- お役立ち記事
- Skillful use of FEM analysis and life prediction for fracture prediction
月間77,185名の
製造業ご担当者様が閲覧しています*
*2025年2月28日現在のGoogle Analyticsのデータより
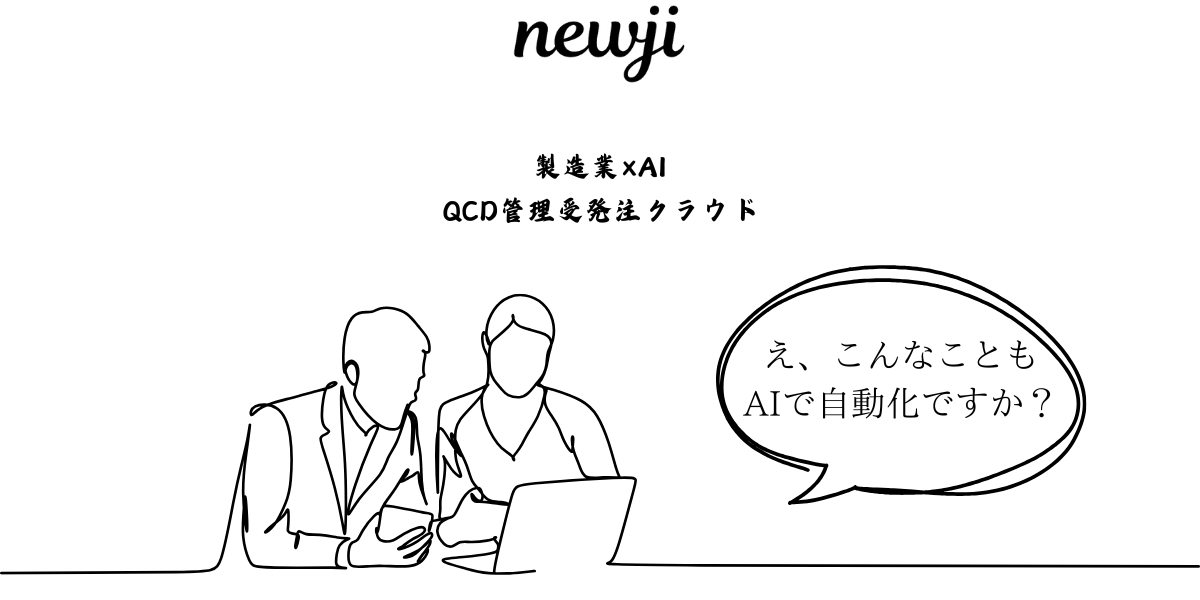
Skillful use of FEM analysis and life prediction for fracture prediction
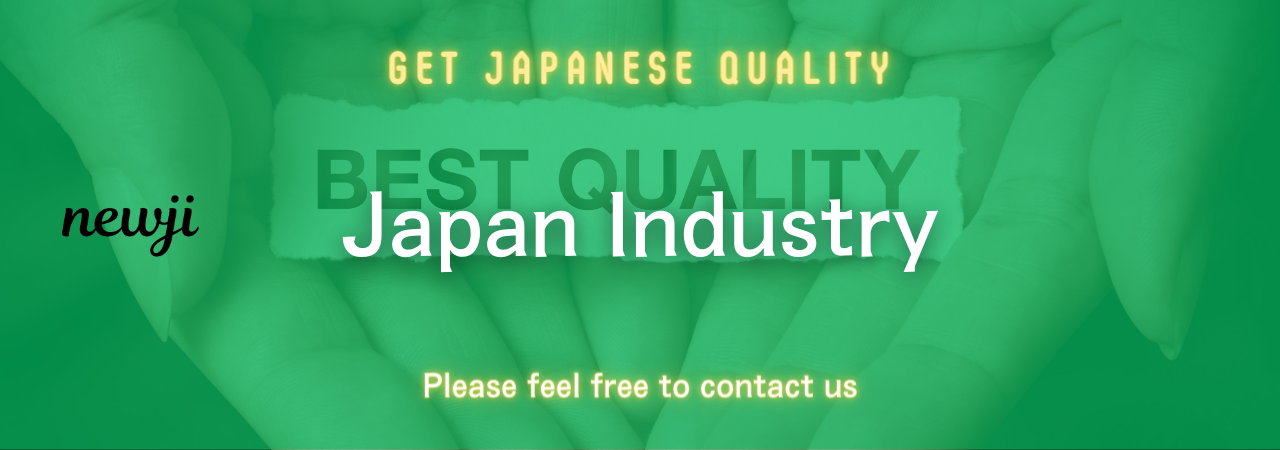
目次
Understanding FEM Analysis
Finite Element Method (FEM) analysis is a powerful computational tool used to predict how materials and structures will behave under various conditions.
It is widely employed in engineering and scientific applications to simulate physical phenomena.
By breaking down a complex system into smaller, manageable pieces, FEM allows engineers to solve problems that would otherwise be too difficult to address analytically.
FEM works by dividing a large system into smaller, simpler parts called elements.
These elements form a mesh across the entire structure, and each element is analyzed individually.
The results from each element are then assembled to diagnose the behavior of the entire structure.
This method is particularly useful for predicting stresses, strains, and displacements in materials.
Applications of FEM Analysis
FEM analysis finds applications in various industries.
In the automotive industry, it is used to design safer and more efficient vehicles.
Engineers can simulate crash tests and optimize designs before creating physical prototypes.
In aerospace, FEM helps in designing lighter yet stronger airframes, thus enhancing fuel efficiency and safety.
Furthermore, FEM analysis is critical in civil engineering for the construction of buildings and bridges.
By simulating loads and stresses, engineers can ensure structural integrity and prevent failures.
In the medical field, FEM is instrumental in designing prosthetics and other medical devices with better fit and functionality.
The Role of Life Prediction
Life prediction involves estimating the operational lifespan of a material or component before it fails.
This process is crucial to prevent unexpected breakdowns and ensure the safety and reliability of engineering designs.
Life prediction utilizes various models and tests to anticipate when a fracture might occur due to fatigue, wear, or environmental conditions.
Engineers use life prediction to determine maintenance schedules and replacement intervals.
By predicting when a component is likely to fail, companies can plan for repairs or replacements proactively, minimizing downtime and reducing costs.
Moreover, life prediction aids in material selection by identifying materials that offer better longevity and performance under specific conditions.
Techniques in Life Prediction
Several methods are employed in life prediction to foresee the failure of materials.
Fatigue analysis is one technique that evaluates how repeated stresses and strains impact the lifespan of a material.
By understanding the fatigue limit, engineers can design components to withstand specific operational conditions without premature failure.
Fracture mechanics is another approach used in life prediction.
It studies the growth of cracks in materials under stress.
By assessing the factors influencing crack propagation, engineers can predict when a fracture might occur and take necessary preventive measures.
Environmental factors such as temperature, corrosion, and humidity also play a significant role in life prediction.
Testing materials under accelerated conditions allows engineers to understand how these factors affect the lifespan of a component.
Fracture Prediction and Its Importance
Fracture prediction is a critical aspect of engineering design, as it helps in preventing catastrophic failures.
By understanding how and when a material is likely to fracture, engineers can implement design adjustments and material improvements to enhance safety and performance.
This predictive approach is essential in industries where failure can have severe consequences, such as aerospace, automotive, and construction.
Techniques for Fracture Prediction
Fracture prediction techniques often involve a combination of FEM analysis and life prediction methods.
By using FEM to analyze stress distributions and life prediction to evaluate crack growth, engineers can obtain a comprehensive understanding of when a fracture might occur.
Computational simulations play a key role in fracture prediction.
These simulations consider various loading scenarios and environmental conditions to assess the probability of fracture.
By accounting for different factors, engineers can design components to be durable under anticipated conditions.
Non-destructive testing (NDT) methods are also employed in fracture prediction.
Techniques such as ultrasound and X-ray allow engineers to detect internal defects and monitor the health of a component without causing damage.
The Intersection of FEM Analysis and Life Prediction
The integration of FEM analysis and life prediction is crucial for accurate fracture prediction.
FEM provides detailed insights into stress distributions and areas of potential weakness, while life prediction estimates the lifespan of components under real-world conditions.
By combining these tools, engineers can create robust designs that balance safety, performance, and cost-effectiveness.
This holistic approach ensures that potential issues are identified early in the design phase, allowing for preemptive solutions.
Advancements in Technology
Recent advancements in computational power and software capabilities have significantly enhanced the effectiveness of FEM analysis and life prediction.
High-performance computing allows for more complex simulations with higher accuracy, leading to better fracture predictions.
Moreover, the advent of machine learning and artificial intelligence is revolutionizing the field.
These technologies enable the analysis of large datasets to identify patterns and predict material behavior more accurately.
As these tools continue to evolve, the accuracy of fracture predictions will improve, further enhancing the safety and reliability of engineering designs.
In conclusion, the skillful use of FEM analysis and life prediction tools is paramount in the realm of fracture prediction.
By understanding the principles of these techniques and integrating them effectively, engineers can design safer, more reliable components and structures.
This proactive approach not only mitigates risks but also optimizes performance across various industries.
資料ダウンロード
QCD管理受発注クラウド「newji」は、受発注部門で必要なQCD管理全てを備えた、現場特化型兼クラウド型の今世紀最高の受発注管理システムとなります。
ユーザー登録
受発注業務の効率化だけでなく、システムを導入することで、コスト削減や製品・資材のステータス可視化のほか、属人化していた受発注情報の共有化による内部不正防止や統制にも役立ちます。
NEWJI DX
製造業に特化したデジタルトランスフォーメーション(DX)の実現を目指す請負開発型のコンサルティングサービスです。AI、iPaaS、および先端の技術を駆使して、製造プロセスの効率化、業務効率化、チームワーク強化、コスト削減、品質向上を実現します。このサービスは、製造業の課題を深く理解し、それに対する最適なデジタルソリューションを提供することで、企業が持続的な成長とイノベーションを達成できるようサポートします。
製造業ニュース解説
製造業、主に購買・調達部門にお勤めの方々に向けた情報を配信しております。
新任の方やベテランの方、管理職を対象とした幅広いコンテンツをご用意しております。
お問い合わせ
コストダウンが利益に直結する術だと理解していても、なかなか前に進めることができない状況。そんな時は、newjiのコストダウン自動化機能で大きく利益貢献しよう!
(β版非公開)