
Moreover, Japanese companies foster a culture of quality and excellence.
This cultural alignment is vital for the successful implementation of Six Sigma.
The result is a unified approach towards achieving manufacturing excellence.
Procurement and Purchasing Strategies
In the realm of procurement and purchasing, Six Sigma enhances efficiency.
Japanese manufacturers utilize Six Sigma to streamline their supply chains.
This involves selecting suppliers that meet stringent quality standards.
Regular evaluations and audits are conducted to ensure compliance.
Six Sigma tools help in forecasting demand and managing inventory.
This proactive approach minimizes wastage and reduces costs.
Furthermore, Six Sigma facilitates better supplier relationships.
By setting clear expectations, Japanese companies ensure consistent quality from their suppliers.
Quality Control and Assurance
Quality control is a cornerstone of Japanese manufacturing success.
Six Sigma provides a structured framework for maintaining high quality.
Statistical process control is employed to monitor production processes.
Any deviations are promptly addressed to prevent defects.
Continuous monitoring ensures that quality standards are upheld.
This relentless focus on quality has earned Japanese manufacturers a reputation for excellence.
Customers trust the reliability and durability of their products.
Advantages of Implementing Six Sigma
Adopting Six Sigma offers numerous benefits to manufacturing companies.
These advantages are particularly evident in the Japanese context.
Enhanced Quality and Consistency
Six Sigma’s focus on defect reduction leads to superior product quality.
Consistency in manufacturing processes ensures reliable outcomes.
This consistency is crucial for maintaining customer trust and loyalty.
Cost Reduction
By eliminating defects and inefficiencies, Six Sigma significantly reduces costs.
Manufacturers save on rework, scrap, and warranty claims.
These savings can be reinvested into other areas of the business.
Improved Customer Satisfaction
High-quality products naturally lead to increased customer satisfaction.
Satisfied customers are more likely to become repeat buyers.
They also contribute to positive word-of-mouth, enhancing the company’s reputation.
Employee Empowerment
Six Sigma involves employees at all levels in the improvement process.
This empowerment leads to increased job satisfaction and productivity.
Employees feel valued and are more committed to the company’s goals.
Challenges and Disadvantages
While Six Sigma offers significant benefits, it is not without challenges.
Japanese manufacturers have encountered and overcome several obstacles.
Implementation Complexity
Six Sigma’s structured approach can be complex to implement.
It requires a deep understanding of statistical tools and methodologies.
Training and education are essential to equip employees with the necessary skills.
Resistance to Change
Introducing Six Sigma can face resistance from employees accustomed to existing processes.
Change management strategies are crucial to address and mitigate this resistance.
High Initial Costs
Implementing Six Sigma often involves substantial initial investments.
Costs include training, consultancy, and process redesign.
However, these costs are typically offset by long-term savings and improvements.
Sustainability of Improvements
Maintaining the gains achieved through Six Sigma requires ongoing effort.
Continuous monitoring and reinforcement are necessary to sustain improvements.
Supplier Negotiation Techniques
Effective supplier negotiation is vital for successful Six Sigma implementation.
Japanese manufacturers employ strategic negotiation techniques to secure quality inputs.
Building Long-term Relationships
Japanese companies prioritize long-term partnerships over short-term gains.
Trust and mutual respect are the foundation of these relationships.
This approach fosters collaboration and continuous improvement.
Clear Communication of Standards
Setting clear quality and performance expectations is essential.
Japanese manufacturers communicate their standards explicitly to suppliers.
This clarity prevents misunderstandings and ensures alignment.
Collaborative Problem-solving
When issues arise, Japanese companies engage in collaborative problem-solving with suppliers.
This joint approach leads to effective and sustainable solutions.
Performance-based Contracts
Contracts are often structured to reward suppliers based on performance.
This incentivizes suppliers to maintain high quality and efficiency.
Market Conditions and Six Sigma
Understanding market conditions is crucial for effective Six Sigma implementation.
Japanese manufacturers adeptly navigate market dynamics to sustain their excellence.
Global Competition
In a highly competitive global market, maintaining quality is imperative.
Six Sigma provides the tools to stay ahead of competitors by ensuring superior products.
Customer Expectations
Increasing customer expectations demand higher quality and reliability.
Six Sigma helps manufacturers meet and exceed these expectations consistently.
Technological Advancements
Rapid technological changes require adaptable and efficient manufacturing processes.
Six Sigma’s continuous improvement focus aligns well with embracing new technologies.
Economic Fluctuations
Economic instability can impact manufacturing operations.
Six Sigma’s cost-reduction strategies help companies remain resilient during economic downturns.
Best Practices for Six Sigma Implementation
Adopting Six Sigma requires a strategic and methodical approach.
Japanese manufacturers have refined their implementation strategies to maximize benefits.
Selecting the Right Projects
Choosing projects that align with business goals is essential.
Prioritizing high-impact areas ensures that Six Sigma initiatives deliver significant results.
Comprehensive Training Programs
Investing in thorough training equips employees with the necessary skills.
Certified Six Sigma practitioners lead projects and mentor teams.
Strong Leadership Commitment
Leadership must demonstrate unwavering commitment to Six Sigma.
Their support is crucial in driving organizational change and overcoming challenges.
Data-driven Decision Making
Reliance on data and statistical analysis underpins Six Sigma.
Decisions are made based on empirical evidence rather than intuition.
Continuous Monitoring and Feedback
Regular monitoring of processes ensures that improvements are sustained.
Feedback mechanisms facilitate ongoing enhancements and adjustments.
Case Studies: Japanese Manufacturers Excelling with Six Sigma
Examining real-world examples provides insights into Six Sigma’s impact.
Japanese manufacturers have showcased remarkable success through Six Sigma.
Toyota Motor Corporation
Toyota integrates Six Sigma into its production system.
This integration has led to significant reductions in defects and production costs.
Their commitment to quality is evident in their global reputation.
Sony Corporation
Sony employs Six Sigma to enhance its electronics manufacturing.
This approach has resulted in improved product reliability and customer satisfaction.
Panasonic Corporation
Panasonic utilizes Six Sigma to streamline its supply chain.
This has led to increased efficiency and reduced lead times.
Future Trends: Six Sigma in Japanese Manufacturing
The future of Six Sigma in Japanese manufacturing looks promising.
Advancements and evolving market conditions will shape its trajectory.
Integration with Industry 4.0
Industry 4.0 technologies complement Six Sigma by providing advanced data analytics.
This integration enhances process optimization and real-time monitoring.
Sustainability and Six Sigma
Sustainability is becoming a key focus in manufacturing.
Six Sigma can drive sustainable practices by optimizing resource usage and minimizing waste.
Global Expansion
Japanese manufacturers are expanding globally, bringing Six Sigma to new markets.
This global presence reinforces their commitment to quality and excellence.
Conclusion
Six Sigma has been a cornerstone of Japanese manufacturing excellence.
Its systematic approach to quality and process improvement has yielded significant benefits.
Japanese manufacturers have demonstrated how Six Sigma can drive efficiency, reduce costs, and enhance customer satisfaction.
Despite challenges in implementation, the advantages far outweigh the disadvantages.
Effective supplier negotiation and a deep understanding of market conditions further bolster their success.
By adhering to best practices, companies can replicate the Japanese model of excellence.
As industries evolve, Six Sigma will continue to play a pivotal role in shaping the future of manufacturing.
Embracing this methodology can lead to sustained growth and competitive advantage.
資料ダウンロード
QCD調達購買管理クラウド「newji」は、調達購買部門で必要なQCD管理全てを備えた、現場特化型兼クラウド型の今世紀最高の購買管理システムとなります。
ユーザー登録
調達購買業務の効率化だけでなく、システムを導入することで、コスト削減や製品・資材のステータス可視化のほか、属人化していた購買情報の共有化による内部不正防止や統制にも役立ちます。
NEWJI DX
製造業に特化したデジタルトランスフォーメーション(DX)の実現を目指す請負開発型のコンサルティングサービスです。AI、iPaaS、および先端の技術を駆使して、製造プロセスの効率化、業務効率化、チームワーク強化、コスト削減、品質向上を実現します。このサービスは、製造業の課題を深く理解し、それに対する最適なデジタルソリューションを提供することで、企業が持続的な成長とイノベーションを達成できるようサポートします。
オンライン講座
製造業、主に購買・調達部門にお勤めの方々に向けた情報を配信しております。
新任の方やベテランの方、管理職を対象とした幅広いコンテンツをご用意しております。
お問い合わせ
コストダウンが利益に直結する術だと理解していても、なかなか前に進めることができない状況。そんな時は、newjiのコストダウン自動化機能で大きく利益貢献しよう!
(Β版非公開)