- お役立ち記事
- Skills Development for Manufacturing Supervisors
Skills Development for Manufacturing Supervisors
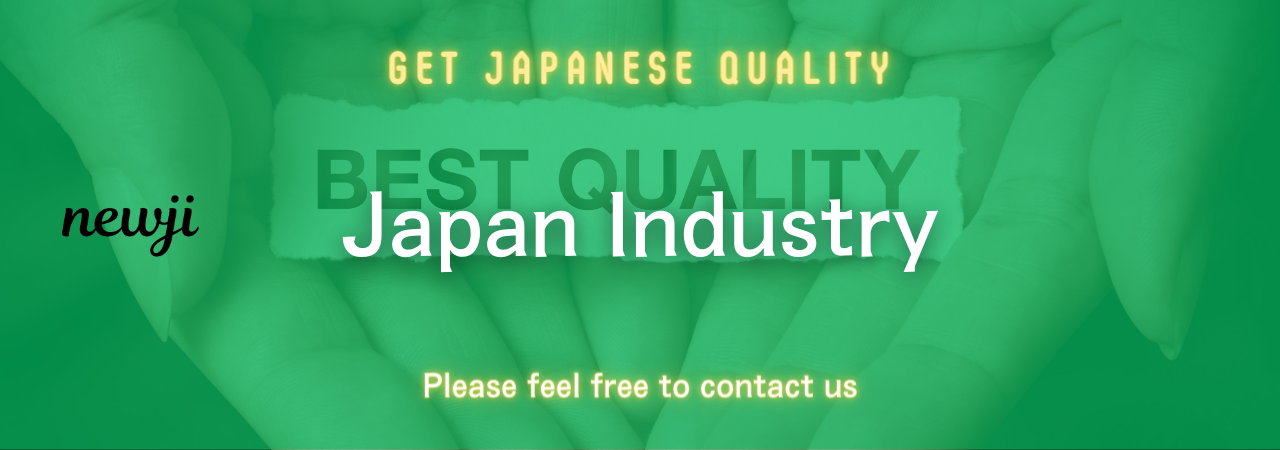
In today’s fast-paced manufacturing industry, the role of a supervisor is more critical than ever.
Supervisors need to possess a unique blend of technical expertise, leadership abilities, and problem-solving skills.
This article will explore the essential skills every manufacturing supervisor should develop to excel in their role.
目次
Technical Expertise
A solid foundation in technical knowledge is crucial for any manufacturing supervisor.
Understanding the machinery, tools, and processes that the team uses can help supervisors identify issues quickly and implement effective solutions.
Regular training sessions and workshops on the latest industry advancements can keep supervisors up-to-date with new technologies and best practices.
Understanding Equipment and Processes
Supervisors must be familiar with the equipment their team uses daily.
This includes knowing how to operate the machinery, troubleshoot common issues, and perform preventive maintenance.
Moreover, understanding the overall manufacturing process allows supervisors to optimize workflow and improve efficiency.
Supervisors should take the time to learn and understand each step of the process, from raw material handling to the final product assembly.
Continuous Learning and Improvement
The manufacturing industry is constantly evolving, with new technologies and methods emerging regularly.
To stay competitive, supervisors should actively seek out opportunities for continuous learning.
This can include attending industry conferences, enrolling in relevant courses, or participating in online forums and communities.
By staying informed about the latest trends and innovations, supervisors can implement new strategies to improve productivity and quality.
Leadership and Communication Skills
Effective leadership and communication are essential for managing a successful manufacturing team.
Supervisors must inspire and motivate their team while ensuring that everyone is on the same page.
Building a Strong Team
A strong team is built on trust, collaboration, and mutual respect.
Supervisors should foster a positive work environment by recognizing employees’ efforts and providing constructive feedback.
They should also encourage teamwork and open communication, allowing team members to share ideas and voice concerns freely.
Regular team meetings and brainstorming sessions can help build a sense of camaraderie and shared purpose.
Clear and Effective Communication
Clear communication is vital for preventing misunderstandings and ensuring that tasks are completed accurately.
Supervisors should practice active listening, making sure they understand their team’s needs and concerns.
They should also provide clear instructions and set realistic expectations.
Utilizing various communication tools, such as email, instant messaging, and project management software, can help keep everyone informed and organized.
Problem-Solving and Decision-Making
In a manufacturing environment, problems can arise at any moment.
Supervisors must be able to think on their feet and make quick, informed decisions to keep the production line running smoothly.
Identifying and Analyzing Problems
The first step in effective problem-solving is identifying the issue.
Supervisors should be observant and proactive, constantly monitoring the production process for potential problems.
Once a problem is identified, it’s essential to analyze the root cause.
This often involves gathering data, consulting with team members, and considering various possible solutions.
Implementing Solutions and Assessing Outcomes
After identifying the cause of the problem, supervisors must implement a solution promptly.
This may involve adjusting the production process, repairing equipment, or reallocating resources.
Once a solution is in place, supervisors should monitor the outcome to ensure the problem is resolved.
If the issue persists, further analysis and adjustments may be necessary.
Time Management and Organization
Efficient time management and organization are critical for meeting production deadlines and maintaining a smooth workflow.
Supervisors must be able to prioritize tasks, delegate responsibilities, and keep the production schedule on track.
Prioritizing Tasks and Delegating Responsibilities
With numerous tasks and responsibilities to juggle, supervisors must be adept at prioritizing their workload.
This involves assessing the urgency and importance of each task and determining the best course of action.
Delegating responsibilities to team members is also crucial, as it allows supervisors to focus on higher-level tasks while ensuring that all necessary work is completed.
Keeping the Production Schedule on Track
A well-organized production schedule is essential for meeting deadlines and maintaining efficiency.
Supervisors should create a detailed production plan, outlining each step of the process and allocating sufficient time for each task.
Regularly reviewing and updating the schedule can help identify potential bottlenecks and ensure that the production line runs smoothly.
Embracing Innovation and Technology
The manufacturing industry is increasingly integrating advanced technologies to improve processes and boost productivity.
Supervisors should embrace innovation and be open to adopting new technologies that can enhance their team’s performance.
Adopting Advanced Technologies
From automation and robotics to artificial intelligence and data analytics, numerous technological advancements can benefit the manufacturing industry.
Supervisors should stay informed about these technologies and assess their potential impact on their operations.
By adopting relevant technologies, supervisors can streamline processes, reduce costs, and improve overall efficiency.
Encouraging a Culture of Innovation
Creating a culture of innovation within the team is essential for continuous improvement.
Supervisors should encourage team members to think creatively and share their ideas for enhancing processes and solving problems.
Providing opportunities for skill development and experimentation can foster a more innovative and adaptable workforce.
Organizing innovation workshops and brainstorming sessions can also help generate new ideas and solutions.
In conclusion, developing a well-rounded skill set is crucial for manufacturing supervisors to excel in their role.
By focusing on technical expertise, leadership and communication, problem-solving, time management, and embracing innovation, supervisors can lead their teams to success.
Continuous learning and improvement are key to staying competitive in the ever-evolving manufacturing industry.
資料ダウンロード
QCD調達購買管理クラウド「newji」は、調達購買部門で必要なQCD管理全てを備えた、現場特化型兼クラウド型の今世紀最高の購買管理システムとなります。
ユーザー登録
調達購買業務の効率化だけでなく、システムを導入することで、コスト削減や製品・資材のステータス可視化のほか、属人化していた購買情報の共有化による内部不正防止や統制にも役立ちます。
NEWJI DX
製造業に特化したデジタルトランスフォーメーション(DX)の実現を目指す請負開発型のコンサルティングサービスです。AI、iPaaS、および先端の技術を駆使して、製造プロセスの効率化、業務効率化、チームワーク強化、コスト削減、品質向上を実現します。このサービスは、製造業の課題を深く理解し、それに対する最適なデジタルソリューションを提供することで、企業が持続的な成長とイノベーションを達成できるようサポートします。
オンライン講座
製造業、主に購買・調達部門にお勤めの方々に向けた情報を配信しております。
新任の方やベテランの方、管理職を対象とした幅広いコンテンツをご用意しております。
お問い合わせ
コストダウンが利益に直結する術だと理解していても、なかなか前に進めることができない状況。そんな時は、newjiのコストダウン自動化機能で大きく利益貢献しよう!
(Β版非公開)