- お役立ち記事
- Solving Manufacturing Industry Issues! Big data analysis to improve efficiency and quality!
月間76,176名の
製造業ご担当者様が閲覧しています*
*2025年3月31日現在のGoogle Analyticsのデータより
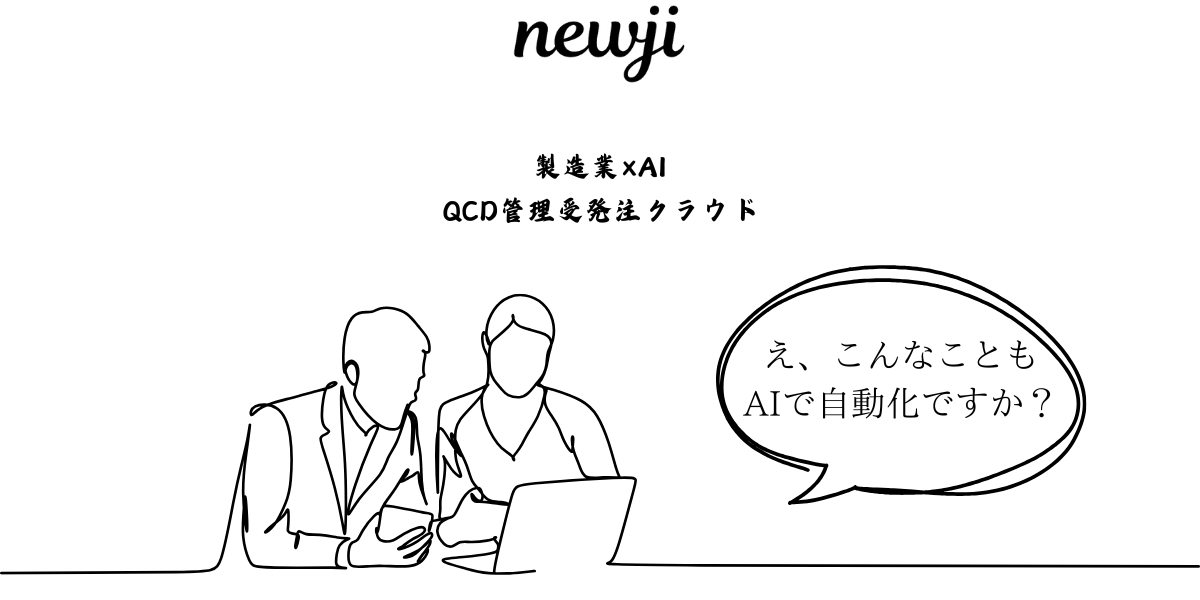
Solving Manufacturing Industry Issues! Big data analysis to improve efficiency and quality!
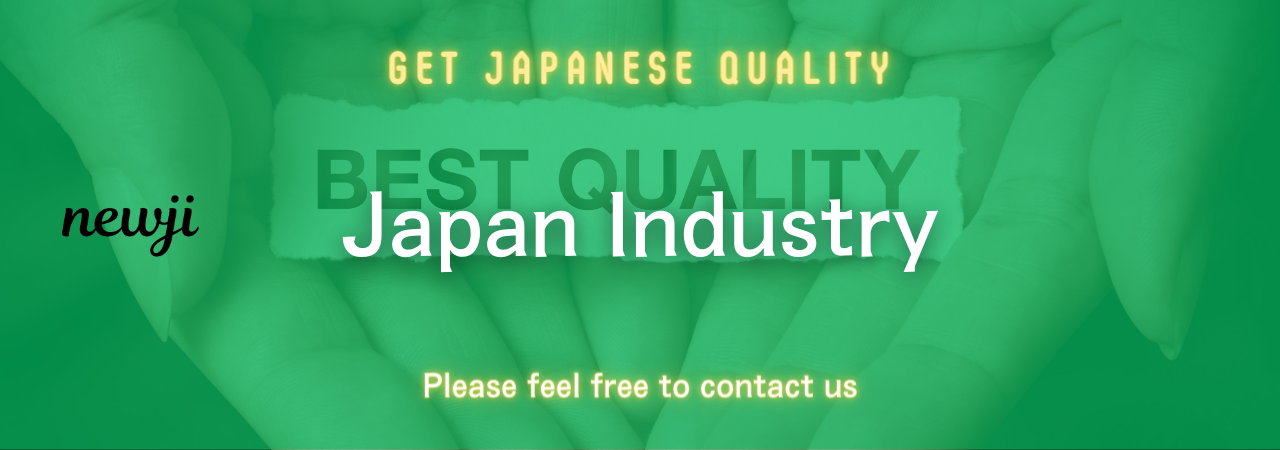
In the competitive world of the manufacturing industry, staying ahead is crucial.
Companies must continuously improve their operations to ensure efficiency and quality.
One of the most effective tools for achieving this is big data analysis.
By leveraging big data, manufacturers can gain invaluable insights that lead to better decision-making, optimized processes, and enhanced product quality.
目次
Understanding Big Data in Manufacturing
Big data refers to the vast amounts of information generated by various sources.
In manufacturing, data comes from machinery, supply chains, production processes, and even customer feedback.
Advanced technologies such as sensors and IoT devices collect this data in real-time.
The key to utilizing this information lies in proper analysis.
Data Collection and Storage
The first step in big data analysis is collecting relevant information.
Manufacturers use a range of devices, like sensors on equipment, to gather data about production processes.
This data includes machine performance, temperature, pressure, and more.
To handle such large volumes of data, companies need robust storage systems.
Cloud computing has become a popular option, allowing businesses to store and access big data efficiently.
Data Processing and Analysis
Once data is collected, it needs to be processed and analyzed.
This requires advanced software tools capable of handling large datasets.
Data scientists and analysts play a pivotal role in interpreting this data.
They use algorithms and models to identify patterns, anomalies, and trends within the data.
Predictive analytics can forecast potential issues before they become problems, enabling preventive maintenance and avoiding costly downtimes.
Improving Efficiency Through Big Data
Efficiency is paramount in manufacturing.
Big data provides a pathway to significant improvements.
Production Optimization
By analyzing data from production lines, manufacturers can pinpoint inefficiencies.
For instance, data might reveal that a particular machine is causing bottlenecks.
With this insight, adjustments can be made, such as reconfiguring the production layout or optimizing machine settings.
This results in smoother operations and reduces waste, both of materials and time.
Predictive Maintenance
Equipment failure can cause significant delays and financial losses.
Big data enables predictive maintenance by analyzing data from machine sensors.
Predictive models can detect signs of wear and tear before a breakdown occurs.
This allows maintenance teams to perform timely repairs, minimizing downtime and extending the lifespan of machinery.
Enhancing Product Quality
Quality control is another crucial area where big data makes a substantial impact.
Quality Monitoring
Throughout the production process, data is collected on product quality.
This includes measurements like dimensions, weight, and material properties.
Analyzing this data helps identify deviations from quality standards.
When issues are detected early, corrective actions can be taken promptly, ensuring that only high-quality products reach the market.
Customer Feedback Analysis
Big data isn’t limited to the factory floor.
Customer reviews and feedback also provide valuable information.
By analyzing this data, manufacturers can understand consumer preferences and pain points.
This feedback loop helps in making informed decisions about product design and improvements.
Ultimately, it leads to higher customer satisfaction and better market performance.
Case Studies: Big Data Success in Manufacturing
Several companies have demonstrated the power of big data in transforming their operations.
Siemens
Siemens, a global leader in industrial manufacturing, utilizes big data to enhance its production processes.
By integrating sensors into their machinery and collecting data on performance, Siemens can monitor operations in real-time.
They have successfully implemented predictive maintenance, which has significantly reduced downtimes and maintenance costs.
Additionally, data analysis has allowed them to optimize energy consumption, leading to more sustainable production practices.
General Electric (GE)
General Electric pioneered the use of big data in their manufacturing processes.
Using their Predix platform, GE collects and analyses vast amounts of data from their industrial equipment.
This has led to insights that improve operational efficiency and product quality.
For example, by analyzing data from jet engines, GE has been able to predict maintenance needs and enhance engine performance.
This has resulted in better fuel efficiency and reduced maintenance costs for their airline customers.
Challenges in Implementing Big Data Solutions
While the benefits of big data are clear, its implementation comes with challenges.
Data Integration
Manufacturers often have data scattered across different platforms and systems.
Integrating this data into a cohesive and accessible format is a significant challenge.
A unified data architecture is essential for effective analysis.
Skilled Workforce
Big data analysis requires a workforce skilled in data science and analytics.
There is a high demand for professionals who can interpret complex data and provide actionable insights.
Companies must invest in training or hiring the right talent to maximize the benefits of big data.
Data Security
With the increase in data collection, security becomes a critical concern.
Manufacturers must ensure that their data is protected from cyber threats.
Using encryption, regular security audits, and adhering to data privacy regulations are necessary measures.
The Future of Big Data in Manufacturing
The future looks promising as big data continues to evolve.
With advancements in artificial intelligence (AI) and machine learning, data analysis will become even more sophisticated.
These technologies will enable more accurate predictions and real-time optimization of manufacturing processes.
Additionally, the rise of edge computing—processing data closer to where it is generated—will reduce latency and improve decision-making speed.
This will be particularly useful in high-speed manufacturing environments.
In conclusion, big data analysis is revolutionizing the manufacturing industry.
By improving efficiency and quality, manufacturers can stay competitive and meet the growing demands of the market.
Embracing big data is no longer optional but has become a necessity for forward-thinking companies.
資料ダウンロード
QCD管理受発注クラウド「newji」は、受発注部門で必要なQCD管理全てを備えた、現場特化型兼クラウド型の今世紀最高の受発注管理システムとなります。
ユーザー登録
受発注業務の効率化だけでなく、システムを導入することで、コスト削減や製品・資材のステータス可視化のほか、属人化していた受発注情報の共有化による内部不正防止や統制にも役立ちます。
NEWJI DX
製造業に特化したデジタルトランスフォーメーション(DX)の実現を目指す請負開発型のコンサルティングサービスです。AI、iPaaS、および先端の技術を駆使して、製造プロセスの効率化、業務効率化、チームワーク強化、コスト削減、品質向上を実現します。このサービスは、製造業の課題を深く理解し、それに対する最適なデジタルソリューションを提供することで、企業が持続的な成長とイノベーションを達成できるようサポートします。
製造業ニュース解説
製造業、主に購買・調達部門にお勤めの方々に向けた情報を配信しております。
新任の方やベテランの方、管理職を対象とした幅広いコンテンツをご用意しております。
お問い合わせ
コストダウンが利益に直結する術だと理解していても、なかなか前に進めることができない状況。そんな時は、newjiのコストダウン自動化機能で大きく利益貢献しよう!
(β版非公開)