- お役立ち記事
- Solutions and Prevention of Leakage: Measures to Improve Production Quality and Processing Efficiency
Solutions and Prevention of Leakage: Measures to Improve Production Quality and Processing Efficiency
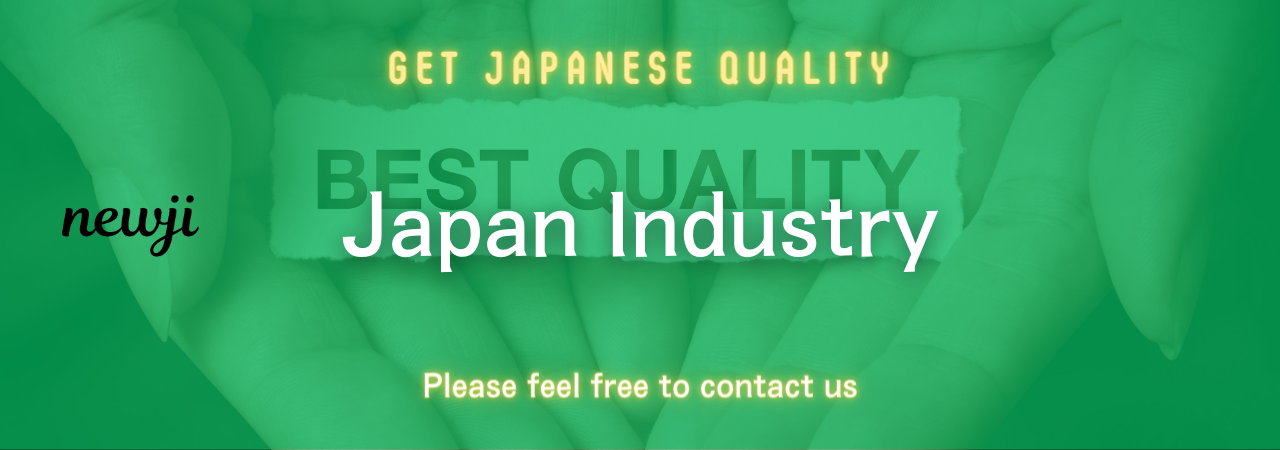
Leakage may seem like a small issue, but it can cause big problems, especially in production and processing industries. Understanding how to prevent and fix leakage not only improves production quality but also boosts efficiency. Here, we will explore various solutions and preventive measures to combat leakage and make your operations run smoother.
目次
Understanding the Impact of Leakage
Leakage can occur in various forms, such as oil, gas, water, or even electricity, within processing systems and production lines. These leaks can lead to material waste, increased costs, potential safety hazards, and environmental impacts. For businesses, this can also mean decreased product quality and customer satisfaction. Therefore, addressing leakage issues promptly and effectively is crucial.
Identifying Common Causes of Leakage
1. Wear and Tear: Over time, pipes, seals, and other components in machinery can wear down, leading to leaks. This natural degradation can be exacerbated by harsh working conditions or poor maintenance.
2. Improper Installation: If components are not installed correctly, they are more likely to leak. This can be due to poor workmanship or the use of substandard materials.
3. Corrosion: Materials like iron and steel can corrode when exposed to certain chemicals or environments, weakening the integrity of pipes and connectors.
4. Temperature Fluctuations: Extreme changes in temperature can cause expansion and contraction in materials, creating cracks and gaps that lead to leaks.
5. Vibration: Machinery that vibrates heavily can loosen joints and fittings over time, leading to leaks if not regularly checked and tightened.
Preventive Measures to Stop Leakage
1. Regular Maintenance: Implementing a routine maintenance schedule can prevent leakage by catching wear and tear early. This includes regular inspections, lubrication of moving parts, and immediate replacement of worn components.
2. Quality Materials and Installation: Use high-quality materials that are suitable for the specific environmental conditions and ensure components are installed by qualified professionals. Properly installed fittings, joints, and seals stand a better chance of withstanding operational stresses.
3. Corrosion Protection: Apply protective coatings to metals exposed to corrosive environments and consider using corrosion-resistant materials like stainless steel or PVC for pipes and fittings.
4. Temperature Control: Controlling the operating environment to prevent extreme temperature fluctuations can help maintain material integrity. Additionally, use materials designed to expand and contract without compromising the system.
5. Vibration Damping: Install vibration damping mounts or materials to reduce the impact of vibrations on machinery. Regularly check and tighten fittings and joints to ensure they stay secure.
Technological Solutions to Enhance Production Quality
1. Leak Detection Systems: Invest in advanced leak detection systems that can monitor pipelines and machinery in real-time. These systems use sensors to detect minute changes in pressure, flow, or composition, enabling immediate identification and addressing of leaks.
2. Automated Maintenance Alerts: Modern manufacturing systems can include automated alerts for maintenance needs. These systems use data from sensors to predict when components are likely to fail, allowing for preemptive maintenance.
3. High-Performance Seals and Gaskets: Utilize seals and gaskets made from advanced materials that offer high resistance to wear, temperature changes, and chemical exposure.
4. Predictive Analytics: Use predictive maintenance software to analyze data trends and anticipate potential leakage points before they occur. This proactive approach helps in scheduling timely interventions, reducing downtime and costs associated with unplanned repairs.
Employee Training and Awareness
Train your staff to recognize early signs of leakage and understand the importance of regular maintenance. Educate them on using proper techniques and tools for component installation and repair. Foster a culture of diligence and attention to detail to reduce human errors that can lead to leaks.
Improving Efficiency Through Proactive Measures
1. Energy Recovery Systems: Implement energy recovery systems to capture and reuse energy from leaking fluids or gases. This not only minimizes waste but also improves overall operational efficiency.
2. Flow Management: Optimize fluid flow in your pipelines to maintain a consistent pressure that diminishes the chances of leaks. Utilize flow meters and control valves to regulate and monitor the flow effectively.
3. Redundant Systems: In critical applications, redundant systems can ensure that even if one part of the system fails, another can handle the load. This redundancy minimizes the chances of shutdowns due to leaks, maintaining continuity in production.
4. Robust Quality Control: Establish rigorous quality control processes to ensure all components meet high standards before being installed. Continuous quality checks can identify potential weak points that may lead to leaks.
Cost-Benefit Analysis of Leak Prevention
While investing in high-quality materials, advanced detection systems, and regular maintenance might seem costly initially, the long-term benefits far outweigh these costs. Preventing leaks reduces material waste, lowers repair costs, extends equipment lifespan, enhances product quality, and safeguards against potential accidents and environmental damage. Ultimately, efficient leak prevention leads to higher productivity and profitability.
Conclusion: Commitment to Continuous Improvement
Preventing and addressing leakage is a proactive approach crucial for maintaining high production quality and processing efficiency. By understanding the causes, implementing preventive measures, leveraging technological advancements, and maintaining a diligent workforce, businesses can minimize the detrimental effects of leaks. Regular assessment and improvement of leak prevention strategies ensure sustainable and effective operations, leading to long-term success and customer satisfaction.
資料ダウンロード
QCD調達購買管理クラウド「newji」は、調達購買部門で必要なQCD管理全てを備えた、現場特化型兼クラウド型の今世紀最高の購買管理システムとなります。
ユーザー登録
調達購買業務の効率化だけでなく、システムを導入することで、コスト削減や製品・資材のステータス可視化のほか、属人化していた購買情報の共有化による内部不正防止や統制にも役立ちます。
NEWJI DX
製造業に特化したデジタルトランスフォーメーション(DX)の実現を目指す請負開発型のコンサルティングサービスです。AI、iPaaS、および先端の技術を駆使して、製造プロセスの効率化、業務効率化、チームワーク強化、コスト削減、品質向上を実現します。このサービスは、製造業の課題を深く理解し、それに対する最適なデジタルソリューションを提供することで、企業が持続的な成長とイノベーションを達成できるようサポートします。
オンライン講座
製造業、主に購買・調達部門にお勤めの方々に向けた情報を配信しております。
新任の方やベテランの方、管理職を対象とした幅広いコンテンツをご用意しております。
お問い合わせ
コストダウンが利益に直結する術だと理解していても、なかなか前に進めることができない状況。そんな時は、newjiのコストダウン自動化機能で大きく利益貢献しよう!
(Β版非公開)