- お役立ち記事
- SPD in Japanese Manufacturing: Unleashing Speed, Standardization, and Security Across Industries
SPD in Japanese Manufacturing: Unleashing Speed, Standardization, and Security Across Industries
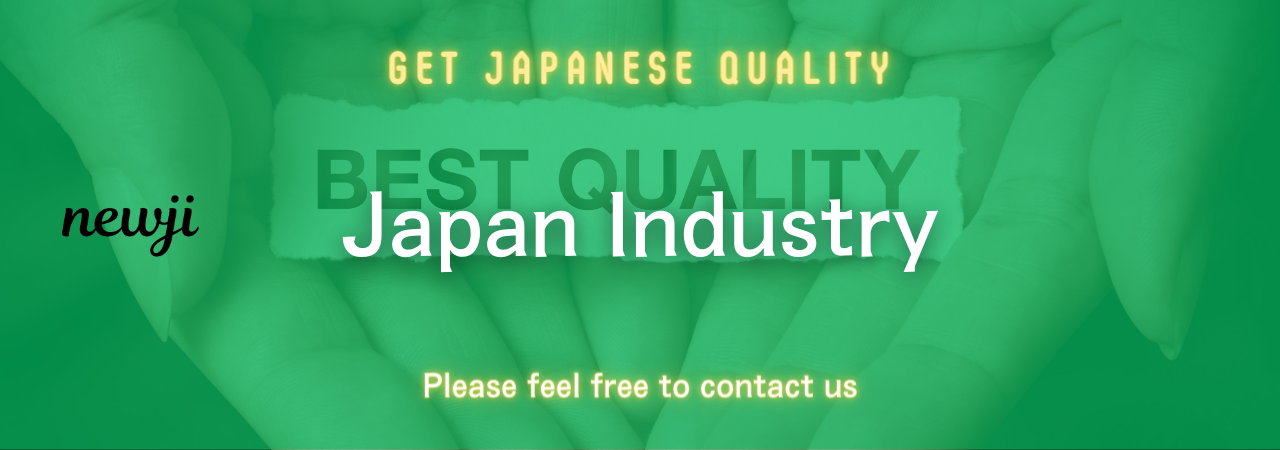
目次
Introduction to SPD in Japanese Manufacturing
Supply Chain Performance and Development (SPD) has been a pivotal aspect of operational efficiency in the manufacturing industry. Japanese manufacturing, renowned for its high standards, precision, and innovation, demonstrates an exceptional model when it comes to SPD. The nation’s approach towards speed, standardization, and security is notably rigorous, providing an edge in the competitive global market.
Japanese manufacturers have established a reputation for their ability to produce high-quality goods consistently while maintaining cost-effectiveness. This success is largely attributed to robust SPD practices, which focus on optimizing the supply chain from procurement to delivery. Understanding these practices, their advantages, and potential pitfalls can provide valuable insights for other industries looking to emulate this efficiency.
Speed in Japanese Manufacturing
One of the cornerstones of Japanese manufacturing excellence is the emphasis on speed. This doesn’t just refer to the pace of production but encompasses all facets of the supply chain, including procurement, logistics, and distribution.
Lean Manufacturing
Lean Manufacturing, or the Toyota Production System (TPS), is a methodology that aims to minimize waste without sacrificing productivity. This system, developed by the Toyota Motor Corporation, involves continuous improvement practices (Kaizen), Just-In-Time (JIT) production, and the elimination of any non-value-added activities.
In practice, Lean Manufacturing enhances speed by ensuring that materials and components are available exactly when needed, reducing idle time significantly. This approach not only accelerates production cycles but also lowers inventory costs.
Supplier Integration
Japanese manufacturers work closely with their suppliers to ensure that both parties are aligned in terms of quality expectations and delivery schedules. This level of integration with suppliers, often referred to as keiretsu, allows for real-time communication and quick response to any disruptions.
This relationship is an embodiment of trust and mutual dependency, ensuring that suppliers are capable and ready to meet the high standards of Japanese production lines swiftly.
Advantages
– **Reduced Lead Times**: Streamlined processes and efficient supplier relationships shorten lead times, improving overall market responsiveness.
– **Cost Efficiency**: Speed in production reduces the holding costs of inventory and minimizes the time goods take to market, optimizing profitability.
– **Enhanced Customer Satisfaction**: Faster turnarounds cater to customer demands promptly, leading to higher levels of customer satisfaction and loyalty.
Disadvantages
– **Supplier Dependence**: Excessive reliance on specific suppliers can become a bottleneck if issues arise, making the system vulnerable.
– **High Pressure**: The emphasis on speed can sometimes compromise thoroughness and increase pressure on employees and suppliers, potentially affecting quality if not managed well.
Standardization in Japanese Manufacturing
Standardization is vital in maintaining consistency and quality in Japanese manufacturing. By adhering to standard operating procedures and quality benchmarks, manufacturers ensure that every product meets the highest possible standards.
Quality Management Systems (QMS)
Systems like Six Sigma and Total Quality Management (TQM) are widely implemented across Japanese manufacturing sectors. These systems involve rigorous training for employees, constant monitoring of processes, and continuous improvement initiatives.
Through these practices, defects are significantly reduced, and processes become more predictable, ensuring that output remains consistent over time.
Automation and Technology
Advanced technologies such as robotics and IoT (Internet of Things) play a critical role in standardization. Automation reduces human error and increases production precision. The integration of IoT enables real-time monitoring and data collection, facilitating prompt adjustments to maintain production standards.
Advantages
– **Increased Consistency**: Standardized processes ensure uniformity in product quality, fostering a reliable brand image.
– **Efficiency and Productivity**: Automation and technology enhance repetitive task efficiency, freeing up human resources for more complex roles.
– **Predictability**: Standardization makes future planning and forecasting more accurate, aiding in strategic decision-making.
Disadvantages
– **Initial Investment**: Implementing advanced technology and standardization measures requires substantial initial investment.
– **Rigidity**: Over-standardization can lead to rigidity, making it difficult to adapt to unique or rapidly changing customer requirements.
Security in Japanese Manufacturing
Security within the supply chain is indispensable to the integrity and reputation of Japanese manufacturers. This includes both cyber and physical security measures to safeguard processes and data.
Cybersecurity
With the advent of Industry 4.0, the integration of digital technology in manufacturing has exposed companies to cyber threats. Japanese manufacturers invest significantly in robust cybersecurity frameworks to protect sensitive data and maintain operational integrity.
Supplier Vetting
Thorough vetting processes are employed to assess suppliers’ reliability and security protocols. This ensures that all links in the supply chain are robust and adhere to stringent security standards.
Advantages
– **Protection of Intellectual Property**: Stringent security measures protect intellectual property and proprietary technologies from unauthorized access.
– **Operational Continuity**: Enhanced security ensures uninterrupted operations, safeguarding against potential disruptions caused by security breaches.
– **Reputation Management**: A secure supply chain helps maintain a strong reputation, instilling confidence among clients and partners.
Disadvantages
– **Costly Maintenance**: Maintaining high standards of security, particularly in cybersecurity, can be expensive.
– **Complexity**: Implementing comprehensive security measures can introduce operational complexity, requiring specialized training and resources.
Best Practices in Supplier Negotiations
Effective supplier negotiations are crucial in maintaining a competitive edge and securing favorable terms. Here are some best practices observed in Japanese manufacturing.
Building Long-Term Relationships
Japanese companies prioritize building long-term, mutually beneficial relationships with suppliers. This involves a transparent and collaborative approach, fostering trust and loyalty.
Clear Communication
Clear and continuous communication is essential. Detailed specifications, quality expectations, and timelines are emphasized from the onset, ensuring both parties are aligned.
Win-Win Philosophy
Negotiations are approached with the philosophy of creating win-win situations. This means fair pricing, shared risks, and sometimes even sharing technological advancements to enhance the supplier’s capabilities.
Regular Audits
Conducting regular audits and reviews ensures that suppliers continue to meet the expected standards. These reviews also provide opportunities to identify areas for improvement and collaboration.
Advantages
– **Improved Supplier Performance**: Strong relationships and clear expectations lead to better supplier performance and reliability.
– **Cost Savings**: Effective negotiations can secure better pricing and terms, leading to cost savings.
– **Risk Mitigation**: Regular audits and clear communication help identify and mitigate risks early.
Disadvantages
– **Time-Consuming**: Building and maintaining long-term relationships can be time-consuming.
– **Dependency Risk**: Heavy reliance on a few key suppliers can pose risks if those suppliers encounter issues.
Current Market Conditions and Trends
Understanding the current market conditions is pivotal for effective SPD. Here are some key trends in Japanese manufacturing.
Technological Advancements
The integration of AI and Machine Learning in manufacturing is transforming production processes, making them more intelligent and efficient. These technologies are enabling more predictive maintenance, better quality control, and efficient resource management.
Emphasis on Sustainability
There is a growing emphasis on sustainable practices. Japanese manufacturers are investing in renewable energy sources, waste reduction techniques, and eco-friendly materials to reduce their environmental footprint.
Global Supply Chain Disruptions
Recent events, such as the COVID-19 pandemic, have highlighted vulnerabilities in global supply chains. Japanese manufacturers are increasingly focusing on building more resilient supply chains, including diversifying supplier bases and increasing local sourcing.
Conclusion
Japanese manufacturing stands as a benchmark for speed, standardization, and security in the supply chain. By adopting Lean Manufacturing principles, integrating technology, and maintaining high standards of security, Japanese manufacturers consistently deliver high-quality products swiftly and efficiently.
While there are challenges and costs associated with these practices, the advantages far outweigh the disadvantages. Understanding and implementing these practices can significantly enhance operational efficiency and market competitiveness. By fostering robust supplier relationships, staying abreast of technological advancements, and emphasizing sustainability, manufacturers worldwide can emulate the success of Japanese manufacturing and drive their own industries forward.
資料ダウンロード
QCD調達購買管理クラウド「newji」は、調達購買部門で必要なQCD管理全てを備えた、現場特化型兼クラウド型の今世紀最高の購買管理システムとなります。
ユーザー登録
調達購買業務の効率化だけでなく、システムを導入することで、コスト削減や製品・資材のステータス可視化のほか、属人化していた購買情報の共有化による内部不正防止や統制にも役立ちます。
NEWJI DX
製造業に特化したデジタルトランスフォーメーション(DX)の実現を目指す請負開発型のコンサルティングサービスです。AI、iPaaS、および先端の技術を駆使して、製造プロセスの効率化、業務効率化、チームワーク強化、コスト削減、品質向上を実現します。このサービスは、製造業の課題を深く理解し、それに対する最適なデジタルソリューションを提供することで、企業が持続的な成長とイノベーションを達成できるようサポートします。
オンライン講座
製造業、主に購買・調達部門にお勤めの方々に向けた情報を配信しております。
新任の方やベテランの方、管理職を対象とした幅広いコンテンツをご用意しております。
お問い合わせ
コストダウンが利益に直結する術だと理解していても、なかなか前に進めることができない状況。そんな時は、newjiのコストダウン自動化機能で大きく利益貢献しよう!
(Β版非公開)