- お役立ち記事
- Smooth transition process from prototype to mass production
月間76,176名の
製造業ご担当者様が閲覧しています*
*2025年3月31日現在のGoogle Analyticsのデータより
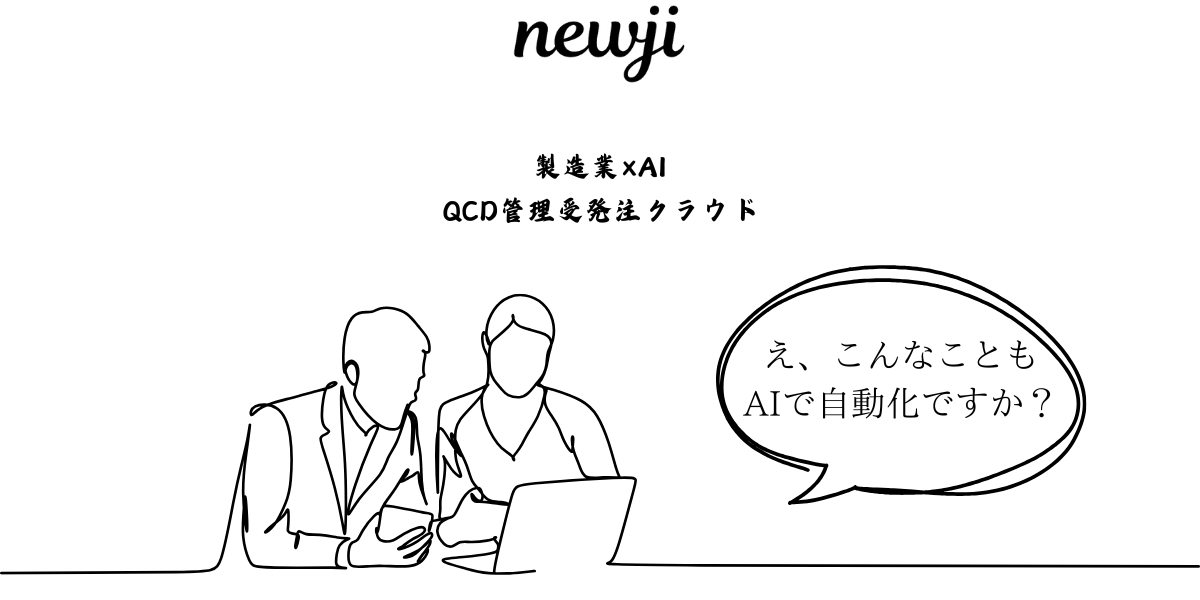
Smooth transition process from prototype to mass production
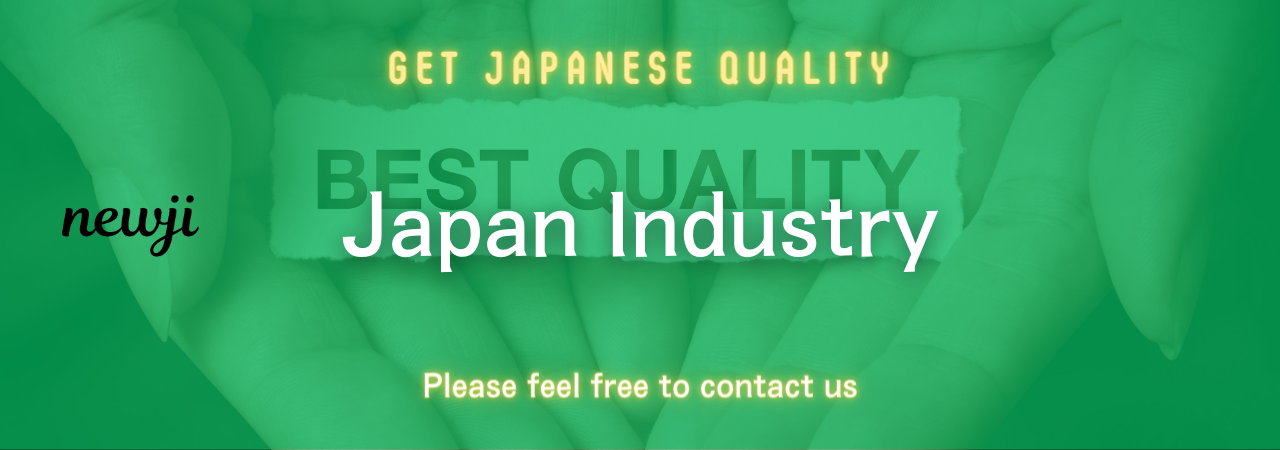
目次
Understanding the Transition Process
The journey from a prototype to mass production is a critical path for any product development.
This process involves multiple stages that ensure the product not only meets the initial specifications but is also ready for large-scale manufacturing.
A smooth transition is crucial to prevent costly delays and ensure customer satisfaction.
What is a Prototype?
A prototype is an early sample or model of a product constructed to evaluate a concept or process.
It serves as a tangible representation to test and refine design aspects, identify potential issues, and gather user feedback.
Typically, prototypes are not built for durability or longevity.
Instead, they focus on mimicking the product’s desired functionalities and aesthetic qualities.
The Importance of a Well-Designed Prototype
Having a well-designed prototype is foundational for successful production transition.
It provides a clear blueprint of the final product and helps teams identify potential challenges before they escalate in the mass production phase.
Moreover, prototypes allow stakeholders to visualize the product, aiding in securing investments and creating marketing strategies.
The Steps in Transitioning from Prototype to Mass Production
Successfully transitioning from a prototype to mass production involves several critical steps:
1. Refined Design and Engineering
After receiving feedback from prototypes, designs often need refinement.
This step includes detailed engineering to confirm that the product can be manufactured efficiently and cost-effectively.
It involves addressing issues related to material choice, functionality, and compliance with regulatory standards.
2. Cost Analysis and Budgeting
Determining the cost of production is a crucial step in the transition process.
An accurate cost analysis involves evaluating factors such as raw material expenses, labor costs, machinery, and logistics.
Budgeting ensures that production aligns with financial expectations and prevents unforeseen expenses that could hinder profitability.
3. Supplier and Manufacturer Selection
Choosing the right suppliers and manufacturers is essential for a smooth transition.
It’s important to evaluate their experience, production capacity, location, and reliability.
A strong partnership with suppliers and manufacturers can mitigate risks and ensure timely delivery of quality components.
4. Pilot Runs and Testing
Before full-scale production, conducting pilot runs is crucial.
These limited production runs help manufacturers tweak the process and ensure product consistency.
Testing during pilot runs aids in identifying defects, verifying quality standards, and ensuring that the final product meets customer expectations.
5. Quality Control and Assurance
Establish a robust quality control process to maintain the integrity of the product during mass production.
Quality assurance helps detect problems early, ensuring that each product manufactured meets the predefined standards.
It involves routine inspections and tests throughout the production process.
6. Scaling Production
Once initial hurdles are addressed and pilot runs are successful, the production scale can be increased.
This involves ramping up manufacturing operations to meet demand.
Efficiency in scaling production is key to maintaining product availability in the market.
7. Distribution and Logistics Planning
Smoothly transitioning to mass production also involves strategizing the distribution and logistics.
Planning effective logistics ensures that the product reaches the market efficiently, keeping pace with customer demand.
It encompasses inventory management, shipping processes, and selecting suitable distribution networks.
Challenges in the Transition Process
The path from prototype to mass production is full of potential challenges.
Design Flaws
Overlooking design imperfections during the prototyping phase can result in costly setbacks during mass production.
Careful validation and testing can help identify and mitigate these issues early.
Cost Overruns
Unexpected expenses can arise from various factors such as material shortages or changes in production requirements.
Regular budget reviews and efficient resource management can help keep costs under control.
Supplier Delays
Delays from suppliers can bottleneck the production line, resulting in missed deadlines.
Having contingency plans and backup suppliers can reduce dependency on a single source.
Quality Inconsistency
Maintaining consistent quality across a large batch of products is challenging.
Relying on structured quality control procedures ensures that each product meets the same high standards.
Conclusion
The transition from prototype to mass production is a significant phase in product development.
With careful planning, proactive problem-solving, and effective collaboration with partners, companies can navigate this complex process smoothly.
This ensures the product’s commercial success and acceptance in the market, while also adhering to cost and quality benchmarks.
Understanding and implementing these strategies empowers businesses to mitigate risks and capitalize on their innovations effectively.
資料ダウンロード
QCD管理受発注クラウド「newji」は、受発注部門で必要なQCD管理全てを備えた、現場特化型兼クラウド型の今世紀最高の受発注管理システムとなります。
ユーザー登録
受発注業務の効率化だけでなく、システムを導入することで、コスト削減や製品・資材のステータス可視化のほか、属人化していた受発注情報の共有化による内部不正防止や統制にも役立ちます。
NEWJI DX
製造業に特化したデジタルトランスフォーメーション(DX)の実現を目指す請負開発型のコンサルティングサービスです。AI、iPaaS、および先端の技術を駆使して、製造プロセスの効率化、業務効率化、チームワーク強化、コスト削減、品質向上を実現します。このサービスは、製造業の課題を深く理解し、それに対する最適なデジタルソリューションを提供することで、企業が持続的な成長とイノベーションを達成できるようサポートします。
製造業ニュース解説
製造業、主に購買・調達部門にお勤めの方々に向けた情報を配信しております。
新任の方やベテランの方、管理職を対象とした幅広いコンテンツをご用意しております。
お問い合わせ
コストダウンが利益に直結する術だと理解していても、なかなか前に進めることができない状況。そんな時は、newjiのコストダウン自動化機能で大きく利益貢献しよう!
(β版非公開)