- お役立ち記事
- Small batch trial production of aluminum casting
月間77,185名の
製造業ご担当者様が閲覧しています*
*2025年2月28日現在のGoogle Analyticsのデータより
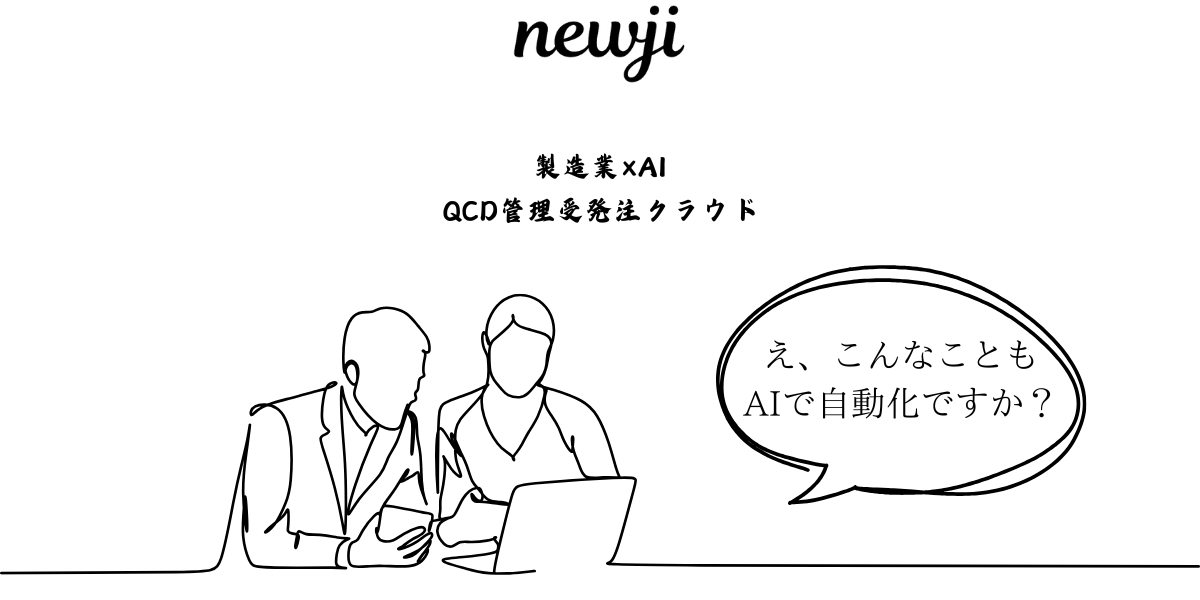
Small batch trial production of aluminum casting
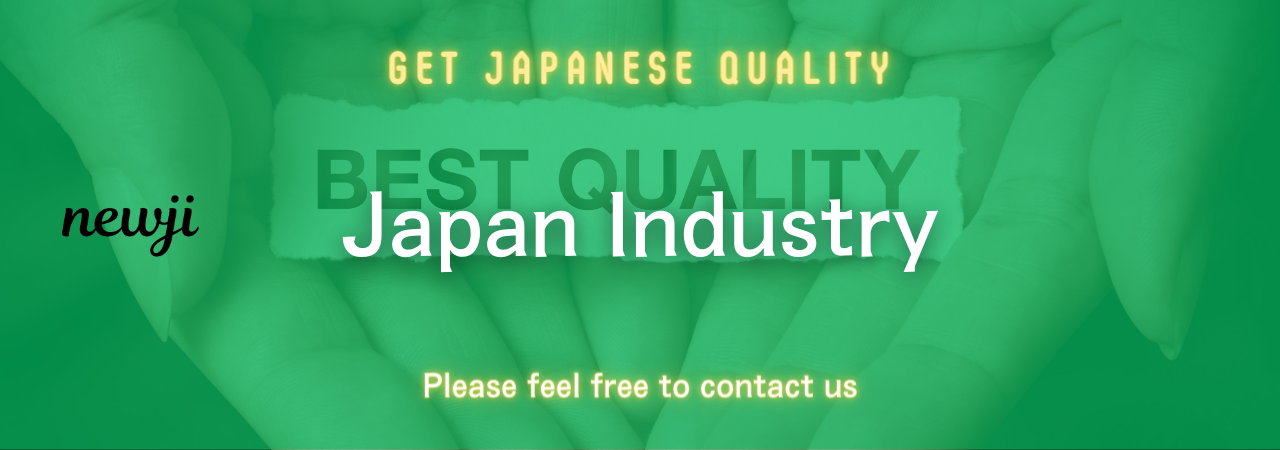
目次
Understanding Small Batch Production
Small batch trial production is a process where companies manufacture a limited number of products for testing and evaluation.
This approach is commonly used in various industries, allowing businesses to refine their product design and production techniques.
In the context of aluminum casting, small batch production presents unique opportunities and challenges.
Aluminum casting is a manufacturing process that involves pouring molten aluminum into a mold to create complex shapes.
It is renowned for producing lightweight, durable, and corrosion-resistant components.
Given its versatility, aluminum casting is widely used in industries such as automotive, aerospace, and consumer goods.
However, innovating or testing new aluminum casting designs can be daunting.
That’s where small batch trial production comes into play.
By limiting the number of initial units, companies can efficiently experiment with new designs, processes, and materials without committing to a full-scale production run.
Benefits of Small Batch Trial Production
Small batch trial production in aluminum casting offers a multitude of benefits that are crucial for product development and market readiness.
Cost-Effective Testing
Investing in a full-scale production run can be risky, especially if the design is unproven.
Small batch production helps mitigate this risk by enabling companies to test and refine products at a significantly lower cost.
This method allows businesses to identify and address any flaws or inefficiencies before going into large-scale production.
Flexibility and Innovation
The smaller scale of production facilitates rapid iterations and adjustments.
Companies can quickly implement changes to the design or process, fostering innovation and creativity.
This flexibility is essential when experimenting with new alloys or intricate casting techniques.
Reducing Time to Market
Small batch production accelerates the development cycle of aluminum castings.
By quickly identifying and correcting issues, businesses can reduce the time it takes to bring a product from concept to market.
This speed is a competitive advantage, allowing companies to respond promptly to customer demands or market trends.
Quality Assurance
Producing a limited number of units helps ensure that quality standards are met before committing to mass production.
With a smaller batch size, companies can conduct thorough inspections and tests to verify product quality.
This approach enhances the overall reliability of the final product.
Challenges of Small Batch Production in Aluminum Casting
While small batch production offers many advantages, it also comes with its set of challenges.
High Setup Costs
The initial setup for small batch production can be costly.
Creating molds, adjusting machinery, and setting up production lines require an investment that may be expensive on a per-unit basis compared to large-scale manufacturing.
However, these costs are often offset by the ability to refine the process and product before a full-scale rollout.
Limited Economies of Scale
Small batch production does not benefit from economies of scale, making the per-unit cost higher than in mass production.
Companies must carefully evaluate whether the benefits outweigh the increased costs.
Finding a balance between batch size and cost-efficiency is key to successful small batch production.
Resource Management
Efficiently managing resources such as materials, labor, and time can be challenging in small batch production.
With fewer units to produce, it may be harder to optimize resource allocation.
Organizations must ensure that their production processes are lean and efficient to minimize waste and improve profitability.
Strategies for Effective Small Batch Production
To overcome the challenges associated with small batch production, companies can implement several strategies to ensure a successful output.
Advanced Technology Integration
Incorporating advanced technologies such as computer-aided design (CAD) and computer-aided manufacturing (CAM) can enhance precision and efficiency.
These tools allow for detailed simulation and testing of designs before moving to physical production.
Automation technologies can further streamline the process, reducing both time and manual labor requirements.
Cross-Functional Collaboration
Involving various departments within an organization, such as design, engineering, and manufacturing, fosters a collaborative environment.
Cross-functional teams can provide diverse insights and expertise, leading to more innovative solutions and risk mitigation.
Open communication ensures that all aspects of the production process are optimized.
Supplier Partnership
Building strong relationships with suppliers can contribute to the success of small batch production.
Reliable suppliers can offer the necessary materials and services, ensuring that quality standards are met.
Moreover, collaboration with suppliers can lead to better material sourcing, potentially reducing costs and lead times.
Continuous Improvement
Adopting a mindset of continuous improvement is crucial in small batch production.
By regularly assessing processes and outcomes, businesses can identify areas for enhancement.
This approach not only leads to higher-quality products but also to more efficient production techniques over time.
Conclusion
Small batch trial production is a powerful tool for companies engaged in aluminum casting.
It provides a cost-effective, flexible, and rapid method for testing new designs and refining production processes.
Despite the challenges of high setup costs and limited economies of scale, strategic planning and the use of technology can make small batch production viable and profitable.
By leveraging the benefits of small batch production, businesses can remain competitive and responsive in rapidly evolving markets.
Ultimately, this approach enhances the quality of products while reducing the risks associated with mass production.
As industries continue to advance, small batch production will play a vital role in driving innovation and meeting consumer demands.
資料ダウンロード
QCD管理受発注クラウド「newji」は、受発注部門で必要なQCD管理全てを備えた、現場特化型兼クラウド型の今世紀最高の受発注管理システムとなります。
ユーザー登録
受発注業務の効率化だけでなく、システムを導入することで、コスト削減や製品・資材のステータス可視化のほか、属人化していた受発注情報の共有化による内部不正防止や統制にも役立ちます。
NEWJI DX
製造業に特化したデジタルトランスフォーメーション(DX)の実現を目指す請負開発型のコンサルティングサービスです。AI、iPaaS、および先端の技術を駆使して、製造プロセスの効率化、業務効率化、チームワーク強化、コスト削減、品質向上を実現します。このサービスは、製造業の課題を深く理解し、それに対する最適なデジタルソリューションを提供することで、企業が持続的な成長とイノベーションを達成できるようサポートします。
製造業ニュース解説
製造業、主に購買・調達部門にお勤めの方々に向けた情報を配信しております。
新任の方やベテランの方、管理職を対象とした幅広いコンテンツをご用意しております。
お問い合わせ
コストダウンが利益に直結する術だと理解していても、なかなか前に進めることができない状況。そんな時は、newjiのコストダウン自動化機能で大きく利益貢献しよう!
(β版非公開)