- お役立ち記事
- Soldering Techniques and Considerations: Joining Processes for Component Bonding and Improved Reliability
Soldering Techniques and Considerations: Joining Processes for Component Bonding and Improved Reliability
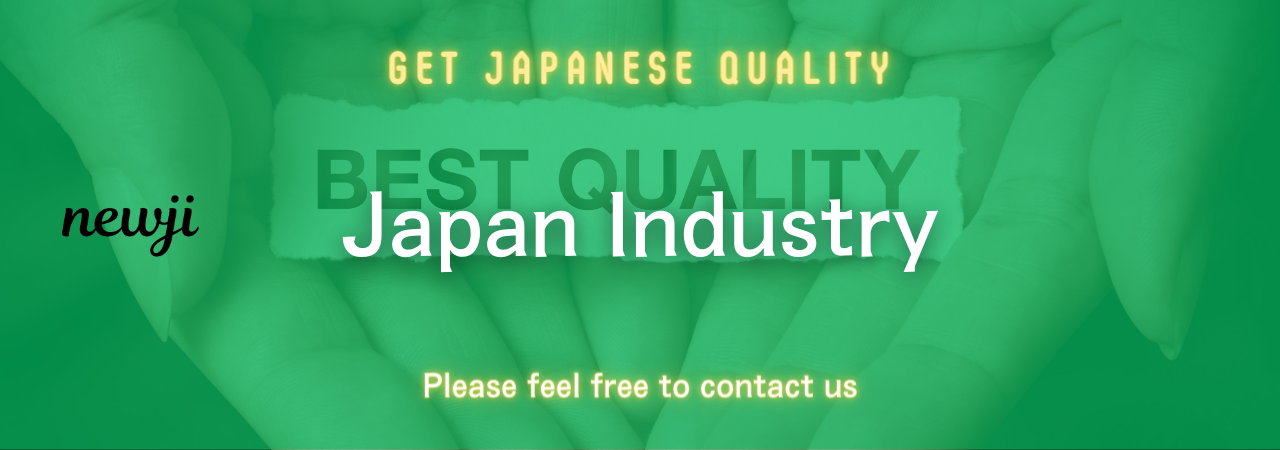
Soldering is a fundamental technique used in electronics to bond components securely, ensuring efficient electrical connectivity and mechanical stability.
Understanding proper soldering techniques and considerations can greatly improve the reliability and durability of electronic devices.
Let’s delve into the essentials of soldering, including crucial methods and things to consider for optimum results.
目次
Understanding Soldering
Soldering involves joining two or more metal items by melting a filler metal, known as solder, into the joint.
The filler metal has a lower melting point than the workpieces, allowing it to melt and flow into the joint without melting the components themselves.
This process creates a strong, electrical bond essential for electronic devices to function properly.
Types of Solder
Lead-based Solder
Lead-based solder used to be the most common option due to its ease of use and reliable results.
It typically consists of a tin-lead alloy, usually in a 60/40 ratio.
However, the use of lead raises significant health and environmental concerns, leading to restrictions and a shift toward lead-free alternatives.
Lead-free Solder
Lead-free solder is now the standard in most electronics manufacturing, particularly in compliance with the Restriction of Hazardous Substances (RoHS) directive.
Common compositions include tin-copper, tin-silver, and tin-silver-copper alloys.
While lead-free solders have higher melting points and can be trickier to work with, they are safer for both the environment and human health.
Soldering Techniques
Hand Soldering
Hand soldering is often performed using a soldering iron.
The soldering iron is heated to a high temperature, allowing the solder to melt and form a bond between the components.
Key steps in hand soldering include:
1. Cleaning the surfaces to be soldered to ensure proper adhesion.
2. Applying flux to remove oxides and improve solder flow.
3. Heating the joint with the soldering iron until the solder melts and flows into the joint.
4. Allowing the joint to cool undisturbed to form a solid connection.
Reflow Soldering
Reflow soldering is commonly used in automated manufacturing for surface-mount components.
The process involves printing solder paste onto the PCB, placing components, and heating the assembly in a reflow oven.
The oven’s controlled temperature profile melts the solder, creating reliable joints.
Reflow soldering ensures high precision and consistency, making it ideal for mass production.
Wave Soldering
Wave soldering is another automated technique often used for through-hole components.
In this process, the PCB passes over a wave of molten solder, which covers and bonds the component leads to the board.
Wave soldering is efficient for soldering multiple joints simultaneously, reducing production time compared to hand soldering.
Soldering Considerations
Temperature Control
Proper temperature control is crucial in soldering, as excessive heat can damage components and cause poor solder joints.
Lead-based solders melt around 183°C (361°F), whereas lead-free solders require higher temperatures, usually around 217°C to 219°C (423°F to 426°F).
Using a temperature-controlled soldering iron or reflow oven helps maintain the optimal temperature for the solder being used, ensuring reliable connections without damaging sensitive components.
Flux Application
Flux is a chemical agent applied to the surfaces being soldered to remove oxides and contaminants.
It enhances the flow of solder and improves the wettability of the surfaces.
Using the correct type and amount of flux is important to achieving high-quality solder joints.
Flux can be found in various forms, such as liquid, paste, or included within the solder wire itself.
Joint Inspection
Inspecting solder joints is essential to ensure they meet the required standards for mechanical strength and electrical conductivity.
Common inspection methods include visual inspection with magnification, X-ray inspection for hidden joints and automated optical inspection (AOI).
Typical defects to look for include cold joints, solder bridges, and voids.
Identifying and addressing these issues early can prevent device failures and ensure long-term reliability.
Component Placement
Proper component placement is key to achieving effective solder joints.
Misaligned components can lead to poor electrical connections and mechanical instability.
Using templates or automated pick-and-place machines can help ensure precise component placement, particularly in high-volume production environments.
For hand soldering, taking the time to carefully position components before soldering is crucial.
Environmental Factors
Environmental factors like humidity and cleanliness can affect soldering quality.
High humidity levels can lead to oxidation on component surfaces, making it harder for solder to adhere.
Maintaining a clean work environment free of dust and contaminants also helps ensure more reliable solder joints.
Using anti-static precautions can protect sensitive components from electrostatic discharge (ESD), which can damage electronic devices during soldering.
Conclusion
Mastering soldering techniques and understanding the key considerations involved in the process are crucial for achieving reliable and durable electronic connections.
Whether using hand soldering, reflow soldering, or wave soldering, maintaining proper temperature control, applying flux correctly, inspecting joints thoroughly and considering environmental factors are all essential steps.
By adhering to these practices, you can ensure the longevity and performance of electronic assemblies, contributing to the overall reliability of electronic devices.
資料ダウンロード
QCD調達購買管理クラウド「newji」は、調達購買部門で必要なQCD管理全てを備えた、現場特化型兼クラウド型の今世紀最高の購買管理システムとなります。
ユーザー登録
調達購買業務の効率化だけでなく、システムを導入することで、コスト削減や製品・資材のステータス可視化のほか、属人化していた購買情報の共有化による内部不正防止や統制にも役立ちます。
NEWJI DX
製造業に特化したデジタルトランスフォーメーション(DX)の実現を目指す請負開発型のコンサルティングサービスです。AI、iPaaS、および先端の技術を駆使して、製造プロセスの効率化、業務効率化、チームワーク強化、コスト削減、品質向上を実現します。このサービスは、製造業の課題を深く理解し、それに対する最適なデジタルソリューションを提供することで、企業が持続的な成長とイノベーションを達成できるようサポートします。
オンライン講座
製造業、主に購買・調達部門にお勤めの方々に向けた情報を配信しております。
新任の方やベテランの方、管理職を対象とした幅広いコンテンツをご用意しております。
お問い合わせ
コストダウンが利益に直結する術だと理解していても、なかなか前に進めることができない状況。そんな時は、newjiのコストダウン自動化機能で大きく利益貢献しよう!
(Β版非公開)