- お役立ち記事
- Smart factory strategy for manufacturing industry that integrates safety management and working time management
Smart factory strategy for manufacturing industry that integrates safety management and working time management
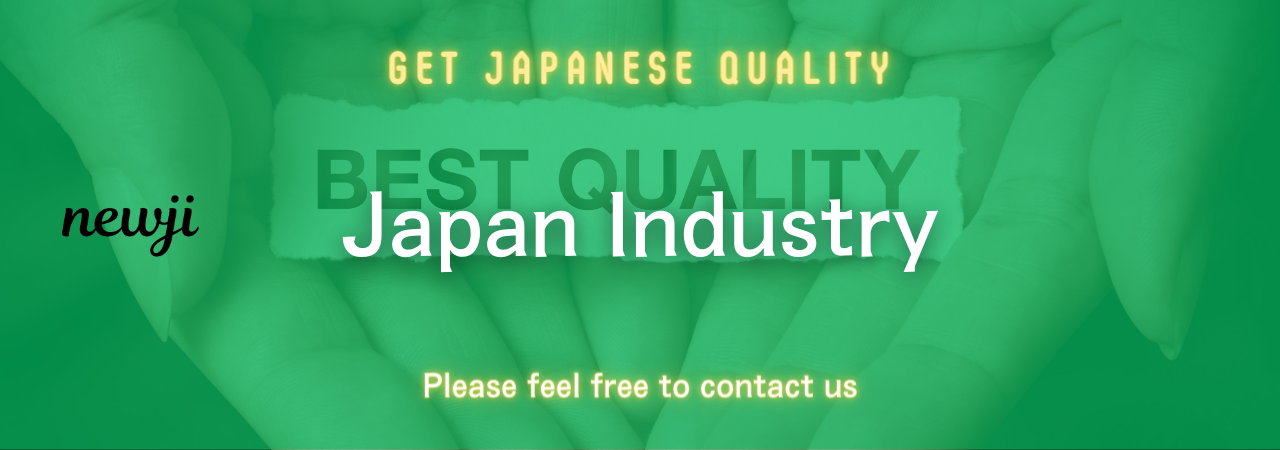
目次
Understanding the Smart Factory Concept
A smart factory is a fully integrated, collaborative manufacturing system that responds in real-time to meet changing demands and conditions.
This advanced system leverages the power of the Internet of Things (IoT), artificial intelligence (AI), and big data analytics to optimize operations, enhance production, and ensure safety.
At its core, the smart factory aims to create an autonomous environment where machines and systems work seamlessly with minimal human intervention.
In the context of the manufacturing industry, the smart factory concept translates into significant competitive advantages.
By embracing this strategy, manufacturers can boost efficiency, reduce downtime, and lower costs.
Moreover, the integration of safety management and working time management is a pivotal aspect that ensures both worker well-being and productivity.
Importance of Safety Management in Smart Factories
Safety management is a crucial component of any manufacturing operation.
In a smart factory, the use of advanced technology can significantly enhance safety protocols.
IoT-enabled devices can monitor machinery, predict failures, and alert maintenance teams before issues lead to accidents.
Integrating safety management within a smart factory involves collecting data from various sensors embedded in equipment and the environment.
This data provides real-time insights into potential hazards, helping managers and workers to mitigate risks effectively.
Additionally, AI algorithms can analyze historical data to predict future incidents, allowing proactive measures to be implemented.
Moreover, wearable technology plays a significant role in improving safety within smart factories.
Wearables can track worker movements, monitor health vitals, and issue warnings if unsafe conditions are detected.
This not only protects employees but also enhances their productivity as they can focus on their tasks without concerns about unforeseen hazards.
Working Time Management: The Smart Approach
Effective working time management is essential for maximizing productivity and ensuring employee satisfaction in the manufacturing industry.
The smart factory strategy incorporates advanced systems that automate and optimize workforce management processes.
By using AI and machine learning algorithms, manufacturers can accurately forecast demand and adjust workforce schedules accordingly.
This reduces idle time and ensures that employees are engaged when needed the most.
Smart factories also offer tools for real-time performance tracking.
With the integration of data analytics, managers can gain insights into employee efficiency, identify best practices, and adjust processes as required.
In addition, automated attendance systems reduce administrative tasks and errors in payroll processing.
This not only saves time but also improves the accuracy of time management, ultimately leading to better resource allocation and enhanced employee morale.
The Integration of Safety and Working Time Management
Combining safety management with working time management within a smart factory creates a comprehensive approach that enhances overall operations.
These elements work in tandem to ensure that the manufacturing process is efficient, safe, and adaptable to changing conditions.
For instance, by using predictive analytics, smart factories can foresee potential equipment failures and reschedule maintenance activities without disrupting production schedules.
This ensures that maintenance tasks are performed during non-peak hours, minimizing impacts on productivity and reducing safety risks associated with unexpected breakdowns.
Moreover, the integration enables better compliance with labor laws and safety regulations.
Automated systems help ensure all safety protocols are followed, and employee working hours do not exceed legal limits.
This dual approach also aids in workforce planning, as it allows management to align workforce availability with machinery requirements.
Thus, not only is the safety of workers prioritized, but production schedules are also optimized to reduce bottlenecks and downtime.
Case Studies of Successful Smart Factory Implementations
Several manufacturing industries have already reaped the benefits of smart factory strategies.
Let’s explore a few case studies that highlight the successful integration of safety and working time management.
1. **Automotive Industry:**
A leading automaker integrated IoT and AI into their assembly line operations, achieving a significant reduction in accidents by predicting equipment failures.
Wearable technology was employed for real-time monitoring of worker safety, further augmenting the safety framework.
2. **Consumer Electronics:**
A major electronics manufacturer embraced smart factory technologies to automate workforce scheduling.
They implemented AI-driven systems to accurately predict consumer demand and align workforce requirements, which resulted in improved efficiency and reduced operational costs.
3. **Food and Beverage:**
In the food processing sector, smart factories utilized sensor technology for real-time monitoring of machinery and environmental conditions.
This move enhanced both safety and compliance with health standards while optimizing workforce management to meet fluctuating production demands.
These examples illustrate how adopting a smart factory strategy can create an environment that not only prioritizes worker safety but also optimizes processes for better productivity.
Future Prospects of Smart Factories
As technology continues to evolve, the role of smart factories in the manufacturing industry will only grow more significant.
Future advancements will bring even more sophisticated systems that integrate safety management and working time management seamlessly.
The rise of digital twins, virtual models of physical entities, will further revolutionize the manufacturing sector.
These digital counterparts allow for simulations that can enhance safety protocols and optimize production scheduling before physical implementation.
Moreover, the acceleration of 5G technology will enhance connectivity and communication between devices, facilitating real-time data sharing and faster decision-making in smart factories.
This will undoubtedly advance the integration of safety and working time management, leading to unprecedented levels of efficiency and safety.
In conclusion, the adoption of a smart factory strategy is not just a trend but a necessity for the modern manufacturing industry.
By focusing on the integration of safety management and working time management, manufacturers can ensure operational excellence while safeguarding their most valuable asset – their workforce.
資料ダウンロード
QCD調達購買管理クラウド「newji」は、調達購買部門で必要なQCD管理全てを備えた、現場特化型兼クラウド型の今世紀最高の購買管理システムとなります。
ユーザー登録
調達購買業務の効率化だけでなく、システムを導入することで、コスト削減や製品・資材のステータス可視化のほか、属人化していた購買情報の共有化による内部不正防止や統制にも役立ちます。
NEWJI DX
製造業に特化したデジタルトランスフォーメーション(DX)の実現を目指す請負開発型のコンサルティングサービスです。AI、iPaaS、および先端の技術を駆使して、製造プロセスの効率化、業務効率化、チームワーク強化、コスト削減、品質向上を実現します。このサービスは、製造業の課題を深く理解し、それに対する最適なデジタルソリューションを提供することで、企業が持続的な成長とイノベーションを達成できるようサポートします。
オンライン講座
製造業、主に購買・調達部門にお勤めの方々に向けた情報を配信しております。
新任の方やベテランの方、管理職を対象とした幅広いコンテンツをご用意しております。
お問い合わせ
コストダウンが利益に直結する術だと理解していても、なかなか前に進めることができない状況。そんな時は、newjiのコストダウン自動化機能で大きく利益貢献しよう!
(Β版非公開)