- お役立ち記事
- Slip Casting Technology and Its Application in Manufacturing
Slip Casting Technology and Its Application in Manufacturing
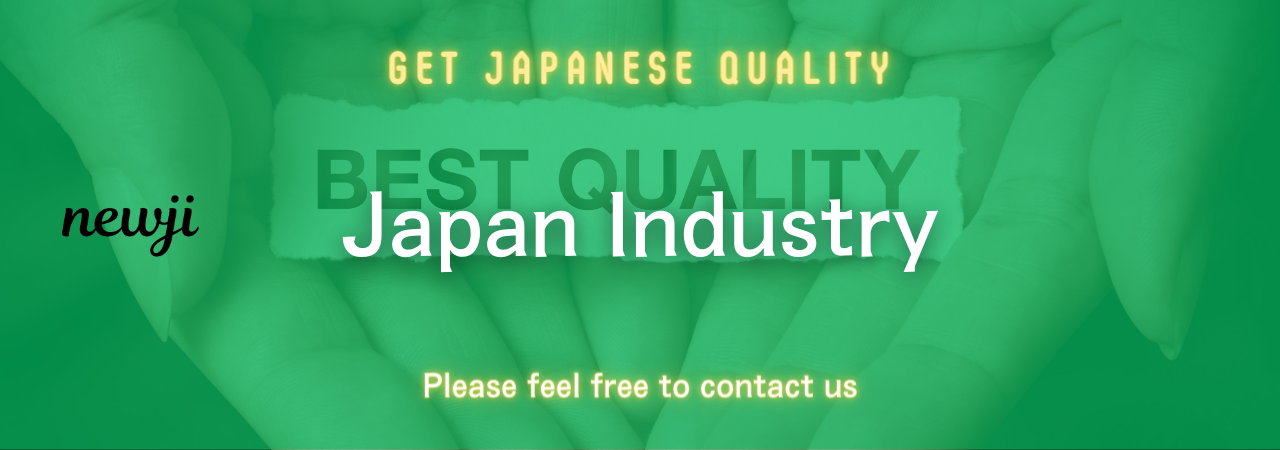
Slip casting is a fascinating process widely used in the manufacturing industry. It involves creating intricate shapes and forms by pouring liquid clay, called slip, into molds. This method is especially popular in ceramics production, as it enables the creation of complex and delicate designs with remarkable precision. Below, we will delve into the intricacies of slip casting technology and its various applications in manufacturing.
目次
Understanding Slip Casting Technology
Slip casting is a technique where liquid clay, known as slip, is poured into a prepared mold. The slip is composed of water and finely ground clay particles. The mold is typically made of plaster, which absorbs water from the slip, causing the clay particles to settle and form a solid layer on the mold’s surface.
The Slip Preparation
The first step in the slip casting process is preparing the slip. This involves mixing water with clay and other additives to create a smooth, pourable slurry. The consistency of the slip is crucial; it should not be too thick or too thin for proper casting. To achieve the right consistency, the clay must be mixed thoroughly and screened to remove any unwanted impurities or air bubbles.
Creating the Mold
Molds used in slip casting are generally made of plaster because of its porous nature. Plaster molds can absorb water from the slip, causing the clay particles to deposit along the mold’s surface. This results in the formation of a solid layer, which is the fundamental structure of the final product.
Molds are usually designed for specific shapes and can be reused multiple times. They can be created by pouring liquid plaster over an existing model or design. Once the plaster sets, the mold is carefully removed from the model, and it’s ready for casting.
The Casting Process
With the slip prepared and the mold ready, the casting process can begin. The slip is poured into the mold, filling it completely. As the plaster mold absorbs water from the slip, the clay particles start to settle against the mold’s interior surface. This process continues until a sufficiently thick layer builds up, forming the outer shape of the cast piece.
After the desired thickness is achieved, the remaining slip is poured out of the mold. This leaves a hollow, clay shell inside the mold. The time required for casting can vary, depending on the mold size and slip composition, but it typically ranges from several minutes to hours.
Drying and Firing
Removing the Cast Piece
Once the slip layer has reached the desired thickness, the mold is left to stand for a short period to allow further water absorption. The cast piece is then carefully removed from the mold. At this stage, the clay is still damp and malleable, so caution is necessary to avoid deforming or damaging the piece.
Drying the Cast
After removal from the mold, the cast pieces must be dried slowly and evenly to ensure they don’t crack or warp. The drying process can take several days, depending on the size and complexity of the cast. During this time, the water in the clay gradually evaporates, leaving behind a solid and stable structure.
Firing the Final Product
The final step in the slip casting process is firing the dried cast pieces in a kiln. Firing involves heating the clay to high temperatures, causing it to harden and become permanently solid. This process also enhances the strength and durability of the final product.
Different types of clay require different firing temperatures, which can range from 1,000 to 1,300 degrees Celsius (1,832 to 2,372 degrees Fahrenheit). Once fired, the pieces can be further glazed and fired again to achieve the desired finish and appearance.
Applications of Slip Casting in Manufacturing
Ceramics Production
One of the most common applications of slip casting is in the production of ceramics. This method is ideal for creating a wide range of ceramic products, from simple household items like plates and cups to intricate artistic sculptures and decorative items.
Slip casting allows manufacturers to produce ceramics with precise details and complex shapes that might be challenging to achieve through other methods.
Sanitary Ware
Slip casting is also extensively used in the manufacturing of sanitary ware, including toilets, sinks, and bathtubs. The ability to create complex and smooth shapes makes slip casting an ideal choice for producing these items. The end products are not only functional but also aesthetically pleasing, with improved hygiene and ease of cleaning.
Advanced Technical Ceramics
In addition to traditional ceramics, slip casting plays a crucial role in the production of advanced technical ceramics. These materials are used in various high-tech applications, such as aerospace, electronics, and medical devices.
Slip casting allows for the precise fabrication of components with intricate geometries and exceptional mechanical properties.
Art and Design
Artists and designers also utilize slip casting to create unique and imaginative works. The flexibility offered by slip casting enables the creation of custom molds and one-of-a-kind pieces that push the boundaries of traditional ceramics.
Many contemporary artists use slip casting to explore new forms and expressions, resulting in innovative and captivating art.
Conclusion
Slip casting technology is a versatile and essential method in modern manufacturing, particularly in ceramics production. The ability to create detailed and complex shapes with precision makes it a preferred choice for various applications. From everyday household items to advanced technical components, slip casting continues to play a vital role in shaping our world. Understanding this process not only highlights the ingenuity behind it but also opens up possibilities for future innovations in manufacturing.
資料ダウンロード
QCD調達購買管理クラウド「newji」は、調達購買部門で必要なQCD管理全てを備えた、現場特化型兼クラウド型の今世紀最高の購買管理システムとなります。
ユーザー登録
調達購買業務の効率化だけでなく、システムを導入することで、コスト削減や製品・資材のステータス可視化のほか、属人化していた購買情報の共有化による内部不正防止や統制にも役立ちます。
NEWJI DX
製造業に特化したデジタルトランスフォーメーション(DX)の実現を目指す請負開発型のコンサルティングサービスです。AI、iPaaS、および先端の技術を駆使して、製造プロセスの効率化、業務効率化、チームワーク強化、コスト削減、品質向上を実現します。このサービスは、製造業の課題を深く理解し、それに対する最適なデジタルソリューションを提供することで、企業が持続的な成長とイノベーションを達成できるようサポートします。
オンライン講座
製造業、主に購買・調達部門にお勤めの方々に向けた情報を配信しております。
新任の方やベテランの方、管理職を対象とした幅広いコンテンツをご用意しております。
お問い合わせ
コストダウンが利益に直結する術だと理解していても、なかなか前に進めることができない状況。そんな時は、newjiのコストダウン自動化機能で大きく利益貢献しよう!
(Β版非公開)